Jessie Kuo
Engineer at 啟碁科技股份有限公司- Claim this Profile
Click to upgrade to our gold package
for the full feature experience.
Topline Score
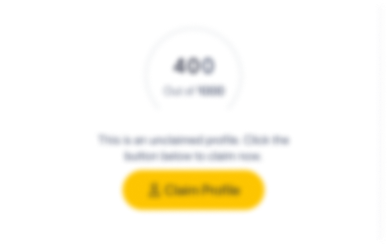
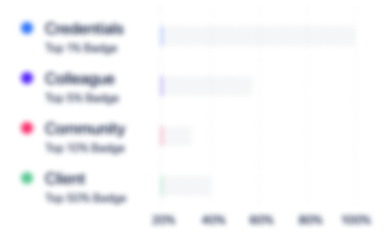
Bio


Experience
-
Wistron NeWeb Corporation (WNC)
-
Taiwan
-
Telecommunications
-
700 & Above Employee
-
Engineer
-
Apr 2022 - Present
Projects- 1. Sorting out processing data for headquarter to establish smart production scheduling system. 2-1. Finalize/standardize the work processes of managing SMT stencils, SMT squeegees, and DIP carriers. 2-2. Following the previous item, train/qualify labors to be adequate for the jobs, including local and foreign (mostly Filipino) employees. Projects- 1. Sorting out processing data for headquarter to establish smart production scheduling system. 2-1. Finalize/standardize the work processes of managing SMT stencils, SMT squeegees, and DIP carriers. 2-2. Following the previous item, train/qualify labors to be adequate for the jobs, including local and foreign (mostly Filipino) employees.
-
-
-
Orient Semiconductor Electronics Ltd.
-
Taiwan
-
Semiconductor Manufacturing
-
1 - 100 Employee
-
-
Apr 2020 - Mar 2022
-New Product Introduction: Create manufacturing data, i.e., BOM(bill of material) and work instructions, based on data pack provided by customers.-Mass production: Issue engineering changes requested from customers or to improve production efficiency.-Communicate/work with customers closely to solve technical issues occurred during production.Skill:Cam 350SAP2020-Jun, AS-9100D
-
-
-
Dec 2018 - Apr 2020
Work as quality engineer in the team. Have knowledge of IPC-A class 3 PCBA and understandings of different customer requirements.Specialize in continuous improvement, especially focus on systematic processes, evaluate work flow and adopt efficient work processes with specific work instructions, thus to improve yield of massive production, to serve the purpose of increasing profit.Work closely with customers through continuous communication with them, so that I have deep-depth understandings on various aspects, including customer company culture, collaboration method, special requirements of products. By working with different functional departments of customers, we are able to build products meeting customers’ needs and strengthen long-term partnership as well.Customer services experiences / Skills• Take actions for Customer complaint - 3D/8D report• Process continuous improvement - monitoring yield, defining problem, locating root cause, developing containment and permanent corrective actions, examining implementation.• Weekly, monthly, quarterly quality review with customer, which includes production yield, process improvement and case studying.• Project planning and implementation• QSA/QPA audit• Quality control plan• PFMEAExpatriate. Worked based on Houston, U.S. from September to November, 2019. Show less
-
-
-
Sep 2016 - Nov 2018
