Jessica Eadie
Quality Assurance Manager/QAP at Dycar Pharmaceuticals Ltd.- Claim this Profile
Click to upgrade to our gold package
for the full feature experience.
Topline Score
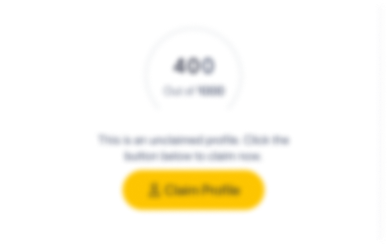
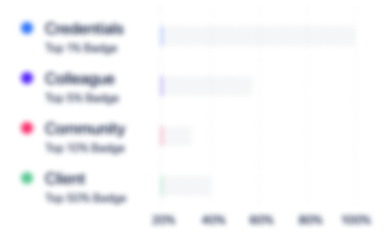
Bio


Experience
-
Dycar Pharmaceuticals Ltd.
-
Canada
-
Pharmaceutical Manufacturing
-
1 - 100 Employee
-
Quality Assurance Manager/QAP
-
Aug 2023 - Present
Canada
-
-
-
Woody Nelson
-
Canada
-
Farming
-
1 - 100 Employee
-
Director Of Quality
-
Aug 2021 - Aug 2023
Nelson, BC -Panel member speaker during Grow Up conference in Edmonton, AB on behalf of the C45 Quality Association May 2023 -Approved Security Cleared, Alternate Responsible Person and Quality Assurance Person based on the Cannabis Act & Regulations -Successfully applied for & obtained sales licenses for dried flower and Cannabis 2.0 products (extract, topical and edibles) to the Canadian recreational marketplace -Successfully applied for & obtained Medical Cannabis sales license for all… Show more -Panel member speaker during Grow Up conference in Edmonton, AB on behalf of the C45 Quality Association May 2023 -Approved Security Cleared, Alternate Responsible Person and Quality Assurance Person based on the Cannabis Act & Regulations -Successfully applied for & obtained sales licenses for dried flower and Cannabis 2.0 products (extract, topical and edibles) to the Canadian recreational marketplace -Successfully applied for & obtained Medical Cannabis sales license for all products Woody Nelson produces -Quality Management System (QMS) creation, implementation from the ground up -Training Program, Sanitation Program, Recall Program, Calibration Program, Pest Control Program and Validation Program creation, implementation, review, and updates as required -Change Management & QMS amendments to ensure compliance -Non-compliance/deviations implementation, review, approval, and follow-up -Review of all testing parameters and CofA’s to ensure products are released based on approved specifications -Creation, review, and approval of Batch/Lot packages of all products for sale to customers or patients based on the QMS & Cannabis Regulations -Risk management review to ensure a scientific based approach to product quality -Deliver presentations to all staff members regarding GMP, Health Canada GPP, and QMS to ensure compliance -Schedule meetings, information sessions, presentations that correspond with quality events, audits, QMS & company values -Co-ordinate deadlines & timelines under the QMS to ensure products can be approved & delivered for sale purposes -Create and ensure job descriptions as relevant and realistic to staffing levels and perform training based on job descriptions -Delegate to QA team members & other department members to ensure compliance to QMS & Health Canada Regulations -Management member for the Health & Safety team, currently hold OFA Level 1 -Perform hiring, firing, review process & improvement for employees under the Quality Department Show less
-
-
-
-
QA Manager
-
Sep 2019 - Jul 2021
Edmonton, Alberta, Canada
-
-
-
-
QA Manager
-
Sep 2018 - Sep 2019
Mission, BC
-
-
Quality Assurance Manager
-
Sep 2017 - Sep 2019
-
-
-
Viridium Pacific
-
Canada
-
Venture Capital and Private Equity Principals
-
Quality Assurance Manager
-
Oct 2017 - Sep 2019
