Joe Hoang
Operation Shift Manager at Life-Space Group- Claim this Profile
Click to upgrade to our gold package
for the full feature experience.
-
English -
-
Vietnamese -
-
Chinese -
Topline Score
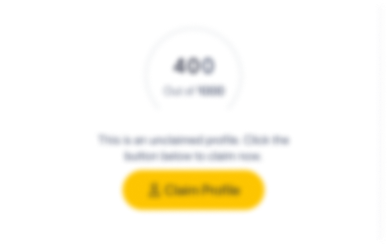
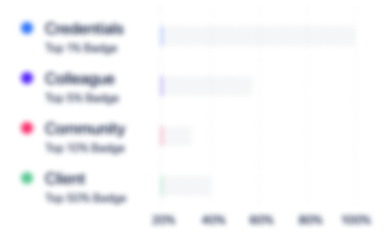
Bio

Peter Pemble-Smith
Having reviewed Joe's analytical work, I found it to be very thorough, well presented and honest. Overall, his professionalism and personal turnout were of the highest order.

Peter Pemble-Smith
Having reviewed Joe's analytical work, I found it to be very thorough, well presented and honest. Overall, his professionalism and personal turnout were of the highest order.

Peter Pemble-Smith
Having reviewed Joe's analytical work, I found it to be very thorough, well presented and honest. Overall, his professionalism and personal turnout were of the highest order.

Peter Pemble-Smith
Having reviewed Joe's analytical work, I found it to be very thorough, well presented and honest. Overall, his professionalism and personal turnout were of the highest order.

