Jeremy Williams
Engineering Manager at Diversified Technologies International- Claim this Profile
Click to upgrade to our gold package
for the full feature experience.
Topline Score
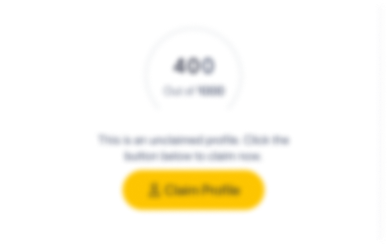
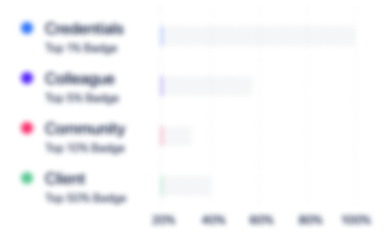
Bio

Kevin Holochwost
Jeremy Williams is a hard working extremely talented individual who is one of the most capable process engineers I have known. His ability to troubleshoot problems based on his in depth knowledge of machines, plastic properties and process has solved many issues before they mushroom. His willingness to work at the genuinely difficult tasks at whatever hours it is required shows a dedication to excellence that is difficult to find in today’s work force. Jeremy does not shy away from challenges, and is a straightforward solutions oriented individual, who is welcome on any project team and in any department I am a leader of.

Donald Benish
Jeremy was a hard working guy who always was willing to learn, not only at his job but in his personal life. He was very motivated to learn new information about different systems and operations through out the company, he would be a valuable asset to which ever company decides to hire him. He has a great personality and is not afraid to share his knowledge with others and will continue to learn and grow not matter what he is doing.

Kevin Holochwost
Jeremy Williams is a hard working extremely talented individual who is one of the most capable process engineers I have known. His ability to troubleshoot problems based on his in depth knowledge of machines, plastic properties and process has solved many issues before they mushroom. His willingness to work at the genuinely difficult tasks at whatever hours it is required shows a dedication to excellence that is difficult to find in today’s work force. Jeremy does not shy away from challenges, and is a straightforward solutions oriented individual, who is welcome on any project team and in any department I am a leader of.

Donald Benish
Jeremy was a hard working guy who always was willing to learn, not only at his job but in his personal life. He was very motivated to learn new information about different systems and operations through out the company, he would be a valuable asset to which ever company decides to hire him. He has a great personality and is not afraid to share his knowledge with others and will continue to learn and grow not matter what he is doing.

Kevin Holochwost
Jeremy Williams is a hard working extremely talented individual who is one of the most capable process engineers I have known. His ability to troubleshoot problems based on his in depth knowledge of machines, plastic properties and process has solved many issues before they mushroom. His willingness to work at the genuinely difficult tasks at whatever hours it is required shows a dedication to excellence that is difficult to find in today’s work force. Jeremy does not shy away from challenges, and is a straightforward solutions oriented individual, who is welcome on any project team and in any department I am a leader of.

Donald Benish
Jeremy was a hard working guy who always was willing to learn, not only at his job but in his personal life. He was very motivated to learn new information about different systems and operations through out the company, he would be a valuable asset to which ever company decides to hire him. He has a great personality and is not afraid to share his knowledge with others and will continue to learn and grow not matter what he is doing.

Kevin Holochwost
Jeremy Williams is a hard working extremely talented individual who is one of the most capable process engineers I have known. His ability to troubleshoot problems based on his in depth knowledge of machines, plastic properties and process has solved many issues before they mushroom. His willingness to work at the genuinely difficult tasks at whatever hours it is required shows a dedication to excellence that is difficult to find in today’s work force. Jeremy does not shy away from challenges, and is a straightforward solutions oriented individual, who is welcome on any project team and in any department I am a leader of.

Donald Benish
Jeremy was a hard working guy who always was willing to learn, not only at his job but in his personal life. He was very motivated to learn new information about different systems and operations through out the company, he would be a valuable asset to which ever company decides to hire him. He has a great personality and is not afraid to share his knowledge with others and will continue to learn and grow not matter what he is doing.

