Jesus Castillo Gomez
Optimization Leader at Kapptek- Claim this Profile
Click to upgrade to our gold package
for the full feature experience.
Topline Score
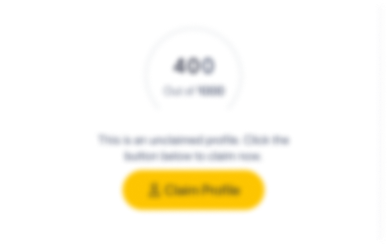
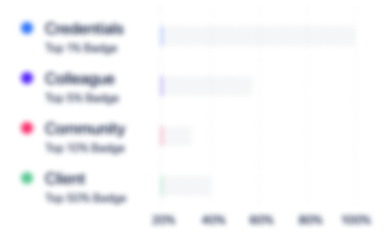
Bio


Experience
-
Kapptek
-
Chile
-
Mining
-
1 - 100 Employee
-
Optimization Leader
-
Oct 2014 - Present
Responsible of Implementation, and development of Kapptek Real Time Optimization Systems (RTO). Successfully implemented optimization systems in Mexico and Chile. Responsible of Implementation, and development of Kapptek Real Time Optimization Systems (RTO). Successfully implemented optimization systems in Mexico and Chile.
-
-
-
Portage
-
Torreon Coahuila
-
Integration Engineer
-
Apr 2014 - Oct 2014
Responsible for development and Implementation of Portage products on site. Advance Regulatory Control. Responsible for development and Implementation of Portage products on site. Advance Regulatory Control.
-
-
-
CADETOCA
-
IT Services and IT Consulting
-
700 & Above Employee
-
Sr Instruments Maintenance Engineer
-
Jan 2009 - Apr 2014
Responsible of instrumentation calibration and traceability. Main duties include but are not limited to propose and implement Improvement Projects, Assure Instruments calibration against certified standards, implementation of preventive and predictive maintenance plans.• Project Management Activities: Successfully lead and implemented significant improvement projects with the instrument technician personnel and as a Green Belt in Six Sigma projects with a designated team. Most remarkable examples of project management with the instrument technician personnel include reducing the gas consumption in Herreshoff Furnance #1. The implementation was carried out in 5 months (from concept to release). These projects resulted in several awards. As a Green Belt in Six Sigma methodology the most remarkable example of project management include reducing the %CaO in the magnesium oxide reactor and the reduction of OOS products in the HQ2001 line. The implementation was carried out in 11 months (from concept to release). These projects resulted in recognition from COO in the chemical division of Peñoles Group, and were key to the successful implementation of new products in the Magnesium Oxide Specialties Plant.• Process Control Enhancement Activities: Tuning and creation of control loops and general automation for all the plant process. The most important include automatic preparation of HQ2001 and Neutromag products, which lead to comply with our clients requirements and increase sales.• New technologies implementation: Successfully migrated from an Excel Calibration Records Database to an Automated Electronic System (2000 instruments) based on Emerson AMS and Beamex MC5 calibrator. This led to the reduction of time per calibration and documentation; also reduce the calibration interval for several instruments in compliance with ISO9000. This resulted in reduction of calibration costs and increasing efficiency of the instrumentation department. Show less
-
-
Instruments Technical Advisor
-
Sep 2007 - Jan 2009
Carried out instrument calibrations and maintenance. Main duties include but are not limited to administration of the Distributed Control System (DCS DeltaV), developing and coordinating projects with external suppliers and contractors. • SOPs Improvements: Standard Operating and Maintenance Procedures reviewed and improved (some of them completely rewritten) most remarkable examples are the reduction of calibration procedures grouping instruments per measured variable, creation of maintenance procedures for all new instruments and on site training for all personnel. • Communication Protocols: Planning and construction of Device Net and Foundation Fieldbus Networks for control process improvement. The most important example include the migration to FF instruments in the Gas Line #1 which supply gas to all Furnaces in the Magnesium Oxide Plant, some of the improvement include Field Control within Control Loops in case of a Loss of Communication with the DCS, Communication Redundancy and Advanced Instruments Diagnostics which led to the Predictive Maintenance Program. Motor control rooms (MCC) migration from typical I/O to Device Net, the most important include migration of MCC#8 which include 50 devices consisting of E3Plus, Power Flex Frequency Drives, DSAs, it include the design of the new networks and Devicenet Devices Configuration from RsNetworx to DeltaV DCS• BOM Creation of Bill of Materials required for Control Valves Preventive Maintenance. Before it was common to unsuccessfully calibrate and repair Control valves due the lack of spare parts. The project consisted in take note of every serial number, model and dimensions of the control valves within plant (500), and defines the BOM for each maintenance and stock. Show less
-
-
Education
-
MIT Professional Education
Online Program, Machine Learning -
Universidad Tecmilenio
Master of Business Administration - MBA, Quality & Productivity, GreenBelt Six Sigma Certification -
Instituto Tecnológico de La Laguna
Engineer's degree, Electronics
Community
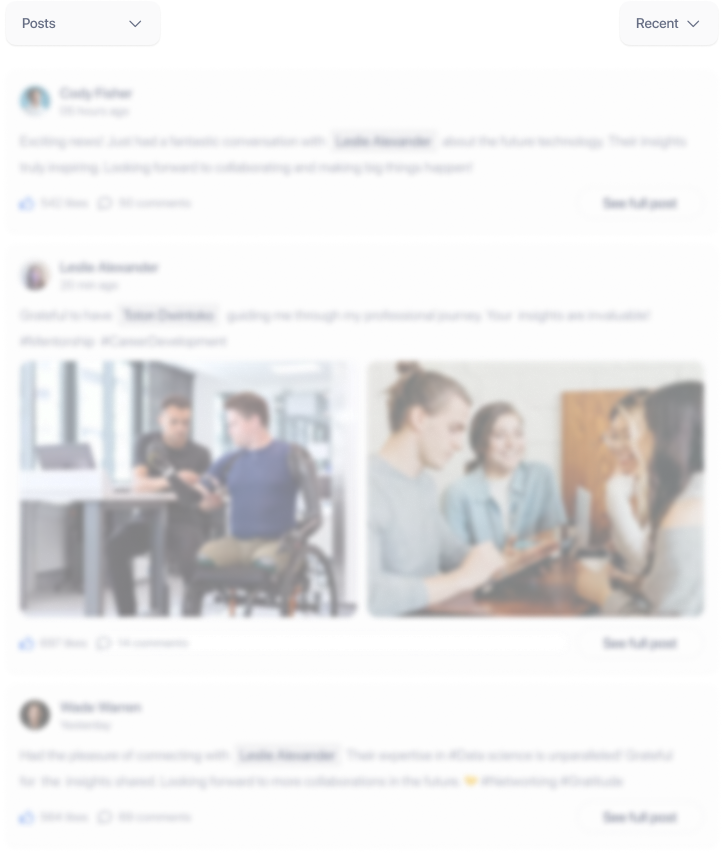