Have 2+ years’ experience in Electronic Manufacturing Service (EMS), thus be well acquainted with how it works in factory.Main job is to deal with material quality issues.-Have knowledge of characteristic of various electrical parts mounting on PCB, e.g., resistor, capacitor, overlay, diode, mechanical parts…etc.-Review Material Inspection Instruction for operator to perform inspection accordingly.-Hold Material Review Board, if defect parts effect/delay production schedule.-Negotiate with supplier/MFG to help provide technician advise/assistance for our factory.Supplier management is also part of my job.-Continuous ImprovementAsk supplier to improve product quality in 8D form, and review the report.-Supplier Quality RatingMonitor IQC data (i.e., LAR, DPPM) and SCAR record to do supplier quality rating.-Supplier Audit/VisitSurvey supplier’s manufacturing capacity, quality system, and factory management.Skill:Continuous improvementData analysisQuality System AssuranceREACH, WEEE, RoHASIPC-610 Show less
-
-
-
-
-
Jan 2016 - Jul 2016
I have two more year experience in traditional industry. Taroko produces safety wearing products and mainly exports to American and European countries. I worked in product development at the beginning, and had the chance to work at the front line serving customers. As much as having the experience of product development, I could provide effective service timely. • Was responsible for customer management, including maintaining customer relationship, introducing new products, and providing customer service.• Finding solution when having customer complaint. • Receive orders, negotiate shipping date with PC if necessary, and arrange shipping work.• Have positive feedback from customer on performance of customer service quality.• Work with other departments to improve sampling process and shortening sampling period. Show less
-
-
-
Apr 2014 - Jan 2016
Was responsible for product development, coordinate related department to build prototype, source local supplier for accessory parts, and arrange test for requested safety regulation certification. • Contact with customer to clarify product requirements.• Coordinate with design department, molding department, coating department and processing department, etc. to build prototype for customers.• Quote to customer after product’s specification/requirement is confirmed.• Source new/alternative supplier that provide component meets special requirements or lower unit price.• Coordinate related departments to do feasibility assessments and execute ECO, when customer has request.• Understand Safety Regulation Certification. Periodically, apply to renew the certificate for test department. In addition, responsible for arranging 3rd party test for developing products. Show less
-
-
Education
-
國立中山大學
Master's degree - Politics, 中國與亞太區域研究所, Institute of China and Asia-Pacific Studies -
國立中山大學
Bachelor's degree, 企業管理學系, Department of Business Management
Community
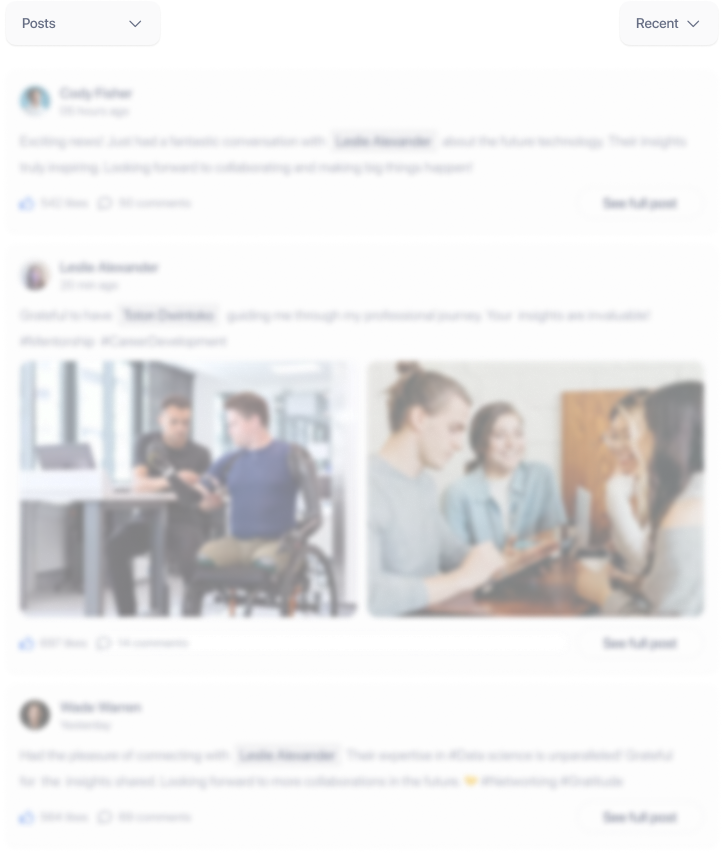