Jeffrey Harrison
Continuous Improvement Director at Carclo Technical Plastics- Claim this Profile
Click to upgrade to our gold package
for the full feature experience.
Topline Score
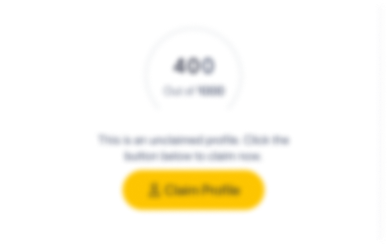
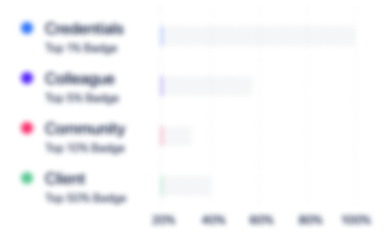
Bio


Experience
-
Carclo Technical Plastics
-
United States
-
Plastics Manufacturing
-
200 - 300 Employee
-
Continuous Improvement Director
-
Oct 2018 - Present
-
-
-
Mitchell Plastics
-
Canada
-
Automotive
-
300 - 400 Employee
-
TPS / Kaizen Manager
-
2014 - Oct 2018
Promoted to head Kaizen team in identifying, establishing, and implementing continuous improvement initiatives across 210K square foot facility with 400 employees. Accountable for Floor Management Development System (FMDS) and KPI reporting throughout the facility.o Coach and develop rotating associates on root cause analysis using 5 Whys technique across six injection molding zones, painting, flocking, and assembly. Perform time studies, redefine work instruction, and standardize work. o Utilize Plex ERP to capture performance in safety, quality, productivity, scrap, and cost. Lead interdepartmental Champions in problem solving evaluation to find solutions that eliminate gap.PROCESS IMPROVEMENT* Saved more than $1M in labor costs involving 54 mold machines with 259 tools. * Eliminated cost of third shift; conducted time studies on register assembly, converting to assembly line process. Adjusted from one operator to three, redesigned work stations, balanced the line, and decreased cycle time.* Redesigned six assembly areas; transitioned from single operator work station to one-to-one sequencing line. Show less
-
-
Training and Kaizen Coordinator
-
2011 - 2014
Selected to oversee On-the-Job Training Team (OJT) with three certified trainers. Trained 400+ production new hires.PROCESS IMPROVEMENT* Recreated training structure to include both classroom and job specific floor training.* Ensured new hires met TS16949 criteria with validated certification. Maintained training and kaizen documentation, achieving 100% completion rate in training record audits.* Worked with production team to customize training based on floor and production needs. Show less
-
-
Mold Tech
-
2009 - 2011
Held technical position to troubleshoot processes and safeguard quality production. Prepared raw materials, set tools, and ensured machine stations met job start-up requirements.
-
-
-
UPS
-
United States
-
Truck Transportation
-
700 & Above Employee
-
Operations - Distribution Manager
-
2001 - 2008
Led team of nine supervisors in production floor pick, pack, ship, and return operations in multi-client atmosphere. Served 500K square feet Louisville location, then selected to design production layout for 400K square feet Chicago facility.PROCESS IMPROVEMENT* Led CDC for largest customer, GE Medical North America. Instrumental in turnaround of underperforming operation that involved production design of 40’ racks, work stations, processes, and workflow. Improved KPI performance from 60% to 99.5% for inbound and outbound orders. * Collaborated with GE engineers to redesign logistics that improved transportation lanes for repair dispatch.* Lowered inventory levels via updated storage strategies for slow and non-moving products.* Created new slotting strategy that improved picking efficiency and reduced customer order turn time. Show less
-
-
Industrial Engineering - Project Manager
-
2002 - 2004
Commuted weekly to Chicago for 22-month project. Represented Engineering team in consolidation of six buildings to two locations to serve customer more rapidly. Worked closely with Industrial Engineering, Plant Engineering, Operations, Human Resources, and regional management. PROCESS IMPROVEMENT* Provided analysis of building, land, and location feasibility options with processes and layouts; resulted in two building solution and savings of $2.5M annually.* Implemented new Warehouse Management System (WMS) for integration of customer, GE Healthcare.* Improved staffing efficiency with staggered start times, shift changes, and process improvements that realized labor savings over $2.5M annually.* Partnered with new acquisition company to improve drayage routing of freight transportation lanes to and from Chicago O’Hare airport. Show less
-
-
Industrial Engineering - Building and Facilities Supervisor
-
2002 - 2002
Held analytic supervisory position for building and facilities throughout Central Region that served 15 states. Accountable for first-line review of real estate, finance, and capital expenditure between $2500 and $50M+. PROCESS IMPROVEMENT* Analyzed ROI, evaluated vendors, and performed cost saving assessment, collaborating across teams, for presentations to REFCO Committee.* Managed square footage, price, and contract leases for 89 locations throughout the region. Show less
-
-
Industrial Engineering - Engineering Supervisor
-
2001 - 2002
Conducted daily volume forecasting for nine operating centers in Indiana District. Applied UPS Standard Operating Procedures (SOPs) to each job function with time values and optimal processes. PROCESS IMPROVEMENT* Tracked production and volume trends that determined labor and route business plans for South Division.* Enhanced staffing models and processes for work station set-up, slotting, and area design.
-
-
Community
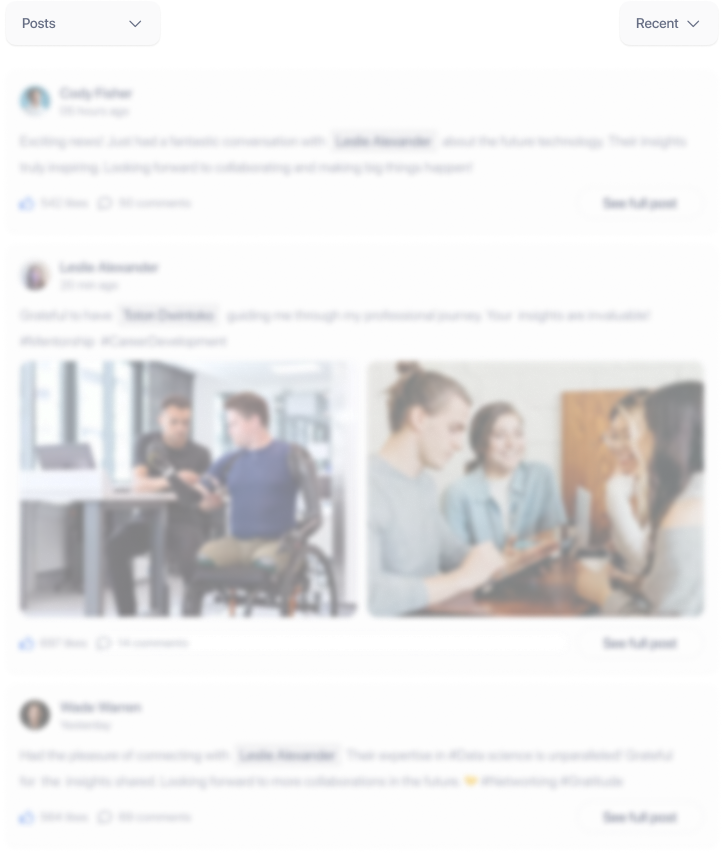