João (John) Marcelo de Carvalho
Supply Chain Analyst at Jamieson Wellness Inc.- Claim this Profile
Click to upgrade to our gold package
for the full feature experience.
-
English Full professional proficiency
-
Portuguese Native or bilingual proficiency
-
French Limited working proficiency
Topline Score
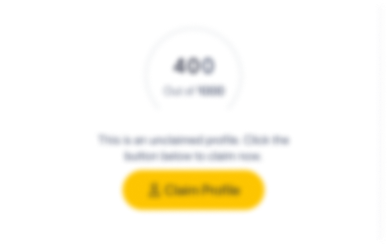
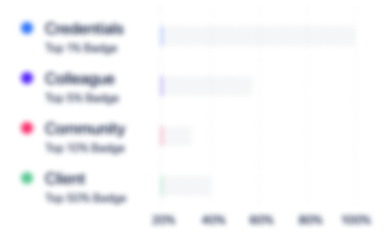
Bio

Adam Kwitko
Joao and I worked together on numerous group projects during our time studying Supply Chain Management and Global Logistics. His vast experience and understanding of industrial engineering, materials management and logistics were evident in his superior quantitative and qualitative analyses. He was highly dependable and a pleasure to work with.

THOMAS FONTES
João possui experiência no ramo industrial onde consegue desempenhar seu trabalho na área de materiais, planejamento e compras de forma bastante profissional e com excelentes resultados. Podemos destacar a sua pró atividade para solucionar problemas e gerir uma equipe, conduzindo-a da melhor maneira para os resultados esperados, além de incentivá-los e motiva-los sempre. Possui um excelente comunicação e é altamente qualificado para cargo de liderança.

Adam Kwitko
Joao and I worked together on numerous group projects during our time studying Supply Chain Management and Global Logistics. His vast experience and understanding of industrial engineering, materials management and logistics were evident in his superior quantitative and qualitative analyses. He was highly dependable and a pleasure to work with.

THOMAS FONTES
João possui experiência no ramo industrial onde consegue desempenhar seu trabalho na área de materiais, planejamento e compras de forma bastante profissional e com excelentes resultados. Podemos destacar a sua pró atividade para solucionar problemas e gerir uma equipe, conduzindo-a da melhor maneira para os resultados esperados, além de incentivá-los e motiva-los sempre. Possui um excelente comunicação e é altamente qualificado para cargo de liderança.

Adam Kwitko
Joao and I worked together on numerous group projects during our time studying Supply Chain Management and Global Logistics. His vast experience and understanding of industrial engineering, materials management and logistics were evident in his superior quantitative and qualitative analyses. He was highly dependable and a pleasure to work with.

THOMAS FONTES
João possui experiência no ramo industrial onde consegue desempenhar seu trabalho na área de materiais, planejamento e compras de forma bastante profissional e com excelentes resultados. Podemos destacar a sua pró atividade para solucionar problemas e gerir uma equipe, conduzindo-a da melhor maneira para os resultados esperados, além de incentivá-los e motiva-los sempre. Possui um excelente comunicação e é altamente qualificado para cargo de liderança.

Adam Kwitko
Joao and I worked together on numerous group projects during our time studying Supply Chain Management and Global Logistics. His vast experience and understanding of industrial engineering, materials management and logistics were evident in his superior quantitative and qualitative analyses. He was highly dependable and a pleasure to work with.

