Jeanne Bisenius
Epicor Business Analyst at Jones Plastic and Engineering- Claim this Profile
Click to upgrade to our gold package
for the full feature experience.
Topline Score
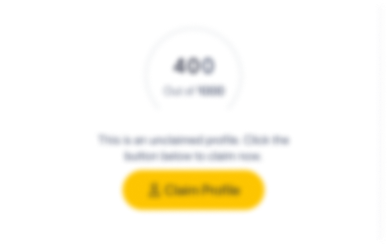
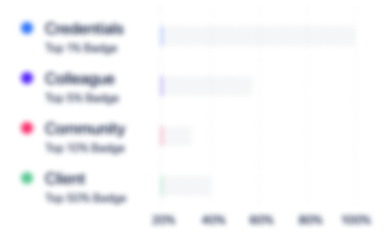
Bio

Nikki Gordon
To whom it may concern, My name is Nicole. I worked with Jeanne Hartmann at MPI Research. I have known Jeanne for 6 years. When I first started in Accounts Payable Jeanne took the time to help me understand what was expected of me. When I had an issues that I could not resolve she would take me step by step to make sure I understood what I was looking for. She knew Shipping and Receiving, Purchasing and Accounts Payable side making it easy for her to track do problems and make suggestion on improving the whole process. Jeanne is a very positive and energetic person. I am pleased to recommend Jeanne Hartmann for employment. She would be an asset to any company. She brings with her the knowledge of managing employees, helping co-workers get along in difficult situations. She was a good mentor to me while she was at MPI. Sincerely, Nicole Gordon

Kelly Parkhill
Jeanne and I worked on an ERP implementation. She was primarily responsible for inventory,purchasing, payables and receivables. Jeanne's experience was a significant factor in MPI meeting our implementation deliverables and quality goals. She is very knowledgable and is an excellent teacher! I would highly recommend Jeanne - an organization would be fortunate to have her on their team!

Nikki Gordon
To whom it may concern, My name is Nicole. I worked with Jeanne Hartmann at MPI Research. I have known Jeanne for 6 years. When I first started in Accounts Payable Jeanne took the time to help me understand what was expected of me. When I had an issues that I could not resolve she would take me step by step to make sure I understood what I was looking for. She knew Shipping and Receiving, Purchasing and Accounts Payable side making it easy for her to track do problems and make suggestion on improving the whole process. Jeanne is a very positive and energetic person. I am pleased to recommend Jeanne Hartmann for employment. She would be an asset to any company. She brings with her the knowledge of managing employees, helping co-workers get along in difficult situations. She was a good mentor to me while she was at MPI. Sincerely, Nicole Gordon

Kelly Parkhill
Jeanne and I worked on an ERP implementation. She was primarily responsible for inventory,purchasing, payables and receivables. Jeanne's experience was a significant factor in MPI meeting our implementation deliverables and quality goals. She is very knowledgable and is an excellent teacher! I would highly recommend Jeanne - an organization would be fortunate to have her on their team!

Nikki Gordon
To whom it may concern, My name is Nicole. I worked with Jeanne Hartmann at MPI Research. I have known Jeanne for 6 years. When I first started in Accounts Payable Jeanne took the time to help me understand what was expected of me. When I had an issues that I could not resolve she would take me step by step to make sure I understood what I was looking for. She knew Shipping and Receiving, Purchasing and Accounts Payable side making it easy for her to track do problems and make suggestion on improving the whole process. Jeanne is a very positive and energetic person. I am pleased to recommend Jeanne Hartmann for employment. She would be an asset to any company. She brings with her the knowledge of managing employees, helping co-workers get along in difficult situations. She was a good mentor to me while she was at MPI. Sincerely, Nicole Gordon

Kelly Parkhill
Jeanne and I worked on an ERP implementation. She was primarily responsible for inventory,purchasing, payables and receivables. Jeanne's experience was a significant factor in MPI meeting our implementation deliverables and quality goals. She is very knowledgable and is an excellent teacher! I would highly recommend Jeanne - an organization would be fortunate to have her on their team!

