Joe Cortesio, PMP
Project Manager at Deployed Resources, LLC- Claim this Profile
Click to upgrade to our gold package
for the full feature experience.
Topline Score
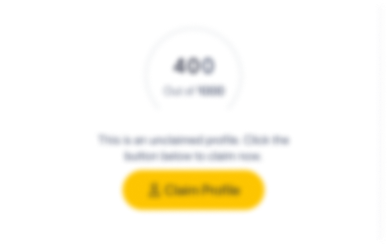
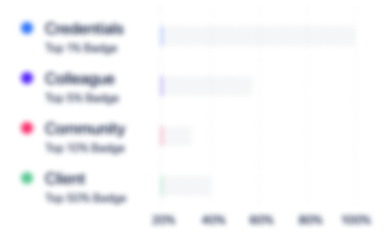
Bio


Credentials
-
PMP® Certification Training Course
SkillsoftOct, 2022- Nov, 2024 -
Occupational Health & Safety - 30 Hours - Construction
Yuma CountyNov, 2015- Nov, 2024 -
Project Management Professional (PMP)
Project Management InstituteMar, 2023- Nov, 2024 -
Red Cross Instructor Training
American Red CrossOct, 2022- Nov, 2024 -
FAA License
Federal Aviation AdministrationMay, 2022- Nov, 2024 -
Certified Mold Inspector (CMI)
360 Training LtdOct, 2022- Nov, 2024 -
Heartsaver CPR AED Classroom
American Heart AssociationJul, 2021- Nov, 2024 -
Heartsaver First Aid Classroom
American Heart AssociationJul, 2021- Nov, 2024 -
Initial 16 Hour Environmental Training
US ArmyOct, 2020- Nov, 2024 -
Initial 8 Hour Environmental Follow On Training
US ArmyOct, 2020- Nov, 2024 -
CPR & AED Certified
American Safety & Health InstituteMay, 2018- Nov, 2024 -
First Aid Certified
American Safety & Health InstituteMay, 2018- Nov, 2024
Experience
-
Deployed Resources, LLC
-
United States
-
Armed Forces
-
200 - 300 Employee
-
Project Manager
-
Apr 2023 - Present
-
-
Environment, Health and Safety Manager
-
Apr 2021 - Apr 2023
Worked long hours that provided outstanding safety oversite for 120+ contractors and subcontractors for federal temporary site build. Inspected 80+ pieces of equipment for safety issues during construction. Inspected Temporary Federal Facility daily. Conducted many daily, weekly, monthly, quarterly, and annual inspections. Trained 20+ personnel in new hire orientation. Ensured inventory of COVID Self-Tests, face shields, non-surgical and KN-95 masks, and gloves were up-to-date to ensure timely reordering of supplies. Provided safety training and oversite to 180+ subcontractors and 20+ contractors. Trained 60+ personnel in forklift and boom lift certification. Effectively communicated via text, email, and verbally concerning various safety-related topics. Reviewed safety policies and SOPs via online programs and websites. Documented hazards found on site along with ways in which to mitigate them. Entered daily, weekly, monthly, and quarterly inspections into IndustrySafe and KPA online safety program. Well-versed in online safety programs, policies, and procedures. Trained in various aspects of OSHA 1910 and OSHA 1926. Forklift, Boom Lift, AED, First Aid, CPR, and Child CPR certified. Performed Job Hazard Analysis on various hazards. Administered COVID Self-Tests to contractor personnel, updated results spreadsheet, and disposed of used COVID Tests into biohazardous waste bin. Conducted inspections for pest to include spikers, mice & small rodents, and snakes. Initiated 10 Incident Reports and conducted follow-on investigations concerning First Aid, Injury, Security, HAZMAT Spills, Property Damage, and Vehicle Accidents. Sent encrypted emails when PII and medical information was used. Coordinated and paid for HEP B shots for at-risk contractors. Coordinated with pest control for spraying, rodent traps, and bee swarm issues. Briefed contractors to expected hazards expected. Show less
-
-
-
SAWTST, LLC
-
Defense and Space Manufacturing
-
100 - 200 Employee
-
Maintenance Program Coordinator
-
Aug 2020 - Apr 2021
Coordinate with internal Army Reserves and external DoD contractors concerning HAZMAT, HAZWASTE, TMDE (Calibration), EPA, and OSHA regulations. Solved issue with battery (HAZWASTE) turn-ins in two days while established entity worked on the problem for 12 months. Solved issue with removing empty HAZWASTE barrels; coordinated with third party and had them removed within 10 days; the customer had been working on removal for 12 months. Not afraid to talk to internal and external customers to get problems resolved. Used soft skills on a daily basis. Show less
-
-
-
Primetime Harvesting, Inc
-
Yuma, Arizona Area
-
Maintenance Manager
-
Apr 2017 - Aug 2020
Lead, mentored, prioritized work for, provided training to, and advised nine direct subordinates in an agriculture and manufacturing environment. Made recommendations to president of company based upon research, analysis, data, and experience. Tracked, acted upon, and sent reports for preventative maintenance servicing every week. Implemented and became Program Administrator of Lock-Out Tag-Out program and used Computer Maintenance Management System (CMMS). Tracked, planned, and prioritized maintenance for 300+ pieces of equipment to include semi trucks, pickup trucks, trailers, tractors, buses, dry vans, welders, compressors, and farm implements. Reviewed, signed off, and/or corrected purchase invoices. Provided guidance, ideas, and tutelage