THOMAS FONTES
João possui experiência no ramo industrial onde consegue desempenhar seu trabalho na área de materiais, planejamento e compras de forma bastante profissional e com excelentes resultados. Podemos destacar a sua pró atividade para solucionar problemas e gerir uma equipe, conduzindo-a da melhor maneira para os resultados esperados, além de incentivá-los e motiva-los sempre. Possui um excelente comunicação e é altamente qualificado para cargo de liderança.
0
/5.0 / Based on 0 ratingsFilter reviews by:
Credentials
-
Microsoft Office Specialist Excel 2013
Microsoft Office SpecialistFeb, 2017- Sep, 2024 -
SAP Certified Application Associate - Business Process Integration with SAP ERP 6.0 EhP7
SAP
Experience
-
Jamieson Wellness Inc.
-
Canada
-
Wellness and Fitness Services
-
200 - 300 Employee
-
Supply Chain Analyst
-
Nov 2021 - Present
Provide daily Service Level report and root cause the items shorted; Provide instock and fill rate reports to customers; Send order script recommendation; Prepare monthly report on Service Level for senior leadership; Lead daily service level meetings to discuss item shortages and potential risks; Provide Service Level forecast based on MRP data and recalibration targets according to previous performance; Work closely with Customer Service, Demand Planners and Supply Planners to determine and solve potential risks; Use of QAD, Deacom and Kinaxis systems to leverage information and provide actionable insights to the Supply Chain group. Show less
-
-
-
Shoppers Drug Mart
-
Canada
-
Retail
-
700 & Above Employee
-
Supply Chain Clerk
-
Aug 2020 - Nov 2021
Created Return to Vendor (RTV) orders on SAP and TecSys systems Recreated Sales Orders; Reviewed and closed Purchase Orders on SAP; Reserved inventory for promotion events on JDA system Investigated root causes for non shipped products from Distribution Centers to stores; Provided KPI reports (inventory levels, service level, short items, etc.) to key vendors; Created ad hoc reports on Microsoft Excel for managers and directors. Created Return to Vendor (RTV) orders on SAP and TecSys systems Recreated Sales Orders; Reviewed and closed Purchase Orders on SAP; Reserved inventory for promotion events on JDA system Investigated root causes for non shipped products from Distribution Centers to stores; Provided KPI reports (inventory levels, service level, short items, etc.) to key vendors; Created ad hoc reports on Microsoft Excel for managers and directors.
-
-
-
-
Logistics Coordinator
-
Nov 2019 - Aug 2020
Scheduled delivery installation of furniture with customer and installers; Coordinated with clients to ensure office space constructions were completed previously to furniture delivery and installation; Followed up with suppliers to ensure all product is delivered on time and in full and communicated accordingly with customers and internal stakeholders when there were any delays; Worked with internal and external partners to solve deficiencies that occurred during the furniture installation. Show less
-
-
-
Club Demonstration Services
-
United States
-
Retail
-
700 & Above Employee
-
Shift Supervisor
-
Jan 2018 - Sep 2019
Supervision of product demonstrations being run, making sure that all sales advisers have what they need to engage COSTCO members and ensuring they follow the company policies and Food Safety Standards; Schedule demonstrators for the next day based on the program sent from Corporate, ensuring there is enough staff for all of them; Purchase of all necessary products from COSTCO; Update of daily results. Supervision of product demonstrations being run, making sure that all sales advisers have what they need to engage COSTCO members and ensuring they follow the company policies and Food Safety Standards; Schedule demonstrators for the next day based on the program sent from Corporate, ensuring there is enough staff for all of them; Purchase of all necessary products from COSTCO; Update of daily results.