Nikki Gordon
To whom it may concern, My name is Nicole. I worked with Jeanne Hartmann at MPI Research. I have known Jeanne for 6 years. When I first started in Accounts Payable Jeanne took the time to help me understand what was expected of me. When I had an issues that I could not resolve she would take me step by step to make sure I understood what I was looking for. She knew Shipping and Receiving, Purchasing and Accounts Payable side making it easy for her to track do problems and make suggestion on improving the whole process. Jeanne is a very positive and energetic person. I am pleased to recommend Jeanne Hartmann for employment. She would be an asset to any company. She brings with her the knowledge of managing employees, helping co-workers get along in difficult situations. She was a good mentor to me while she was at MPI. Sincerely, Nicole Gordon

Kelly Parkhill
Jeanne and I worked on an ERP implementation. She was primarily responsible for inventory,purchasing, payables and receivables. Jeanne's experience was a significant factor in MPI meeting our implementation deliverables and quality goals. She is very knowledgable and is an excellent teacher! I would highly recommend Jeanne - an organization would be fortunate to have her on their team!

Experience
-
Jones Plastic and Engineering
-
United States
-
Plastics Manufacturing
-
200 - 300 Employee
-
Epicor Business Analyst
-
Feb 2019 - Present
Onsite SME Training, Documentation, Process Improvements , User Dashboard development, Implementation Support to all USA and Mexico companies under the Jones ownership Onsite SME Training, Documentation, Process Improvements , User Dashboard development, Implementation Support to all USA and Mexico companies under the Jones ownership
-
-
-
Brown Jordan
-
United States
-
Furniture and Home Furnishings Manufacturing
-
100 - 200 Employee
-
Epicor Business Analyst
-
Sep 2014 - Nov 2017
On site SME supporting multiple locations with Epicor 9,10 in U.S. and Mexico Training and providing ongoing process improvement using Epicor Proficient in BAQ and Dashboard design Project management On site SME supporting multiple locations with Epicor 9,10 in U.S. and Mexico Training and providing ongoing process improvement using Epicor Proficient in BAQ and Dashboard design Project management
-
-
-
TydenBrooks
-
United States
-
Transportation, Logistics, Supply Chain and Storage
-
100 - 200 Employee
-
E9 Implementation Lead Manager
-
Sep 2012 - Sep 2014
Project Lead for all Plant E9 Implementation and continous improvement in the software utilization. Supported U.S. and Mexico locations Well rounded in all the Epicor Modules, Finance, Manufacturing, Engineering, Materials and Sales. Supporting four manufacturing facilities in the use of Epicor in the day to day operations. I am the resident SME for the software. Project Lead for all Plant E9 Implementation and continous improvement in the software utilization. Supported U.S. and Mexico locations Well rounded in all the Epicor Modules, Finance, Manufacturing, Engineering, Materials and Sales. Supporting four manufacturing facilities in the use of Epicor in the day to day operations. I am the resident SME for the software.
-
-
-
TydenBrooks
-
Angola, IN
-
Demand Manager
-
Jul 2011 - Dec 2012
Responsible for all product flow between China , Mexico and U.S. operations Managed staff buyers/planners Responsible for all product flow between China , Mexico and U.S. operations Managed staff buyers/planners
-
-
-
-
Business Analyst
-
Oct 2010 - May 2011
Contract position completed with Alcoa in Mary 2011 Provided coverage for Pricing Business Cases,Oracle Items Masters Templetes, BOM Templetes and Routing Templates. Maintaned Standard Cost Data Base Contract position completed with Alcoa in Mary 2011 Provided coverage for Pricing Business Cases,Oracle Items Masters Templetes, BOM Templetes and Routing Templates. Maintaned Standard Cost Data Base
-
-
-
-
Business Anaylst, Contract
-
Jan 2009 - Nov 2009
