Jayaprakash(JP) Gnanam
President at Lean Six Sigma Experts Corporation- Claim this Profile
Click to upgrade to our gold package
for the full feature experience.
Topline Score
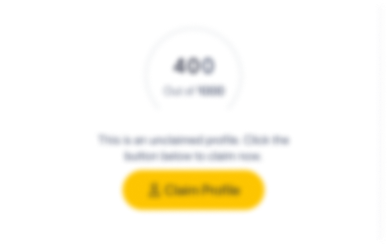
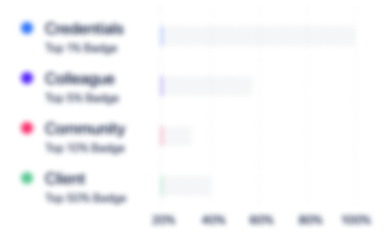
Bio

Christine Grove
JP is one of the best to work with. His Six Sigma skills and people skills are top shelf!

Chris Underwood
At Mountainside, as we started our lean journey, we recognized that we would need a Lean Sensei to help us define both our long term and short term strategies for adopting lean manufacturing, and to help us with the tactical implementation. After talking to a few experts and consultants, we selected JP for his years of experience and his engaging style. JP has a fantastic, casual teaching and facilitation style that allowed our engineers, inspectors and machine operators to

Tim Schmit
I have worked with JP on several levels of Lean implementation. JP’s knowledge and experience along with his ability to engage employees at all levels of the organization are what made our lean implementation a success. JP was instrumental in coaching and mentoring me and others in the organization so we could continue our lean journey for years to come. I have a lot of respect for JP and highly recommend him to anyone interested in learning the correct approach to lean implementation.

Christine Grove
JP is one of the best to work with. His Six Sigma skills and people skills are top shelf!

Chris Underwood
At Mountainside, as we started our lean journey, we recognized that we would need a Lean Sensei to help us define both our long term and short term strategies for adopting lean manufacturing, and to help us with the tactical implementation. After talking to a few experts and consultants, we selected JP for his years of experience and his engaging style. JP has a fantastic, casual teaching and facilitation style that allowed our engineers, inspectors and machine operators to

Tim Schmit
I have worked with JP on several levels of Lean implementation. JP’s knowledge and experience along with his ability to engage employees at all levels of the organization are what made our lean implementation a success. JP was instrumental in coaching and mentoring me and others in the organization so we could continue our lean journey for years to come. I have a lot of respect for JP and highly recommend him to anyone interested in learning the correct approach to lean implementation.

Christine Grove
JP is one of the best to work with. His Six Sigma skills and people skills are top shelf!

Chris Underwood
At Mountainside, as we started our lean journey, we recognized that we would need a Lean Sensei to help us define both our long term and short term strategies for adopting lean manufacturing, and to help us with the tactical implementation. After talking to a few experts and consultants, we selected JP for his years of experience and his engaging style. JP has a fantastic, casual teaching and facilitation style that allowed our engineers, inspectors and machine operators to

Tim Schmit
I have worked with JP on several levels of Lean implementation. JP’s knowledge and experience along with his ability to engage employees at all levels of the organization are what made our lean implementation a success. JP was instrumental in coaching and mentoring me and others in the organization so we could continue our lean journey for years to come. I have a lot of respect for JP and highly recommend him to anyone interested in learning the correct approach to lean implementation.

Christine Grove
JP is one of the best to work with. His Six Sigma skills and people skills are top shelf!

Chris Underwood
At Mountainside, as we started our lean journey, we recognized that we would need a Lean Sensei to help us define both our long term and short term strategies for adopting lean manufacturing, and to help us with the tactical implementation. After talking to a few experts and consultants, we selected JP for his years of experience and his engaging style. JP has a fantastic, casual teaching and facilitation style that allowed our engineers, inspectors and machine operators to

