Jeremy Young
Maintenance Manager at Foam Holdings, Inc.- Claim this Profile
Click to upgrade to our gold package
for the full feature experience.
-
English -
-
Spanish -
Topline Score
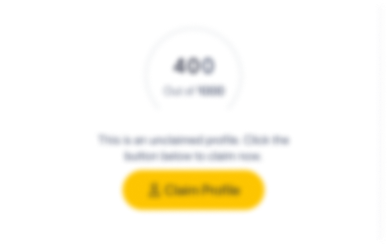
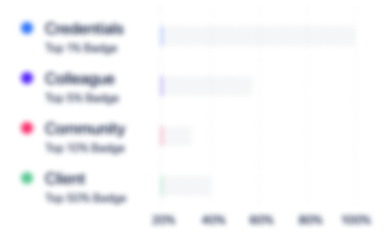
Bio


Credentials
-
HVAC Recovery - Universal
RSESJun, 2014- Nov, 2024 -
RCRA/DOT #0816
Tech-ResQMar, 2016- Nov, 2024
Experience
-
Foam Holdings, Inc.
-
United States
-
Plastics Manufacturing
-
1 - 100 Employee
-
Maintenance Manager
-
May 2021 - Present
In May of 2021, I started my current position as Maintenance Manager for the Radford Branch of Huntington Solutions, a Shape Molding Facility that had ten active presses running 24/5. My position was billeted to be in charge of the Maintenance Department, including Maintenance Technicians, Tools Setters, and the Mold Repair Shop, billeted as thirteen personnel. • Part of my responsibilities were to completely create the preventative maintenance program, a localized parts storage facility for time critical parts, and to bring safety and compliance to a forefront. • I worked with surrounding companies to fill parts requirements without increasing the plant parts inventory. • Trained a maintenance crew to start fulfilling preventative and corrective maintenance requirements. • I worked with the corporate purchasing department to decrease the cost of consumable materials. • I’ve successfully trained up multiple iterations of personnel due to the current fluctuating work environment. Show less
-
-
-
-
Reliability Manager
-
Feb 2019 - Present
-
-
MRO Buyer/PSM Coordinator
-
Oct 2017 - Present
As MRO Buyer - responsible for Entire Maintenance Department budget and checkbook, keeping track of entire facility's maintenance expenditures, working with other departments to get company bills paid in a timely manner.This includes tracking items being shipped for missing cargo,Coordinating with outside agencies to ensure proper shipping conditions,Working with facility technicians and engineering personnel to ensure that the items ordered are to the correct specifications.Keeping correct inventory of the facility's repair parts to minimize MTTR for missing parts.Become familiar with the Oracle software as well as the Maximo CMMS.As PSM Coordinator - responsible for working with both outside contracted personnel and internal resources to ensure that the facility Ammonia safety Program is up to standard with both EPA and OSHA regulations. This includes verifying procedures are being maintained to regulation standards,Tracking progress in on site related projects to maximize efficiency in maintaining the equipment within standards,Helping to develop a more granulated tracking system for documenting the training personnel.Working with outside vendors to look for deficiencies and finding ways to overcome them. Show less
-
-
Maintenance Supervisor
-
Aug 2016 - Oct 2017
In this position I was responsible for the assignments, training, and safety of the A shift personnel in the Bakery on a 3/3/4 on a daily basis, with increasing duties as needed.Supervise outside personnel in addition to the standard work force, tracking performance as needed..Provide guidance and direction for work assignment completion.Coordinate with the Maintenance Planner and Parts Room personnel to facilitate acquisition of required parts and tools for personnel. Minimize Plant downtime by providing valuable instruction on Troubleshooting techniques and Electrical Theory of Operation.Start implementation of employee training project to further maximize the availability of maintenance resources to the job that they are needed at.Moved from this position to a combined position of MRO Buyer and PSM coordinator due to facility vacancies and company needs. Show less
-
-
-
Volvo Trucks
-
Sweden
-
Motor Vehicle Manufacturing
-
700 & Above Employee
-
Maintenance Supervisor
-
Nov 2014 - Apr 2016
In this position I was responsible for the assignments, training, and safety of the 2nd shift personnel in the Assembly Plant on a daily basis, with increasing duties as needed. Supervise outside personnel in addition to the standard work force, tracking performance as needed.. Provide guidance and direction for work assignment completion. Coordinate with the Maintenance Planner and Central Stores personnel to facilitate acquisition of required parts and tools for personnel. Direct input into capital projects and upgrades that would save the company over 50,000. Work to right size the workforce to ensure minimization of line downtime. Complete a program on cross-training personnel in specified job categories into specialized work to allow for greater support during reduced personnel conditions. Participate in the Master Truck Builder program and achieve 1st place on month to month basis repeatedly. Show less
