Jenna-Lee Fraser
Senior Process Engineer at KC8 Capture Technologies- Claim this Profile
Click to upgrade to our gold package
for the full feature experience.
-
English Native or bilingual proficiency
-
Afrikaans Elementary proficiency
Topline Score
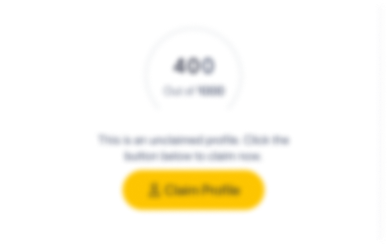
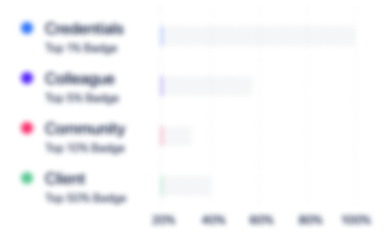
Bio


Experience
-
KC8 Capture Technologies
-
Australia
-
Services for Renewable Energy
-
1 - 100 Employee
-
Senior Process Engineer
-
Jul 2022 - Present
-
-
-
Chemical Plant Engineering
-
South Africa
-
Engineering Services
-
1 - 100 Employee
-
Lead Process Engineer
-
Sep 2021 - May 2022
-
-
-
Fluor Corporation
-
United States
-
Construction
-
700 & Above Employee
-
Business Development Specialist - Energy Transition
-
Jun 2021 - Sep 2021
Business Development Specialist for Fluor South Africa with a focus on the generation of new business in the front end phases of projects that are supportive of a shift to net-zero carbon emissions.
-
-
Business Development Specialist - Sales Coordinator
-
Sep 2019 - Sep 2021
Energy Solutions Sales Coordinator for Fluor South Africa Business Development.This role provided exposure to opportunity pursuits from initial screening to contract closure. Responsibilities tested communication with management, co-workers, clients and visitors, attention to detail and time management. An understanding of key business drivers, industry issues, trends, strengths, weaknesses, strategies, and services was acquired and a meticulous attention to detail and ability to work in a time-conscious and time-effective manner was reinforced. Show less
-
-
Process/Specialty Engineer II
-
Mar 2018 - Aug 2019
The purpose of this position is to provide Process Technology engineering and technical support for intermediate systems with moderate complexity.ConfidentialFluor South Africa08/2018The objective of the project was to reduce the sulphur in the Full Range Catalytic Naphtha (FRCN), thereby reducing overall sulphur in the gasoline pool, while minimizing octane loss. The client selected technology for this project was the Axens Prime G+ technology which included 63 pieces of new equipment in 6 different sections. The team worked closely with the Prime G+ technology Licensor to develop a complete CNHT unit.Responsible for the evaluation of a number of existing, redundant heat exchangers for reuse on the new plant in the Detailed Feasibility Phase. Developed the OBL P&IDs and converted the Licensor’s IBL P&IDs to Engen formats in the Basic Engineering Phase of the project. Participated in the P&ID review and HAZOP study. Indeni Energy Management and Conservation StudyFluor South Africa10/2018Following 45 years of operation, the Indeni Refinery, situated near the town of Ndola in Zambia, decided to conduct an energy management and conservation study to evaluate plant performance with the intention of reducing energy cost by optimising operations and improving efficiencies. The study conducted by Fluor, considered both thermal and electrical energy systems evaluating them against industry benchmarks and the original design. It identified energy losses and inefficient operations in the refinery, highlighting opportunities where plant optimisation is possible.Responsible for the thermal evaluation of a number of existing heat exchangers using HTRI. Show less
-
-
Process/Specialty Engineer I
-
Mar 2016 - Feb 2018
The purpose of this position is to provide Process Technology engineering and technical support for intermediate systems.SAPREF T6502 Spent Caustic DisposalFluor Igoda Projects02/2018The primary purpose was to reduce the fluoride loading in Alkylation Unit Spent Caustic to below refinery effluent permitted levels. The scope included a vendor supplied treatment facility including a fluidised bed reactor with chemical dosing facility, neutralisation facility and influent and effluent settling tanks. Responsible for the OBL Process design and coordination and interface with the vendor of the IBL facility. SAPREF D50Fluor Igoda Projects02/2017The primary purpose was to enable the SAPREF refinery to produce at least 30% of its diesel output as 40ppm sulphur (D50) to meet the