Jim Murphy
Operations Manager / Plant Change Agent – Shelbyville Facility at Bekaert Corporation- Claim this Profile
Click to upgrade to our gold package
for the full feature experience.
Topline Score
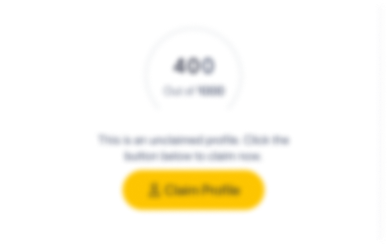
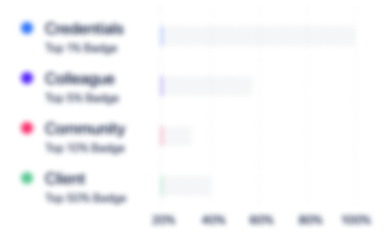
Bio


Experience
-
Bekaert Corporation
-
United States
-
1 - 100 Employee
-
Operations Manager / Plant Change Agent – Shelbyville Facility
-
2018 - Present
Excel in strategic leadership role as Shelbyville facility’s second in command and head of production, transforming plant into manufacturer of high quality, high margin steel wire products. Oversee 6 production leaders and 100+ production operators. Lead safe, streamlined operations and drive continuous improvements to enhance cost-per-ton, output, scrap, safety, and other key metrics.> Increased gross earnings per ton by 30% by changing strategic focus of production from volume produced to profit achieved.> Minimized returns due to poor quality products and enabled plant to produce higher quality, higher margin products by driving culture change to focus on quality.> Reduced internal rejection rate 60% and recorded zero customer rejections for products going through furnace and water air patenting (F&WAP) heat treatment process, while increasing production rate of sellable products.> Solidified new high margin anchor account by leading effort to achieve correct tensile strength and ductility. > Led development of special nylon coated wire for global client.> Addressed spike in safety issues at plant that resulted in changes in machinery and processes, and 67% incident reduction.> Established plant as world-class provider of emerging, high-end electro galvanized wire product.> Lowered cost to manufacture electro galvanized wire product line by $147K annually by reducing amount of expensive zinc required.> Created culture of continuous improvement that encouraged operators to identify and communicate ides to improve quality, safety, and efficiency.> Increased on time delivery rate from 92% to 98%.Core Competencies: Strategic Leadership | Production & Plant Operations | High Quality Manufacturing | Continuous Improvements | Efficiency Initiatives | Quality Program Design & Implementation | Furnace & Water Air Patenting Heat Treatment Process | Account Management | New Product Development | Safety Initiatives | Electro Galvanized Wire Products
-
-
Corporate Manufacturing System Change Agent
-
2015 - 2018
Contributed as member of 8-person US change agent team on strategic corporate effort to achieve standardization, enhance efficiency, and increase productivity across 90 global facilities. Traveled to facilities and engaged workforce to improve operations; analyzed work streams, brainstormed improvements, tested ideas, provided financial aspects for proposals, and launched programs to achieve bottom-line-driven 2-year-plan objectives. Served on team at 8 facilities, lead change agent at 2 facilities, and maintenance and energy regional change agent for North American facilities. > Oversaw change agent team at Rogers Wave facility that identified 104% of targeted savings.> Reduced scrap by 40 metric tons a month and saved $300K annually through scrap reduction effort. > Led initiative that reduced expense waste by $190K annually.> Saved 10,000 labor hours and $174K in cost of dies by using new die that lasted 20% longer, suffered 50% less fractures, and required less production labor.> Revamped spool reconditioning process that reduced rejection rate of reconditioned spools 80% and saved $92K in annual labor.> Restructured vendor contracts at Rome facility resulting in annual savings of $141K in forklift costs, $54K in HVAC, $111K in cleaning services, and $153K in maintenance expenses.> Enabled a 50% reduction in labor required to operate machines by reorganizing production layout at Orville facility, which eliminated need for 8,000 man-hours.Core Competencies: Team Collaboration | Standardization Program Development | Productivity Initiatives | Work Stream Analysis | Financial Analysis | Facility-Wide Change Program Leadership | Scrap & Waste Reductions | Vendor Contract Renegotiations | Facility Layout Optimization
-
-
Supply Chain Manager – Orville Facility
-
2013 - 2015
-
-
Materials Manager
-
2011 - 2013
-
-
Production Manager
-
2009 - 2011
-
-
Quality Assurance Manager
-
2001 - 2009
-
-
Continuous Improvement Coordinator
-
1999 - 2001
-
-
Senior Process Engineer
-
1997 - 1999
-
-
Education
-
The Ohio State University
Bachelor of Science, Materials Science Engineering
Community
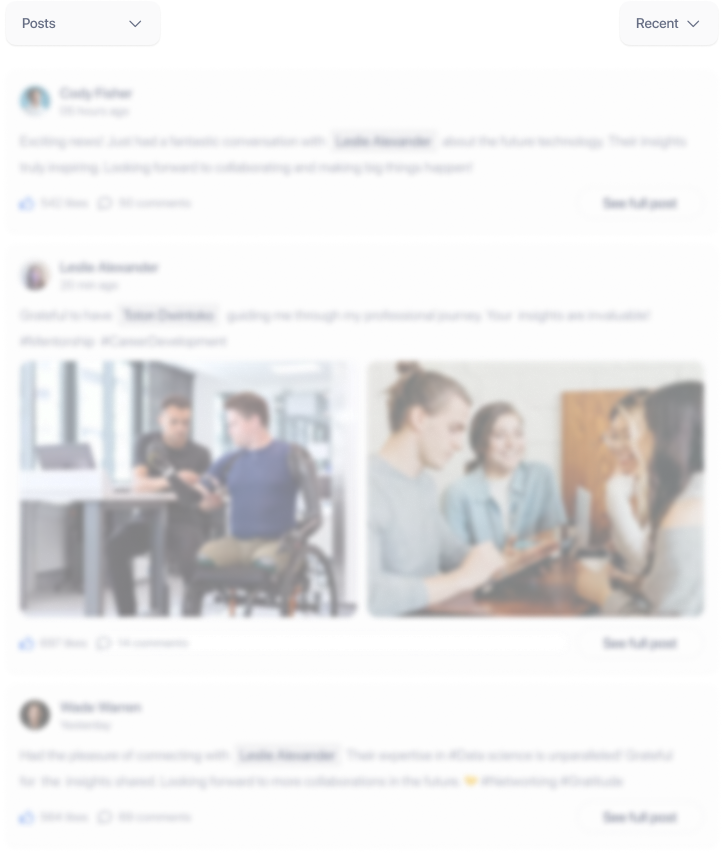