Jessica Stein
Master Production Scheduler at LEIXIR DENTAL GROUP- Claim this Profile
Click to upgrade to our gold package
for the full feature experience.
Topline Score
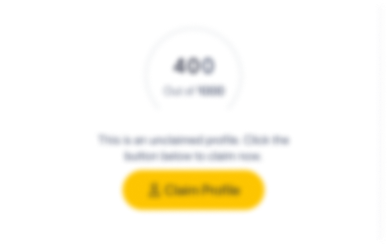
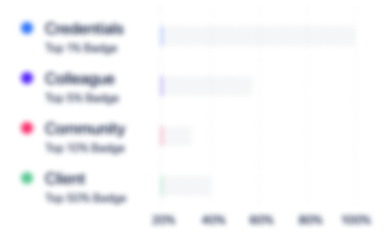
Bio


Experience
-
LEIXIR DENTAL GROUP
-
United States
-
Hospitals and Health Care
-
200 - 300 Employee
-
Master Production Scheduler
-
Jan 2019 - Present
Tampa/St. Petersburg, Florida Area
-
-
-
-
Production Planner II
-
Jul 2018 - Dec 2018
Tampa/St. Petersburg, Florida Area Contract Position Hired to help this company close in Florida and move to Massachusetts. Worked on several projects to clean up outstanding work orders, purchase orders, and sales orders. - Utilized Infor LN ERP system to create project transfers - Coordinated shipments for materials pulled on customer orders - Performed stock checks and material cost checks to provide to customers - Investigated and solved shipping and order discrepancies - Physically counted parts and… Show more Contract Position Hired to help this company close in Florida and move to Massachusetts. Worked on several projects to clean up outstanding work orders, purchase orders, and sales orders. - Utilized Infor LN ERP system to create project transfers - Coordinated shipments for materials pulled on customer orders - Performed stock checks and material cost checks to provide to customers - Investigated and solved shipping and order discrepancies - Physically counted parts and systemically updated locations to insure inventory accuracy - Kept track of and reports on status of open orders to management - Pulled materials to ship for hot orders - Confirmed shipments and pick tickets had accurate information - Ran reports and created excel spreadsheets to provide to management Show less
-
-
-
Custom Manufacturing & Engineering
-
United States
-
Appliances, Electrical, and Electronics Manufacturing
-
1 - 100 Employee
-
Procurement Specialist
-
Feb 2018 - Jul 2018
Pinellas Park, FL Consultant - Sourced new vendors to buy materials from - Negotiated prices and then re-negotiated for higher volume buys - Sendt multiple RFQ's to vendors for pricing and price comparison - Verified several sources to verify best price is given - Reviewed Govgistics website daily for new opportunities to bid on government defense contracts - Created Indented Bills of Materials from legacy drawings - Provided costing and Engineering work up spreadsheets to proposal expert
-
-
-
Leonardo DRS
-
United States
-
Defense & Space
-
700 & Above Employee
-
Material Handler / Expeditor
-
Jul 2017 - Jan 2018
Largo, FL - Moved materials and WIP goods throughout facility and systemically in Oracle ERP - Processed Return to Vendor materials in and out of MRB cage - Performed data entry in computer system in order to track material locations - Ordered and picked materials from stockroom and assigned to specific projects - Prepared shipments including paperwork and computer moves for customer orders as well as inter-organization transfers
-
-
-
Dynatect Manufacturing, Inc.
-
United States
-
Industrial Machinery Manufacturing
-
1 - 100 Employee
-
Engineering Assistant
-
Jun 2016 - Dec 2016
New Berlin, WI Contract Position - Read CAD and Interpreter drawings to calculate labor rates, production times, and material usage for estimation - Entered new part numbers and specifications into Syteline ERP along with BOM and production routes - Created new Bills of Material using CAD drawings and cut lists while updating new part numbers - Ran daily reports to determine and update Engineering status on new orders and drawings to be created - Ran costing reports after entering bill of… Show more Contract Position - Read CAD and Interpreter drawings to calculate labor rates, production times, and material usage for estimation - Entered new part numbers and specifications into Syteline ERP along with BOM and production routes - Created new Bills of Material using CAD drawings and cut lists while updating new part numbers - Ran daily reports to determine and update Engineering status on new orders and drawings to be created - Ran costing reports after entering bill of materials to verify materials are withing margin for profit Show less
-
-
-
Harley-Davidson Motor Company
-
United States
-
Motor Vehicle Manufacturing
-
700 & Above Employee
-
Product Lifecycle Management Coordinator
-
Mar 2016 - Jun 2016
Milwaukee, WI Contract Position
-
-
-
RAFI Group
-
Germany
-
Appliances, Electrical, and Electronics Manufacturing
-
300 - 400 Employee
-
Engineering Assistant
-
Nov 2014 - Dec 2015
Milwaukee, WI Contract Position - Converted all parts from flow chart system to new MRP system - Estimated material usage and production times to determine costs of new projects. - Implemented system for keeping track of tools and test fixtures for specific parts. - Trained Engineering team on standardization of Bills, Routes, Part Numbers and Fixtures - Cleaned up extensive Engineering Change Order database backlog - Helped in shipping, testing, and assembly when there was a need for extra… Show more Contract Position - Converted all parts from flow chart system to new MRP system - Estimated material usage and production times to determine costs of new projects. - Implemented system for keeping track of tools and test fixtures for specific parts. - Trained Engineering team on standardization of Bills, Routes, Part Numbers and Fixtures - Cleaned up extensive Engineering Change Order database backlog - Helped in shipping, testing, and assembly when there was a need for extra help - Researched cost variances and made changes as necessary - Tracked and updated CAR and PAR system - Created Work Instructions for updated system Show less
-
-
-
-
Inside Sales / Expeditor
-
Jun 2012 - Jun 2014
Sussex, WI - Entered sales orders, purchased materials, matched paperwork and proofed for errors - Processed cash receipts and invoices in Sage MAS ERP system - Updated pricing and part number changes, ship dates from acknowledgements, contacted vendors for expedites - Created and monitored reports for backorders, late orders, and shortages while recording in computer system - Assisted in taking physical inventory counts and then researched discrepancies - Assisted with tax audit
-
-
-
McKey Perforating Co.
