Jeffrey Norris
Production Supervisor at Heating & Cooling Products, Inc.- Claim this Profile
Click to upgrade to our gold package
for the full feature experience.
-
English -
-
Spanish -
-
German -
Topline Score
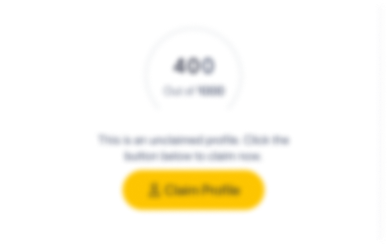
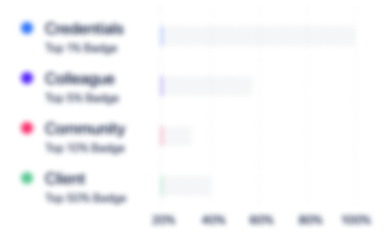
Bio


Credentials
-
American Chemical Society
Chemical Abstract ServiceJun, 1995- Oct, 2024 -
Food Safety Manager Certification (FSMC)
American National Standards InstituteNov, 2020- Oct, 2024 -
Emergency Medical Technician
State of Ohio Department of Public Safety
Experience
-
Heating & Cooling Products, Inc.
-
United States
-
Wholesale Building Materials
-
1 - 100 Employee
-
Production Supervisor
-
Aug 2022 - Present
-
-
-
PharmaCann Inc
-
United States
-
Alternative Medicine
-
400 - 500 Employee
-
Processing Manager
-
Aug 2020 - Aug 2022
-
-
-
Hitachi Astemo
-
Japan
-
Motor Vehicle Manufacturing
-
700 & Above Employee
-
Senior Engineering Technician, Tech Staff
-
Feb 2018 - Aug 2020
Work in high speed high production rate environment for automotive part production of Tier 1 automotive part supplier for foreign and domestic automotive supplier. Work with CNC lathe, Fanuc Robotics, Chrome platting, various hydraulic and pneumatic fixtures and assemblies and equipment to maximize production uptime and minimum downtime as well as scrap reduction and maximum safety and ergenomics. Work in high speed high production rate environment for automotive part production of Tier 1 automotive part supplier for foreign and domestic automotive supplier. Work with CNC lathe, Fanuc Robotics, Chrome platting, various hydraulic and pneumatic fixtures and assemblies and equipment to maximize production uptime and minimum downtime as well as scrap reduction and maximum safety and ergenomics.
-
-
-
-
Electrical Engineer
-
Feb 2019 - Jun 2019
Machine Specialist in CNC, and electrical engineering/PLC/automation. Machine Specialist in CNC, and electrical engineering/PLC/automation.
-
-
-
Covert Manufacturing, Inc.
-
United States
-
Motor Vehicle Manufacturing
-
1 - 100 Employee
-
Machine Specialist
-
Aug 2017 - Feb 2018
Machine builds, panel builds, CNC maintenance, robot integration and rebuild/programming, AB PLC work, precision machining. Machine builds, panel builds, CNC maintenance, robot integration and rebuild/programming, AB PLC work, precision machining.
-
-
-
AK Steel Corporation
-
United States
-
Mining
-
700 & Above Employee
-
Maintenance Manager
-
Sep 2016 - Aug 2017
Manage union hourly employees and workday to improve maintenance up-time and reliability as well as maintain consistent safety of plant employees and maintenance personnel through daily supervision and observations. Resolve conflicts as they arise and act as an intermediary between corporate production goals and policy compliance and enforcement while ensuring safety and OSHA compliance of union employees and conformance to contract negotiated outlines. Troubleshooting of mechanical and electrical problems as they arise and delegate personnel based upon union guidelines and experience. Schedule overtime daily as need arises and for engineering projects to meet production requirements while reducing impact to production. Environmental and safety inspections as well as housekeeping inspections of various assigned areas. Review of various procedures for improving processes and personnel. Report to upper management daily for plant downtime and maintenance issues.
