
Jennifer McGinnis
Vice President at Priority Restoration- Claim this Profile
Click to upgrade to our gold package
for the full feature experience.
Topline Score
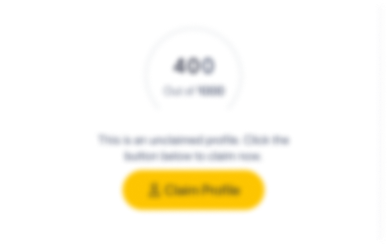
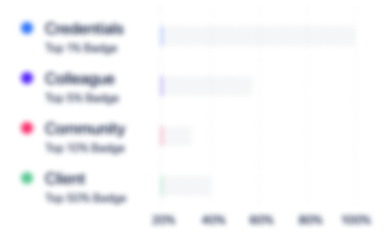
Bio

Churaman Singh
Jennifer is a powerhouse of committment, drive and dedication to her career . If there is a task that Jennifer has taken on, it will be completed with accuracy, efficiency and flair for the creative !! I highly recommend Jennifer to work in fast paced, collaborative environment also she is one of the best collegue that you ever mate.

Jeff Patelo
Jennifer shows constant drive to seek improvements and find better ways to do things.

Churaman Singh
Jennifer is a powerhouse of committment, drive and dedication to her career . If there is a task that Jennifer has taken on, it will be completed with accuracy, efficiency and flair for the creative !! I highly recommend Jennifer to work in fast paced, collaborative environment also she is one of the best collegue that you ever mate.

Jeff Patelo
Jennifer shows constant drive to seek improvements and find better ways to do things.

Churaman Singh
Jennifer is a powerhouse of committment, drive and dedication to her career . If there is a task that Jennifer has taken on, it will be completed with accuracy, efficiency and flair for the creative !! I highly recommend Jennifer to work in fast paced, collaborative environment also she is one of the best collegue that you ever mate.

Jeff Patelo
Jennifer shows constant drive to seek improvements and find better ways to do things.

Churaman Singh
Jennifer is a powerhouse of committment, drive and dedication to her career . If there is a task that Jennifer has taken on, it will be completed with accuracy, efficiency and flair for the creative !! I highly recommend Jennifer to work in fast paced, collaborative environment also she is one of the best collegue that you ever mate.

Jeff Patelo
Jennifer shows constant drive to seek improvements and find better ways to do things.

Experience
-
Priority Restoration
-
Canada
-
Construction
-
1 - 100 Employee
-
Vice President
-
Apr 2021 - Present
-
-
Claims Manager
-
Nov 2014 - Apr 2021
-
-
Quality Assurance Coordinator
-
Jun 2014 - Nov 2014
-
-
-
CG Power Systems Canada Inc
-
Canada
-
Utilities
-
1 - 100 Employee
-
Quality Systems and Lean Specialist
-
Sep 2013 - Apr 2014
- Contributed to creation, communication, facilitation, implementation, and reporting for the internal audit program as well as responses to external audits.- Maintained knowledge of latest ISO 9000 Series Quality Standards.- Assisted development of quality assurance policies, procedures, and work instructions.- Implemented training on quality systems and Lean principles, as well as contributing to Kaizen events effectively.- Communicated with management to provide ongoing status of process reviews and redesign.
-
-
-
MacDon Industries
-
Canada
-
Machinery Manufacturing
-
400 - 500 Employee
-
Quality Management System Manager
-
Aug 2012 - Sep 2013
- Managed and maintained MacDon QMS, monitoring and improving effectiveness of QMS as well as implementing QMS training.- Served as lead auditor, executing and managing Internal Audit program, setting objectives as well as handling planning, scheduling, reporting, surveillance, and issuance.- Led Corrective Action and Preventive Actions systems including database development, tracking, and reporting of CAR status, ensuring proper closures of issued CAR.- Provided support for Quality Management Review (QMR) process.- Developed and reported on QMS key performance indicators (KPIs).
-
-
-
Cascades
-
Canada
-
Packaging and Containers Manufacturing
-
700 & Above Employee
-
Quality Control Technician
-
Oct 2010 - Aug 2012
- Coordinated with Continuous Improvement to redevelop Quality System, improving accessibility, including streamlining QAR process, simplifying technical jargon, and increasing efficiency.- Refocused facility attention to quality, raising awareness and collaborating with employees to instill core principles of Containment, Correction, and Prevention.- Investigated and reported on internal or external quality issues and concerns.- Conducted internal business audits, ensuring standard operating procedures.- Acted as gatekeeper for document control within the plant.- Managed a variety of programs including food safety as well as ISO 9001:2008, coordinating with third-party auditors and collaborating with staff to ensure improvement of regulations.
-
-
Customer Service Representative
-
Mar 2008 - Oct 2010
I requested to join Cell C, where I eagerly assumed the responsibilities of two customer service representatives, while simultaneously maintaining some of my previous accounts.- Initiated and coordinated the team effort that saw the creation of a new ordering/production schedule to help better facilitate the working logistics with one of our biggest accounts. This in turn helped regain the trust of the customer who had recently experienced some inconsistent customer service. - Acted as liaison, connecting customers to account managers and the production cell.- Duties included: overseeing customer accounts; creating dockets for production; handling quality issues; scheduling shipping; coordinating shipments; maintaining and controlling inventory levels; and general customer maintenance.
-
-
Education
-
Management Red River College Winnipeg
Certificate in Operations Management, Operations Management and Supervision
Community
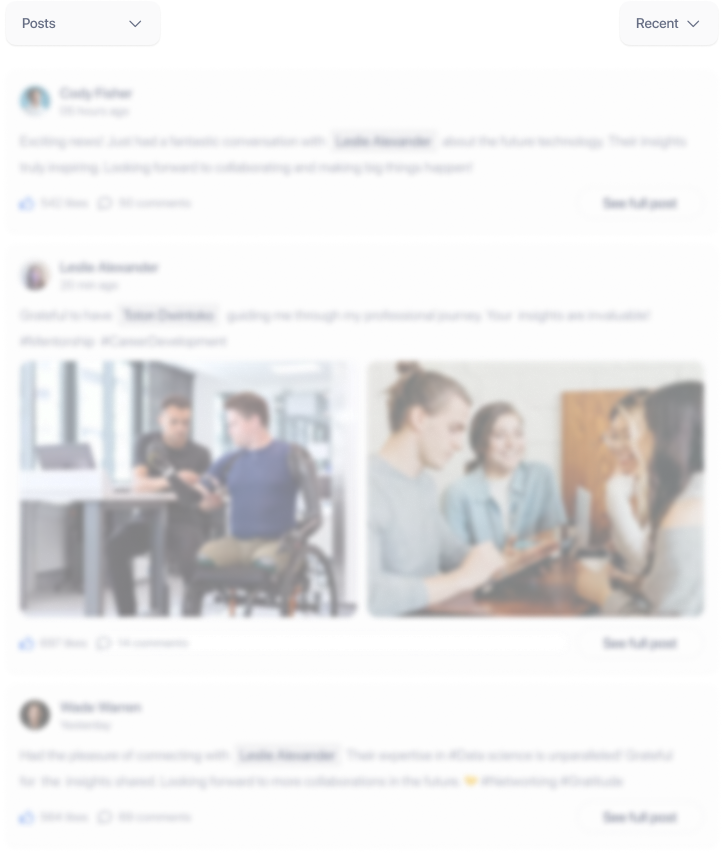