Jean Rivera
Sr Supply Chain Quality Engineer at Raytheon Technologies- Claim this Profile
Click to upgrade to our gold package
for the full feature experience.
Topline Score
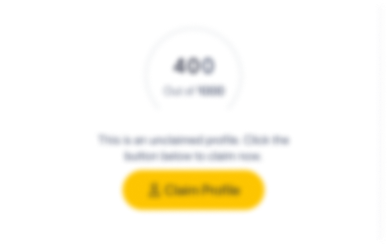
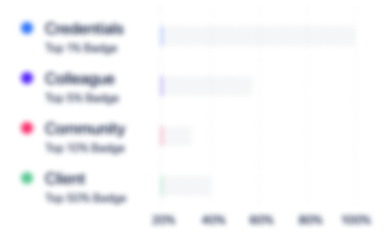
Bio


Credentials
-
Green Belt
- -
Lean Six Sigma Black Belt (ICBB)
ICBB
Experience
-
Raytheon Technologies
-
United States
-
Aviation and Aerospace Component Manufacturing
-
700 & Above Employee
-
Sr Supply Chain Quality Engineer
-
Oct 2020 - Present
-
-
-
L3Harris Technologies
-
United States
-
Defense and Space Manufacturing
-
700 & Above Employee
-
Supplier Quality Engineer
-
Dec 2014 - Present
o Developed deep supplier relationships with strategic suppliers and actively managed supply base to achieve a quality score above 98% goal for assigned focus teams to ensure company expectations are met as Supplier Quality commodity lead for Complex Electronics Critical Suppliers (CECS) and Distributors. o Conducted strategic sourcing activities assessing Quality Management System (QMS), special processes, facilities, capacity and technical capabilities for potential and current suppliers to provide feedback to programs to minimize risk and ensure adequate supply sources. o Implemented strategic quality initiatives for assigned commodities to attained nonconformance per inspectable receipt rate of 1.9%, exceeding 6.5% goal for a 12-month period. o Proven track record of building credible, reliable, customer focused sources of supply across multiple regions and multiple business units. o Served as single point of contact between suppliers and programs, partnering with procurement, engineering, supply chain, manufacturing and other functions to drive functional engagement and continuous improvement. o Prepared and presented plans, reports and presentations to senior supplier quality and supply chain managers, and other team members during Corrective Action Board (CAB) meetings. o Monitored and analyzed supplier performance metrics, identified areas of opportunity, communicated supplier risks, and drove the resolution of supplier quality issues and risk control processes. o Gathered market intelligence and trends for the commodity to bring innovation to the business, to continued robustness and evolution of strategy. o Provided supplier training for quality and lean methodologies/tools to drive high capability processes at high capacity and support strategic supplier partnerships. Show less
-
-
-
Lockheed Martin
-
United States
-
Defense and Space Manufacturing
-
700 & Above Employee
-
Operations Engineer
-
Sep 2012 - Dec 2014
o Led multi-disciplined team toward continuous improvement goals and cost improvement initiatives to save $2 million exceeding original goal of $850K for a 2 years period. o Managed and approved purchase of tools and equipment for program manufacturing areas exceeding $35k for a 2 years period. o Established accident prevention measures and mistake proofing techniques to achieve 0 lost workday cases in 3 years for assigned areas. o Assisted manufacturing engineers and production supervisor in the planning, design, modification and layout of facilities and equipment to successfully duplicate production rate. o Designed new layout for a 1.75 M capital investment optimizing space and available resources. o Established standard times for a new contract by analyzing historical data, providing guidance to manufacturing for scheduling, maximum utilization of production facilities and personnel, achieving 100% on time delivery. o Led FMEA team to effectively determine the root cause of FOD quality issues and then implemented a dedicated packaging station that have eliminated internal escapes. o Led a Standardization Project for an anti-air missile system program (Terminal High Altitude Area Defense) to reduce operators walking time and ensure tool control saved over $55K. Show less
-
-
-
Bristol Myers Squibb
-
United States
-
Pharmaceutical Manufacturing
-
700 & Above Employee
-
Operational Excellence Engineer
-
Mar 2012 - Sep 2012
o Used the DMAIC methodology to study the line flow in a packaging line utilizing lean tools, SPC analysis and time studies to balance and establish effective standard times and increased productivity that resulted in the reduction of one shift. o Conducted time studies to increase process efficiency and obtained 55% reduction in “change over” and “back to back” time for a new product. o Familiarized staff and supervisors and trained operators concerning all phases of new methods and allocation of resources via meetings and job aids. Show less
-
-
-
Eagle Industries del Caribe, Inc.
-
Import & Export
-
1 - 100 Employee
-
Industrial Engineer-Capstone Project
-
Jan 2011 - Jun 2011
o Successfully optimized a manufacturing line by implantation of line balancing increasing production efficiency from 50% to 90%. This work allowed the company to meet their daily demand. o Designed and implemented a Kanban system to eliminate material shortages in the production line. o Successfully optimized a manufacturing line by implantation of line balancing increasing production efficiency from 50% to 90%. This work allowed the company to meet their daily demand. o Designed and implemented a Kanban system to eliminate material shortages in the production line.
-
-
Education
-
University of Puerto Rico-Mayaguez
B.S. Industrial Engineering,, B.S. Industrial Engineering,
Community
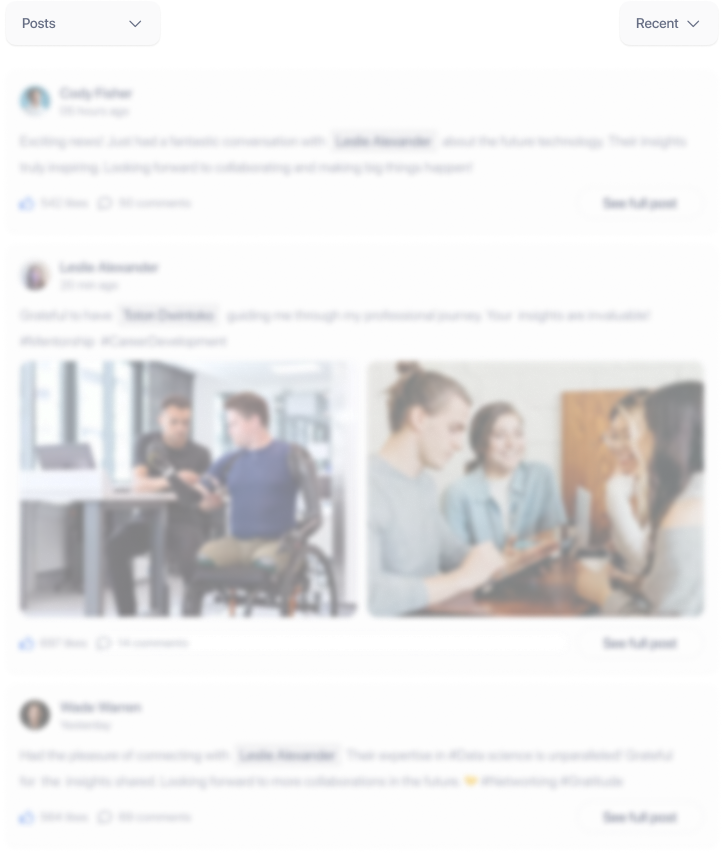