-
-
-
RobotWorx
-
United States
-
Automation Machinery Manufacturing
-
1 - 100 Employee
-
Program Manager
-
Apr 2016 - Sep 2016
Managed projects and assisted with production schedules as well as budgeting of programs and component ordering as well as timeline preparation for customer approval. Assisted sales in preparation of proposal packages for presentation to customers for approval. Managed projects and assisted with production schedules as well as budgeting of programs and component ordering as well as timeline preparation for customer approval. Assisted sales in preparation of proposal packages for presentation to customers for approval.
-
-
-
-
Electrical Engineer
-
Jul 2015 - Jun 2016
Design PLC interface for screw machine upgrade and servo encoder upgrades. Including design of electrical drawings, bill of materials, and equipment specifications. Troubleshoot electrical issues with various equipment and machine centers. Supervise maintenance personnel and lead in direction for repairs and supervise project implementation. Provide capital budgets as required and ROI projections. Design PLC interface for screw machine upgrade and servo encoder upgrades. Including design of electrical drawings, bill of materials, and equipment specifications. Troubleshoot electrical issues with various equipment and machine centers. Supervise maintenance personnel and lead in direction for repairs and supervise project implementation. Provide capital budgets as required and ROI projections.
-
-
-
PPG
-
United States
-
Paint, Coating, and Adhesive Manufacturing
-
700 & Above Employee
-
Electrical Engineering Technician
-
Nov 2015 - Apr 2016
Electronics, Robotics, Programming, Industrial Electrical, Engineering support. Extensive experience in Fanuc robotics troubleshooting and programming as well and time studies for process improvement. Troubleshooting in PLC networking and programming as well as furnace control programs to prevent downtime and safety issues related to production. Laser and vision inspection systems experience as well as ultrasonic. Report daily to engineering manager as well as plant manager for KPI. Schedule engineering projects as required as well production improvement projects.
-
-
-
Ariel Corporation
-
United States
-
Oil and Gas
-
400 - 500 Employee
-
Senior Maintenance Technician
-
Oct 2014 - Nov 2015
Perform all aspects of machine repair for compressor manufacturer. Includes robotics (Fanuc), PLC (Mitsibushi, Allen Bradly, Fanuc, etc). Repairs and experience includes facilities (extensive plumbing and electrical), mills (CNC and manual), CNC Machine centers, lathes (CNC and manual), ladder logic programing of PLC, network and ethernet interface with equipment. Precision machining of required repair parts, along with MRO inventory maintenance and ordering of parts required. Experience and training in SAP inventory management system. Servo motor replacement and encoder repairs. Experience includes repairs using, and repair of welding equipment (stick, MIG, TIG, and wire feed for stainless and steel). Troubleshooting includes all aspects of communication, PLC, electronic, electrical (110/208/480 VAC and 5/24 volt DC controls), hydraulic, pneumatic, and finally mechanical as the need arises. Supervised apprentices and their training.
-
-
-
Cardington Yutaka Technologies
-
United States
-
Motor Vehicle Manufacturing
-
100 - 200 Employee
-
Maintenance Technician I
-
Sep 2013 - Oct 2014
Perform all aspects of high speed/high production rate automotive manufacturing equipment repair. Includes robotics (Fanuc, Motoman, OTC, Panasonic), PLC (Mitsibushi, Allen Bradly, Fanuc, etc). Repairs and experience includes facilities, mills (CNC and manual), CNC Machine centers, lathes (CNC and manual), inline feeders, bowl feeders, ladder logic programing of PLC, laser detect and fiber optics, network and ethernet interface with equipment, and pipe bending centers/presses, inventory control using laser and RF tracking. Large scale (3000 TON) Japanese press repair and synchronization, as well as preventive maintenance of all and various aspects. Precision machining of required repair parts, along with MRO inventory maintenance and ordering of parts required. Servo motor replacement and encoder repairs. Experience includes repairs using, and repair of welding equipment (MIG, TIG, wire feed and resistance and laser for stainless, steel, copper and aluminum). Troubleshooting includes all aspects of communication, PLC, electronic, electrical (110/208/480 VAC delta and Y and various DC controls and drive units), hydraulic, pneumatic, and finally mechanical as the need arises. Camera and laser (QA/QC and inspection systems) maintenance included as well.
