Jim Wagner
Quality Engineer at forteq North America Inc.- Claim this Profile
Click to upgrade to our gold package
for the full feature experience.
Topline Score
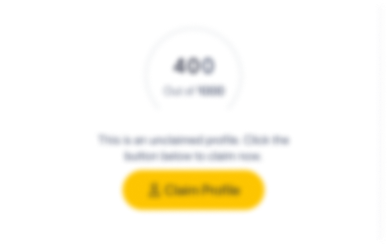
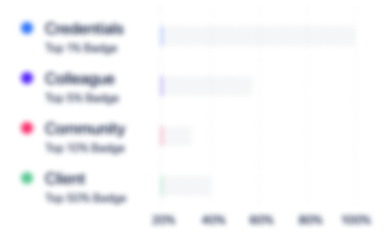
Bio

Hari Nayar
I have known Jim as a very methodical and sincere individual with a unique skill to take full ownership of a given task and execute it to fullest with minimal input or supervision. Jim and I have worked closely on developing numerous reports, test plans and hazard analysis documents and in each case, Jim has impressed me with his attention to detail and very thorough documentation skills. Jim's eye for quality and his ability to spot trends early on have tremendously helped mitigating numerous project risks. I have enjoyed working with Jim and wish him the very best.

Mark Appell
I worked with Jim Wagner at Ultralife Corporation and during that time Jim has always presented himself in a professional manner. His work ethic and commitment has always been admired. I feel that Jim is an asset and he has my recommendation. Thank you, Mark Appell

Hari Nayar
I have known Jim as a very methodical and sincere individual with a unique skill to take full ownership of a given task and execute it to fullest with minimal input or supervision. Jim and I have worked closely on developing numerous reports, test plans and hazard analysis documents and in each case, Jim has impressed me with his attention to detail and very thorough documentation skills. Jim's eye for quality and his ability to spot trends early on have tremendously helped mitigating numerous project risks. I have enjoyed working with Jim and wish him the very best.

Mark Appell
I worked with Jim Wagner at Ultralife Corporation and during that time Jim has always presented himself in a professional manner. His work ethic and commitment has always been admired. I feel that Jim is an asset and he has my recommendation. Thank you, Mark Appell

Hari Nayar
I have known Jim as a very methodical and sincere individual with a unique skill to take full ownership of a given task and execute it to fullest with minimal input or supervision. Jim and I have worked closely on developing numerous reports, test plans and hazard analysis documents and in each case, Jim has impressed me with his attention to detail and very thorough documentation skills. Jim's eye for quality and his ability to spot trends early on have tremendously helped mitigating numerous project risks. I have enjoyed working with Jim and wish him the very best.

Mark Appell
I worked with Jim Wagner at Ultralife Corporation and during that time Jim has always presented himself in a professional manner. His work ethic and commitment has always been admired. I feel that Jim is an asset and he has my recommendation. Thank you, Mark Appell

Hari Nayar
I have known Jim as a very methodical and sincere individual with a unique skill to take full ownership of a given task and execute it to fullest with minimal input or supervision. Jim and I have worked closely on developing numerous reports, test plans and hazard analysis documents and in each case, Jim has impressed me with his attention to detail and very thorough documentation skills. Jim's eye for quality and his ability to spot trends early on have tremendously helped mitigating numerous project risks. I have enjoyed working with Jim and wish him the very best.

Mark Appell
I worked with Jim Wagner at Ultralife Corporation and during that time Jim has always presented himself in a professional manner. His work ethic and commitment has always been admired. I feel that Jim is an asset and he has my recommendation. Thank you, Mark Appell