Tim Schmit
I have worked with JP on several levels of Lean implementation. JP’s knowledge and experience along with his ability to engage employees at all levels of the organization are what made our lean implementation a success. JP was instrumental in coaching and mentoring me and others in the organization so we could continue our lean journey for years to come. I have a lot of respect for JP and highly recommend him to anyone interested in learning the correct approach to lean implementation.
0
/5.0 / Based on 0 ratingsFilter reviews by:
Credentials
-
ASQ Certified Manager of Quality/Organizational Excellence
- -
ASQ Certified Quality Engineer
- -
ASQ Certified Six Sigma Black Belt
- -
Certified Professional in Lean
- -
Certified Six Sigma Green Belt
- -
Certified Six Sigma Master Black Belt
- -
Certified Trainer/Practitioner in Lean
-
Experience
-
Lean Six Sigma Experts Corporation
-
United States
-
Business Consulting and Services
-
1 - 100 Employee
-
President
-
Jan 2011 - Present
Lean Six Sigma Experts Corp. provides training, consulting, recruiting, and customized software to ensure long-lasting results for clients, including: ▶ Re-engineer processes for scale, growth and employee engagement ▶ Streamline operations and improve employee engagements ▶ Reduced lead times and WIP ▶ Reversed losses, retained business, and millions of dollars in increased sales. ▶ Millions in annual cost savings and company valuation increases KEY SUCCESSES: ➤ Led successful business growth strategy resulting in 50% YOY growth, 80% return businesses and 90% client satisfaction ➤ Secured $50+ million in cost savings for clients. ➤ Added $100+ million in company valuation for clients. ➤ Facilitated more than 200 Kaizen rapid improvement events delivering up to 10x ROI. Show less
-
-
-
Accellent
-
South Africa
-
1 - 100 Employee
-
Global Director, Continuous Improvement
-
Jun 2008 - Jan 2011
Through the implementation of a world-class Lean Six Sigma program, I led continuous improvement and turnaround efforts for this $550 million company with 18 locations across the U.S., India, and Europe, driving alignment between program strategy/policies and corporate/supply chain objectives. Built and trained team of 12 Lean Leaders. ➤ Evaluated and improved plant manager performance by teaming with HR to develop and roll out Leadership Assessment process. Evaluated Lean Managers across all sites, partnering with third party firm to examine leaders’ situational responses and preferred workstyle. ➤ Saved $4.2 million through continuous improvement strategies and kaizen events resulting in significant improvements in safety, quality, delivery, and costs. ➤ Generated $15 million in annual sales from new business. ➤ Collaborated with consulting firm to introduce “Breakthrough Improvement Program,” saving $17 million and improving employee engagement scores across 8 plants. Show less
-
-
-
Avaya
-
United States
-
IT Services and IT Consulting
-
700 & Above Employee
-
Lean Six Sigma Master Black Belt
-
Jan 2008 - Jun 2008
Implemented Lean and Six Sigma principles company-wide to improve business process efficiency and reduce costs. ➤ Contributed to development of Sales Factory concept to process new business quotes efficiently. ➤ Saved $1.2 million and reduced cycle time of sales quoting process 80%. ➤ Secured $150 million in new business after implementation of new process improvement framework, which reduced cost of service and improved new business win rate 8%. ➤ Collaborated on “Rapid Quoting” process with 6 other departments. Reduced time to create a quote from 6 hours to less than 25 minutes. Show less
-
-
-
-
Lean Sigma Black Belt
-
Sep 2006 - Jan 2008
