Jerome Ty
Senior Clinical Supply Manager at RAPT Therapeutics- Claim this Profile
Click to upgrade to our gold package
for the full feature experience.
-
Chinese -
-
Tagalog -
Topline Score
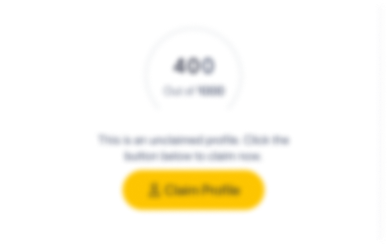
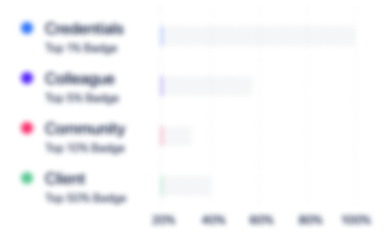
Bio

Kevin Okimura
From my experience, Jerome is a supply chain professional that has the ability to grow into a key asset for a company in many areas of supply chain management. While working at Portola, I was in the external manufacturing group while Jerome was in global supply chain management. Once trained and acquainted with the scope of work, Jerome is a business partner that you can always trust to work collaboratively with high effort. With a passionate fervor he will ensure he will do everything within his power to answer a query, tackle a problem, move a process forward or make improvements to systems. He is a team player that is a great collaborator and an enjoyable colleague to work with.

Zane Howard
Jerome is a high energy, hard worker. He was a great support to me in my marketing role and always was willing to roll up his sleeves to get the job done. I enjoyed working with Jerome at Columbus Foods.

Kevin Okimura
From my experience, Jerome is a supply chain professional that has the ability to grow into a key asset for a company in many areas of supply chain management. While working at Portola, I was in the external manufacturing group while Jerome was in global supply chain management. Once trained and acquainted with the scope of work, Jerome is a business partner that you can always trust to work collaboratively with high effort. With a passionate fervor he will ensure he will do everything within his power to answer a query, tackle a problem, move a process forward or make improvements to systems. He is a team player that is a great collaborator and an enjoyable colleague to work with.

Zane Howard
Jerome is a high energy, hard worker. He was a great support to me in my marketing role and always was willing to roll up his sleeves to get the job done. I enjoyed working with Jerome at Columbus Foods.

Kevin Okimura
From my experience, Jerome is a supply chain professional that has the ability to grow into a key asset for a company in many areas of supply chain management. While working at Portola, I was in the external manufacturing group while Jerome was in global supply chain management. Once trained and acquainted with the scope of work, Jerome is a business partner that you can always trust to work collaboratively with high effort. With a passionate fervor he will ensure he will do everything within his power to answer a query, tackle a problem, move a process forward or make improvements to systems. He is a team player that is a great collaborator and an enjoyable colleague to work with.

Zane Howard
Jerome is a high energy, hard worker. He was a great support to me in my marketing role and always was willing to roll up his sleeves to get the job done. I enjoyed working with Jerome at Columbus Foods.

Kevin Okimura
From my experience, Jerome is a supply chain professional that has the ability to grow into a key asset for a company in many areas of supply chain management. While working at Portola, I was in the external manufacturing group while Jerome was in global supply chain management. Once trained and acquainted with the scope of work, Jerome is a business partner that you can always trust to work collaboratively with high effort. With a passionate fervor he will ensure he will do everything within his power to answer a query, tackle a problem, move a process forward or make improvements to systems. He is a team player that is a great collaborator and an enjoyable colleague to work with.

