Jenny Chang
Senior Consultant at X/Celerant Consulting- Claim this Profile
Click to upgrade to our gold package
for the full feature experience.
Topline Score
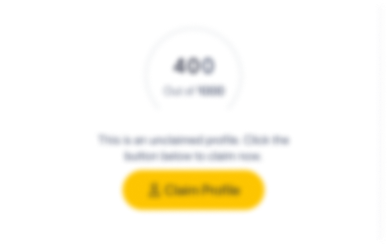
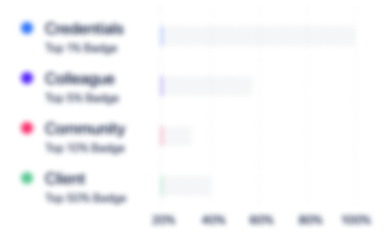
Bio
0
/5.0 / Based on 0 ratingsFilter reviews by:
Experience
-
X/Celerant Consulting
-
United States
-
Business Consulting and Services
-
1 - 100 Employee
-
Senior Consultant
-
Apr 2015 - Present
Global Specialty Chemical manufacturer in China Conducted organization development design (ODD) and site assessments to assess and highlight operational strengths, capacity and integration opportunities, risk and challenges. Developed integration plans and partnered with site leaders and PE firm to help realize synergy benefits through M&A. Achieved targeted +$40 MM in COGS based Operations and global SG&A. This was enabled through foot print rationalization, territory realignment, and distributor consolidation and warehousing optimization. Show less
-
-
-
Foxconn
-
Taiwan
-
IT Services and IT Consulting
-
1 - 100 Employee
-
Leadership Program
-
Dec 2010 - Apr 2015
Key interface with GSM Team for operations related negotiations, including product demand, supply, inventory, delivery, capacity and resources investment. Responsible for project on-time deliveries for A-team Product Design, with key contributions to process, material, equipment specifications lock down, resource readiness, risk management and trouble- shooting from development stage to mass production. Lead project schedule, deliveries, resources, risks, quality, spec relief related negotiations with A-team engineering and operations teams. Responsible for Lean Manufacturing and Supply-Chain Integration from upstream suppliers to downstream customers. Key involvement with procurement activities, including demand forecasting, VMI, quality, supply negotiations with vendors, and defining business strategies. Drive for failure analyses (FA), corrective actions (CA) to hit higher output volume and process yield rate. Identify strategic and bottleneck resources, and lead a cross-functional team for alternative solutions. Competitor analyses, data analyses, sales projection. Show less
-
-
-
-
Management Consultant
-
Nov 2005 - Oct 2010
US$ $9.73 MM large scale cost reduction implementation project focused on Production, Maintenance, Organizational Effectiveness, Energy, Material Control, Procurement and MCRS™. Overall project benefits case realized was $23.74mm annualized. Rapid Cash Program - $200M of working capital freed by reducing inventories. And shared planning and forecasting with supplier to reduce inventory and lead times. For aligning inventory levels more closely with customer demand and increase focus on cash. Brand New processes installed in MCRS™ all the company in scope. Follow the guide book what published from HQ of 21st Century manufacturing and implemented a site wide Management Control and Reporting System. Show less
-
-
-
American Standard Heating & Air Conditioning
-
United States
-
Industrial Machinery Manufacturing
-
1 - 100 Employee
-
Accounting & Finance Controller
-
Sep 1991 - Nov 2006
1. Completed the necessary returns to achieve 684.7K plan compliance with GAAP requirements for the plan years ended 8/2003. 2. Introduced and initiated regular bi-monthly meeting to address problem areas, review current projects and progress made on old projects. 3. Recommended the retention of a second banking relationship to expand finance options. 4. Organized trained, and spearheaded a team to clean up the books, eliminate backlog of non-financial reporting, put procedures and controls in place to stop incorrect processing of information, and create a disciplined accounting department. Development to standardized reports from ERP with department managers and eliminated need to recreate same information outside of ERP. Achieved a 100% improvement in overall operations, and received clean opinions internally and externally for years ended 2001 and 2002. 5. Organized work groups to maximize benefits and problem solve the ERP system. 6. Coordinated year-end physical inventory reducing down time from 1 week to 2 days. 7. Coordinated year-end review with independent accountants. 8. Formalized and re-engineered procedures to ensure compliance with complex government proposal submissions, awarded contract requirements, and government accounting requirements. 9. Skillfully negotiated bank line of credit increase while reducing covenants and shareholder guarantees. 10. Just location recognized by internal auditors for achieving financial organization within record time. 11. Reconciliation of intercom any accounts revealed over dues processed prior to 2002. 12. Work with External Auditors (Ernst & Young) for group and local statutory audits. Show less
-
-
Education
-
University of Leicester
Master of Business Administration - MBA
Community
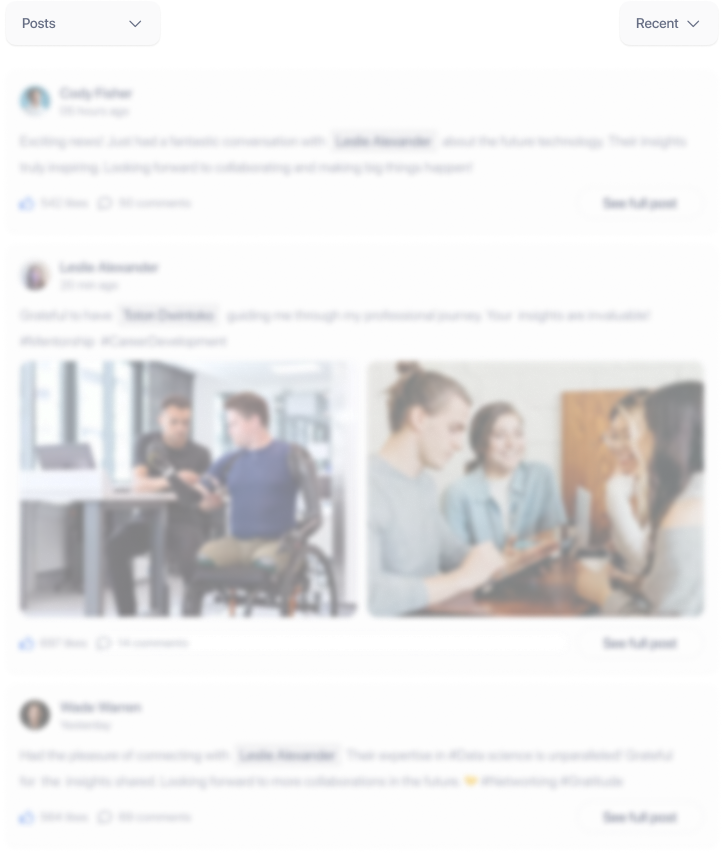