Jeffrey Pass, MBA, PMP
Senior Project Manager at Paramount Tool Company Inc- Claim this Profile
Click to upgrade to our gold package
for the full feature experience.
Topline Score
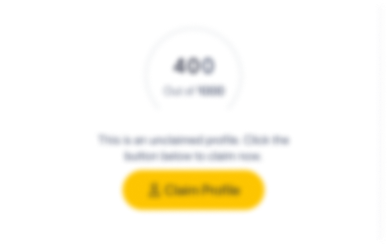
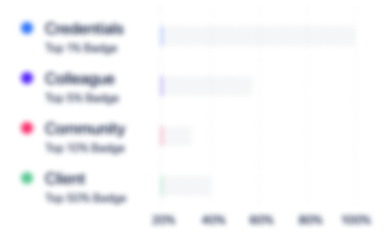
Bio

Jasen Haskins
Jeff is the type of person that people enjoy working with. His positive can do attitude helps him work within a team environment. Jeff positively motivates people while focusing on the budget, schedule, and finished product. Jeff seeks ways to simplify problems vs creating a complicated research project. Jeff understands the importance of seeking advice and taking the time to listen. Jeff is a good project engineer and project manager. I would hire him again.

Jeremy Bekritsky
I had the pleasure of working on a number of projects with Jeff. My perceptions are that he is on-point, an effective communicator, is efficient about his work, and delivers good results. He has earned my strong endorsement.

Jasen Haskins
Jeff is the type of person that people enjoy working with. His positive can do attitude helps him work within a team environment. Jeff positively motivates people while focusing on the budget, schedule, and finished product. Jeff seeks ways to simplify problems vs creating a complicated research project. Jeff understands the importance of seeking advice and taking the time to listen. Jeff is a good project engineer and project manager. I would hire him again.

Jeremy Bekritsky
I had the pleasure of working on a number of projects with Jeff. My perceptions are that he is on-point, an effective communicator, is efficient about his work, and delivers good results. He has earned my strong endorsement.

Jasen Haskins
Jeff is the type of person that people enjoy working with. His positive can do attitude helps him work within a team environment. Jeff positively motivates people while focusing on the budget, schedule, and finished product. Jeff seeks ways to simplify problems vs creating a complicated research project. Jeff understands the importance of seeking advice and taking the time to listen. Jeff is a good project engineer and project manager. I would hire him again.

Jeremy Bekritsky
I had the pleasure of working on a number of projects with Jeff. My perceptions are that he is on-point, an effective communicator, is efficient about his work, and delivers good results. He has earned my strong endorsement.

Jasen Haskins
Jeff is the type of person that people enjoy working with. His positive can do attitude helps him work within a team environment. Jeff positively motivates people while focusing on the budget, schedule, and finished product. Jeff seeks ways to simplify problems vs creating a complicated research project. Jeff understands the importance of seeking advice and taking the time to listen. Jeff is a good project engineer and project manager. I would hire him again.

Jeremy Bekritsky
I had the pleasure of working on a number of projects with Jeff. My perceptions are that he is on-point, an effective communicator, is efficient about his work, and delivers good results. He has earned my strong endorsement.