in the fabrication of five farm implements. Ensured DOT compliance with tractor trailers and buses via 90 day and annual inspections. Filled out compliance paperwork in a timely manner for DOT inspections. Sold worn and unused assets; three buses, and seven vehicles. Coordinated with outside entities to include engineers, parts stores, and private parties to ensure mission accomplishment of Primetime goals. Communicated on a daily basis with the cooler, packline, maintenance, harvest, farm, office, sales, and leadership personnel to ensure mission accomplishment. Collaborated with external and internal customers for design and efficiency implementations, LEAN ideas and theory, and continued process improvement. Performed duties of Procurement Manager in regards to total material management in the planning and execution of material control, procurement, expediting, logistics, inspections, and field material management. Contracted outside entities to repair packing house facility. Ran maintenance of packline and packing house facility for three years. Tracked preventative, predictive, scheduled, and unscheduled maintenance on packline. Repaired Kwik Lok bagging machines, packline wiring, sensors, lasers, and VFDs. Show less
-
-
-
Corsair Technical Services
-
Bingen, Wa
-
Integrated Logistics Product Support Analyst
-
Mar 2016 - Mar 2017
Authored Integrated Logistics Support portion for US Coast Guard contract proposal with upward to $40M+ for Unmanned Aerial Systems placement in new and emerging land and maritime markets. Reviewed multiple Requests for Proposals (RFPs) and Statements Of Work (SOW) for contract and proposal preparation. Reviewed 500+ Engineering Changes and Requests as to effect of provisioning and sustainment of spare parts for over 30 countries, DoD CONUS, DoD OCONUS, and our allies. Continually track 3800+ part numbers that require changes and updates for use on Initial Provisioning and Sustainment Plans. Assisted with Sustainment and Provisioning Model with part number parent/child relationships, obsolete parts, system and subsystem relationships, and unit of issue/unit of measure issues. Used Predictive Maintenance (Lead Time, Mean Time between Demand) and quantity in Sparing Plans for review to ensure all ancillary parts are accounted for. Used past vast maintenance experience in engineering requests and proposed changes (ECRs/ECNs). Participated in continuous process improvement for repair induction to determine repairable components of X200 ScanEagle aircraft. Involved with entire life-cycle of product from design to end of life. Assisted in the development and performed a statistical modeling analysis for ILS programs. Assisted in the identification of barriers with RCA and problems affecting readiness and provided recommendation for RCCA in forecasting of parts. Show less
-
-
-
TRAX International Corporation
-
United States
-
Defense and Space Manufacturing
-
400 - 500 Employee
-
Supply and Logistics Manager
-
Apr 2015 - Feb 2016
Utilized the Automated Scanning and Tracking System (ASTS) database to update, add, transfer, and turn-in items for the U.S. Army. Turned-in $3M+ in assets that were damaged, obsolete, or no longer used for testing. Maintained 13 Hand Receipt Holders with 4k items worth $40M+. Added $1M+ worth of inventory. Performed annual inventories that involved physical hands-on of each piece of gear. Utilized PBUSE to track inventory and submitted proper paperwork with photo evidence for administrative changes to items. Coordinated with Hand Receipt Holders to conduct inspections, scan barcodes, count inventory, and submit documentation. Conducted research on parts, components, and test sets using FEDLOG, SLAMIS, and Google. Worked autonomously in pursuit of company goals and personal satisfaction. Very motivated to get the job efficiently completed safely and on time. Show less
-
-
Engineering Technician
-
Aug 2013 - Apr 2015
Applied mechanical and technical knowledge to perform all phases of technical test data observation and data recording in support of engineering projects. Used standardized, but varied, military technical manuals. Maintained an accurate and detailed chronological record of all test item operations and related maintenance. From the detailed records, updated supervisor as appropriate as to any anomalies within the data and engineering test. Created and proficiently used MS Excel and Word to record testing data. Maintained test parameters on test systems such as radar hours in operation and radiate and vehicle odometer miles to monitor test progress. Used CB radio to communicate to Range Control for clearance to testing sight. Performed pre-operational inspection on government owned vehicles to drive to and from test sights. Used effective communication, both written and verbal, on a professional level with Fleet Support Representatives (FSR) (employees of Boeing, Raytheon, Lockheed Martin, etc.). Show less
