Jerry Barley
Quality Inspector at Tyonek Services Group, Inc.- Claim this Profile
Click to upgrade to our gold package
for the full feature experience.
Topline Score
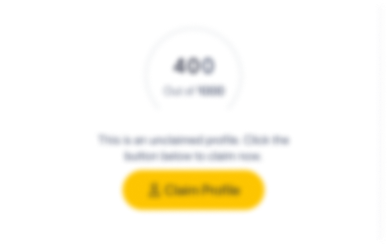
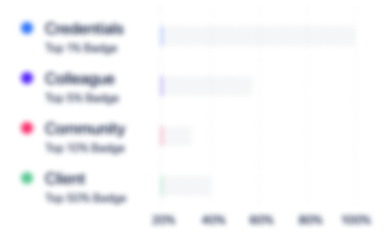
Bio


Experience
-
Tyonek Services Group, Inc.
-
United States
-
Business Consulting and Services
-
1 - 100 Employee
-
Quality Inspector
-
Oct 2020 - Present
Tyonek Services Group Incorporated (TSGI) operates the Region Aircraft Phase Sustainment Center (RAPSC) in Marana, AZ conducting sustainment maintenance for various rotary-wing aircraft for the National Guard Bureau (NGB) to contract specification. LEADERSHIP & MANAGEMENT: Assists RAPSC Site Lead with management of the contract, workforce performance, and customer requirements. Works diligently with Government Ground Flight Representative (GGFR) and Contracting Officer’s Representative (COR) to execute the contract to support customer requirements. Solely responsible for the quality management, safety, and training programs on-site. QUALITY MANAGEMENT/ASSURANCE: Provide aircraft quality control and technical inspection services in compliance with governing contract documents and site ground operating procedures. Executes and evaluates site quality control plan to achieve standards outlined in the quality assurance surveillance plan (QASP) and aircraft quality management systems (QMS) TRAINING AND SAFETY: Identify any shortcomings in operations and safety discrepancies. Creates and instructs classes related to the contract, ground operating procedures, and applicable regulations. SELECTED ACCOMPLISHMENTS: *Identified and corrected shortfalls in aircraft maintenance and service quality before they were an issue. This resulted in zero corrective action reports (CAR) from the customer. *Advised site lead on maintenance trends, equipment inspection, and supply shortfalls. Minimized negative impact on service delivery times and supply chain availability. *Achieved an overall “Highly Effective” rating on performance reviews as site quality inspector. * Exercised quality control and technical inspection expertise on over 40 Phase Maintenance Inspections (PMI) and 49 total major maintenance events on H-60 series aircraft. Show less
-
-
-
Jackie's Aircraft Certification Specialist LLC
-
United States
-
Certification Program Manager
-
Jan 2018 - Jan 2022
Executed technical oversight and engineering management for five to ten projects per month on aircraft modification/certification projects on general aviation and special mission aircraft, including five specialized test bed aircraft. Provide program management services for Supplementals Type Certifications and Field approvals. - Fostered good vendor relations and customer service satisfaction for aircraft certification services to military, air ambulance, defense contractor, and other clients including U.S. Naval Air Systems Command, Raytheon Missile Systems, and the FAA on contracts worth between $2K and $300K. - Strategic facilitation with the FAA to arrange compliance audits for aircraft, subsystems, and documentation. - Recognized and corrected discrepancies in subcontractor-provided supplies and equipment, saving the company $94K and weeks of downtime. Show less
-
-
-
-
Quality Control Manager
-
2016 - 2017
Led 150 personnel and provided quality control over the maintenance of 25 UH-60 helicopters. Planned, developed, and implemented quality control programs, communicating standards to be met and ensuring maintenance personnel understood established requirements and guidelines. Ensured all maintenance activities complied with applicable written guidance. Trained, qualified, and oversaw new technical inspectors. Reviewed aircraft records and forms to ensure currency and accuracy. Identified and corrected unsatisfactory conditions or elements and provided trusted advice to executive leadership on complex safety and quality control issues. Planned and monitored workflow based on shop capacity and mission priorities, adjusting jobs in progress to adapt to changing circumstances. Determined, assessed, and evaluated the status of jobs in progress, time to complete assigned jobs, and availability and adequacy of materials and tools and established priorities. Prepared production plans for assigned projects and operations, integrating end user requirements, engineering data designs, and technical specifications. Established Quality Control Standard Operating Procedures that streamlined quality standards and established inspection and enforcement processes that enabled maintenance program certification in less than 90 days. Corrected shortfalls in recordkeeping processes, increasing aircraft availability and saving $367K. Show less