Experience
-
Diversified Technologies International
-
United States
-
Motor Vehicle Manufacturing
-
1 - 100 Employee
-
Engineering Manager
-
Jun 2021 - Present
Deliver high quality molds serving all markets including but not limited to single cavity, multi-cavity, family molds, 2 shot, multi-shot, overmold, insert mold, stack molds and LSR Collaborate with OEM product designers to improve product design to reduce risk of failure Direct oversight of Design for Manufacturing, Moldflow Analysis, Mold Design, Mold Build, Engineering Changes and Validation Assist molders with machine selection to ensure robust process can be achieved to maintain customer satisfaction Not only do we design and build robust molds, but we engineer from the plastics point of view Show less
-
-
-
RJG, Inc.
-
United States
-
Plastics Manufacturing
-
100 - 200 Employee
-
Consultant/Trainer
-
Dec 2015 - Jun 2021
Consulting for the injection molding industry serving automotive, medical, furniture and consumer markets. Work with customers to create robust part design, rugged mold design/construction and optimize the injection molding process. Create value by reducing part or mold redesigns, which minimizes lead time to market. Lower part costs by decreasing cycle time while maintaining quality requirements and reduce manufacturing scrap rates. Training for injection molding industry: Essentials of Injection Molding, Systematic Molding, Decoupled Workshop and Master Molder. Show less
-
-
-
Amway
-
United States
-
Manufacturing
-
700 & Above Employee
-
Principal Engineer
-
Jun 2013 - Dec 2015
Participate on Team that generates savings totaling over $10 Million through improved supply chain, manufacturing efficiencies and alternate materials on a yearly basis. Global supply chain management of, but not limited to mold builders, molding facilities and contract assembly for production and R & D activities. Develop, implement and maintain global training plan for plastics utilizing RJG® Decoupled methodology for internal candidates & supplier(s) globally. Generate and apply global strategy of data collection for “real time” molding analysis with RJG® EDM System. Work directly with Design, Reliability, Quality and Process Engineering to determine appropriate specification(s) for products. Direct involvement in component design, material selection, mold build and part validations for new product launches and product improvements. Create and continually improve Injection Molded Component Standardization System (IMCSS). Utilize CAE, FEA, DFMEA and PFMEAto mitigate risk on molded components. Use scientific and statistical methods for injection component validation(s). Apply problem solving techniques such as 5-Why’s, Fishbone Diagrams and 8D to determine root cause. Transfer technology from R & D location(s) to manufacturing site(s) around the globe to meet cost and demands of supply chain. Domestic & International travel to various suppliers including, but not limited to mold builders, molding facilities and contract manufacturing. Show less
-
-
-
Nolato GW, Inc.
-
United States
-
Plastics Manufacturing
-
200 - 300 Employee
-
Automation / Process Engineer
-
Apr 2008 - May 2013
$3.2 Million dollars in cost savings annually through cycle time reduction. Develop corporate training matrix for all departments (Engineering, Manufacturing and Management) that includes classroom instruction with Paulson and RJG in conjunction with OJT in Materials, Mold Maintenance, Machine Maintenance, Processing, Automation, Secondary Operations & Engineering. Complete Authorization for Equipment documentation to support purchasing new molding equipment including but not limited to molding machines, robots, temperature control units, hot runner systems and secondary equipment. Installation and Validation of 15 new molding machine over 5 year period. Implementation of fifteen RJG eDart ® Data acquisition systems with plans to full instrument fifty-six injection