I have currentlycompleted my contract with Pfizer, Kalamazoo, Michigan working on the implementation of Galaxie and LimsLink to SQL Lims. I am support for the CDS project thru to completion. Modifing SOP's, etc. Testing and Validating system requirements. I have currentlycompleted my contract with Pfizer, Kalamazoo, Michigan working on the implementation of Galaxie and LimsLink to SQL Lims. I am support for the CDS project thru to completion. Modifing SOP's, etc. Testing and Validating system requirements.
-
-
-
-
Business Analyst
-
Jan 2009 - Nov 2009
-
-
-
MPI Research
-
United States
-
Research Services
-
300 - 400 Employee
-
Business Anaylst
-
Aug 2003 - Dec 2008
MPI Research Inc. Mattawan, MI Aug. 2003 – Dec. 2008 Business Analyst/Process Manager •Project Manager for the implementation of Deltek Costpoint system, converting from Great Plains Dynamics. •Provided continuous improvement support and filled the role of SME for Costpoint. •Implemented Cognos IWR web reporting, and Cognos Planner Revenue Model. •Provided support in the improvement and automation of the MPI Internal Study Pricing model. •Made recommendations for improved processes for Finance, Purchasing, and Operations in how to use the system effectively. One extremely timesaving module was procurement, which allowed us to go paperless for requisitioning outside purchases. •Provided employee training and development on all business modules. Investigating bringing SAP in house as Core Business and LIMS Enterprise system. •Business Partner to the MPI Discovery Center. •Project Lead for Saleforce.com hosted CRM solution implemented at MPI.
-
-
-
-
Materials/Implementation Manager
-
Nov 2001 - Feb 2003
Accepted a contract position to complete the implementation of the M2M ERP system for a Tier One Automotive Supplier. Duties consisted of the design of the system, integration to Auto Cad, writing procedures and training of all company personnel. Additionally was assigned the responsibilities of the Materials Department Manager, supervising all buyers, shipping and receiving, inventory control, production control and process job costing staff. Accepted a contract position to complete the implementation of the M2M ERP system for a Tier One Automotive Supplier. Duties consisted of the design of the system, integration to Auto Cad, writing procedures and training of all company personnel. Additionally was assigned the responsibilities of the Materials Department Manager, supervising all buyers, shipping and receiving, inventory control, production control and process job costing staff.
-
-
-
-
Implementation Project Account Manager
-
Feb 1999 - Nov 2001
Provided Project Management Services for a Made2Manage Reseller in Michigan. Responsible for project management and implementation consulting services to assist business in installing, setup, instruction and training in the use of the M2M ERP System. This included A/P, A/R, Inventory, Purchasing and Manufacturing Orders. Provided both classroom and onsite training of all modules. Provided leadership for the quarterly M2M West Michigan User Group. Throughout the process I lead a number of companies in Michigan and Indiana to excellence in the utilization of the ERP system with an average turnaround time of six months to a go live status. This was done by bringing 20 years experience of Finance and Manufacturing background to the table to help companies develop and streamline their operations.
-
-
-
-
Operations Manager
-
Jul 1997 - Feb 1999