Credentials
-
PMP- Project Management Professional
Project Management InstituteMar, 2015- Nov, 2024
Experience
-
Paramount Tool Company Inc
-
United States
-
Automation Machinery Manufacturing
-
1 - 100 Employee
-
Senior Project Manager
-
Feb 2022 - Present
• Manages all aspects of new assembly cell fabrication projects from concept to installation • Prepares schedules, timelines, change order quotations, and applicable documentation • Manages cost vs budget to ensure ventures are profitable with both labor and material purchases • Collaborates with cross functional team including sales, design, assemblers and vendors to ensure reliable and robust machines are delivered to customers. • Works with remote customers, vendors, and installation teams for design reviews and in-field troubleshooting • Manages projects through Job Boss E2 ERP system • Actively manages 5-15 concurrent projects from $900 to $4.5M, while implementing continuous improvement projects for internal profitability increases. • Mentors & trains coworkers on appropriate communication pathways, principles, and PM activities to ensure consistent communication and transparent reporting. • Working to define and develop new project management department in an iterative, diverse, agile-minded environment Show less
-
-
-
Audible Cone
-
Grant County, OR
-
Director Of Product Development
-
Jul 2019 - Present
Managing design, logistics, marketing material, cost analysis and validation, pricing structure, industry applicability, testing, and manufacturing ramp-up for a start-up company Managing design, logistics, marketing material, cost analysis and validation, pricing structure, industry applicability, testing, and manufacturing ramp-up for a start-up company
-
-
-
Solutions CPAs
-
John Day, Oregon, United States
-
Auditor / Tax Preparer
-
Sep 2020 - Feb 2022
Prepared local business and individual tax returns Worked as a team for municipal auditing of accounts, projects, and public fund usage. Prepared local business and individual tax returns Worked as a team for municipal auditing of accounts, projects, and public fund usage.
-
-
-
Motive Power
-
United States
-
Railroad Equipment Manufacturing
-
1 - 100 Employee
-
Technical Project Manager
-
Sep 2017 - Jul 2019
-Used root cause analysis for shop floor & fabrication issues - Identified and worked to correct inconsistencies in the bills of material (BOM) to fit the proper work cell function. - Single point of contact between customer and project team for all technical questions and concerns. - Worked with management team to assess schedule impacts and change order requests - Ensured accuracy between contract and manufacturing execution. - Planned and helped develop project deliverables and schedules for new contracts - Managed engineering portion of project development regarding budgets and schedules - Ensured compliance of final product to contract requirements - Reviewed all project technical documents and ECO’s as necessary - Responsible for locomotive weight management - Directly interfaced with customers and leadership as needed to communicate technical info and design intent. -Provided leadership to multi-functional technical teams Show less
-
-
-
Capella University
-
United States
-
Higher Education
-
700 & Above Employee
-
Graduate Student
-
Aug 2016 - Apr 2018
MBA program focused on operations, finances, and improving efficiencies for companies seeking growth. Main topics: Operational excellence, continuous improvement, capital project validation MBA program focused on operations, finances, and improving efficiencies for companies seeking growth. Main topics: Operational excellence, continuous improvement, capital project validation
-
-
-
Danone
-
France
-
Food and Beverage Manufacturing
-
700 & Above Employee
-
Sr Project Manager
-
Aug 2016 - Mar 2017
Fostered collaboration between cross-functional, multi-cultural teams of 10-50 individuals to advance common project goals. Coordinates scope changes and setbacks to project timelines. Maintains/updates financial savings files, ensuring accuracy. Communicates with upper management to support informed decision making regarding investment of savings and capital expenditure budgets. Facilitates knowledge sharing among team members and onboards/trains/mentors new hires. Tasked to lead a high-profile project to reduce the carbon footprint of yogurt production and save $62K/month. Provided documentation to support plans for four other product formats featuring the same polymer change expected to save up to $350K/month in 2017. Improved profits by spearheading initiatives focused on reducing costs ($200K-$1.7M) and elevating quality. Met plant downtime goals, enabling material trials to be started in order to reach deadlines. Developed cost savings calculation tools used to show current project status; aligned all needed components to effectively test savings theories. Restructured inherited unrealistic project schedules and prepared detailed plans to facilitate future projects into 2018; built in buffers to help offset unseen delays or complications and sustain project/team credibility. Show less
-
-
-
Memry Corporation
-
United States
-
Medical Device
-
1 - 100 Employee
-
Manufacturing Engineer
-
Jun 2015 - Aug 2016
Focused on keeping nine production lines operational and at maximum capacity. Managed continuous improvement projects and identified opportunities to increase profitability. Created new procedures, fixtures, tooling, and inspection qualifications; redesigned and refurbished existing machinery. Addressed and resolved issues related to quality, machinery, repeatability, and customer returns. Served as a subject matter expert to maintain up-to-date training records for all production staff. Functioned as the main programmer for a 2D CAM machine (Werth measurement system). Mentored fellow engineers in tooling design, machine troubleshooting, report generation, and overall good engineering practices. Aligned workflow with production improvements, product line sustainability, and facility worker training schedules for projects ranging in scope from $10K/year to $120K/year. Prepared a proposal to purchase a $70K piece of capital equipment. Boosted productivity for one product line with an updated trimming fixture that not only expedited processing time from ~30 seconds per piece to ~10 seconds per 5 pieces, but also slashed the overall reject rate by 60%. Identified and investigated significant inconsistencies with actual production speed versus recorded production speed and initiated corrective measures across seven product lines, resulting in much higher production capacity, Introduced a new visual standard for another product on a legacy line, which dramatically cut reprocessing time and reject percentage while substantially increasing production speed. Extended improvements to the chemical processing department by using DirectSoft6/Automation Direct software to develop a new PLC recipe control system that decreased parts defects by up to 50%, saving thousands of dollars per week in scrapped parts and propelling yield from 38% to 70%. Show less