-
-
-
Potemkin Industries Inc
-
United States
-
Accounting
-
1 - 100 Employee
-
Machinist
-
2013 - Sep 2013
Perform all aspects job shop experience to prepare production assemblies for shipment using Mazatrol CNC centers. Experience includes both CNC milling and CNC lathe experience. I utilize my own personal precision hand tools for all aspects of first piece inspection as well as ongoing quality control inspection throughout the process. Trained in safety and bench work layout as well as blueprint reading and set-up, and finally fixturing and tooling required for process conformance as well as required efficient change-overs. Position requires operations of multiple machines at times (both mill and lathe) for one piece flow as well as little supervision, while other times integration into a team environment.
-
-
-
HI Stat Manufacturing
-
United States
-
Appliances, Electrical, and Electronics Manufacturing
-
1 - 100 Employee
-
Advanced Development Product Engineer (Chemist)
-
2004 - Oct 2012
Function as Project/Program Manager and team leader while providing continuing production support cross-functionally over various product team phases. Program Management tools include Gantt charts, timelines, project expense authorization submittals, ROI calculations, capital expense and payback for investment schedules, budget preparations, and cost of capital determinations, as well as weekly team meetings and gate/design reviews. Perform all aspects of research and development including supervision/support of outside laboratories responsible for: metallurgical review of metals, welds, weld processes, new materials development, and interfaces. Assignments included research and development of new material applications for polymers, plastics, dielectrics, alloys, coatings, and corrosion inhibitors. Experience with plating, electrolytic coatings, ceramic coatings, ceramic metal oxides, precious metal platting and flash coats to prevent electrolytic base material ion migrations, corrosion inhibitors, galling inhibitors, and high temperature high corrosion resistance coatings that can be processed in high speed production with reduced labor. Prepare quarterly budgets, yearly equipment budgets, and evaluation of launch projects for EBIT, ROA and capital tooling requirements. Testing responsibilities include: AA, SEM/EDX, GC/MS, GC, surface finish, hardness, metallurgical mounts/cross-sections/analysis for weld penetration studies. Experience in weld development includes ultra-sonic, spin, resistance, MIG, TIG, plasma, and laser. Experience in processes includes laser weld development, resistance welds, solid state dissimilar precious metals and stainless steel welds, ceramic welds and ceramic wafer interfaces, ultrasonic welds, induction pre-/post- heating processes, and selective/controlled atmosphere TIG/MIG weld processes. Research involves improvement for high-speed low scrap processes involving weld analysis, metallurgical review of interfaces.
-
-
Product Engineer II (Chemist)
-
2000 - 2004
Design and develop new automotive (Tier I, II, III supplier) environmental emission control sensor products (using IDEAS 2D and 3D Modeling) for high volume (>500,000) production that will be of high quality (meet Divisional goals for internal PPM first runs yields), meet cost objectives (value engineering using polymer and material specifications), meet product performance goals (ISO/TS-16949 and QS-9000 customer compliance), and be on schedule. Direct Product Engineering Technicians through all phases of testing (ED/DV/PV using DVP&R) and line debug (using PFMEA). Responsible for DOE and failure root cause analysis as well as perform Design for Six Sigma projects. Interact with customer and sales for development/interpretation of application and specifications in effort to create DFMEA and risk/lifetime failure determinations. FEA analysis on new product proposals and failure determination on existing product for continuous improvement. Responsible for project time lines (Gantt charts using Microsoft Project). Approval of all production/product deviations in assembly of finished good(s), as well as write BOMs, internal specifications, SOPs for laboratory practices, and MWIs for production procedures. Spring design, stamping specifications, and new compound development with vendors for special application rubbers and films. Mold flow analysis and plastic polymer selection based upon FEA modeling. Platting research for contact and stamping development of low voltage oil submerged applications.