Responsible for the re-implementation of the M2M ERP System, from customer quoting through product shipment. Ensured full integration to the Financials. Developed a Standard job cost system. Implemented internal structure and systems to provide for managed growth for both the Spring and Machine components of the company. Facilitated the weekly production meeting and provide a weekly Master Production Schedule for both shops to insure on time deliveries. Developed and facilitated a management team. Provided guidance and established policies and training for employees at all levels. Attained QS9000 certification. Provided a system of management reporting, to assist the owner in sound business decisions to ensure future growth and profitability. Managed a department of 30 employees consisting of, a Senior Buyer, Production Control Planners, Network Administrator, Shipping and Receiving and a number of secondary manufacturing associates. Highlight of this period- Established a management team of five and began to actively mentor to the team to participate jointly in the running of the company. Set hiring policies and new wage scale. Secured a Michigan Training Grant. Selected by Made2Manage National Advisory Board, to serve a two year term to assist in future direction of the development of the M2M ERP System. Accepted a position with CDI West's steering committee to assist in helping other West Michigan companies achieve excellence in implementing M2M. A quest speaker at the 1998 M2M User Conference for the implementation and troubleshooting of job cost systems.
-
-
-
-
Manager of Support Systems
-
Feb 1994 - Jul 1997
Developed employees by providing support and training through example and positive encouragement for facilitating growth. Maintenance and continuous improvement of the on line standard cost systems. Support to engineering staff in the calculations of cost and ROI justifications. Performed Audits of the ROI after implementation of the projects. Provided profitability analysis on all current and upcoming product lines. Provided guidance and insured proper management of the Specials Product Line. Automated all system processes as necessary to reduce lead-times in both pre-production and production. Led the department in insuring the accuracy if the Bills of Materials and Routing databases to Class A MRP Standards. Maintained all required ISO9000 documentation and training of the department. Facilitated the weekly ECN meetings.Managed a department of nine that consisted of one Process Engineer, five Process Technicians, one Project Management Coordinator, Specials Coordinator and an Internal Auditor.Highlights - Was a Change Facilitator for the Gordon Graham Program "Change is and Inside Job". Assisted in the implementation of a Flextime policy for all office personnel. Team Fascinator responsible for the automation of the Specials manual quoting process to a paperless system utilizing Lotus Notes and Key File PC Programs interfaced to the QMRP business System. Assisted in the design and implementation of colorless and flatter Bills of Materials for production. Began the implementation of an ABC costing system. Member of the Strategic Planning Committee and Business Systems selection Team.
-
-
Cost Accounting Manager
-
Oct 1989 - Feb 1994
Developed and maintain a standard cost system. Prepared monthly cost of goods sold and related journal entries and account analysis. Responsible for quoting all specials product lines. Made recommendations to Marketing and D&D as to what products should be converted to standards based on volumes. Member of Bill of Material Review Board responsible for making recommendations of improvements to the structuring of product bills of materials and routings to insure compatibility within the company systems. Assisted in the implementation of QRMP business system and reaching a class A status certification from the Olli Wright organization. Responsible for all physical inventories and cycle count programs.
-
-
-
-
Cost Accounting Supervisor
-
Oct 1985 - Jan 1989
-
-
-
-
Owner, Manager
-
Mar 1985 - Nov 1987
-
-
-
-
Cost Accountant
-
Jul 1983 - Oct 1984
-
-
-
Thermatool
-
United States
-
Industrial Machinery Manufacturing
-
1 - 100 Employee
-
Accounts Payable Supervisor
-
Aug 1982 - Jul 1983
-
-
-
-
Cost Accountant
-
Jan 1976 - Jan 1978
-
-
Education
-
Davenport University
General Business and Accounting -
Butler Business School
Associate in Accounting and Business -
Danbury High School
Community
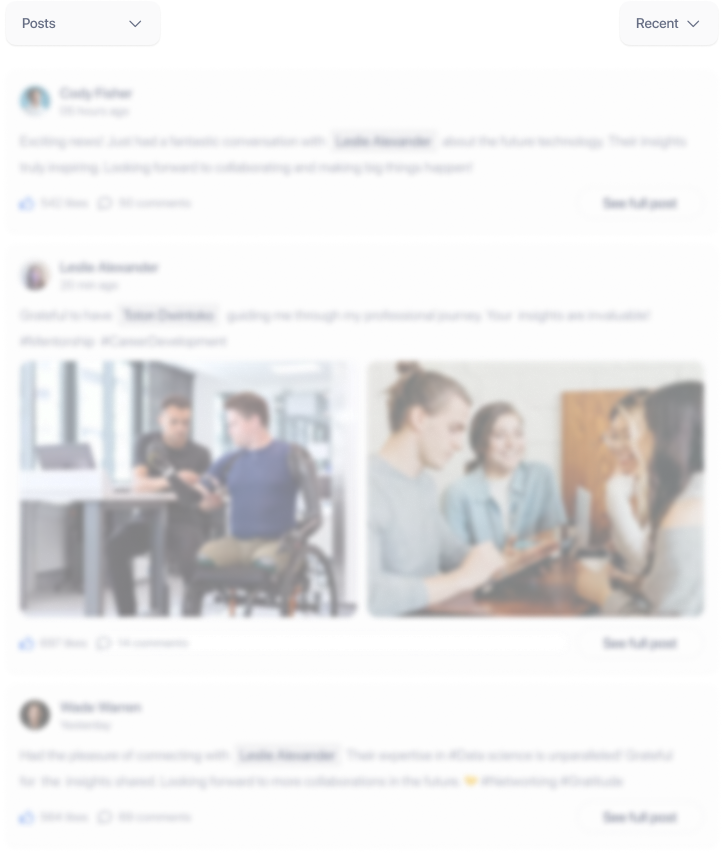