-
-
-
-
Aircraft Maintenance Supervisor
-
2014 - 2016
Led 20 technicians in supervising mission-essential maintenance for five UH-72 and seven UH-60 helicopters worth $11M combined. Maintained accountability for $1.2M in specialized equipment. Planned and managed work assignments, estimating maintenance-related labor hours and expediting or adjusting operations as required to adapt to evolving circumstances. Monitored work in progress and evaluated time available to complete jobs and the availability of materials and tools. Coordinated with the FAA to arrange interviews for Airframe and Powerplant Certification candidates, enabling both military maintainers and civilian contractors to pursue certification. Advised on procurement and supply issues in order to meet material requirements and operational schedules. Led the unit’s transition between two different aircraft types, establishing schedules and milestones for aircraft logbook and historical records transition, aircraft inspection technicians, and safety of flight certifications in order to enable the progression from an FAA-approved maintenance program to a fully certified Army Unit Level Logistics System–Aviation (ULLS-A). Orchestrated the turn-in of excess equipment, including $4M in materiel and five helicopters, as well as associated items worth more than $27M. Show less
-
-
-
-
Aircraft Maintenance Supervisor
-
2012 - 2014
Supervised 30 personnel, directing the maintenance of up to 30 helicopters valued at $122.5M combined and managing specialized equipment worth more than $2M. Managed the organization’s Flight Operations, Tactical Operations, Safety and Standards, Supply, Communications, and Electronics Sections. Developed and implemented training and development plans to increase workforce ability to support no-notice and dynamic operations, conducting regular professional development sessions. Ensured proper aircraft recordkeeping, maximizing airframe readiness for essential missions. Applied composite risk management principles to ensure zero accidents or injuries. Managed job flow and task assignments according to work center capacity and organizational goals and objectives, adapting assignments and resource allocations to dynamic circumstances. Maintained a 100% readiness rating during the unit’s transition between two different airframes. Managed maintenance operations at four different locations in austere conditions, resulting in a 100% mission success rate for medical evacuation flights. Served as Crew Chief on 72 combat medical evacuation missions, successfully evacuating 51 casualties in dynamic and high-risk operations. Overhauled equipment accountability processes and practices in order to prevent the potential loss of specialized equipment worth more than $350K during unit relocation. Show less
-
-
-
-
Quality Control Manager | Technical Inspector
-
2010 - 2012
Led 10 personnel and served as technical inspector, evaluating the work of 80 military personnel and 15 contractors in a rapidly deployable aircraft maintenance unit supporting UH-60 and CH-47. Performed quality control functions and technical inspections of up to 51 aircraft worth $980M combined. Trained and certified more than 30 technical inspectors. Enforced aircraft maintenance quality standards to ensure airworthiness and mission readiness. Reviewed and updated aircraft logbooks and historical records and ensured timely compliance with technical directives. Oversaw the teardown and reassembly of aircraft for shipment. Supervised the accountability and tracking of more than 5K aircraft components. Monitored and evaluated work progress, adjusting task assignments and resource allocations to ensure alignment with mission requirements and adapt to dynamic situations. Established Standard Operating Procedures that enabled the timely and safe transition of the organization into a multifunctional aviation task force. Played a critical role in the recovery of seven damaged aircraft from remote locations in hazardous conditions in Afghanistan. Show less
-
-
Education
-
Everglades University
Bachelor of Science - BS, Aviation/Airway Management and Operations -
Thomas Edison State University
Associate of Science - AS, Aeronautics/Aviation/Aerospace Science and Technology, General
Community
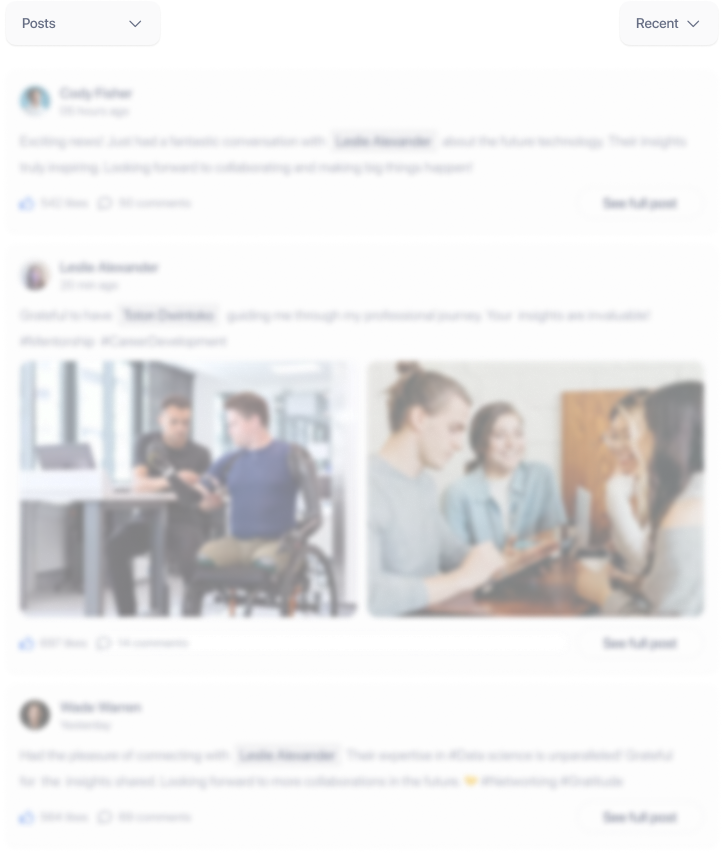