Mission, BC · Approving each lot or batch or product deemed acceptable to international pharmacopoeia standards prior to sale through the verification process of internal auditing and verifying internal SOP's protocol and external laboratory analysis. · Investigating all quality complaints and deterring corrective and preventative measures. · Classifying each quality complaint as a production issue, adverse reaction or other and initiating proper notification and documentation. · Initiating recall… Show more · Approving each lot or batch or product deemed acceptable to international pharmacopoeia standards prior to sale through the verification process of internal auditing and verifying internal SOP's protocol and external laboratory analysis. · Investigating all quality complaints and deterring corrective and preventative measures. · Classifying each quality complaint as a production issue, adverse reaction or other and initiating proper notification and documentation. · Initiating recall procedures and protocol if required with proper notification and documentation. · Ensuring that product, site and equipment is produced, packaged labelled and stored in accordance to the sites sanitation plan. · Quarantined product that was rejected through internal non-conformance or returned from customers will be dispositioned and destroyed under documented SOP's to ensure product is not resold or provided again. · Approve all SOP's, directives, and protocol prior to implementation. · Internally audit and verify SOP's to ensure the quality of products at all steps of the production and to certify that all processes were conducted as per Division 4 of the ACMPR. · Ensure that all staff members are following SOP’s at all times. · Maintain accurate GPP records for the product and ensure that all staff members do so as well. · Oversee and advise on pharmacovigilance activities. · Set up and validate and approve in process inspections. · Set up and approve final inspections. · Ensure samples are retained. · Regular reporting to the minister. · Ensure adherence to the sanitation plan, the status and monthly review of cleaning. · Liaison with Health Canada on matters invoicing the MMJ products. · Liaison with and approve suppliers and vendors. · Training staff and employees on GPP’s and relevant SOP’s. · Continuously improving sanitation systems and programs throughout facility. Show less
-
-
-
Univar
-
Pharmaceutical Manufacturing
-
Quality Assurance Analyst
-
Feb 2017 - Oct 2017
Edmonton, Alberta, Canada • Analyze regional non-conformance and audit data to identify changes in internal and external issues as well as risks and opportunities • Assist in the investigation of non-conformance and CAPA’s using an appropriate root-cause-analysis methodology • Train staff on principles pertaining to Quality Management Systems and associated procedures •Respond to Customer, Supplier or Regulatory requests for Quality related information • Initiate and log non-conformance reports and CAPA… Show more • Analyze regional non-conformance and audit data to identify changes in internal and external issues as well as risks and opportunities • Assist in the investigation of non-conformance and CAPA’s using an appropriate root-cause-analysis methodology • Train staff on principles pertaining to Quality Management Systems and associated procedures •Respond to Customer, Supplier or Regulatory requests for Quality related information • Initiate and log non-conformance reports and CAPA reports in the system • Lead non-conformance investigations in partnership operations, supply chain and sales • Track completion of corrective actions, trend and analyze non-conformance data • Effectively communicate the non-conformance investigation process and results to internal and external clients • Train employees on the reporting processes for non-conformance matters • Engage various internal and external stakeholders (including suppliers, operations, supply chain, sales) in continuous improvement initiatives Show less