Experience
-
Life-Space Group
-
Australia
-
Wellness and Fitness Services
-
100 - 200 Employee
-
Operation Shift Manager
-
Aug 2020 - Present
• Actively leading a team of 8 to 10 full-time and contract personnel.• Provides training, guiding, and mentoring team’s members daily to maximise production performance, but maintains high levels of Products’ quality as well as right-first-time standard in a compliance manner.• Performs KSAs and periodically performance review to full-time team’s members.• Liaises with relevant departmental regarding production’s schedules &/ or activities.• Participates in initiation, discussion, investigation, and agreements on non-conformances, deviations, CAPAs, etc. • Reviews and approves Batch Records before and after production’s runs to ensure cGMP compliance.• Effectively managing resources, directing staffs, assigning tasks, fosters open communicating and influencing the team to achieve department’s objectives.• Ensuring the adequacy of Production’s staffs by liaising with the Agencies on a weekly basis &/or an emergency replacement to ensure daily &/or weekly production’s target met.• Responsible for the reviews and approves of Production Staffs’ working timesheets to be paid on a weekly basis. Show less
-
-
Project/Quality Coordinator
-
Sep 2020 - Aug 2022
• Search, liaise, and negotiate with external suppliers/vendors for new equipment/systems to be installed and associated documentation provides for both, the current as well as the newly constructed manufacturing sites.• Participates in the discussion, agreement and preparation of Site Master File, Project Validation Plan, Site Validation Master Plan and Validation Schedule Matrix, etc.. Schedule, execute, data analyse, and reports generate for qualification/validation’s activities (IQ, OQ, PQ, PV, CV, etc.,) on new equipment/systems.. Schedule, execute, and analyse of PV & CV samples on new & existing products.• Discusses, agrees, prepares and/or reviews on Qualification’s documentation (U/FRSs, DQs, IQ, OQ, PQ, etc) on new facilities, systems, instruments, and equipment.• Establish and maintain PQS documentations such as Policies, SOPs, WIs, Forms, Templates, etc.• Professional communications (both verbal & written) and presentations to internal and external stakeholders in relation to PQS’s documentations, qualification/validation activities, results, variations, and recommendations.• Effectively liaison and coordinates with related internal functional departments, engineers, and external consultants regarding works according to the company’s needs.. Responsible for the reviewal and approval of consultants and subcontractors working hours on a weekly basis. Show less
-
-
-
Blackmores Group
-
Australia
-
Wellness and Fitness Services
-
500 - 600 Employee
-
Analytical Scientist (Validation, QC and R&D)
-
Mar 2016 - Sep 2020
Quality & Regulatory Affairs – Validation: • Participated in the preparation, execution & qualification/validation of equipment (computerized & non computerized) deployed in the new Solid Dose (SD) facility to run fully under Real-Time Release Testing (RTRT) environment. • Supported the operations of new SD facility under RTRT environment (i.e. maintained instruments’ calibration status & functionality, provided accesses & trainings to production’s staffs at all levels, trouble-shooting, investigated OOS results, raised deviation, change control, CAPA, etc.) • Appointed as a SME for the analytical instruments deployed in an At-Line measurement environment in the new SD facility. • Planned, scheduled & executed validation works on existing & new products for the new SD facility to run under a fast-pace, At-Line measurement environment. • Liaising with suppliers to ensure IQ/OQ/PQ are completed, & documentation provided for new purchased instruments • Supported, conducted & consulted on validation projects and activities, included sampled and laboratory analyzed efficiently and accurately • Conducted sampled & tested of PQ, PV & CV's samples • Professional communication (verbal & written) & presentation with internal & external stake holders in relation to Validation activities, variables, results & recommendations • Writes protocols, reports & other documentation to required requirements & timelines (eg. TC, TP, TR, PQ, PQR, SOPs, WIs, etc) QC & R&D Departments: • Performed routine & non-routine analyzed of starting materials, intermediate, finished & stability products • Carried out laboratory investigations for OOT, OOS or atypical results as per SOP’s in order to ensure root cause identification & appropriate action • Helped with method development & method validation by conducted validation tests & method verification; discussion of outcomes & method amendments. • Conducted internal inspections of the laboratory & other areas regarding GMP & WHS activities Show less
-
-
-
IDT Australia Ltd
-
Melbourne, Australia
-
Analytical Chemist
-
Dec 2013 - Dec 2015
• Oversaw incoming raw materials (i.e., APIs, excipients, primary & secondary packaging) including labels and provided documentation inspected, samples sampled and tested (both routine & non-routine) and prepared associated documents and/or certification to ensure cGMP compliance. • Liaised with Suppliers on issues regarding visuals, physicals, and analytical results; requested documentation such as C of A/C of C and other clarification information to ensure cGMP compliance as per the company’s quality requirements. • Performed routine & non-routine analysis of intermediate, stability samples and finished products using instruments such as particle sizes, optical rotation, Karl Fischer, melting point, UV-vis, HPLC, etc. • Performed wet chemistry analysis in accordance with BP and USP’s methods. • Co-ordinated and performed water analysis for the whole site using TOC, conductivity, pH meter, etc. • Instrument calibrated for the following: HPLC, UV-vis, IR, KF, pH, conductivity, polarimeter, etc. • Provided training and/or supervision and supported to new and less experienced team members to ensure consistency in the delivery of Laboratory operations Extra responsibilities: • Helped with validation activities, including process and cleaning validation and laboratory analysis efficiently and accurately • Helped with method development, verification & validation for R&D projects (external clients) • Performed routine inspections of high-risk Cytotoxic facility • Conducted internal Audits/Inspections as part of the Company Internal Auditing Program, reported outcomes, raised non-compliance, and provided recommendations for corrective actions • Appointed Fire Warden for the Laboratory • Prepared, reviewed, and updated documents such SOPs, WIs, and Quality Control (QC) documentation to ensure it is maintained up to date & is compliance with standard practice Show less
