Joe Hannold
Director of Operations at Dresser Utility Solutions- Claim this Profile
Click to upgrade to our gold package
for the full feature experience.
-
English -
Topline Score
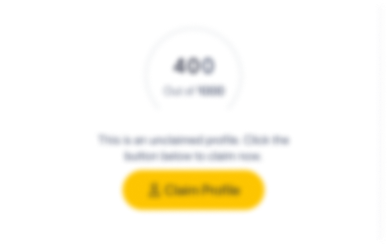
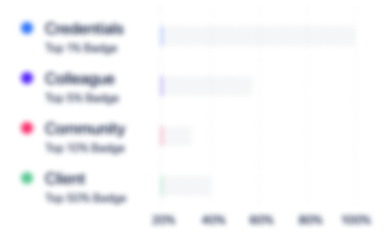
Bio


Experience
-
Dresser Utility Solutions
-
United States
-
Utilities
-
100 - 200 Employee
-
Director of Operations
-
Jun 2023 - Present
-
-
Director Of Manufacturing
-
Apr 2021 - Present
Direct and oversee the organizations manufacturing processes, monitors, and evaluates workflow and assembly methods and makes recommendations for process improvements. Additionally, responsible for developing employees, including a transformational, forward-looking approach to long-term growth
-
-
-
OneSubsea
-
United States
-
Oil and Gas
-
700 & Above Employee
-
Global Operations Manager Assembly & Test
-
Jun 2018 - Apr 2021
Responsible for Global Assembly & Test execution strategy, planning, & support in all Global OneSubsea manufacturing facilities, Service facilities, Third Party suppliers, & Customer locations. Drive standardization, efficiency, & continuous improvement initiatives across various global facilities.
-
-
Plant Manager
-
Mar 2017 - May 2018
Responsible for the coordination of manufacturing, production and inventory control facets of plant operations, ensuring safety, quality, on-time delivery, profitability and achievement of corporate and company established objectives. Ensure the safety of all employees by enforcing established HSE procedures and practices. Hire, develop, and retain critical talent and create an environment, which drives employee engagement, safe work practices, continuous improvement, and profitability. Maintain and improve upon the plant's physical structure and grounds. Annual financial budgeting and execution. Ensure the appropriate capital, technology, and resources are employed to maximize profitability and meet customer delivery and quality commitments. Show less
-
-
Plant Manager
-
Feb 2016 - Feb 2017
Responsible for the coordination of manufacturing, production and inventory control facets of plant operations, ensuring safety, quality, on-time delivery, profitability and achievement of corporate and company established objectives. Ensure the safety of all employees by enforcing established HSE procedures and practices. Hire, develop, and retain critical talent and create an environment, which drives employee engagement, safe work practices, continuous improvement, and profitability. Maintain and improve upon the plant's physical structure and grounds. Annual financial budgeting and execution. Ensure the appropriate capital, technology, and resources are employed to maximize profitability and meet customer delivery and quality commitments. Show less
-
-
Plant Manager
-
Jan 2014 - Feb 2016
Responsible for the coordination of manufacturing, production and inventory control facets of plant operations, ensuring safety, quality, on-time delivery, profitability and achievement of corporate and company established objectives. Ensure the safety of all employees by enforcing established HSE procedures and practices. Hire, develop, and retain critical talent and create an environment, which drives employee engagement, safe work practices, continuous improvement, and profitability. Maintain and improve upon the plant's physical structure and grounds. Annual financial budgeting and execution. Ensure the appropriate capital, technology, and resources are employed to maximize profitability and meet customer delivery and quality commitments. Show less
-
-
-
Dresser-Rand - A Siemens Business
-
United States
-
Machinery Manufacturing
-
700 & Above Employee
-
Operations Manager - Assembly and Test
-
Feb 2013 - Jan 2014
Managed the overall Assembly & Test operations for the Centrifugal Compressor product line. Responsible for the management of Safety, Quality, Delivery, & Cost measures as established and set for the Operation. Enhanced operational procedures & business processes in the areas of material & information flow. Carried out management responsibilities in accordance with company’s policies and applicable laws.Responsible for interviewing, selection, hiring, & training of new employees. Planned, assigned and directed all work activities. Performed employee performance appraisals; addressed employee performance and corrective action plans as well as employee motivation and rewards. Prepared annual budgets. Show less
-
-
Operational Excellence Program Manager
-
Aug 2012 - Feb 2013
Led and drove Operational Excellence initiatives that strategized and shaped the long-term vision and re-engineering of processes accordingly. Main focus was the implementation of an Employee Participation Process in the Dresser-Rand North America factories. Worked with internal teams in developing a strategy that helped them succeed in their business goals related to Safety, Quality, Delivery, & Cost.