current Schedule 3 specification for the niche grade. The scope included equipment and instrumentation modifications and additions to existing operating units. Responsible for the thermal design and rerate of a number of heat exchangers in the crude distillation unit (CDU) preheat train as well as the sizing and Process specifications for a new CDU feed pump. Carried out post HAZOP hydraulic and safeguarding investigations on a hydrodesulphurising (HDS) unit to progress the design from FEED to AFD early in the project. SAPREF Jet & AGO Stadis 450 Injection Systems UpgradeFluor Igoda Projects10/2016The primary purpose was to improve the antistatic additive (ASA) dosing systems on Jet Fuel, Kerosine and automotive gasoil rundowns such that the products were always as per specification and to reduce the inherent risks involved with operator handling of ASA.Responsible for the Process design development from conceptual to AFD. Firm engagement with a potential injection skid vendor early on in the project resulted in a significant reduction of the project scope and overall cost saving for the client at a time when the client’s CAPEX budget was severely constrained. Show less
-
-
Associate Process/Specialty Engineer II
-
Mar 2014 - Feb 2016
The purpose of this position is to provide Process Technology engineering and technical support for simple systems.SAPREF Safeguarding UpgradeFluor Igoda Projects 10/2015The primary purpose was to (1) review and, if necessary, upgrade the current or implement new emergency depressurizing systems and back-up instrument air supplies and;(2) review identified relief scenarios and, if required, make modifications, upgrade existing or install new pressure relief valves.Responsible for reviewing the basis of the relief capacity and relief valve sizing calculations undertaken by the previous contractor and making amendments where necessary. Identified sectionalizing limits and sized emergency depressurizing and pressure relief valves as well as inlet and outlet piping on the relief valves. Engen / Shell S&D Tanker Loading Vapour Recovery Units Fluor Igoda Projects05/2014The primary purpose was to align seven of Shell’s Terminals across South Africa and Engen’s Durban Refinery with legal emission requirements before the 31 March 2015 deadline by installing new vapour recovery units (VRU) and internal floating roofs at their road and rail loading facilities where required. Developed the basis for the design of the eight VRUs and provided input into the RFQs for the VRU packaged units. The terminals involved were spread across South Africa so site visits were limited and most information was received via terminal personnel making effective communication with the client imperative. Responsible for the design of the OBL scope which included tank modifications, vapour recovery arms and gasoline supply pumps. Show less
-
-
Associate Process/Specialty Engineer I
-
Apr 2013 - Feb 2014
The purpose of this position is to perform Process Technology engineering work requiring application of standard engineering techniques and procedures.Shell S&D Alberton Terminal UpgradeFluor Igoda Projects 04/2013The primary purpose was to upgrade the terminal by increasing the storage capacity of one of Shell’s Terminals by installing four new 10,000m³ storage tanks, rationalizing the utilization of existing storage tanks and pumps, installing a new road tanker loading gantry and upgrading the existing fire protection facilities. Developed a phasing plan to turn over existing storage tanks and pumps to their new services while maintaining the overall storage capacity and road tanker loading capabilities of the terminal. Responsible for the RFQ for the skid mounted road loading gantry. Provided instructions and remote support for commissioning of the new tanks and pumps. Show less
-
-
-
Aveng
-
South Africa
-
Construction
-
300 - 400 Employee
-
Graduate Engineering Trainee
-
Feb 2013 - Mar 2013
-
-
Education
-
Stellenbosch University/Universiteit Stellenbosch
Bachelor of Engineering (BEng), Chemical Engineering -
Durban Girls' High School
National Senior Certificate
Community
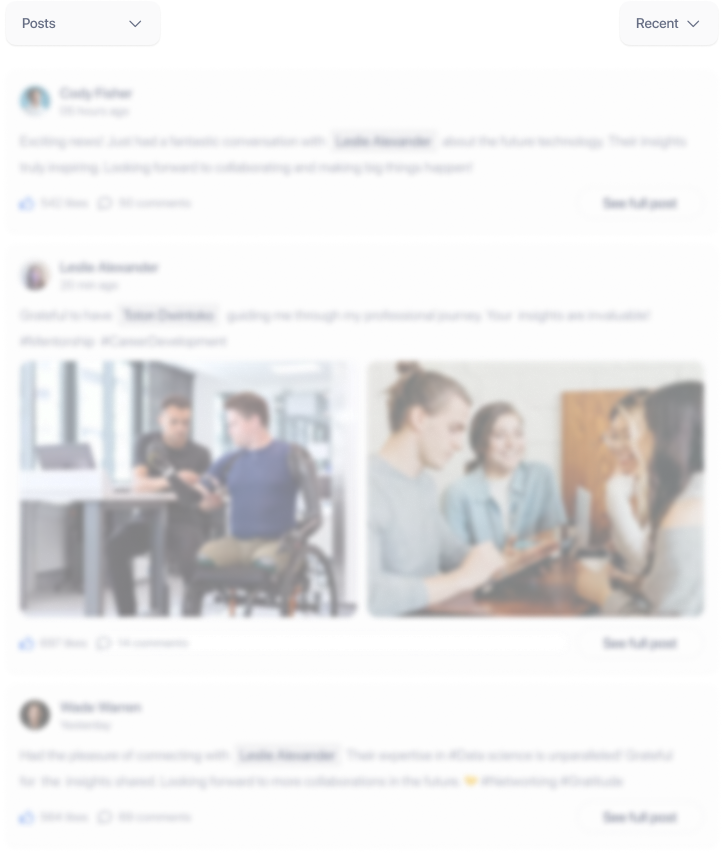