-
-
-
Marine Corps Recruiting
-
Armed Forces
-
700 & Above Employee
-
Liaison Officer
-
Sep 2010 - Nov 2012
Took Recruiting Station St. Louis from the third worst Recruiting Station in the western recruiting region in regards to quality control to the fourth best out of over 30 Recruiting Stations. Experienced with OPM (Office of Personnel Management) and JPAS background checks to ensure applicants were qualified under Marine Corps standards. Was named Military Entrance Processing Station Liaison of the Year, 9th Marine Corps District, 2012.
-
-
Recruiter
-
Mar 2009 - Sep 2010
Performed cold calls, public speaking events, and high school and college setups to get applicant’s information to set up appointments. Performed screening of applicants interested in obtaining information about the Marine Corps to determine if they met the basic criteria. Interviewed applicants to discover the need behind the need, discuss the features and benefits of the Marine Corps, and closed hard to ensure the successful sale. Briefed and processed applicants for enlistment into the military service. Demonstrated public speaking skills by conducting 34 public speaking events from small classrooms to medium sized auditoriums. Earned several awards for superior achievement in recruiting and quality control measures to include: Rookie Recruiter of the Month, June 2009; Rookie Recruiter of the Month, September 2009; Recruiter of the Month September 2009; Rookie Recruiter of the Quarter, 4th Quarter, 2009; Recruiting Sub-Station of the Month, June 2010. Show less
-
-
Safe for Flight Maintenance Manager
-
Sep 2004 - Feb 2009
Ensured quality control and safety was implemented by signing ADBs (Aircraft Discrepancy Books) "Safe for Flight" after a thorough review of aircraft safety of flight issues before every sortie. Trained seven senior enlisted Marines in the performance of their duties in maintenance control and releasing aircraft "Safe for Flight". Well versed in Naval Aviation Logistics Command Management Information System (NALCOMIS) and Optimized Organizational Maintenance Activity (OOMA). Spear-headed the implementation of the Automated Aircraft Discrepancy Books (AADBs) in OOMA, which allowed the unit to more effectively track, conduct, and supervise maintenance actions. Received a grade of on-track for all Group and Wing training inspections. Managed up to 20 aircraft, 140 Marines, aircraft maintenance and operational flight schedules required to support numerous Weapons and Tactics Instructor (WTI) Courses, Mojave Vipers, and pre-deployment, deployment, combat operations, and post-deployment movements. Coordinated and set priorities for all 9 work centers and 100K+ maintenance actions to ensure daily objectives were accomplished within time parameters. Scheduled and managed dozens of major aircraft maintenance (Phase) inspections which had a direct impact on the safety of flight for aircraft and aircrew. Have superior communication skills and have the ability to persuade others to produce results in a timely manner. Actively supervised the maintenance personnel to ensure that they are working and that the job gets completed on time. Conducted morning and afternoon maintenance meetings to prioritize the work center's work load between maintenance and the operational flight schedule, thus demonstrating public speaking skills. Controlled material requisitions from initial document number to prioritization code, expediting parts requests and close out. Received two Navy and Marine Corps Achievement Medals for hard work and dedication in this field. Show less
-
-
Avionics CD/QAR
-
Aug 2004 - Sep 2004
As a Collateral Duty/Quality Assurance Representative (CD/QAR), possessed a thorough understanding and working knowledge of sound management principles, workshop supervision, proper training methods, and approved maintenance procedures. Coordinated maintenance actions and ensured appropriate maintenance documentation was performed. Witnessed and supervised safety of flight functional tests to include landing gear, flight controls, and engine tests up to 40% of available aircraft throttle settings. Also performed duties under 'Avionics CDI' job description. Show less
-
-
Avionics CDI
-
Jun 2001 - Jul 2004
As a Collateral Duty Inspector (CDI), performed inspections of completed maintenance actions, conducted technical training within the avionics division, and monitored source data collection in the preparation of reports and records. Assisted in the planning and scheduling of work assignments and supervised maintenance performed on installed systems. Also performed all duties under 'Aviation Electronics Technician' job description.