-
-
-
Dresser, Inc.
-
United States
-
Oil and Gas
-
300 - 400 Employee
-
Manufacturing Manager
-
Dec 2004 - Aug 2012
Managed production operations for all manufacturing processes in the facility; directing staff and resources to meet production goals in the most efficient manner. Established work schedules, resource allocations and machine operations; resolving problems as they occurred. Monitored production schedules to ensure meeting customer demand. Executed various operational initiatives to improve safety, quality and efficiency. Managed production operations for all manufacturing processes in the facility; directing staff and resources to meet production goals in the most efficient manner. Established work schedules, resource allocations and machine operations; resolving problems as they occurred. Monitored production schedules to ensure meeting customer demand. Executed various operational initiatives to improve safety, quality and efficiency.
-
-
-
MPP
-
United States
-
Industrial Machinery Manufacturing
-
100 - 200 Employee
-
Production Manager
-
May 2003 - Dec 2004
Directed all production and manufacturing related activities in an industrial environment for the St. Marys, Washington St. Division of Metal Powder Products Inc. Responsible for the efficient and on – time production schedules in accordance with safety and quality standards. Directed all production and manufacturing related activities in an industrial environment for the St. Marys, Washington St. Division of Metal Powder Products Inc. Responsible for the efficient and on – time production schedules in accordance with safety and quality standards.
-
-
-
Kane Magnetics International
-
Kane PA
-
Plant Superintendent
-
May 1994 - May 2003
Managed all plant operations, production, and processes in a unionized environment for the Kane facility. Accountable for achievement of plant performance objectives and product quality. Monitor plant expenditures and budget. Review production schedules; determine workforce requirements and monitor production to ensure customer requirements are met. Recommend and implement changes to improve quality and reduce costs. Monitor labor efficiencies and labor variances; put forth corrective actions when needed. Evaluate subordinates. Ensure compliance to QS 9000 quality standards. Interface with customers. Show less
-
-
Education
-
University of Pittsburgh
Business Management -
Ashford University
Bachelor's degree, Business Administration and Management, General -
Penn State University
Business Administration and Management, General
Community
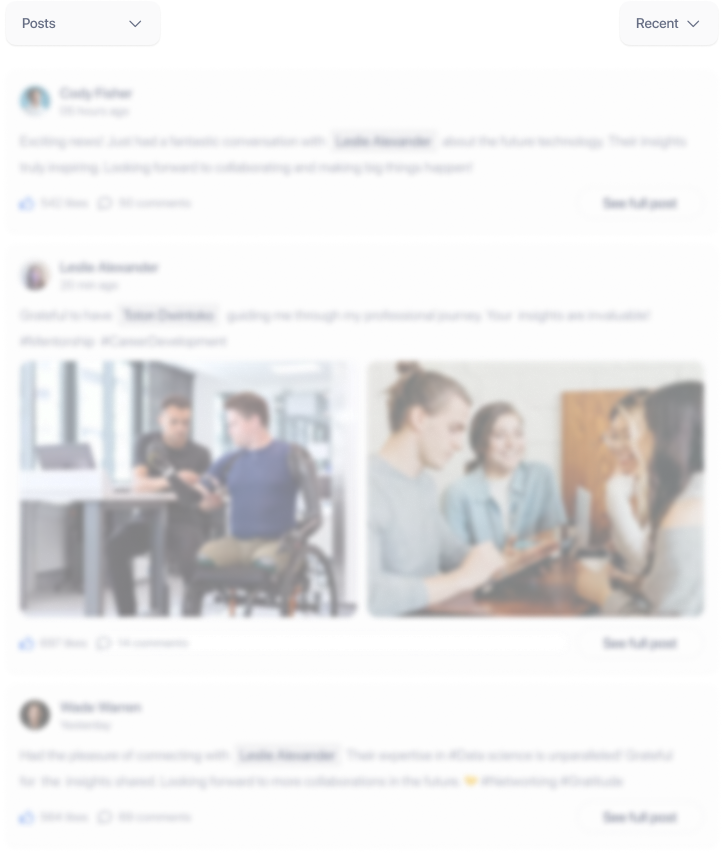