-
-
-
Cameron
-
Australia
-
Leasing Non-residential Real Estate
-
1 - 100 Employee
-
Materials Supervisor
-
Sep 2015 - Mar 2016
- Supervised the following areas: Purchasing, Planning, Warehouse and Shipping;- Monthly update of the area to the division Vice President and Directors;- Updated of the plant's Capacity Planning;- Realized one annual Inventory count, with great results, within the budget;- Managed supplier relations;- Controlled the supplier performance, specially for outsourced parts;- Updated and was responsible for the operating budget.
-
-
Logistics Specialist
-
Jul 2014 - Sep 2015
- Followed up all import / export shipments, from the request to collect the goods at the vendor until delivery at the plant. Always focused on keeping critical materials available.- Managed vendors from all over the world;- Conducted daily meetings with all departments to determine the strategic planning to achieve monthly revenue.
-
-
GRDP
-
Jul 2012 - Jul 2014
Participated of the Global Rotational Development Program or GRDP, where I was exposed to several business areas and worked directly in four of them:Quality Area (Salvador plant): - Presented the major daily quality issues at the production meeting;- Developed a report and a follow up system for the non-conformities inside the Cameron-Vescon plant in Simões Filho. Materials area (Salvador plant):- Helped developed the Capacity Planning tool- Created manuals and standards for the Planning area procedures;- Generated Production Orders;- Traced materials inside the shop floor. Operations area (Taubaté plant) - Managed two AFEs (investment plans): one to conclude the expansion of the plant and the other to increase safety and comply with legal requirement regarding Health, Safety & Environment legislation within deadline and budget.- Managed the construction of the clean room ( a engineered space with a very low concentration of airbourne particles), a Petrobrás requisition for the assembly of actuators for valves also within deadline and budget;- Presented weekly projects updates to the plant Director and Managers.Industrial Engineering (Taubaté plant):- Concluded the previous investment plans within deadline budget;- Managed a project to build a new Assembly and Test for tools, from the definition of the layout to the delivery of the area ready for use by the Manufacturing department. This project involved many smaller projects, from retrofitting overhead cranes, project and development of a test bunker and purchase of all necessary tools and equipment. Show less
-
-
-
PSA Peugeot Citroën
-
Slovakia
-
Motor Vehicle Manufacturing
-
1 - 100 Employee
-
Intern
-
Jul 2008 - Jul 2010
- Analyzed quality checklists; - Coordinated the Kaizen Teian program (idea suggestion system); - Created and updated KPIs; - Managed measuring devices, assuring they were in conformity with the quality standards; - Participated in internal quality audits. - Analyzed quality checklists; - Coordinated the Kaizen Teian program (idea suggestion system); - Created and updated KPIs; - Managed measuring devices, assuring they were in conformity with the quality standards; - Participated in internal quality audits.
-
-
Education
-
Seneca College of Applied Arts and Technology
College Certificate, Supply Chain Management -
Universidade do Estado do Rio de Janeiro
Bachelor's degree, Industrial Engineering
Community
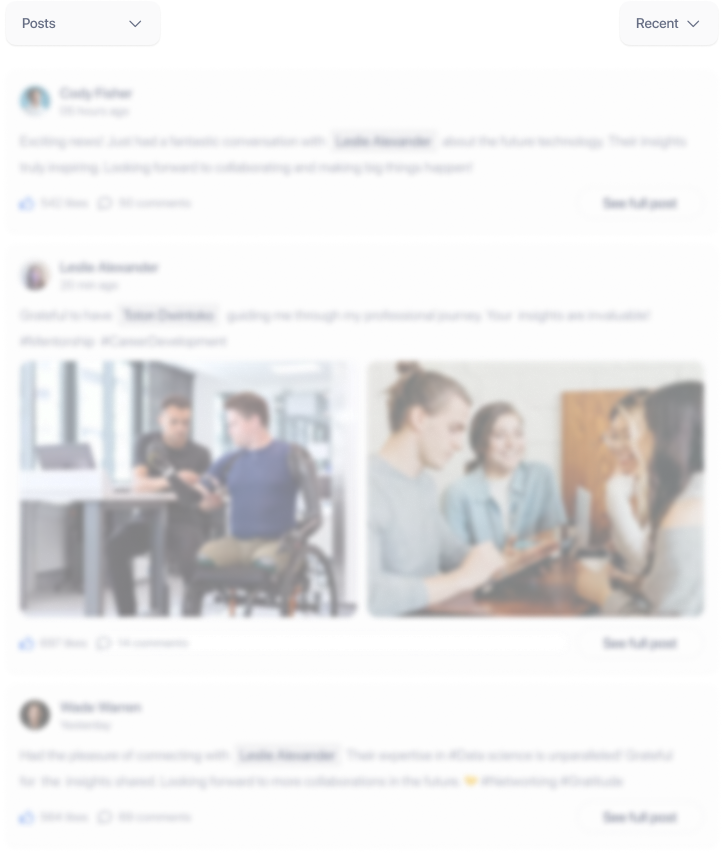