Jeff Taylor
Lead Commercial Project Manager at Lumbermen's Inc.- Claim this Profile
Click to upgrade to our gold package
for the full feature experience.
Topline Score
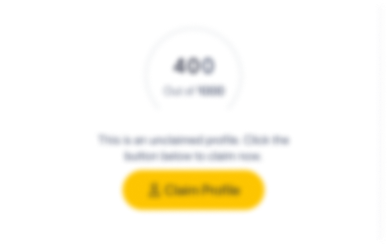
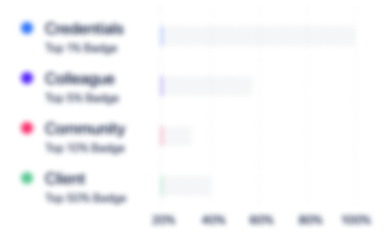
Bio


Credentials
-
Six Sigma Champion Certified
Management & Strategy InstituteOct, 2022- Nov, 2024 -
Lean Six Sigma Black Belt (LBBP)
Management & Strategy InstituteSep, 2022- Nov, 2024 -
Six Sigma Black Belt Professional (SSBBP)
Management & Strategy InstituteAug, 2022- Nov, 2024 -
30 Hour Construction Industry Outreach
360trainingMay, 2022- Nov, 2024 -
Certified Associate in Project Management (CAPM)
Career AcademySep, 2021- Nov, 2024 -
Security Reaction Force - Advanced (SRF-A)
UNITED STATES DEPARTMENT OF THE NAVYMay, 2010- Nov, 2024 -
AN/USM-458C Electronic Attack (EA) Suite Intermediate Maintenance
UNITED STATES DEPARTMENT OF THE NAVYJun, 2009- Nov, 2024 -
Avionics Electronics Technician (AVN)
UNITED STATES DEPARTMENT OF THE NAVYApr, 2009- Nov, 2024 -
Project Management Professional (PMP)®
Project Management InstituteOct, 2022- Nov, 2024
Experience
-
Lumbermen's Inc.
-
United States
-
Wholesale Building Materials
-
100 - 200 Employee
-
Lead Commercial Project Manager
-
Jan 2023 - Present
● Evaluate project proposals, specifications, and blueprints to grasp the project's entirety and facilitate seamless coordination across all phases. ● Estimate project timelines, labor needs, material costs, and product expenses to determine accurate cost projections for construction projects, supporting well-informed decision-making. ● Provide meticulous quantity takeoff information, compiling detailed material lists and assessing overall construction expenditures to maintain precise cost control and budget adherence. ● Plan and coordinate construction operations, meticulously scheduling intermediate phases and optimizing resource allocation to ensure on-time project completion and adherence to milestones. ● Monitor and assess project progress, consistently offering detailed progress reports that inform stakeholders and enable data-driven adjustments to ensure timely achievement of project milestones. ● Collaborate cross-functionally to prepare comprehensive documentation, reports, and presentations that effectively communicate project status, ensuring transparency, accountability, and informed decision-making throughout construction projects. ● Play a key role in maintaining accurate loan files and databases, implementing a robust organization system that enhanced team efficiency and facilitated seamless audits, leading to consistent compliance with regulatory guidelines. Show less
-
-
-
Hard Rock Stone Works
-
United States
-
Manufacturing
-
1 - 100 Employee
-
Project Manager
-
Aug 2018 - Jan 2023
● Lead a team of 12 employees through 5 large-scale commercial projects concurrently, valued up to $3.3 million guiding projects from the bid phase through the completion ● Negotiate with an architect and general contractor on a $500,000 project, achieving a 10% decrease in project costs ● Manage a 10-worker cross-functional project team, integrating changes to the scope & schedule in real-time, controlling costs, and allocating resources, delivering a successful execution within 3 months and $450,000 budget ● Ensure a safe work environment through the implementation of safety awareness programs and 100% compliance with Occupational Safety and Health Act (OHSA) regulations ● Conduct 4 financial evaluations annually to attain budgetary objectives and adjust project constraints, accordingly, promptly communicating changes to the team to stay on time with deliverables Show less
-
-
-
Avancez LLC
-
Warren, MI
-
Manufacturing Engineer
-
Sep 2017 - Aug 2018