-
United States
-
Mechanical Or Industrial Engineering
-
1 - 100 Employee
-
Administrative Assistant
-
Jan 2012 - Jun 2012
New Berlin, WI
-
-
-
-
Account Manager
-
Sep 2008 - Oct 2009
West Allis, WI Contract Position - Provided written and verbal quotes for pricing/delivery and MSDS or Spec Sheets to customers as requested - Entered orders received into specific manufacturing schedules while monitoring production times and rescheduling as necessary - Sold electric motors, gears, and their parts via phone, email, and faxed orders - Managed a few large accounts handling all of their orders, acknowledgements, quotes, and follow-up requests - Liason between offsite office and… Show more Contract Position - Provided written and verbal quotes for pricing/delivery and MSDS or Spec Sheets to customers as requested - Entered orders received into specific manufacturing schedules while monitoring production times and rescheduling as necessary - Sold electric motors, gears, and their parts via phone, email, and faxed orders - Managed a few large accounts handling all of their orders, acknowledgements, quotes, and follow-up requests - Liason between offsite office and public warehouse Show less
-
-
-
Western Building Products, Inc.
-
United States
-
Wholesale Building Materials
-
1 - 100 Employee
-
Material Control Coordinator / Purchasing Assistant
-
Oct 2002 - May 2008
Greater Milwaukee Area - Cross trained in several departments as a backup and trained new employees - Assisted the company in changeover from MRP to ERP system - Entered customer orders, purchase orders, RMAs, and inventory information into database - Tracked shortages and backorders contacting vendors when necessary - Utilized daily reports for purchasing and expediting planning; Entered purchase orders and contacted vendors for expediting raw materials - Established new office procedures, ordered… Show more - Cross trained in several departments as a backup and trained new employees - Assisted the company in changeover from MRP to ERP system - Entered customer orders, purchase orders, RMAs, and inventory information into database - Tracked shortages and backorders contacting vendors when necessary - Utilized daily reports for purchasing and expediting planning; Entered purchase orders and contacted vendors for expediting raw materials - Established new office procedures, ordered office supplies, conducted performance reviews Show less
-
-
Education
-
Milwaukee Area Technical College
Associate's degree, Business Administration and Management, Logistics
Community
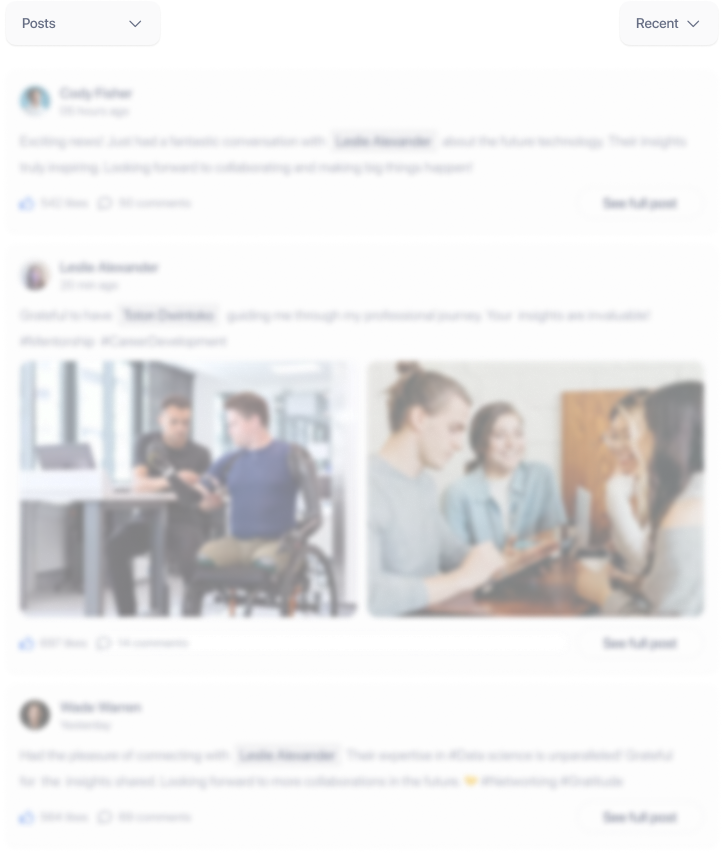