Jesse Riegle
Technical Services Manager at Box On Demand- Claim this Profile
Click to upgrade to our gold package
for the full feature experience.
Topline Score
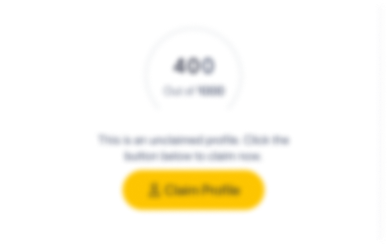
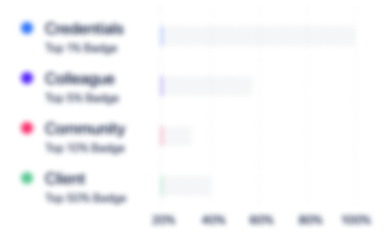
Bio
0
/5.0 / Based on 0 ratingsFilter reviews by:
Experience
-
Box On Demand
-
United States
-
Packaging & Containers
-
1 - 100 Employee
-
Technical Services Manager
-
Jan 2017 - Present
Battle Creek, Michigan
-
-
-
Baker Perkins
-
United Kingdom
-
Machinery Manufacturing
-
100 - 200 Employee
-
Global Field Service Engineer
-
Sep 2014 - Jan 2017
Grand Rapids, Michigan Providing support for new and existing food process equipment that includes installation, start-up, troubleshooting, inspection, training, repair and system optimization. Duties Include: Installation and commissioning of baking equipment for the biscuit, snack and cracker industries. This includes the installation (and modification) of PLC software and electrical control systems for said equipment, and subsequent customer training on correct operation and maintenance. After-care… Show more Providing support for new and existing food process equipment that includes installation, start-up, troubleshooting, inspection, training, repair and system optimization. Duties Include: Installation and commissioning of baking equipment for the biscuit, snack and cracker industries. This includes the installation (and modification) of PLC software and electrical control systems for said equipment, and subsequent customer training on correct operation and maintenance. After-care responsibilities for legacy installations include system diagnosis, inspection of problems and failures, replacement or repair of parts, pre-failure component inspections, testing and adjustment of baking equipment as needed. Perform oven safety inspections on customer’s equipment in compliance with OSHA requirements. Responsible for promoting the full range of the Baker Perkins product line and aftermarket solutions. Qualifications: Experience in performing the installation, start-up, training and troubleshooting of complex electrical/electronic and mechanical control systems. Ability to effectively communicate verbally and in writing with both customers and internal team members on a technical and commercial level. Knowledge of cookie, cracker and confectionery equipment. Able to understand AB PLC programs, and understand AB Control Logix systems. Proficiency in Microsoft Office programs and AutoDesk packages and familiarity with State, Federal and various equipment safety standards such as OSHA, FM, NFPA, and ANSI. Capable of travel internationally. Education and experience: Electrical and mechanical repair skills of industrial equipment. Four years technical training. PLC and electrical training and repair experience. Show less
-
-
-
Kellogg Company
-
United States
-
Manufacturing
-
700 & Above Employee
-
Process Manager
-
Mar 2013 - Aug 2014
Battle Creek, Mi
-
-
-
PulverDryer USA, Inc.
