Jeffrey Johnson
Production Control Coordinator at United Alloy- Claim this Profile
Click to upgrade to our gold package
for the full feature experience.
Topline Score
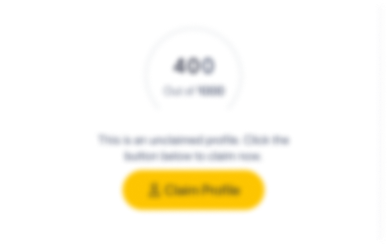
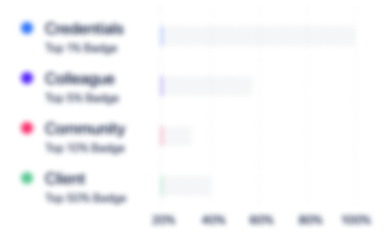
Bio


Experience
-
United Alloy
-
United States
-
Industrial Machinery Manufacturing
-
1 - 100 Employee
-
Production Control Coordinator
-
Oct 2022 - Present
-
-
Receiving Coordinator
-
Jan 2022 - Oct 2022
-
-
-
NFI
-
United States
-
Transportation, Logistics, Supply Chain and Storage
-
700 & Above Employee
-
Warehouse Operations Supervisor
-
Nov 2021 - Jan 2022
Responsible for the efficient day-to-day operation of the warehouse with particular emphasis on the supervising warehouse personnel and achieving daily production goals. Develops and implements shipping and receiving work schedules and assignments to assure effective and efficient operations to meet goals. Provides direct supervision to warehouse personnel matching skill and background of personnel to work required. Supervises all inbound and outbound shipments to ensure they are correct and carried out in a timely fashion. Reviews the daily work objective and determines productivity requirements to produce during the shift to meet the overall building objectives. Partners with other leaders to balance labor ensuring appropriate levels of staffing. Drafts and submits daily end of shift report. Makes recommendations to management on initiatives and programs to improve operations and works on those programs. Conducts the daily pre-shift meetings covering previous shifts productivity, operational problems, forecasting workload and any other pertinent company information. Assists in developing a program to train and motivate personnel for increased effectiveness. Ensures the safe, clean and efficient operation of the warehouse to meet service standards. Supports all safety programs and OSHA compliance to ensure a safe work environment for all employees. Show less
-
-
-
United Alloy
-
United States
-
Industrial Machinery Manufacturing
-
1 - 100 Employee
-
Inventory Control Specialist
-
Jan 2021 - Nov 2021
-
-
Inventory Control Specialist
-
Jan 2021 - Nov 2021
• Maintain inventory data integrity and track inventory accuracy- completes accurate and timely system transactions thru daily, weekly monthly review of exceptions reports.• Perform routine Cycle Counts of raw materials, hardware, work in progress inventory and finished products creating variance reports to maintain accurate inventory records.• Handles adjustment request and inventory issues from the floor employees or other company personnel.• Research root causes of inventory discrepancies by extracting data from the ERP system.• Creates and maintains organization of inventory in the stock room and the production floor.• Establishes partnership with other departments to build inventory accuracy, standard procedures, controls, practices, and systems.• Initiates physical and systematic inventory Non-compliant material request and follow thru completion.• Prioritize tasks and recommend improvements in inventory management.• Serve as back up for receiving to accurately account for raw materials received in according to the purchase order quantities, quality, and sizes according to measurements from blueprints using gauge checkers calipers and tape measures.• Creating orders for assemblers that include components to create a finished product.• Manage/Enter Job orders into the ERP system allowing for on time delivery of finished products.• Examine contents ad compare with the records, manifest and invoices to verify accuracy of incoming shipments.• Manage day to day receipts of purchased materials for production.• Perform material transactions using CSI EPR system to account for materials procured for the manufacturing of the end products for the customers. Show less
-
-
Stockroom coordinator
-
May 2019 - Jan 2021
-
-
-
Continental
-
Germany
-
Motor Vehicle Manufacturing
-
700 & Above Employee
-
Logistics Intern
-
Oct 2018 - Dec 2018
Continental Automotive Systems Logistics Intern 10/2018 to 12/2018 • Applied analytic methods or tools to understand, predict, or control logistics operations or processes. • Developed or maintained freight rate databases for use by supply chain departments to determine the most economical modes of transportation. • Develop or maintain models for logistics uses, such as cost estimating or demand forecasting. • Enter logistics-related data into databases. • Interpreted data on logistics elements, such as availability, maintainability, reliability, supply chain management, strategic sourcing or distribution, supplier management, or transportation. • Maintain databases of logistics information. • Review procedures, such as distribution or inventory management, to ensure maximum efficiency or minimum cost. Show less
-
-
-
Ryder System, Inc.
