Jean Cormier
Director National Support Services at Com-Net Networks & Security- Claim this Profile
Click to upgrade to our gold package
for the full feature experience.
Topline Score
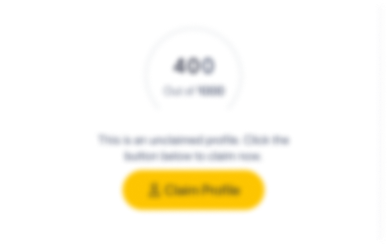
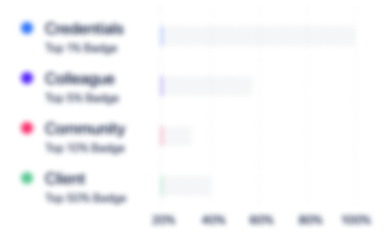
Bio

Daniel Bizier
Very good to work with and good leadership skills. Knowledgeable in plant operations.

Daniel Bizier
Very good to work with and good leadership skills. Knowledgeable in plant operations.

Daniel Bizier
Very good to work with and good leadership skills. Knowledgeable in plant operations.

Daniel Bizier
Very good to work with and good leadership skills. Knowledgeable in plant operations.

Experience
-
ComNet Networks and Security Inc.
-
Canada
-
Security and Investigations
-
1 - 100 Employee
-
Director National Support Services
-
Jun 2021 - Present
As Director National Support Services, I manage a team of Senior Project Managers as well as a team of Professional Engineering Services. This combination of expertise allows us to assess our national customers' needs, propose and implement custom integrated security systems solutions.
-
-
Director Of Operations
-
Jul 2021 - Dec 2021
As the Security Division OPS Director, I oversee the project management team, installation and service teams and contractual PM's, installers and servicemen across Canada. I am responsible for managing the division's P&L.
-
-
Senior Project Manager
-
Jun 2021 - Jul 2021
As Senior Project Manager, I manage 5 PM's from the security division as well as contractual PM's. We manage projects from coast to coast.
-
-
-
AIR LIQUIDE ADVANCED MATERIALS INC.
-
United States
-
1 - 100 Employee
-
Site Leader
-
Oct 2017 - Dec 2020
Overseeing electronic gases production activities of the New Jersey USA site. Responsible for the overall site safety and administration. Supporting cross-functional teams like, Process Development, R&D, QC/QA and Supply Chain teams. Responsible for 40 production technicians including Shift Leads (4), Supervisors (3) and Production Engineers (2). Responsible for the plant staffing strategy. Responsible to identify efficiency projects to improve production costs YOY. Responsible to identify, develop and train future managers. Responsible to prepare the facility capital requests projects. Show less
-
-
-
Somati
-
1 - 100 Employee
-
General Manager
-
Oct 2015 - Oct 2017
This subsidiary is owned by Air Liquide Morocco. I have been tasked in October 2015 to take over the General Management responsibilities left vacant by the retired General Manager. I was cumulating both the Somati General Management position and the Industrial Director of Air Liquide Morocco until my 3 year mandate elapsed. Overseeing all operational and commercial activities. Budget preparation and follow up. This facility manufactures welding rods. Responsible for 40 employees and all labor relations with the union representatives. Maintaining the appropriate level and quality of staff in order to support the sales and on-time delivery. Responsible to implement and follow up on the ISO certification. Export products to other African Air Liquide subsidiaries as well as direct customers. Responsible to identify efficiency projects to improve production costs YOY. Responsible to identify, develop and train a local candidate to take over this role. Show less
-
-
-
Air Liquide
-
France
-
Chemical Manufacturing
-
700 & Above Employee
-
Industrial Director
-
Aug 2014 - Oct 2017
Overseeing all technical and financial aspects of the following industrial operations: Two ASU’s (Air Separation units) producing each 70 tons / day One CO2 production plant producing 8,8 tons / day One acetylene production and filling plant One hydrogen filling plant One industrial air gas and CO2 filling plant One dry ice production facility One cylinder recertification facility One medical oxygen and nitrous oxide filling plant Customer installation and maintenance teamso Installation teamo Maintenance teamo Monthly efficiency reporting of each unit Customer On-sites units (small N2 (nitrogen) and H2 (hydrogen) production units) Bulk liquid distribution (N2, O2, CO2)o Asset purchase and maintenance strategyo Production strategy to fit sales needs.o Negotiate contract with carriers. Package gas distributiono Asset purchase and maintenance strategyo Negotiate contract with carriers. Responsible to hire and develop new managers and perform annual appraisals. 7 direct reports and 80+ industrial employees. o Responsible for all safety related aspects of the industrial operations. (Procedures, audits etc.) Meeting customers as needed and supporting commercial team. Member of the upper management committee for Air Liquide Morocco. Responsible for developing and implementing relevant KPI’s in order to monitor financial related operation activities and meet business financial plan/expectations. Responsible to launch yearly efficiency projects and support the production costs reduction initiative. Responsible to prepare CAPEX requests and ROI calculation for each project. Show less