-
-
-
Probiotec Limited
-
Melbourne, Australia
-
Senior Analytical Chemist
-
Mar 2012 - Dec 2013
Quality Department – Validation Group: • Professional communication (both verbal & written) and presentation with internal & external stakeholders in relation to qualification & validation activities, results, variations & recommendations. • Performed qualifications & re-qualifications (including performance qualification, process & cleaning validation) on new & existing equipment. • Conducted sampling & testing for performance qualification (PQ), process validation (PV) and cleaning validation (CV), using HPLC, UPLC, GC, etc. • Supported, conducted & consulted on Validation projects & activities, including sampling & laboratory analysis efficiently and accurately. • Documented & entered raw data & results as per GMP requirements and ensured data were collated for reports. • Investigated atypical results to find the root cause and appropriate action &/ method amendments to achieve the agreed results. • Prepared protocols, reports & other documentations to required requirements and timelines (e.g. PQ, PQR, SOPs, WIs, Change Controls, etc) QC Department - Raw Materials & Finished Product Groups: • Performed routine and non-routine analysis of starting raw materials, intermediate and finished products using instruments such as HPLC, UPLC, UV-Vis, NIR, etc • Performed physical tests and standard wet chemistry techniques following BP, USP monographs • Documented and entered raw data and results as per GMP requirements and ensured data was collated for reports • Carried out laboratory investigations for out-of-trend, out-of-specification or atypical results as per SOP’s to ensure root cause identification and appropriate action • Helped in method development & method validation by conducting validation tests and method verification and discussion of outcomes and method amendments • Provided training to less experience & new analysts Show less
-
-
-
PZ Cussons Aust Pty Ltd
-
Victoria, Australia
-
Quality Specialist
-
Jan 2011 - Mar 2012
• Carried out day to day QA activities. • Scheduled, prepared, coordinated & monitored Process Validation’s activities on new products introduced into Production. • Liaised with Suppliers on issues regarding visuals, physicals, and analytical results; requested documentation such as C of A/C of C and other clarification information if required. • Reviewed & ensured batch documents were completed and cGMP compliance prior to batches released. • Managed and followed up on customer complaints regarding product quality, hazards and fitness for purpose. This involved testing of returned sample/s against retention and control samples to identify and define processes and product quality issues and provided insightful and achievable recommendations to improve areas such as: materials, formulas and techniques. • Established & maintained the 5S system into the Laboratory to preserve consistency, safety, and efficiency of operational activities. • Conducted internal inspections of the laboratory & manufacturing site regarding 5S and EH&S activities. • Reviewed and updated SOP, Test Methods, Work Instructions, etc. Show less
-
-
-
Sanofi
-
France
-
Pharmaceutical Manufacturing
-
700 & Above Employee
-
Quality Control Analyst
-
Jan 2010 - Dec 2010
- Dealt with all Laboratory analysis - Particle size (wet & dry samples) - Optical rotation & Karl Fischer - LOD/LOI, Sulphated Ash & Melting point - Identification tests – FTIR, TLC, etc - Heavy Metal tests (USP & BP’s monograms) - Assay (HPLC, UV-Vis, Manual- & Auto-Titration) - Atomic Absorption Spectrometry (AAS) - Water & Ethanol analysis - Instruments Calibration (UV-vis, IR, etc) - Microscope - Other wet chemistry analysis, etc. - Conducted internal audits relating to 5S & EH & S activities. Show less
-
-
-
Alphapharm
-
Australia
-
Pharmaceutical Manufacturing
-
100 - 200 Employee
-
Production - R & D Laboratory - QA/QC Laboratory
-
Sep 1999 - Mar 2009
Raw Materials Group: - Dealt with all Laboratory analysis - Particle size (wet & dry samples) - Optical rotation & Karl Fischer - LOD/LOI, Sulphated Ash & Melting point - Identification tests – FTIR, NIR, TLC, etc - Heavy metal tests (USP & BP’s methods) - Assay (HPLC, UV-Vis, Manual- & Auto-Titration) - Other wet chemistry analysis, etc. Finish Product Group: • Dissolutions – UV & HPLC • Assay – UV & HPLC • Uniformity of Weights • Identification tests – NIR, TLC, etc • Physical Tests (Appearance, thickness, Hardness, Friability, Disintegration, etc) Stability Group: • Dissolutions – UV & HPLC • Physical tests (Appearance, thickness, Hardness, Friability, Disintegration, etc) • Familiar with calibrating machines & glassware • Samples & Solvents preparation • Assisting Chemists & Technicians • General glass ware cleaning Manufacture: - Cleaned the machines & equipments - Fills out log books & labels - Machine operator - Forklift operator Show less
-
-
Education
-
Griffith University
Bachelor of Pharmaceutical Science, Pharmaceutical Sciences and Pharmacy -
IBI Australia
Diploma of Quality Auditing, Quality Auditing -
Victoria Food Safety
Food Safety Supervisor
Community
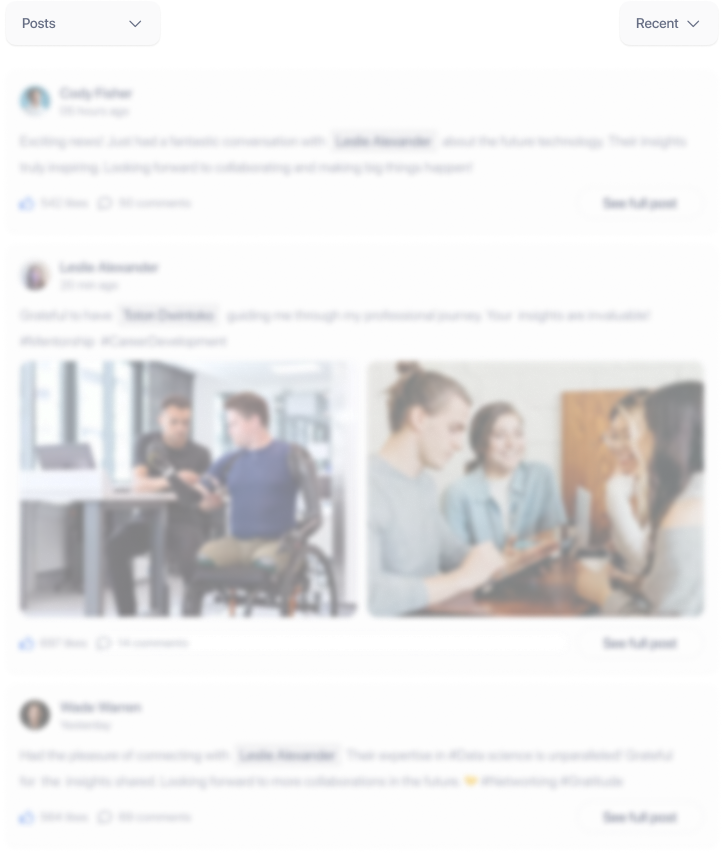