Zane Howard
Jerome is a high energy, hard worker. He was a great support to me in my marketing role and always was willing to roll up his sleeves to get the job done. I enjoyed working with Jerome at Columbus Foods.
0
/5.0 / Based on 0 ratingsFilter reviews by:
Credentials
-
Supply Chain Management
California State University, East Bay
Experience
-
RAPT Therapeutics
-
Biotechnology Research
-
100 - 200 Employee
-
Senior Clinical Supply Manager
-
May 2023 - Present
-
-
-
Coherus BioSciences
-
United States
-
Biotechnology Research
-
200 - 300 Employee
-
Senior Supply Chain Manager
-
Jul 2022 - Mar 2023
Responsible for leading Supply Chains role in helping implement (ground-up) live ERP system in collaboration with Accounting, Quality, Procurement, IT and Finance in accordance with cGMP/cGXP/SOX controls. Successfully implemented system from single product company to a multi-product company. Primary system used: Oracle • Developed standardized operating procedures and work instructions for daily use of Oracle. • Act as the liaison between the Technical Operations (Supply Chain, Manufacturing and Quality) and Accounting to reflect accurate reporting of virtual manufacturing, material movements and inventory balances are aligned with GMP/GXP/Financial audit controls. • Lead Supply Chain group in developing and standardizing inventory procedures for month-end closes. • Maintain Coherus inventory records to ensure real time accurate reporting of clinical and commercial inventory through the completion of daily transactions including stock transfers, work orders, inventory and adjustments and disposals. • Created Purchase Orders in Oracle for Coherus Raw Materials, Drug Product and Finished goods along with invoice approvals for payments to CMOs. • Subject Matter Expert (SME) for Oracle Inventory and Financial closes. Show less
-
-
-
Puma Biotechnology, Inc.
-
United States
-
Biotechnology Research
-
100 - 200 Employee
-
Global Supply Chain Manager
-
Jul 2020 - Jun 2022
Responsible for the leadership and management of global supply chain activities in support of commercial and clinical development programs and registration of Puma drug candidates. Oversaw contract manufacturing operations related to packaging, labeling, inventory and distribution drug supporting all of Puma Biotechnology drug candidates through the oversight of multiple Contract Manufacturing Operations (CMOs) and related distribution providers globally. Primary System Used: Oracle • Lead Supply Chain group in developing and executing supply plans to patients. • Support manufacturing (API/DP), packaging and labeling operations (FP) within our CMOs. • Achieve order fulfilment target goals with strategic partners. • Manage global distribution networks, 3PLs and development of logistics strategies. • Subject Matter Expert (SME) for Oracle R13 Inventory and Financial closes. • Build, lead and manage an effective supply chain organization by coaching and mentoring. Show less
-
-
-
Portola Pharmaceuticals
-
United States
-
Pharmaceutical Manufacturing
-
1 - 100 Employee
-
Senior Supply Chain Analyst
-
Mar 2020 - Jun 2020
Execute inventory and material management activities for entire Global Supply Chain team for both commercial and clinical operations. Primary system used: Oracle • Implement and support the current GMP Inventory Management System.• Achieve month end inventory reconciliation at 95% and above with all our CMO’s for entire network.• Responsible for leading raw material planning for Drug Substance outsourced manufacturing.• Responsible for Master Data Management setups which includes BOM’s, Recipes, Formulas, Routing for both Biologics and Small Molecule organizations. • Oversight of CMO inventory control, process and procedures.• Subject Matter Expert (SME) and Business Process Owner (BPO) for Oracle R13 – Material Management. Show less
-
-
Supply Chain Analyst
-
May 2018 - Mar 2020
-
-
Global Supply Chain Specialist - Contractor
-
Mar 2017 - Apr 2018
-
-
-
Perricone MD
-
Personal Care Product Manufacturing
-
1 - 100 Employee
-
Supply Chain Manager - Consultant
-
Dec 2016 - Mar 2017
