
Jim Salois
Director of Supply Chain at FN America, LLC- Claim this Profile
Click to upgrade to our gold package
for the full feature experience.
Topline Score
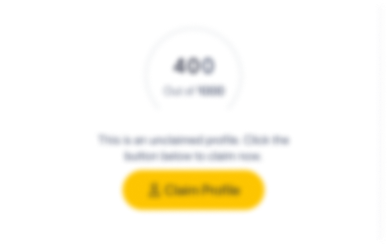
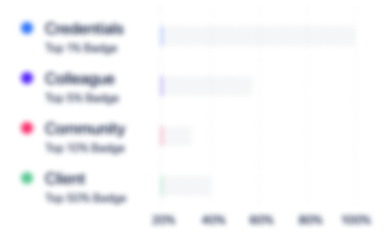
Bio

April Wolfe
Jim excels as a Supply Chain leader. He is able to build strong work relationships/connections across functions and cultures in order to effectively deliver change initiatives such as inventory reduction.

April Wolfe
Jim excels as a Supply Chain leader. He is able to build strong work relationships/connections across functions and cultures in order to effectively deliver change initiatives such as inventory reduction.

April Wolfe
Jim excels as a Supply Chain leader. He is able to build strong work relationships/connections across functions and cultures in order to effectively deliver change initiatives such as inventory reduction.

April Wolfe
Jim excels as a Supply Chain leader. He is able to build strong work relationships/connections across functions and cultures in order to effectively deliver change initiatives such as inventory reduction.

