Joaquin Jack Caselles
Global Manufacturing Technology Director at Axalta Coating Systems- Claim this Profile
Click to upgrade to our gold package
for the full feature experience.
-
English -
-
Spanish -
Topline Score
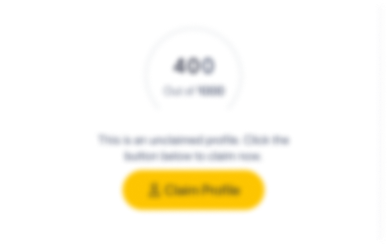
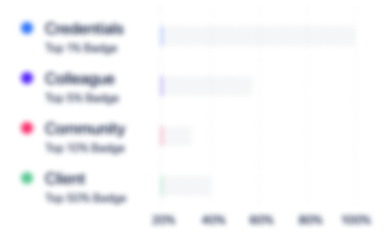
Bio


Credentials
-
Black Belt Certification
-
Experience
-
Axalta
-
United States
-
Chemical Manufacturing
-
700 & Above Employee
-
Global Manufacturing Technology Director
-
Feb 2013 - Present
Setting and implementing manufacturing processes and systems improvements to positively impact Productivity, Production Capacity, Cost, Product Quality, and SHE in all manufacturing plants globally: Manufacturing Process optimization, Product by Process and Waste elimination through Lean Manufacturing Transformation. Develop & Implement Manufacturing Best Practices , PSM (Process Safety Management and Reactor Safety) , Global Manufacturing Technology Org staffing & development, Develop basic data, design new plants and upgrade exiting processes to meet our Manufacturing Best Practices
-
-
-
DuPont
-
United States
-
Manufacturing
-
700 & Above Employee
-
Performance Coatings Global Manufacturing Technology Manager
-
2009 - Jan 2013
Create, set strategy, direction and lead a new Global DuPont Performance Coatings Manufacturing Technology (MT) organization at paint manufacturing plants to accelerate globally the rate of improvement and positively impact Safety, Cost, Productivity and Quality with no additional headcount to the business Create, set strategy, direction and lead a new Global DuPont Performance Coatings Manufacturing Technology (MT) organization at paint manufacturing plants to accelerate globally the rate of improvement and positively impact Safety, Cost, Productivity and Quality with no additional headcount to the business
-
-
-
-
Plant Manager
-
2006 - 2009
Created systems, processes and a strong management team that lead the significant plant improvements through strong team work and culture change. Prior to DuPont purchase, the site was a state owned facility, I changed 40% of my leadership staff within the first 4 months, established new management processes and delivered a step change improvement in safety, health, environmental performance, quality, productivity and cost , with a change in mindset and behavior and overall site performance metrics. Safety: Improved overall year over year site safety performance per corporate safety metrics Cost savings $ 2.6 MM, and other improvements resulting in reduced product cost per unit manufacture Capacity and Productivity; 40% Increased production in vs 2005 achieving record production months with an average of 6% plant fixed cost reduction vs. profit objectives during 3 years Quality Following a series of successful customer quality audits the plant was upgraded from class B to Class A supplier for international and national OEM customers in recognition for overall quality improvements. Increased in 25% our share at existing customers and new and international customers The site achieved its TS16949 follow up audit certification Employee moral and personnel development Based FranklinConvey’s xQ survey results used by DuPont corporate at the time, the Changchun plant personal experienced a significant execution and moral improvement change from 47% (2006) to 62% (2008) . Survey results reflected improvement in clarity of goals, commitment to goals, translation of goals into action, enabling performance by removing barriers, synergy, trust, communication and processes and accountability to management to each other for achieving results
-
-
Community
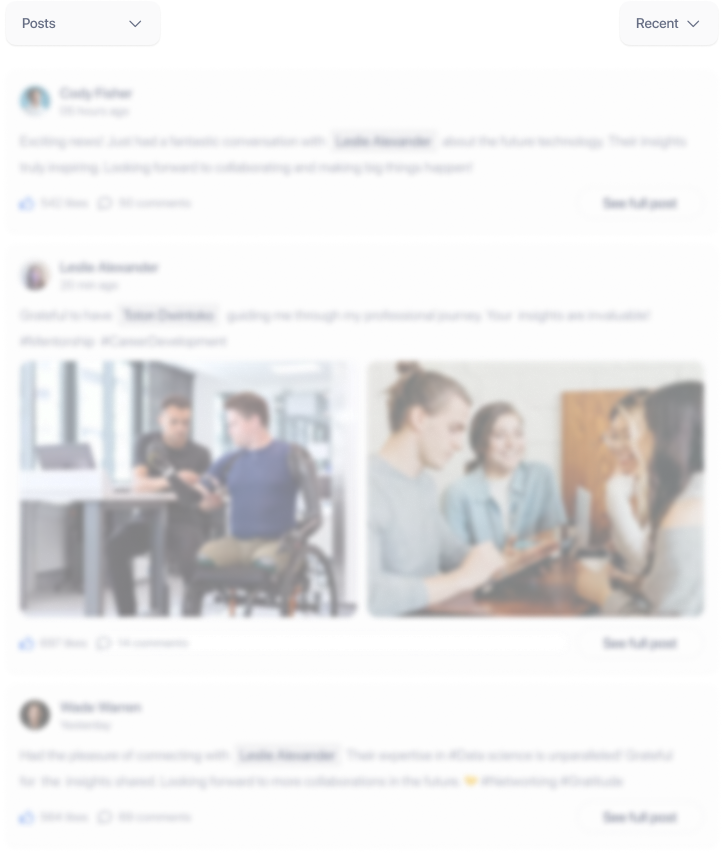