molding machines. Process Development for injection molded components using Scientific Injection Molding, Decoupled II & Decoupled III ® molding techniques. IQ/OQ/PQ mold qualifications for medical device components. Implementation of Six Sigma controls limits for process control. Domestic travel to mold builders and/or tryout facilities for design reviews and/or mold trial runs. Analyze Mold/Automation design through established Good Plastic Manufacturing Practices with the use of Design Review Guidelines and Moldflow ® Analysis. Injection molding thin wall, automotive safety critical, gears, surgical and implantable medical devices. Manage new mold testing schedule requirements for on-time delivery Show less
-
-
-
Display Pack Inc
-
United States
-
Packaging & Containers
-
1 - 100 Employee
-
Process Engineer
-
Aug 2007 - Apr 2008
Annual cost savings of $3.45 Million dollars with implementation of improved Mold Change Standard Operating Procedures. Develop standard process for thermoforming of blisters, clamshell and interior grade automotive films based on key plastic film variables. Co-Author of tooling standards for automotive and packaging business units. Implement/Improve process control and documentation that adhere to ISO 9000 requirements. Monitor day to day thermoforming processing on all machines, assist with daily processing issues and determine root cause. Show less
-
-
-
A&A Manufacturing
-
Valparaiso, IN
-
Process Engineer Leader
-
Mar 2007 - Aug 2007
Annual cost saving in exceeding $1.5 Million dollars with implementation of new scheduling format. Co-Authored tooling standards new products. Process Development for new tooling with De-Coupled® molding techniques. Initiate Process Documentation, Process Control and document retention for all products. Implement Lean Manufacturing, JIT and 5s manufacturing in department. Established machine testing, benchmarks and calibration requirements. Manage all molding department employees within facility. Show less
-
-
-
ADAC Automotive
-
Motor Vehicle Manufacturing
-
400 - 500 Employee
-
Lead Process Engineer
-
May 2005 - Mar 2007
Implement $11 Million dollars annually in cost savings over twenty-two different injection molds through reduction of cycle time and non-conforming product. Molding Interior/Exterior trim and lighting components for the automotive industry. Create tooling standards for various machine sizes and implement Efficient Mold Change. Process Development for new tooling with De-Coupled II® molding techniques. Organize and manage Continuous Improvement projects for department with established timelines. Established Standard Operating Procedure for machine set-up to improve change over time. Established FMEA, DFMEA, PFMEA and Control Plans for presentation with customers during launch phase. Interface with suppliers, customers, sales representatives, outside contractors to improve quality and delivery of product. Supervise key technical department employees including technicians, die setters and material handlers. Show less
-
-
-
Cascade Engineering
-
United States
-
Plastics Manufacturing
-
200 - 300 Employee
-
Process Technician
-
Sep 2000 - May 2005
Complete mold changes and material changes in safe and efficient manor to reduce downtime. Start up of molding machines, process documentation and maintaining product quality during production runs. Monthly reports for scrap reduction, mold change over time both with corrective actions and improvements for department. Preventative Maintenance work on all molds, machines and secondary equipment per establish Preventive Maintenance Schedule. Implement new ideas to reduce downtime by creating centralized tooling hook-ups. Show less
-
-
Education
-
Community College of Vermont
Associate’s Degree, Business -
Grand Rapids Community College
Associate’s Degree, Plastics Technology -
Lakewood Public School
High School Diploma, General Studies
Community
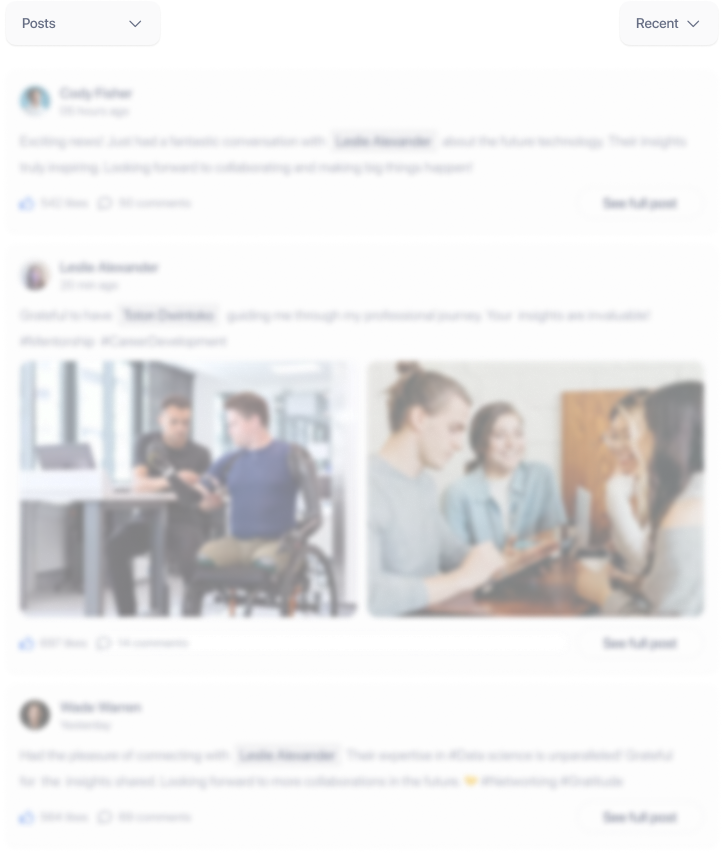