Analyzed, managed, planned FG KIT assembly activities with 3PL’s for high volume and strategic customers. Led formal process for establishing communications for all North America Perricone team. Primary system used: Great Plains • Managed strategic relationship with 3PL’s to meet sales demand of $35MM annually for 165 Perricone SKUS’s. • Created work order and BOM information flow for production assembly within internal/external team. • Provided new product development for Supply Chain support in 11 successful SKU’s launches equaling to $12.5MM in FY2017Q1. • Created KIT Assembly Tool for internal business communication scope. Show less
-
-
-
Genentech
-
United States
-
Biotechnology Research
-
700 & Above Employee
-
Supply Chain Specialist
-
Apr 2016 - Dec 2016
Analyze, manage, plan and responsible for end to end API Drug Substance material activities linking Small Molecules Contract Manufacturer Organization to Roche Global Internal Supply Chain Networks. Support the Global Order Management Genentech/Roche process for Material Management. Primary system used: SAP/R3/BW • Act as the logistics link between Small Molecule External Manufacturing the Contract Manufacturing Organization (CMO) and Roche plants and logistics functions and responsible for the detailed on time inbound/outbound flow of material. • Perform necessary material movements in SAP to ensure on time inbound and outbound flow of material to the CMO. • Manage inventory at CMO and responsible for accuracy of inventory records and status in Genentech’s ERP system for all GNE-owned material. • Monitor outbound shipping schedule to ensure on time fulfillment of orders in collaboration with different parties (CMO, GNE transportation, freight forwards, etc.) to resolve any gaps that are occurring and coordinate required changes with the CMO. • Perform analysis regarding supply/demand and capacity issues. • Support data analysis in preparation for management meetings such as S&OP and generation of weekly metrics. Show less
-
-
-
Nestlé
-
Switzerland
-
Food and Beverage Services
-
700 & Above Employee
-
Commercialization Project Manager
-
Feb 2016 - Apr 2016
Managed cross-functional innovation and renovation projects to support annual Nestle Dreyer's goals for incremental innovation revenue, improved consumer acceptance of existing products, cost savings and productivity targets. • Commercialization project management for innovation, renovation, cost savings and productivity projects. • Lead and manage initiatives through the project life cycle: scope definition, analysis of alternatives, development, industrialization, launch/start-up, post launch and close-out. • Manage cross-functional project teams: Sales, Marketing, Intelligence, Innovation Brand Marketing, Brand Finance, Product Development (Process Engineer/Pack Engineer), R&D, Manufacturing and Supply Chain. • Assume accountability for key project deliverables: schedule, budget/P&L, scope and success criteria. Show less
-
-
-
Columbus Foods
-
United States
-
Food and Beverage Manufacturing
-
1 - 100 Employee
-
Supply Planning Manager
-
Apr 2012 - May 2015
Reported to the VP of Supply Chain and responsible for decisions on purchases of raw material requirements, packaging components, scheduling and logistics. Managed two direct reports. Primary system used: Adage (Oracle-based system). ● With the support of 2 direct reports (Materials Coordinator and Supply Chain Analyst), secured raw material supply for weekly production requirements, developed capacity supply plan and responsible for material management/inventory levels for all production facilities. ● Maintained master material plan and designed/implemented new tools to optimize material flow, establishing lead times/safety stocks to ensure material availability and accuracy which reduced loss of sales from CY2013 to CY2014 by 10%. ● Led weekly S&OP meetings for “Big 3” customers (Costco/Trader Joe/Safeway) sales requirements, projected volume, promotions and sales forecast. ● Instrumental in leading customer-critical projects/initiatives, including CY2014 data synchronization project (via 1SYNC Global Data Network) for Wal-Mart/Target/Kroger. ● Manage master data and created new data management tool and process for support in growing business and increased demand for Accurate Data Management Information specs. ● Received continuous and extensive training from the VP of Supply Chain on developmental concepts such as team management/motivation, as well as technical principles such as demand-chain, measurement methodologies, S&OP design/implementation, etc. Show less