Experience
-
FN America, LLC
-
United States
-
Defense and Space Manufacturing
-
200 - 300 Employee
-
Director of Supply Chain
-
Apr 2018 - Present
Proud to lead the supply chain at FN America, LLC where we design, build, and deliver The World’s Most Battle-Proven Firearms.® Proud to lead the supply chain at FN America, LLC where we design, build, and deliver The World’s Most Battle-Proven Firearms.®
-
-
-
MEKRA Lang North America, LLC
-
United States
-
Motor Vehicle Parts Manufacturing
-
1 - 100 Employee
-
Director of Supply Chain
-
2014 - Present
Director, Supply Chain, North AmericaHired to lead company’s global purchasing organization. Within 6 months, promoted to take on accountability for multimillion-dollar annual spend and performance of end-to-end supply chain with 35-member team across purchasing, manufacturing planning, supplier quality, S&OP, warehousing, logistics, shipping, and customer service. Holds COO-level responsibility for production results of 8-line, discrete manufacturing/assembly operation. Reports to CEO and VP of Logistics (Germany). Led discovery-phase evaluation of supply chain team capabilities, processes, systems, and supplier relationships. Worked with team, CEO, and CFO to establish a corporate culture focused on quality, on-time delivery, and accountability within each division. Efforts have elevated on-time delivery 15%. Member of steering committee that established global purchasing function. Implemented supplier scorecard and initiatives that reduced supplier PPMs 100-fold. Designed and implemented “Care and Control” initiative that improved inventory accuracy to 98% from 85%. Migrated company from vertical integration to full assembly purchasing strategy, eliminating quality problems. Reduced backorders 10-fold by measuring production results, improving schedule planning, and implementing Kanban restocking. Consults daily with CFO on go/no-feasibility of capital projects and potential Investments to modernize production.
-
-
-
-
Interim Chief Operating Officer / Strategic Advisor
-
Dec 2013 - Feb 2014
Serving as interim COO and strategic advisor to CEO, led small manufacturing company’s extensive equipment, technology, and operations modernization project which resulted in 200% ROI within first 2 years. Serving as interim COO and strategic advisor to CEO, led small manufacturing company’s extensive equipment, technology, and operations modernization project which resulted in 200% ROI within first 2 years.
-
-
-
Esab Welding & Cutting
-
United States
-
1 - 100 Employee
-
Senior Director Supply Chain North America
-
2011 - 2013
Senior Director, Supply Chain, North AmericaHeld accountability for North American supply chain for rapidly growing stock distributor and OEM supplier with supply/distribution network of 18K SKUs operating through 9 distribution centers and 5 manufacturing facilities across U.S., Mexico, and Canada. Managing end-to-end supply chain, achieved 48% inventory reduction, delivered multimillion-dollar procurement savings, and increased on-time delivery 10%. Results helped position company for successful sale. Led consolidation of supply planning organization into cohesive North American model adopted on global scale.
-
-
-
Prysmian Group
-
Italy
-
Manufacturing
-
700 & Above Employee
-
Purchasing Director North America
-
2006 - 2011
Purchasing Director, North America, ’08 – ’11 Director, Strategic Metals & Supplier Quality, ’06 – ’08Recruited to manage hedging and purchasing of copper, aluminum, and tin. After identifying and resolving critical ERP reporting problem and negotiating extended payment terms with suppliers, promoted to manage raw material and MRO spend supporting 4 manufacturing sites in U.S. and Canada. Reported directly to CEO. Delivered multimillion-dollar savings in 1 year by implementing pricing indexed to feedstocks. Led aggressive program to update departmental procedures/audits, ensuring compliance with IAS/FASB and ISO requirements.
-
-
-
Delphi
-
United Kingdom
-
Motor Vehicle Manufacturing
-
700 & Above Employee
-
Manager, Value Analysis/Value Engineering, ’05 – ’06
-
1989 - 2006
Manager, Value Analysis/Value Engineering, ’05 – ’06Global Commodity Manager, Platinum Group Metals, ’03 – ’04Global Commodity Manager, Base Metals, ’01 – ’03Advanced Supplier Quality Manager, Steering Division, ’00 – ’01Senior Buyer, Global Purchasing, ’98 – ’00Assistant Staff Project Engineer, Steering Column New Development, ’89 – ’97Advanced rapidly through positions of increasing accountability; repeatedly promoted into turnaround environments. Identified internal/external opportunities that generated multimillion-dollar cost savings. Scope of leadership accountability spanned suppliers worldwide, 14 team members, and up to $1.5B in annual spend.
-
-
Education
-
University of Michigan
MBA, Business -
Michigan State University
MSME, Mechanical Engineering -
Michigan Technological University
BSEE, Electrical Engineering
Community
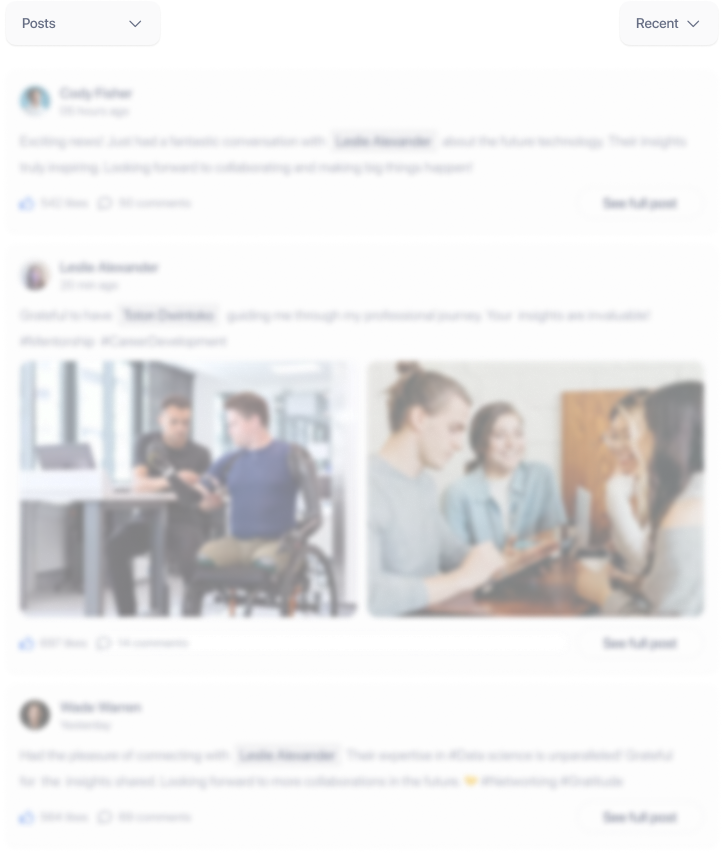