
Jeff Post
Senior Maintenance Supervisor at Country Maid, Inc- Claim this Profile
Click to upgrade to our gold package
for the full feature experience.
Topline Score
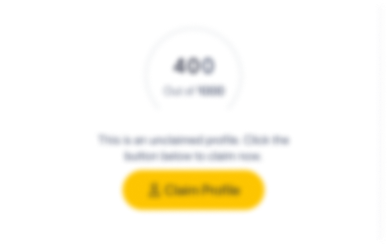
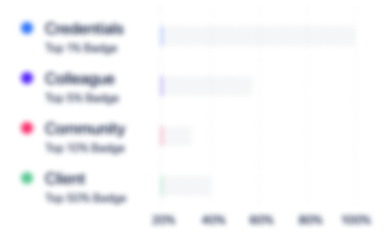
Bio
0
/5.0 / Based on 0 ratingsFilter reviews by:
Experience
-
Country Maid, Inc
-
United States
-
Food and Beverage Manufacturing
-
1 - 100 Employee
-
Senior Maintenance Supervisor
-
Jul 2022 - Present
Responsible for Maintenance Technicians providing upkeep on all Plant equipment. Responsible for Maintenance Technicians providing upkeep on all Plant equipment.
-
-
-
Liguria Foods
-
United States
-
Food and Beverage Manufacturing
-
1 - 100 Employee
-
Maintenance Manager
-
Dec 2021 - Apr 2022
Worked as the Plant Maintenance Supervisor at Liguria Foods since January 2020. Transitioned to the Facility's Maintenance Manager position when it became available in December of 2021.-Developed and instituted a Rust Survey Program, Light Survey Program, and Floor Survey Program to improve overall Good Manufacturing Practices (GMP) and decrease the possibility of negative findings during annual Safe Quality Foods (SQF) Inspections. These programs enable CTI Foods, Humboldt, IA to maintain a proactive approach within these areas instead of being in “Reactive” mode.-Researched and implemented a circuit card repair system with a Global repair company. This initiative reduced cost by over 50% by having expensive circuit cards repaired instead of purchasing them new from the Original Equipment Manufacturers (OEM’s).-Purchased and installed two new Ingersol-Rand 100HP air compressors. These new compressors replaced our old, outdated, Atlas-Copco compressors, reducing plant downtime and overall condensation distribution throughout the facility.-Initiated a Vibration Analysis Program for the Company’s Ammonia Compressors and other large stationary equipment. This will result in identifying anomalies and problem areas within equipment well before it gets to a serious nature.-Initiated switching companies for forklifts, motorized pallet jacks, and stand-up riding lifts leases. This enabled CTI Foods to recoup a 30% savings in leasing lifting equipment.-Initiated a Maintenance, Repair, and Operations (MRO) project to eliminate parts that were no longer needed and also obtain the correct parts, and quantities, for existing equipment resulting in decreasing downtime and reducing the Storeroom total cost by 30%.
-
-
Maintenance Supervisor
-
Jan 2020 - Dec 2021
-
-
-
Conagra Brands
-
United States
-
Food and Beverage Services
-
700 & Above Employee
-
Maintenance Supervisor
-
Jul 2017 - Dec 2021
Manage the day to day activities of 6 Mechanics, 4 Electricians, and 6 Boiler/Refrigeration Operators to ensure all equipment is available for production.Plant Process Safety Management Coordinator Manage the day to day activities of 6 Mechanics, 4 Electricians, and 6 Boiler/Refrigeration Operators to ensure all equipment is available for production.Plant Process Safety Management Coordinator
-
-
-
-
Shop Manager
-
Jan 2014 - May 2017
Manage the day to day activities of ten fabricators, five assemblers, two painters, one plasma table operator, 2 machinists, and one Production Foreman in the fabrication of conveyors, washers, dryers, grading tables, etc. for use in agricultural companies over the 48 contingent states as well as internationally. He manages these systems from conception to completion ensuring high quality standards are met in conjunction with maintaining stringent timelines. Provide daily equipment and systems updates to the General Manager relating to shop operations and production.Maintain a mishap free workplace and abided by all Federal, State, and OSHA regulations pertaining to facility maintenance and operations.Consistently applying waste reduction and process efficiency techniques to minimize waste in the fabrication of equipment and increase efficiency for the company.Troubleshoot and repair the company’s electrical systems as well as maintaining fabrication equipment to include; machinist’s equipment (lathe, mill, drill press, grinders, etc.), electro-mechanical and electronic systems.
-
-
-
-
Maintenance Manager
-
Jun 2012 - Nov 2013
Manage 16 mechanics/electronic technicians in maintaining production equipment, facilities, automation, in support of operations.Additional supporting roles include: Process Improvement, 5S, Program Management, Production Efficiency, new installations support, Engineering support, operational budgeting. Manage 16 mechanics/electronic technicians in maintaining production equipment, facilities, automation, in support of operations.Additional supporting roles include: Process Improvement, 5S, Program Management, Production Efficiency, new installations support, Engineering support, operational budgeting.
-
-
-
-
Maintenance Supervisor
-
Oct 2010 - Jun 2012
Maintaine production equipment and associated electrical systems and automation for the facility for ten (10) production lines. Maintaine production equipment and associated electrical systems and automation for the facility for ten (10) production lines.