-
-
-
Bemis Company, Inc.
-
Switzerland
-
Packaging and Containers Manufacturing
-
700 & Above Employee
-
Supply Chain Anayst
-
Oct 2010 - Mar 2012
Analyzed, managed, and planned production activities including assessing raw material supply, ownership of bill of materials, production performance and customer requirement for shipping releases and manufacturing. Primary systems used: Data3 AS400 and Biz Warehouse/SAP ● Led daily production meetings for Operations, Printing, QC/QA, Logistics, Warehousing Departments and Service Floor employees which resulted in increase of 5.5% OEE in Newark plant from CY2010 to CY2011. ● Created/maintained raw material master forecast which resulted in reduction of production stock-outs by 10% in CY2011. ● Developed new tool for Bill of Material creation resulting in reduction of material waste and allocation efficiency by 5%. ● Identified and screened potential raw material suppliers for alternative solutions with our high volume resins which resulted in spec deviations of 2%. Show less
-
-
-
Bayer
-
Chemical Manufacturing
-
700 & Above Employee
-
Buyer/Planner
-
Apr 2010 - Oct 2010
Managed a portfolio of GMP raw materials to include forecasting, planning, purchasing, delivery, receipt, release, FIFO consumption, reserves/scrap and disposal. Primary system used: SAP R3 ● Responsible for 120 high value raw materials ($40MM). ● Drove new QCRM process for material evaluation within internal stakeholders. Tool allowed the Planning group to have visibility to capture accurate, real-time data - and improved collaboration and accountability throughout internal groups. ● Maintained scorecard with KPI that reported department, supplier and internal business partner performance. Show less
-
-
-
The Clorox Company
-
United States
-
Consumer Goods
-
700 & Above Employee
-
Sr. Sourcing Analyst
-
Dec 2006 - Jan 2010
Managed global spend analytics and execution, created e-Sourcing events, supported multiple commodity packaging buyers (plastic & printed), and reporting processes through cross functional collaboration. Primary system used: SAP. ● Expanded diverse supplier base and created diverse mandatory category profiles to support $20MM initiative of Clorox packaging diverse spend in FY09. ● Developed/delivered training on economic order quantities resulting in cost savings of 2% for business units across network ● Supported creation of global category strategies. Collaborated with global owners to gather spend data by region and division ● As a Senior Sourcing Analyst for the Packaging team from 2007 to 2008: o Involved in $1.5MM cost savings in Global Corrugate Sourcing in FY08 o Developed, supported and reported KPI’s in addition to supporting development and execution of sourcing strategies, projects, and initiatives; o Provided analytical support for $700M packaging spend including savings calculations and analysis; o Created print pack sourcing projects template and SAP analytical procedure deck. Templates established communication between sourcing analysts and buyers. Integrate workflow throughout team and resulted in communication efficiencies Show less
-
-
Education
-
St. Mary's College of California
Business & Economics, Finance, Economics, Business Law, Marketing, Accounting -
California State University-Hayward - School of Business and Economics
Supply Chain Management Certification, Product Supply, Advance Negotiation, Purchasing -
Bemis - Neenah, Wisconsin
Lean Six Sigma Green Belt Certification - Internal, Project Management -
Saint Mary's College of California
Bachelor of Science - BS, Business/Managerial Economics
Community
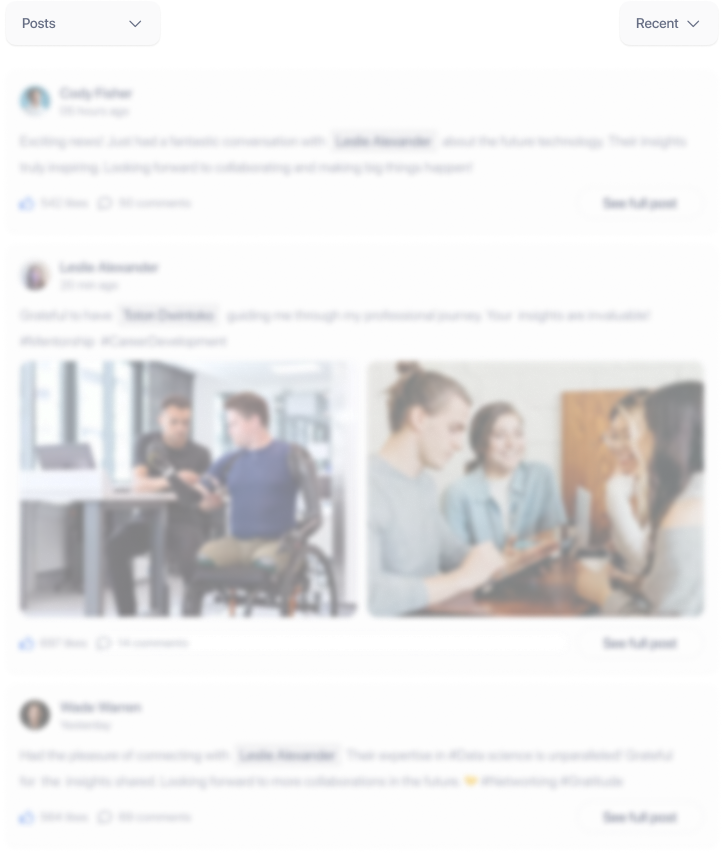