-
-
-
Saf-T-Pak
-
Canada
-
Packaging and Containers Manufacturing
-
1 - 100 Employee
-
Assistant Quality Manager
-
Sep 2014 - Jan 2017
Edmonton, Alberta, Canada . Conduct quality checks using established methods and operating procedures . Aid and perform R&D projects, lab experiments and maintain lab note books . Work with vendors to maintain the QMS and a quality product, aid in evaluation of NCR/CAR’s to provide the best results in correction and prevention of issues to prevent reoccurrences . Provide guidance to customers/employees with products and evaluation of quality attributes from customer complaints and in house quality methods … Show more . Conduct quality checks using established methods and operating procedures . Aid and perform R&D projects, lab experiments and maintain lab note books . Work with vendors to maintain the QMS and a quality product, aid in evaluation of NCR/CAR’s to provide the best results in correction and prevention of issues to prevent reoccurrences . Provide guidance to customers/employees with products and evaluation of quality attributes from customer complaints and in house quality methods . Perform general lab maintenance and ensure testing occurs in accordance with Saf-T-Pak procedures and Good Laboratory Practices. . Maintain and Archive QA Quality Records. . Investigate & follow up on consumer complaints. . Assist with Quality Management System implementation . Monitor/Audit process control and manufacturing compliance with processing requirements per Saf-T-Pak procedure. Conduct internal audits as needed based on responsibility for the audit area . Follow Non-conforming product procedures in the event of a deviation from established processes and procedures. . Take corrective action to correct deficiencies identified through audits, deviations or other observations. . Maintain records of QMS activities in accordance with Saf-T-Pak's Quality Manual and procedures to provide objective evidence of compliance (i.e. Training records, inspection records). . Author/Maintain Validation Master Plan . Author Test Plans including those for IQ, OQ, PQ activities and support their execution . Support team members to develop suitable Test Plans & Test Methods . Knowledge of and certification of the current regulations for the transportation of dangerous goods in the US, UK and Canada (IATA, Division 6.2, Class 9) Show less
-
-
-
-
Quality Assurance Specialist
-
Oct 2013 - Sep 2014
Morinville, Alberta, Canada *Testing of raw material, in process material and finished product. *Collect, analyze and retain samples from raw materials, in process and finished products. *Testing includes PV, pH, water activity, toxin testing, and NIR. *Testing for protein, moisture, fat, ash, fiber in raw materials. *Environmental monitoring by swabs and ATP testing. *Sampling for salmonella, clostridium, yeast/mould, TC, e. coli, HPC, SPC and more. *Investigation of issues that relate to… Show more *Testing of raw material, in process material and finished product. *Collect, analyze and retain samples from raw materials, in process and finished products. *Testing includes PV, pH, water activity, toxin testing, and NIR. *Testing for protein, moisture, fat, ash, fiber in raw materials. *Environmental monitoring by swabs and ATP testing. *Sampling for salmonella, clostridium, yeast/mould, TC, e. coli, HPC, SPC and more. *Investigation of issues that relate to HACCP, food safety, and GMP's. *Knowledge of EU, FDA regulations, HACCP principles and GMP's. *Working with and communicating with all departments, senior management and QA team members. Show less