-
-
-
Saint-Gobain Performance Plastics
-
United States
-
Plastics Manufacturing
-
700 & Above Employee
-
Maintenance Technician
-
May 2011 - Oct 2014
In this position, I was primarily responsible for off shift operation and upkeep of the facility, including: Perform all necessary maintenance-related activities required to ensure continued operation of the facility, including the installation, removing, replacing, and repairing of any and all systems used in factory operations. Maximize machine run time while minimizing occurrence, severity, and cost of equipment failure. Other roles I perform include: Installation of new equipment; electrical, pneumatic, and mechanical troubleshooting; PLC programming; maintenance of photo-eyes, safety components, and HVACR systems. Work directly with EHS coordinator to mitigate hazards and downtime. Identify deficiencies in preventative maintenance tracking, prepare reports and presentations for division-wide executive personnel, and coordinate an extensive revitalization of the MP2 CMMS. Schedule outside personnel, as required. Serve as departmental “Livewell Champion” coordinator. Show less
-
-
-
Economy Linen Hospital Services
-
United States
-
Facilities Services
-
1 - 100 Employee
-
Assistant Plant Engineer
-
Mar 2009 - Apr 2011
In this position as Assistant Plant Engineer, my role included: Operate as the Plant Engineer during periods when the Plant Engineer was unavailable. Supervise outside personnel in addition to the standard work force, tracking performance as needed. Provide weekly reports to the Plant Engineer and Director of Operations on maintenance activities. Provide guidance and direction for work assignment completion. Order repair parts and keep inventory control. Direct supervision of various capital projects, both mechanical and aesthetic improvements. Re-evaluate the preventative maintenance program and make corrections to enhance effectiveness. Show less
-
-
-
Hutchinson
-
France
-
Plastics and Rubber Product Manufacturing
-
700 & Above Employee
-
Lead Maintenance Technician
-
Jan 2007 - Feb 2009
In this position I was the Lead Maintenance Technician for the rubber manufacturing facility during off-shift operations. This role included: Install, troubleshoot, repair, and/or replace multiple different interrelated systems used in factory operations. Maintenance of routine operations, including pipe fitting; electrical, mechanical, pneumatic, and mechanical troubleshooting and installation; installation and calibration of photo-eyes, safety components, and industrial scales; troubleshooting of PLCs and VFD’s. Supervision of shift personnel, new hires, and rotationally assigned personnel. Show less
-
-
-
US Navy
-
United States
-
Armed Forces
-
700 & Above Employee
-
Electricial Supervisor
-
Aug 2004 - Nov 2006
In this position I was in charge of various facility maintenance concerns, including:Supervise a wide range of facility-related operations, including the installation and removal of electrical equipment.Ensure the maintenance of the facility grounds, both internal and external. Other Duties that I had were:Direct the entire facility vehicle program. Re-engineer the facility’s Command Engraving Program, increasing quality of the finished product while decreasing cyclical costs to the facility. Show less
-
-
Electrician's Mate 2nd Class
-
Oct 2002 - Aug 2004
At this facility I performed in a supervisory and team building role during my tenure. In addition to standard responsibilities, this included:: Act in a supervisory role while operating a power plant to support operations afloat. Direct and maintain inventory control of replacement and repair parts.Ensure the full training of personnel under my command.Perform all high profile maintenance on any equipment. Other positions I fulfilled include: Electrical Supervisor for the shipShip's Navigational MonitorCareer CounselorMaintenance Supervisor Show less
-
-
Nuclear Power Plant Operator
-
Jul 2000 - Sep 2002
In this position I was required to work in a variety of positions regarding the operations, upkeep, and repair of a Naval Nuclear Power Plant, including::Material Control Area SecurityPower Plant Condition Monitoring, Repair, Preventative Maintenance, and OperationsMotor Repair and Preventative Maintenance.
-
-
Education
-
US Navy
Naval Nuclear Training Command and Electrician A School, Nuclear Power plant Theory, Operation, procedures, and Electrical Theory and Operation -
Hunter Tannersville High School
Regents Level Diploma, Honors/Regents High School/Secondary Diploma Program
Community
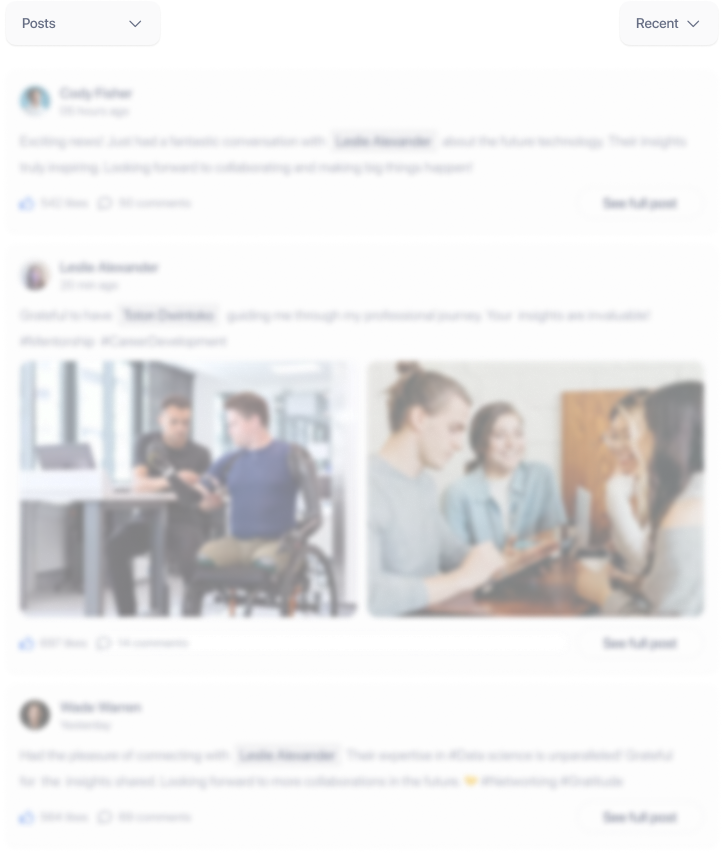