● Collaborated with 20+ staff through 10 complex process improvement projects, working with departments to establish deliverables, resolve obstacles, and deliver 100% on-time solutions ● Led 12 planning teams through business readiness phases, using project methodology such as Lean and Six Sigma to facilitate new cost-saving processes, saving approximately $110,000 year over year ● Reviewed causes of downtime, identifying areas for improvement, and implementing solutions, reducing production waste by 23% in production ● Spearheaded the management and implementation of 80 continuous improvement initiatives, streamlining operations to enhance process quality by 28% Show less
-
-
-
Adient Automotive Seating
-
Auburn Hills, MI
-
Production Manager
-
Oct 2015 - Sep 2017
● Collaborated with 20+ staff through 10 complex process improvement projects, working with departments to establish deliverables, resolve obstacles, and deliver 100% on-time solutions ● Led 12 planning teams through business readiness phases, using project methodology such as Lean and Six Sigma to facilitate new cost-saving processes, saving approximately $110,000 year over year ● Reviewed causes of downtime, identifying areas for improvement, and implementing solutions, reducing production waste by 23% in production ● Spearheaded the management and implementation of 80 continuous improvement initiatives, streamlining operations to enhance process quality by 28% Show less
-
-
-
FCA Fiat Chrysler Automobiles
-
United Kingdom
-
Motor Vehicle Manufacturing
-
700 & Above Employee
-
Production Supervisor
-
Feb 2014 - Oct 2015
● Supervised a continuous and rigorous production schedule, ensuring compliance with 100% of safety and quality standards, facilitating production outcomes through the management of 130 staff members ● Created standard workflows for set-up operations, benefiting 120 employees and increasing quality measures by 28% through add-on implementation ● Directed a cost-effective manufacturing process, using Lean, Six Sigma, and Statistical Process Control (SPC) techniques to deliver results, such as decreasing scrap by 35% using Quick Response Quality Control (QRQC) Show less
-
-
-
ED Brands
-
Whitmore Lake, MI
-
Production Supervisor
-
Jun 2012 - Feb 2014
● Oversaw the planning and cost estimation of 50 projects over 2 years, organizing activities to remain on time and collaborating with 18 coworkers to deliver projects 100% with agreed criteria ● Led 30 quality assurance checks monthly, optimizing workflow processes and reducing waste by 32% ● Trained 8 new employees on material handling and production line expectations, onboarding staff efficiently to reduce missed shipments by 20% in 4 months ● Oversaw the planning and cost estimation of 50 projects over 2 years, organizing activities to remain on time and collaborating with 18 coworkers to deliver projects 100% with agreed criteria ● Led 30 quality assurance checks monthly, optimizing workflow processes and reducing waste by 32% ● Trained 8 new employees on material handling and production line expectations, onboarding staff efficiently to reduce missed shipments by 20% in 4 months
-
-
-
United States Navy
-
Norfolk, VA
-
Avionics Technician/Navy Security Forces
-
Jun 2008 - Jun 2012
● Deployed in support of Operation Iraqi Freedom and Operation Enduring Freedom ● Performed quality inspections and executed preventive maintenance on all aircraft electronics at the intermediate level for ensuring safe operating of aircraft ● Trained and developed 6 new Sailors and Marines to boost staff skills for performing allocated job roles ● Deployed in support of Operation Iraqi Freedom and Operation Enduring Freedom ● Performed quality inspections and executed preventive maintenance on all aircraft electronics at the intermediate level for ensuring safe operating of aircraft ● Trained and developed 6 new Sailors and Marines to boost staff skills for performing allocated job roles
-
-
Education
-
Cleary University
Bachelors Degree, Business Administration, Management and Operations
Community
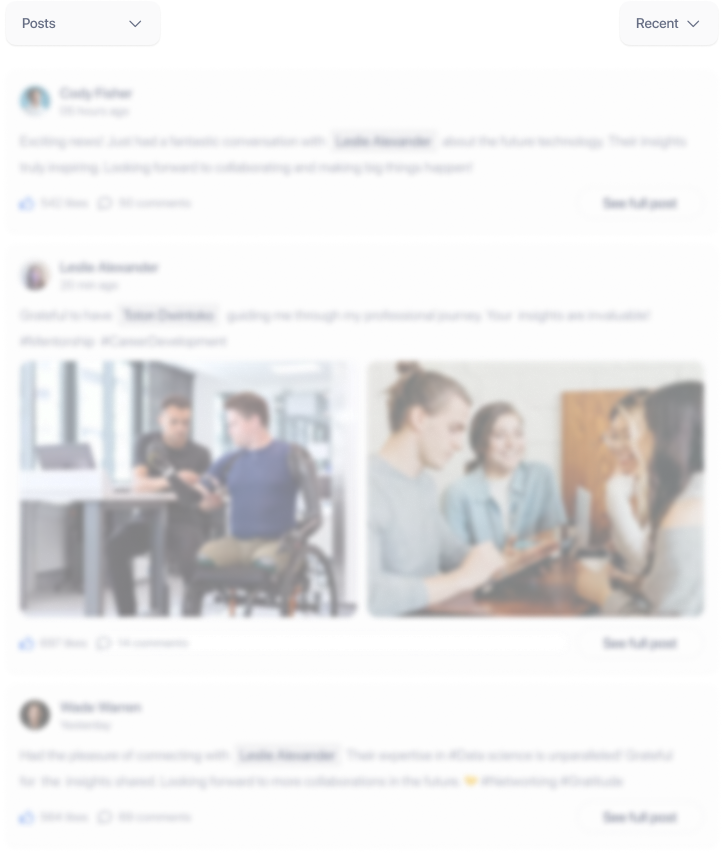