-
United States
-
Transportation, Logistics, Supply Chain and Storage
-
700 & Above Employee
-
Heavy Diesel Mechanic
-
Aug 2013 - Nov 2016
Ryder Truck Rental Oregon, IL Heavy Mechanic 08/2013 to 11/2016 • Adjust or repair computer-controlled exhaust emissions devices. • Attach test instruments to equipment to diagnose malfunctions. • Diagnose and repair vehicle heating and cooling systems. • Disassemble and overhaul internal combustion engines, pumps, generators, transmissions, clutches, and differential units. • Examine and adjust protective guards, loose bolts, and specified safety devices. • Follow green operational practices involving the conservation of water or energy or reduction of solid waste. • Inspect and verify parts to ensure conformance to factory specifications. • Inspect, repair, and maintain automotive and mechanical equipment. • Inspect, test, and listen to defective equipment to diagnose malfunctions, using test instruments such as handheld computers, motor analyzers, and chassis charts. • Maintain or repair vehicles with alternative fuel systems, including biodiesel, hybrid, or compressed natural gas vehicles. • Measure vehicle emissions to determine whether they are within acceptable limits. • Rebuild gas or diesel engines. • Rewire ignition systems, lights, and instrument panels. • Specialize in repairing and maintaining parts of the engine. • Use hand tools such as screwdrivers, pliers, wrenches, pressure gauges, and precision instruments, as well as power tools such as pneumatic wrenches, lathes, welding equipment, and jacks and hoists. • Operate forklift to move materials and help with vehicle repairs. Show less
-
-
-
Crete Carrier Corporation
-
United States
-
Transportation/Trucking/Railroad
-
700 & Above Employee
-
OTR Driver
-
Nov 2012 - Jul 2013
Crete Carrier Corp Lincoln, NV OTR Driver 11/2012 to 07/2013 • Check all load-related documentation for completeness and accuracy. • Check vehicles for mechanical, safety and emergency equipment in working order. • Collect delivery instructions verifying instructions and routes. • Follow appropriate safety procedures for transporting dangerous goods. • Inventory and inspect goods to be moved to determine quantities and conditions. • Maintain logs of working hours or of vehicle service or repair status, following applicable state and federal regulations. • Maneuver trucks into loading or unloading positions, following signals from loading crew and checking that vehicle and loading equipment are properly positioned. • Obtain receipts or signatures for delivered goods and collect payment for services when required. • Plan or adjust routes based on changing conditions, using computer equipment, global positioning systems (GPS) equipment, or other navigation devices to minimize fuel consumption and carbon emissions. • Read bills of lading to determine assignment details. Show less
-
-
-
Wisconsin Air National Guard
-
Milwaukee Wisconsin
-
Heavy Mobile mechanic
-
Nov 2005 - Oct 2011
Compile operational or personnel records, such as time and production records, inventory data, repair or maintenance statistics, or test results. • Conduct or arrange for worker training in safety, repair, or maintenance techniques, operational procedures, or equipment use. • Counsel employees about work-related issues and assist employees to correct job-skill deficiencies. • Design equipment configurations to meet personnel needs. • Determine schedules, sequences, and assignments for work activities, based on work priority, the quantity of equipment, and skill of personnel. • Develop or implement electronic maintenance programs or computer information management systems. • Develop, implement, or evaluate maintenance policies and procedures. • Examine objects, systems, or facilities and analyze information to determine needed installations, services, or repairs. • Inspect and monitor work areas, examine tools and equipment, and provide employee safety training to prevent, detect, and correct unsafe conditions or violations of procedures and safety rules. • Inspect, test, and measure completed work, using devices such as hand tools or gauges to verify conformance to standards or repair requirements. • Investigate accidents or injuries and prepare reports of findings. • Monitor employees' work levels and review work performance. • Monitor tool and part inventories and the condition and maintenance of shops to ensure adequate working conditions. • Participate in budget preparation and administration, coordinating purchasing and documentation and monitoring departmental expenditures. • Perform skilled repair or maintenance operations, using equipment such as hand or power tools, hydraulic presses or shears, or welding equipment. • Operate forklift to move materials loading and unloading trucks and trailers. • Operate overhead crane to move heavy vehicle parts. Show less
-
-
Education
-
South West Technical College, Fennimore, Wisconsin
Associate's degree, Logistics, Materials, and Supply Chain Management
Community
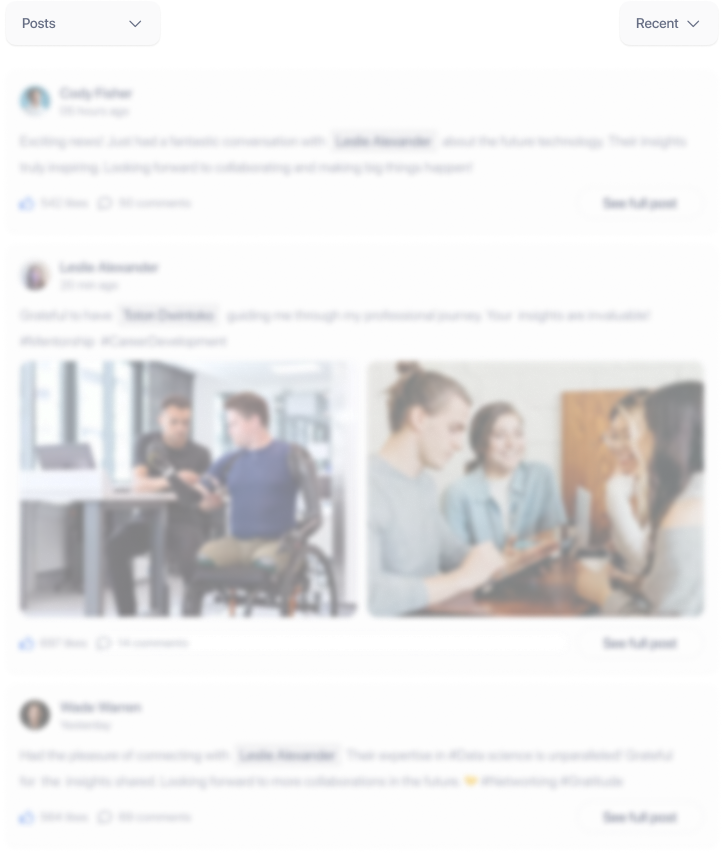