-
-
-
Fairfield Engineering Company
-
United States
-
Consumer Goods
-
Chemical Engineer/Engineering Manager
-
1997 - 2000
Performed all phases of start-up, design, and repair of commercial/municipal freshwater/wastewater and conveyor equipment. Assisted sales with technical client consultations, estimates, specifications, and proposals. Responsible for computer upgrades and PLC program development. Experience included chemical, electrical, mechanical, and hydraulics. Sole responsibility for all control panel specifications and designs, electrical interfaces, hydraulic control and interfaces, and chemical applications. Further responsibilities included review of blueprint submittal packages, training of new personnel, personnel management, maintenance of server, CAD program review, general accounting functions, fiscal reports for board, and quality assurance. Design responsibilities included control panel units, pump specification for waste water handling, conveyor design/specification, structural design/specification for bar-screen units, HP calculations and pump lift calculations, motor/gearbox units for screen design, water screw lift station design, pump stations for municipal installations, repair/upgrade design of existing waste water and fresh-water/potable water installations in commercial and municipal applications. Managed and directed hourly employee (unionized) fabrication of all equipment. Extensive chemical knowledge required for materials applications in corrosive and aggressive environments. Extensive knowledge and training in NFPA/NEC, as well as Federal/State EPA regulations and codes were required.
-
-
Education
-
The Ohio State University
Bachelor of Applied Science - BASc, Chemisty/Chemical Engineering & Business -
Knox County Career Center
NIMS Certified CNC Machinist, Heavy/Industrial Equipment Maintenance Technologies -
Miami University
Electro-Mechanical Engineering, Electrical and Electronics Engineering -
North Central State College
Associate of Science (A.S.), Electrical and Electronics Engineering -
North Central State College
Associate of Science (A.S.), Mechanical Engineering -
Community College of the Air Force
Associate's degree, Clinical Laboratory Science/Medical Technology/Technologist -
Ashland University
Bachelor of Applied Science - BASc, Pharmacology and Toxicology
Community
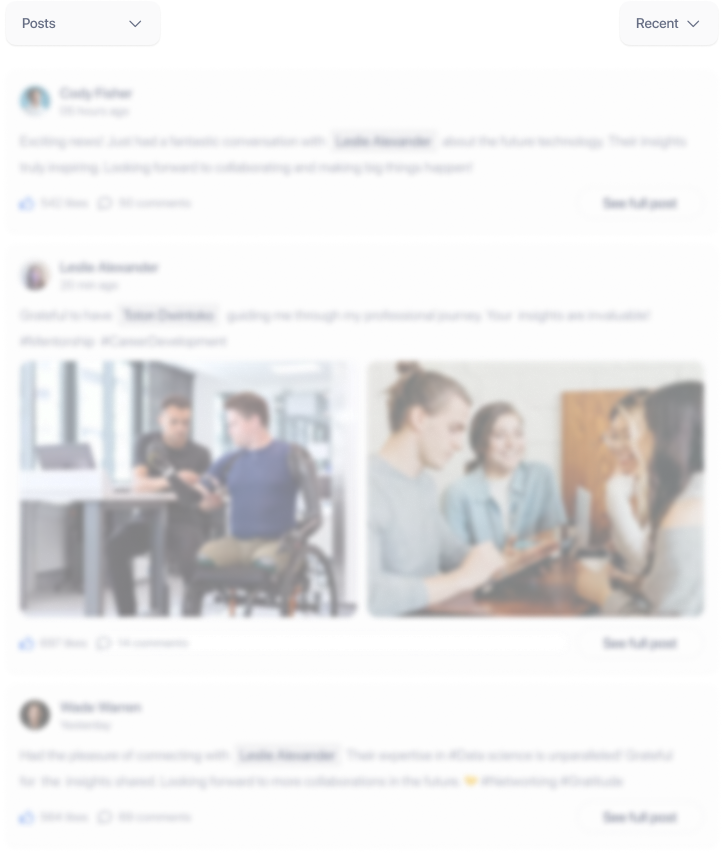