-
-
-
Emerson
-
United States
-
Industrial Machinery Manufacturing
-
700 & Above Employee
-
Project Engineer - Systems, Precision Cleaning
-
Aug 2013 - Jun 2015
Promoted to transform customer concepts into fully customized industrial cleaning equipment, including multi-stage cleaning stations and a 2D pick and place robot. Administered cradle-to-grave project development, encompassing BOM preparation, electronic selection and interface, 3D models, 2D production drawings, fabrication process control, and technical operation manuals for customers. Aligned form and function by designing effective routing for all components, including wires, piping, flow, and thermal insulation templates. Loaded programs into PLCs. Troubleshot equipment setup and manufacturing issues on the production floor. Brought various teams together to achieve desired product quality within budgets and projected delivery dates. Identified and drove efforts to minimize excessive internal costs related to manufacturing, obsolescence, and product flow. Increased profitability by developing a system to identify/eliminate sources of scrap and utilize common components. Established finishing specifications that accelerated the approval process, heightened production floor autonomy, and boosted engineering productivity. Led development of a custom finishing booth that enabled standardized product quality across all product lines and platforms. Pioneered a fully custom, fully enclosed system with a unique PLC language used to control, within one degree Fahrenheit, an ultrasonic vibration and heated bath for acid etching platinum parts. Responded to a recall that followed an in-field catastrophic failure by supporting product redesigns and upgrades of ‘off the shelf’ items created by the group, including sourcing new component suppliers and updating records. Advocated for the engineering group’s adoption of SolidWorks Electrical to streamline component selection and wire selection/routing; initiated database development and prototype runs. Show less
-
-
Applications Development Engineer
-
Jun 2011 - Aug 2013
Interfaced with sales, customers, and internal manufacturing staff. Provided cost-effective solutions to customer applications for plastic joining/spin welding. Simplified complex assemblies to produce customers’ desired outcomes within cost. Designed prototype tooling to validate customer concepts for production. Simplified and communicated complex scenarios for ease of understanding by all stakeholders. Troubleshot failure modes and resolved them for customer applications, on and off site. Presented hands-on training to customers. Completed complex design reviews within strict customer-set schedule for multiple concurrent projects. Mentored new hires in application development, technical report writing, and welder troubleshooting. Supported tooling design and development as the single point of contact for spin welding in Connecticut. Chosen to represent the company at tradeshows such as Assembly Tech and NPE. Brought together tooling engineers, sales team members, customers, lab staff, and other applications engineers to develop the most robust solutions with a process-neutral approach. Enhanced reporting consistency, group efficiency, and quality by developing applications templates that featured interactive SolidWorks designs and pre-filled bullet lines, which reduced turnaround time from an average of 4.1 days to 3.2 days—the templates were adopted globally by all overseas facilities (Germany, China, India). Elevated awareness of safety issues and strived to foster a safety-centric work culture. Recognized as a top performer in quality and quantity of applications executed; maintained the highest monthly average for two consecutive years. Show less
-
-
-
ACMI
-
Medical Device
-
100 - 200 Employee
-
Assistant Manufacturing Engineer - Shared Services
-
May 2009 - Dec 2009
World’s leading supplier of medical visualization and energy systems Initiated the build and design of a universal durability testing machine to be used across all product platforms and all corporate locations to establish a global acceptance criteria / test procedure. This was the main focus of this internship. Ensured proper methods were being followed for all product assembly, and addressed issues with tooling / operators / tool makers accordingly. Helped to analyze new optical assembly and compare to the previous generation to determine percent improvement versus cost, to validate the cost to benefit of a new assembly. Assisted R&D with any additional projects that came along, such as analysis of failure modes in the field, and ways to reduce / eliminate them. Show less
-
-
-
ACMI
-
Medical Device
-
100 - 200 Employee
-
Assistant Manufacturing Engineer - Digital Value Stream
-
Aug 2008 - Dec 2008
World’s leading supplier of medical visualization and energy systems. Assisted in implementing new product line into manufacturing. Creating method sheets, most effective production procedures, product validation builds, quality / acceptance criteria and testing methods, and helped to design tooling for ease of manufacturing. Attended R&D meetings to discuss potential changes / fixes to issues seen in development of assembly process, then implemented changes where needed to the assembly procedure. Created fixtures to reduce cost of failure from over $1000 down to approximately $200 per piece by preemptive inspection. Show less
-
-
-
Wytech Industries
-
Rahway, NJ
-
Assistant Manufacturing Engineer
-
Jan 2008 - May 2008
World leader in the manufacture of components for the medical device industry. Retrofit of optical sensor array system to reinstate a center-less grinding machine that was previously not capable of use for production. Repair and retrofit sand blasting machine to assist in stripping wire coating for annealing processes. Designed and manufactured (personally, via bridgeport machine) tooling to improve product machining lead time per part (reduction from ~1min per part, to ~25 seconds per part). Established useful acceptance criteria for large product runoffs. Updated documentation to reflect current process more precisely. Show less
-
-
Education
-
Stevens Institute of Technology
Bachelor of Engineering (B.E.), Mechanical Engineering, Mechatronics, Robotics, and Automation Engineering -
Capella University
MBA, Entrepreneurship/Entrepreneurial Studies