-
United States
-
Process Operations Manager
-
May 2010 - Mar 2013
Springfield, Michigan • Provide general supervision over production staff. • Recognize and solve problems affecting production including schedules, staff, quality, and order of production line. • Ensure customer requirements are met. • Identify and resolve issues with materials, processes, or equipment. Recommend changes to improve quality, throughput, operating conditions and cost reduction. • Provide day to day guidance and oversight of subordinates; actively work to identify problem areas and take… Show more • Provide general supervision over production staff. • Recognize and solve problems affecting production including schedules, staff, quality, and order of production line. • Ensure customer requirements are met. • Identify and resolve issues with materials, processes, or equipment. Recommend changes to improve quality, throughput, operating conditions and cost reduction. • Provide day to day guidance and oversight of subordinates; actively work to identify problem areas and take corrective action as well as promote and recognize performance. • Maintain project timelines and task personnel appropriately for timely completion of scheduled operations. Ensure proper recording of all operational and machine data. • Communicate engineering changes and implement design improvements throughout the production process. • Write and review operation reports, papers, and other records for clarity, completeness and accuracy. • Ensure the correct and timely distribution of processed product. • Ensure compliance to all safety and health regulations as established by OSHA/MIOSHA guidelines. • Oversee and conduct training of new or existing employees. • Interact with outside vendors and departments to research equipment modifications and expedite repair. • Writes/approve Maintenance Work Requests, Engineering and Facility Change Requests, and Purchase Requisitions. • Perform PulverDryer operation demonstrations for clients as requested. • Install PulverDryer units at customer facilities worldwide. • Ability to proficiently trouble shoot and repair or facilitate repair of all mechanical issues related to any equipment involved in the PulverDryer process. • Oversee the installation and operation of PulverDryer drying systems during field projects and new customer installations. • Troubleshoot and repair mechanical and electrical issues including Programmable Logic Control and Variable Frequency Drive problems during installation and operation. Show less
-
-
-
PulverDryer USA
-
United States
-
Sr. Field Service Technician
-
Mar 2007 - Mar 2013
• Responsible for the installation and operation of PulverDryer drying systems during field projects and new customer installations. • Support in-house research and development activities to include process development, material handling, machine operations and industrial maintenance. • Provide assembly and installation of machine components and auxiliary equipment for the operation of PulverDryer drying systems. • Troubleshoot and repair mechanical and electrical issues including… Show more • Responsible for the installation and operation of PulverDryer drying systems during field projects and new customer installations. • Support in-house research and development activities to include process development, material handling, machine operations and industrial maintenance. • Provide assembly and installation of machine components and auxiliary equipment for the operation of PulverDryer drying systems. • Troubleshoot and repair mechanical and electrical issues including Programmable Logic Control and Variable Frequency Drive problems during installation and operation. • Proficiency in troubleshooting and programing Reliance and Baldor drives. • Train and supervise customer personnel in operation, troubleshooting, service and maintenance of machinery. • Advanced knowledge of augers, high speed belts, metering hoppers, pumps, hydraulics, pneumatics, diesel and electric motors. • Proficiency in Microsoft Office products to include Excel and Word. • Daily activity report writing to include power use graphing and machine data collection downloads. • Blueprint reading. Show less
-
-
-
Johnstown Township Fire Department
-
United States
-
Firefighter / Medical First Responder
-
Jun 2002 - Dec 2009
-
-
Education
-
Allen Bradley
PLC 1 programming and troubleshooting, RSLogix -
Allen Bradley
PLC 2 programming and troubleshooting, RSLogix -
Kalamazoo Valley Community College
Technical, Industrial Technology/Technician -
Barry County Fire Fighter School
Fire science, Fire Science/Fire-fighting -
Kellogg Community College
Assoicates, Science, Firefighter 1 and 2 Medical First Responder -
Kellogg Community College
Associates, Science
Community
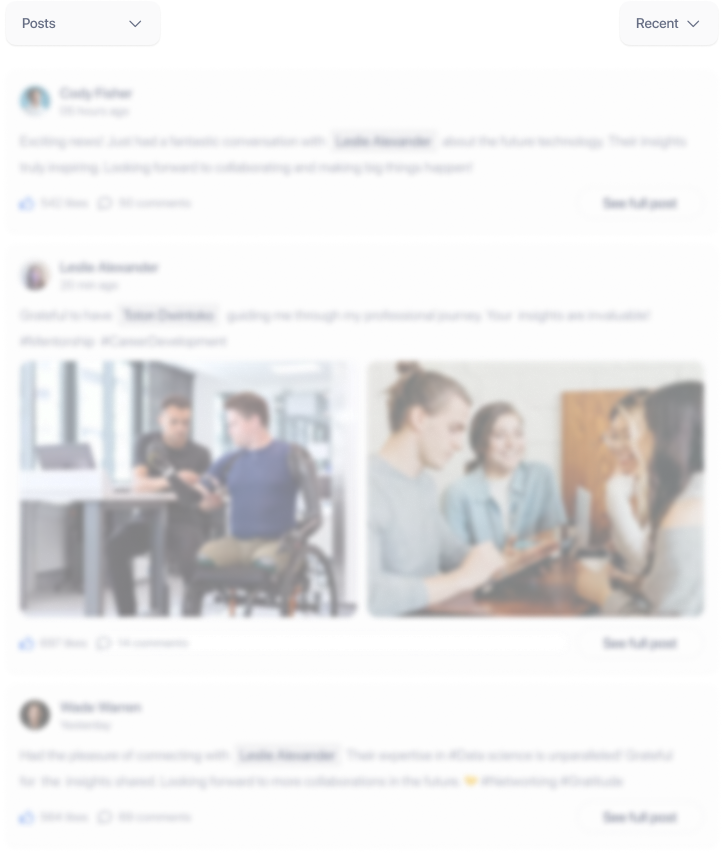