Jeff Bennett
President at Dymicron- Claim this Profile
Click to upgrade to our gold package
for the full feature experience.
Topline Score
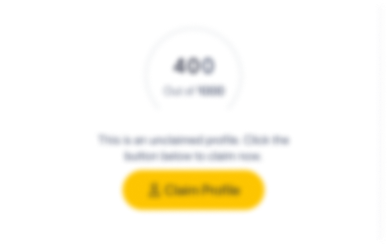
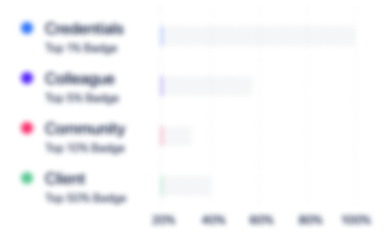
Bio

Skyler Martinson
It’s rare that you come across a leader like Jeff. Over the past two-plus years, I have had the pleasure of working with Jeff at Dymicron. I have been particularly impressed by Jeff’s ability to lead the company through very difficult challenges. He gives his employees opportunity and space to work on projects and trusts his employees to perform well. He is also a very approachable boss and has shared with me some of his excellent wisdom. Any company would be fortunate to have Jeff as its leader.

Skyler Martinson
It’s rare that you come across a leader like Jeff. Over the past two-plus years, I have had the pleasure of working with Jeff at Dymicron. I have been particularly impressed by Jeff’s ability to lead the company through very difficult challenges. He gives his employees opportunity and space to work on projects and trusts his employees to perform well. He is also a very approachable boss and has shared with me some of his excellent wisdom. Any company would be fortunate to have Jeff as its leader.

Skyler Martinson
It’s rare that you come across a leader like Jeff. Over the past two-plus years, I have had the pleasure of working with Jeff at Dymicron. I have been particularly impressed by Jeff’s ability to lead the company through very difficult challenges. He gives his employees opportunity and space to work on projects and trusts his employees to perform well. He is also a very approachable boss and has shared with me some of his excellent wisdom. Any company would be fortunate to have Jeff as its leader.

Skyler Martinson
It’s rare that you come across a leader like Jeff. Over the past two-plus years, I have had the pleasure of working with Jeff at Dymicron. I have been particularly impressed by Jeff’s ability to lead the company through very difficult challenges. He gives his employees opportunity and space to work on projects and trusts his employees to perform well. He is also a very approachable boss and has shared with me some of his excellent wisdom. Any company would be fortunate to have Jeff as its leader.