-
-
-
J.R. Simplot
-
Food and Beverage Manufacturing
-
700 & Above Employee
-
Electrical Maintenance Supervisor
-
Jul 2008 - Aug 2010
Managed the day today activities of 13 electricians in the operation and maintenance of industrial production equipment, automated processing systems, electrical distribution systems, switchgear, facility lighting, etc.Provided daily equipment and systems updates to the Maintenance Manager relating to plant operations and production.Provided regular training to 13 electricians as part of professional development.Maintained a mishap free workplace and abided by all Federal, State, and OSHA regulations pertaining to facility maintenance and operations.Maintained an annual budget in excess of $1.4 Million.Managed Preventive and Corrective Maintenance through work orders to include man-hours expended, parts, etc.
-
-
-
United States Navy
-
United States
-
Armed Forces
-
1 - 100 Employee
-
Consolidated Maintenance Officer
-
Jul 2005 - Jul 2008
Directed five (5) Supervisors in managing 135 personnel in performing day to day preventive and corrective on Satellite Communications systems, Radar systems, facilities, access control systems, telephone systems, video surveillance systems, etc.Provided meticulous oversight on a $1.7 Million High Frequency (HF) antenna installation project, resulting in greater HF coverage within the Western Pacific Ocean Region.Key individual in negotiating multi-million dollar facility issues, maintenance issues, equipment installations, and treaty modifications for the Australian based Radio Transmitting Facility. Consistent participation was vital in maintaining a reliable US/Australian partnership in the utilization of this joint asset.Continuous dialogue with Hawaiian Electric Company resulted in the installation of the Commercial and Industrial Load Control Program (CIDLC) at two major Naval Facilities on O'ahu.. Implementation of this program saved the Navy an average of $46 thousand per month in energy consumption costs.Successful with the installation of new power generation equipment for the O'ahu Naval Communications Station Operations building. The new power generation equipment replaced older, antiquated systems and resulted in the Operations Building being "self sustainable" in the event of commercial power casualties.Served as Chairman, Technical Evaluation Board in the Source Selection Process to award an Operation and Maintenance (; Meticulous research resulted in a final contract award with an annual savings of $2.8 million as compared to the previous contract.
-
-
-
USS Abraham Lincoln
-
United States
-
Mining
-
1 - 100 Employee
-
Combat Systems Information Officer
-
Jul 2003 - Jul 2005
Responsible for maintaining the classified and unclassified networks for the ship and battle group. Responsible for maintaining the classified and unclassified networks for the ship and battle group.
-
-
-
-
Officer in Charge
-
Nov 2000 - Jul 2003
Managed 2 Division Officers in maintaining cryptographic keys and equipment, communications, and ICE systems for Commander, Patrol and Reconnaissance Wing Ten.Maintained an annual budget in excess of $1.2MM for repair parts, training, and operating supplies.Total Detachment was comprised of Managed 2 Division Officers in maintaining cryptographic keys and equipment, communications, and ICE systems for Commander, Patrol and Reconnaissance Wing Ten.Maintained an annual budget in excess of $1.2MM for repair parts, training, and operating supplies.Total Detachment was comprised of
-
-
Education
-
Villanova University
Certified in Government and Commercial Contract Management, Conttract management -
Juran Institute
Six Sigma Green Belt for Process Improvement, Six Sigma Master Black Belt -
Excelsior University
AAS, Liberal Arts -
Villanova University
Certification Lean Six Sigma Black Belt, Proccess improvement and Waste Reduction
Community
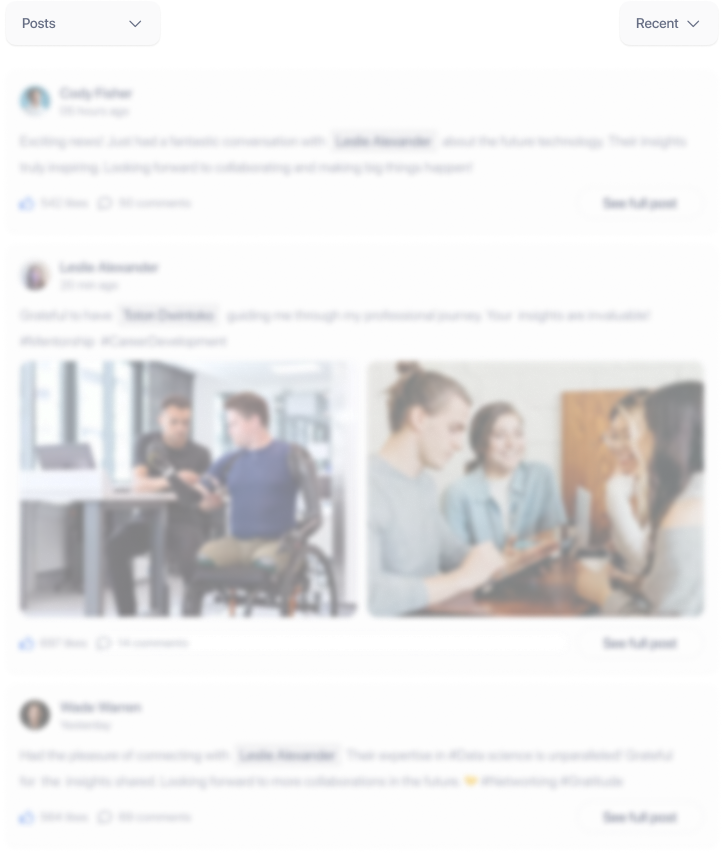