Credentials
-
ISO 14001 Environmental Management Systems Certified Internal Auditor
Bureau Veritas -
ISO/TS16949 Quality Management Systems Certified Internal Auditor
International Automotive Task Force (IATF)
Experience
-
forteq North America Inc.
-
United States
-
Motor Vehicle Manufacturing
-
1 - 100 Employee
-
Quality Engineer
-
Jul 2015 - Present
-
-
-
CAR Engineering and Manufacturing, Inc.
-
United States
-
Machinery Manufacturing
-
1 - 100 Employee
-
Quality Control Process Engineer
-
Sep 2013 - Jul 2015
-
-
-
Crosman Corp.
-
United States
-
Sporting Goods Manufacturing
-
1 - 100 Employee
-
Quality Assurance Engineer
-
May 2012 - Sep 2013
Quality Assurance Engineer at Crosman Corporation, a leading, worldwide designer, manufacturer and supplier of products for the shooting sports. Documented track record of reducing product returns using statistical analysis in concert with product design and manufacturing improvements. Active participant in weekly Customer Service team meetings to review up to the minute customer concerns and incorporate into product improvement efforts. Facilitated product family meetings and actions, participated in problem solving, 5S and TPM teams. Received Crosman “President’s Award” in July 2013 for work on the ‘Returns Reduction Team’.
-
-
-
-
Quality/Safety Engineer
-
Aug 2007 - Mar 2012
Part of strategic new products team, working on high profile renewable energy and military/industrial power saving projects. Developed extensive MIL-SPEC First Article Test (FAT) plans, defined test protocol per DoD MIL-STD and UK DEF STAN procedures. Developed military Safety Assessment Report (SAR) plans and final reports. Planned and coordinated associated validation tests. Trained and certified in CASSANDRA® Hazard Management Software in the UK. CASSANDRA® is the UK Ministry of Defence approved and preferred through life hazard management tool for use by contractors working on the safety of all defense equipment contracts.
-
-
-
-
Project Management Engineer
-
Aug 2004 - Sep 2007
Established and maintained project timelines and related activities for Automotive/Transportation, Metal to Plastic Conversion and Parker Hannifin inter-company programs. Qualified new products utilizing a variety of advanced measurement devices including DCC CMM units and automated vision systems. Well versed in SPC (Minitab), GD&T, and Automotive PPAP/PSO requirements. Experienced in PC-DMIS CMM programming. Completed Parker Hannifin in-house ‘Six Sigma’ program, TS-16949 and ISO-14001 internal auditor.
-
-
-
-
Quality Engineer, Supervisor
-
Jun 1991 - Aug 2004
Led all plant quality assurance activities to ensure finished products met customer specifications. Scope of responsibility included quality inspection during and after the manufacturing process and coordination of corrective action to eliminate defective products. Coordinated validation of new products and developed the quality assurance work instructions required to ensure those products met all customer specifications. Utilized SPC, GD&T, and PPAP - Production Part Approval Process to qualify products. Inspected first-run products to ensure compliance with customer specifications.
-
-
Education
-
University of Northern Iowa
Bachelor of Arts (BA)
Community
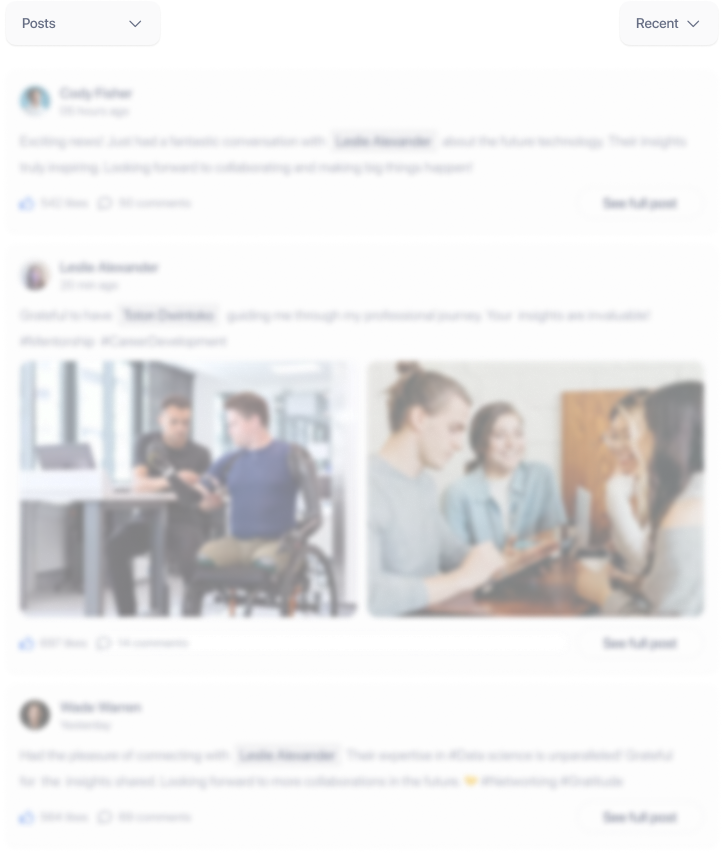