-
-
Aviation Electronics Technician
-
Apr 1997 - Jun 2001
Interpreted schematics, wiring diagrams, and technical data contained in publication pertaining to avionics systems, test equipment, and aircraft. Observed safety precautions while working on and around aircraft. Diagnosed and isolated system failures of integrated avionics systems using appropriate test equipment and publications. Performed corrective action for corrosion of electronic components. Completed maintenance action forms (MAFs) to include man-hours, parts ordered and received, and specific aircraft systems inoperable codes. Operated ground support equipment to perform maintenance of installed systems. Performed avionics systems maintenance and operational tests IAW acceptable procedures. Performed maintenance functions for system, including removal, installation, adjustment, and alignment of system components and repair or replacement of associated aircraft wiring and interconnecting devices. Show less
-
-
Education
-
Liberty University
Master of Business Administration - MBA, Logistics, Materials, and Supply Chain Management -
Grand Canyon University
Bachelor’s Degree, Crisis/Emergency/Disaster Management -
Arizona Western College
Associate’s Degree, General Studies
Community
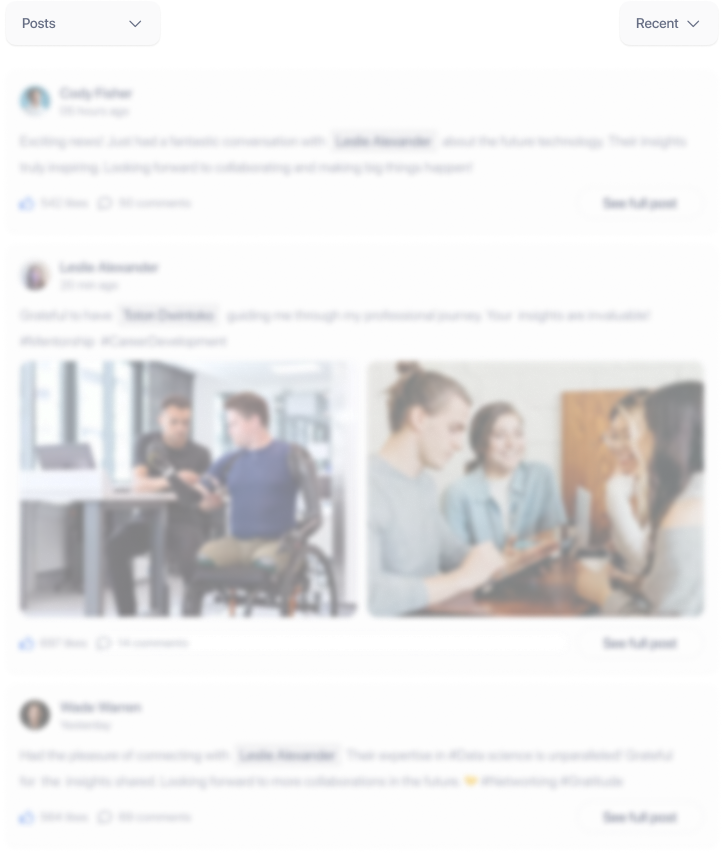