Hired to lead multiple Lean Manufacturing Projects, I trained employees in several plants and: ➤ Implemented a Kanban system in the facility. ➤ Used Six Sigma process to resolve critical customer complaint in UK facility. ➤ Cut lead time 33%, inventory 50%. Increased throughput 250%, saving $81,000 in labor costs. ➤ Improved forming process using Six Sigma principle, avoiding $1 million in costs. ➤ Received “Builders Award” from Accellent in recognition of best project of the year. Show less
-
-
-
Eaton Corporation
-
United States
-
Wellness and Fitness Services
-
Manufacturing Engineer
-
Jun 2003 - Sep 2006
Initially hired as a Lean Coordinator, I earned 2 promotions during my 3 years with Eaton. I was promoted to Manufacturing Engineer to develop and improve manufacturing processes, efficiencies, and product quality. ➤ Launched new $1.8 million aftermarket business, implementing $1.2 million in CNC machines to support the business.➤ Applying Lean Manufacturing and Six Sigma principles, saved $240,000, improved process capability 331%, and reduced tooling cost 285%.➤ Reduced cycle time of the bottleneck operation by 6%, tooling costs 3%, and setup time 50% in 2 different operations. Show less
-
-
Lean Manufacturing Engineer
-
Feb 2004 - Jun 2005
Charged with driving improvements at the site level, I introduced a comprehensive continuous improvement system to implement, manage, and sustain Lean Manufacturing principles and established OEE measures throughout the facility.➤ Implemented Kanban system and reduced the WIP 13%.➤ Reduced setup time of the friction weld cell 41%.➤ Increased throughput of the seat grinding operation, achieving $99,000 in cost savings.➤ Improved productivity of the profile grinding operation to save $18,000. Show less
-
-
Lean Coordinator
-
2003 - 2004
Hired to implement Lean principles at the site level, I trained, I trained all personnel across the entire facility in Lean Manufacturing principles and implemented a continuous flow assembly line to assemble commercial electrical panels.➤ Implemented Lean Manufacturing tools, including Value Stream Map, 5S, Standardized Work, TPM, Error Proofing, Setup Reduction, Continuous Flow Manufacturing, and Pull Systems.➤ Converted batch operation into a Continuous Flow manufacturing using Lean tools. Project resulted in 15% productivity improvements and $45,000 in cost savings. Show less
-
-
-
Colorado State University-Pueblo
-
United States
-
Higher Education
-
500 - 600 Employee
-
Graduate Assistant
-
2002 - 2003
Developed methodology for integrating Lean and Six Sigma principles, a one-of-a kind approach at the time and one of the very first attempts to integrate Lean and Six Sigma into one comprehensive approach. Developed methodology for integrating Lean and Six Sigma principles, a one-of-a kind approach at the time and one of the very first attempts to integrate Lean and Six Sigma into one comprehensive approach.
-
-
-
-
Engineer In Training
-
2001 - 2001
Completed internship; Developed an online weight control system to reduce the weight variation in the final packaging of tea powder. Used Six Sigma statistical tools and analysis to define and establish control limits for this system. Completed internship; Developed an online weight control system to reduce the weight variation in the final packaging of tea powder. Used Six Sigma statistical tools and analysis to define and establish control limits for this system.
-
-
-
ICF
-
Tunisia
-
Construction
-
Engineer In Training
-
2000 - 2000
-
-
Education
-
Colorado State University Pueblo
Master of Science - MS, Industrial & Systems Engineering -
PSG College of Technology
Bachelor of Science - BS, Production Engineering
Community
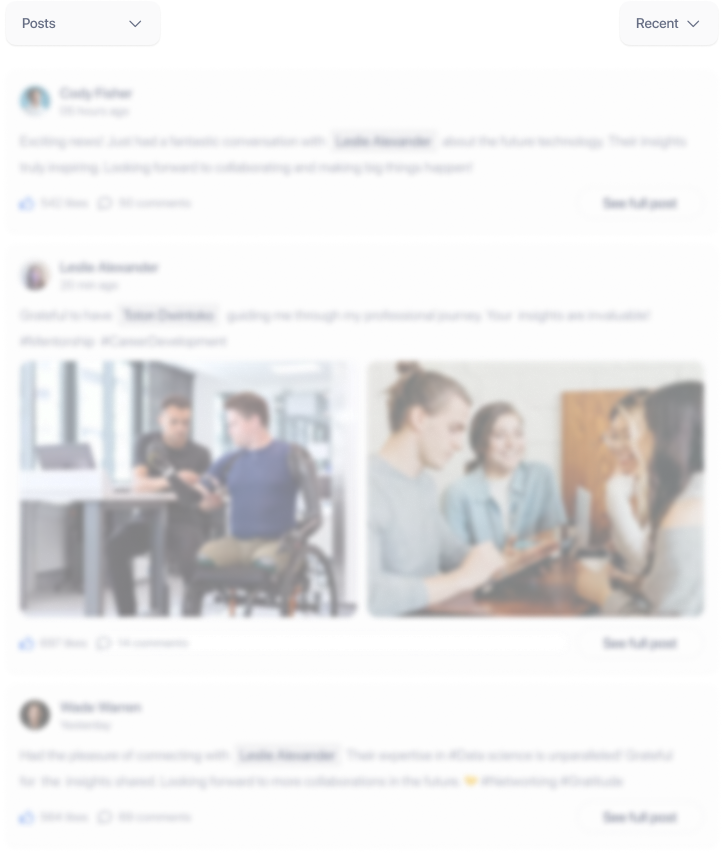