-
-
-
Granny's Poultry Cooperative Ltd.
-
Canada
-
Food and Beverage Manufacturing
-
1 - 100 Employee
-
HACCP Coordinator
-
Apr 2013 - Sep 2013
Blumenort, Manitoba, Canada * Review, edit, and maintain the Pre-requisite Program, CCP’s, HACCP Plans, SOP’s and other process controls in the facility * Use of the FSEP and MOP in daily activities * Update, implement, and distribute procedures, programs, and documents * Provide training/orientation to existing/new employee’s on HACCP concepts and General Food Hygiene * Lead, coordinate, and conduct department meetings * Lead and coordinate HACCP meetings with facility Supervisors and CFIA *… Show more * Review, edit, and maintain the Pre-requisite Program, CCP’s, HACCP Plans, SOP’s and other process controls in the facility * Use of the FSEP and MOP in daily activities * Update, implement, and distribute procedures, programs, and documents * Provide training/orientation to existing/new employee’s on HACCP concepts and General Food Hygiene * Lead, coordinate, and conduct department meetings * Lead and coordinate HACCP meetings with facility Supervisors and CFIA * Cooperate and work with the CFIA to implement changes to the Pre-requisite Program and other documents * Other duties include filing, organization, time management, verbal and written communication, team work, use of Microsoft Office: Word, Outlook, Excel, PowerPoint, Visio * Report to Technical Services Manager and Supervisor Show less
-
-
-
Airmaster Signs
-
Canada
-
Manufacturing
-
1 - 100 Employee
-
Executive Assistant
-
Feb 2013 - Apr 2013
Phone calls, emails, document organization, data entry, customer listings/contact listings, general office duties
-
-
-
ALS Environmental Ltd
-
United Kingdom
-
Environmental Services
-
200 - 300 Employee
-
Lab Assistant 2
-
Aug 2010 - Sep 2011
* Lab duties include: MF, MPN, Quanty-Tray, HPC, 1-2 Tests, shelf-life, API strips, sterility testing and reporting, Listeria-Rapid, Salmonella-Rapid, CFIA testing, HACCP testing, yeast and mould test, E.coli/ Clostridium/Giardia identification * Other duties include: media preparation, autoclave use, calibration of equipment, use of LIMS and Microsoft Office programs, and QC analysis * QA/QC done on samples, lab materials, equipment, review of reports and results obtained… Show more * Lab duties include: MF, MPN, Quanty-Tray, HPC, 1-2 Tests, shelf-life, API strips, sterility testing and reporting, Listeria-Rapid, Salmonella-Rapid, CFIA testing, HACCP testing, yeast and mould test, E.coli/ Clostridium/Giardia identification * Other duties include: media preparation, autoclave use, calibration of equipment, use of LIMS and Microsoft Office programs, and QC analysis * QA/QC done on samples, lab materials, equipment, review of reports and results obtained, non-conformance reporting and investigation * Safety Officer for Microbiology lab, attended meetings, meeting minutes to Safe Manitoba, worked with co-workers and management to correct and prevent issues in the workplace * SOP correction, writing, evaluation, and use * Training, organization, multi-tasking, aseptic technique, monitoring/verification of equipment and materials, communication, documentation, and investigational skills Show less
-
-
Education
-
University of Manitoba
Bachelor of Science - BS, Microbiology, General -
Red River College
Advanced Diploma, QA/QC in the Pharmaceutical Industry -
The University of British Columbia
Micro-credential, Regulatory Affairs
Community
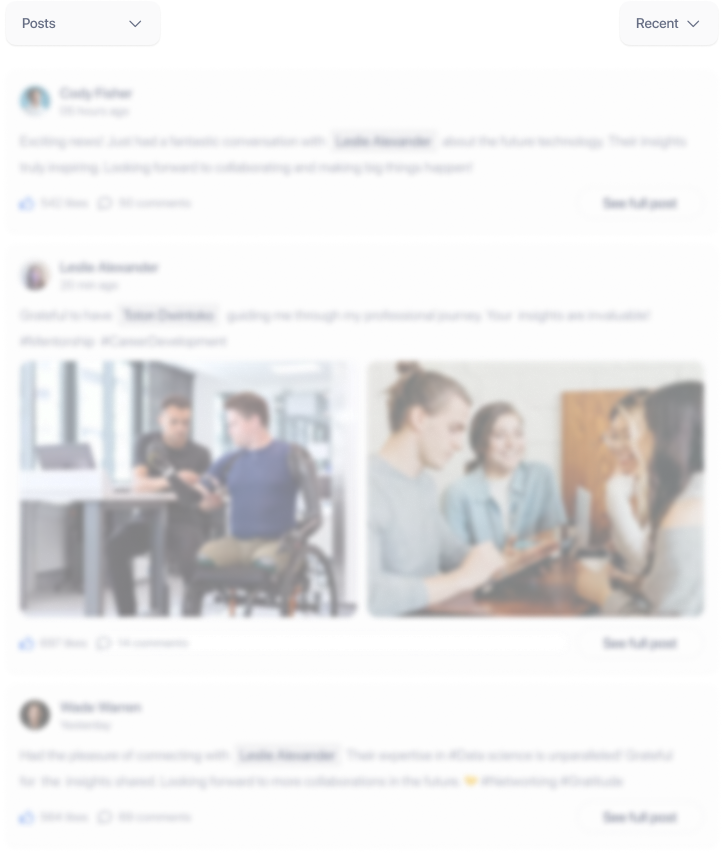