Experience
-
Dymicron
-
United States
-
Medical Equipment Manufacturing
-
1 - 100 Employee
-
President
-
2010 - Present
Responsible for corporate strategy focused on the application of advanced diamond materials to orthopedic implants. Direct business activities and provide team leadership to implement this strategy producing return for investors, opportunities for employees, and improved medical devices for patients. Currently commercializing Dymicron's first product, the Triadyme-c, a cervical spine total disc replacement. See Dymicron.com. Coordinate and participate in fund raising with members of the Board of Directors. Show less
-
-
-
Merit Medical
-
Hong Kong
-
Medical Device
-
1 - 100 Employee
-
General Manager, Richmond Division
-
2006 - 2009
Operational responsibility for all aspects of Merit's Convenience Kit Division including quotes, purchasing, production planning, manufacturing, warehousing, QA, HR, finance, and facilities.Mentored and developed team that led division from loss to profitability.Managed 40% growth in one year with no significant backorders or increases in quality issues.Dispersed responsibility for quality system from QA to all departments, developing a more cooperative and quality conscious organization.Organized initial Kaizan event beginning implementation of an active pursuit of Lean manufacturing. Show less
-
-
Director, Quality Assurance
-
2005 - 2006
Led manufacturing quality team consisting of 10 engineers and technicians and 40 quality inspectors and supervisors;Coordinated ISO 13485:2003 certification for entire corporation; and Streamlined quality processes using quality data to identify problems and direct improvement efforts.
-
-
-
Dimicron
-
Brazil
-
Farming
-
1 - 100 Employee
-
Director, Quality Assurance and Regulatory Affairs / Corporate Secretary
-
Apr 2004 - Apr 2005
Reporting to the President accomplishing: Initial development of FDA compliant Quality System and Regulatory Approval Strategy for first Total Hip Replacement with Polycrystalline Diamond bearing surfaces. Significant contribution in the negotiation of a $10M support and distribution agreement with a prominent orthopedic device firm. Collected and organized corporate documentation (as Corporate Secretary) improving company operation. Participated in development and initial execution of a preferred stock offering to begin funding other diamond based medical devices. Show less
-
-
-
MedQuest Products
-
United States
-
Medical Device
-
Quality Assurance and Regulatory Affairs Manager
-
Aug 2003 - Apr 2004
Reporting to the CEO with accomplishments including: Creation and implementation of an effective and compliant Design Control System to guide development efforts for the Heart Quest Left Ventricular Assist Device. Development of a regulatory strategy for initial EU and PMA approval. Construction of a Quality system starting with a Quality Manual and including key procedures. Reporting to the CEO with accomplishments including: Creation and implementation of an effective and compliant Design Control System to guide development efforts for the Heart Quest Left Ventricular Assist Device. Development of a regulatory strategy for initial EU and PMA approval. Construction of a Quality system starting with a Quality Manual and including key procedures.
-
-
-
-
Quality Technical Team Manager
-
Jan 2001 - Jul 2003
Staff comprised of 16 people, 7 professionals (BS or MS in Science or Engineering) and 9 Technicians divided into Quality Engineering, and Quality Laboratory Teams. Specific accomplishments included: Successful management of an FDA audit that was follow-up to a warning letter resulting in the firm being placed back on normal inspection status. Directed Quality Engineering Team providing QA input to Design Control, implementing SPC with real time feed back and correction, deciding what issues need formal CAPA treatment, and approving Process Validation protocols and reports. Led Quality Laboratory Team in implementing in-house microbiology testing to realize annual cost savings over $400,000. Instrumental in Ballard's successful certification to ISO 13485. Show less
-
-
-
Ballard Medical Products
-
United States
-
Appliances, Electrical, and Electronics Manufacturing
-
Operations Manager
-
Jan 1998 - Jan 2001
Successfully coordinated the transition of TriMed Specialties, a $28,000,000 acquisition. Managed and consolidated operations originally in Australia, Virginia, and Kansas. Approved by the State of Utah and served as Ballard's Radiation Safety Officer for radiopharmaceutical diagnostics manufacturing.Directed successful FDA pre-approval inspection. Reorganized diagnostic manufacturing department to achieve a 30% efficiency improvement. Drove down customer complaints 50% in two years with thorough investigations and effective corrective actions. Show less
-
-
Project Manager
-
Jan 1994 - Jan 1998
Responsible for independent management of quality, manufacturing, and business development projects. Leading participant on three transition teams responsible for relocating operations to Ballard's manufacturing facilities. Key member of ISO Certification Team that executed a complete Quality System redesign for initial ISO compliance.Implemented cost savings projects one of which realized $300,000 annualized savings.
-
-
-
Becton Dickinson
-
Hospitals and Health Care
-
1 - 100 Employee
-
Research Associate
-
Jan 1988 - Jan 1994
Formulated or assisted with the formulation of eight antimicrobial surgical scrub and prep solutions and a variety of antimicrobial coatings for medical devices or surgical skin preparation. Three of the surgical scrub solutions yielded sales of approximately five million units annually. Participated in the development of an analytical method for para-chloroanaline (PCA) that was later adopted as the official method by the US Pharmacopoeia. Formulated or assisted with the formulation of eight antimicrobial surgical scrub and prep solutions and a variety of antimicrobial coatings for medical devices or surgical skin preparation. Three of the surgical scrub solutions yielded sales of approximately five million units annually. Participated in the development of an analytical method for para-chloroanaline (PCA) that was later adopted as the official method by the US Pharmacopoeia.
-
-
Education
-
University of Utah
Graduate Work, Public Health -
University of Utah
BS, Chemistry
Community
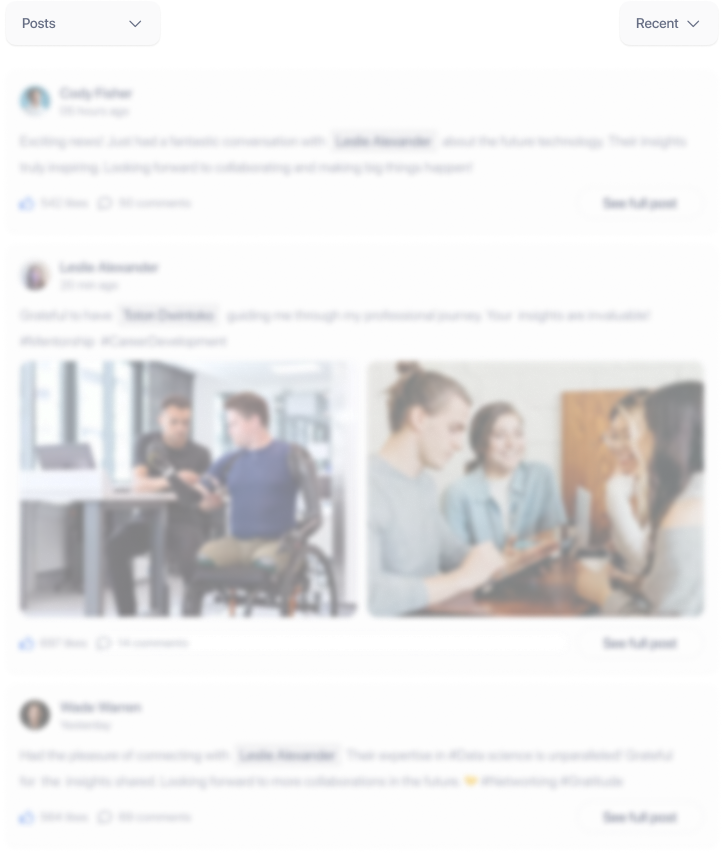