-
-
Regional Distribution Manager
-
Feb 2012 - Aug 2014
Responsible for liquid bulk distribution activities for Quebec and Maritimes. Operating budget of 12 million dollars. More than 50 employees + brokers. ♣ Responsible to hire the best and safest drivers and brokers. ♣ Responsible to hire key personnel (supervisors and dispatchers) ♣ Responsible to follow up all relevant KPI’s (financial & operational) ♣ Responsible to implement and follow preventive maintenance programs. ♣ Responsible for the labor relation between union and Liquid Supply Center for Quebec. Responsible to negotiate a new collective agreement. Show less
-
-
Special Project Manager
-
Oct 2010 - Feb 2012
This position reported directly to the OPS VP.♣ implementing a cylinder tracking system throughout Canada for more than 800,000 cylinders. Project budget of 5 million dollars.♣ Travel to and build teams in each Canadian provinces (10) in order to locally launch the project ♣ Implement in each province a computer Wi-Fi network♣ Responsible for all purchasing aspects of the project ♣ Responsible for training all employees related to this project. ♣ Responsible to provide the technical and financial specifications of all interfaces to the IT team in order to adapt the ERP to this new software. Show less
-
-
Plant Operations Manager
-
Aug 2008 - Oct 2010
♣ Responsible for all filling activities for four (4) filling plants across Ontario ♣ Responsible for a cylinder recertification facility in Cornwall ♣ Overseeing technical and financial activities for the industrial filling activities ♣ Overseeing technical and financial activities of the specialty gas filling activities. (2nd largest in Canada) ♣ Responsible for all safety related programs for the industrial operations. ♣ Implement and follow up KPI’s to improve productivity and production capability using the Six Sigma methodology and other related tools. ♣ Responsible to interview, hire and train new supervisors. Perform yearly appraisals Show less
-
-
-
Praxair Canada Inc
-
Canada
-
Chemical Manufacturing
-
1 - 100 Employee
-
Operations Manager (Production & Distribution)
-
Jun 2007 - Oct 2008
♣ Responsible for the overall plant operations (production and distribution) with a $12 million dollar budget and 63 employees.♣ Improved on-time delivery for our specialty gases department ♣ Improved on-time delivery for our commercial gas department ♣ Improved attendance and absenteeism stats. ♣ Prepare & negotiate the CBA renewal. It has been renewed on time with no labor disruption nor work slowdowns. ♣ Six Sigma Green Belt certification.♣ Overseed a $10 million site improvement project. Show less
-
-
Plant Manager
-
Apr 2005 - Jun 2007
Responsibility: ♣ Responsible for the overall plant operations with a $6 million dollar budget and 32 employees. ♣ Sustained and/or improved our relationship with our Canadian and American customers. Renew the collective bargaining agreement. (CBA)♣ Six Sigma Green Belt Achievements: ♣ Build a partnership and confidence relationship between the management team and the employees. ♣ Build a strong relationship with our Canadian and American customers. ♣ Improvement of the production cost by 10% ♣ Implementation of an automated acetylene debit control to maximize usage of the acetylene received from our supplier. ♣ Implement a second production meeting to maximize our production. ♣ Renew the collective agreement for 4 years with no strike and no slowdown production and before the expiry date. Awards: ♣ Stock options in 2006 for meeting and/or exceeding financial goals. ♣ Stock options in 2007 for meeting and/or exceeding financial goals ♣ Host of the 2006 Leadership Commitment Day for the Quebec division Show less
-
-
Education
-
Six Sigma Academy (Black Belt)
Certificate of competency, Lean Manufacturing
Community
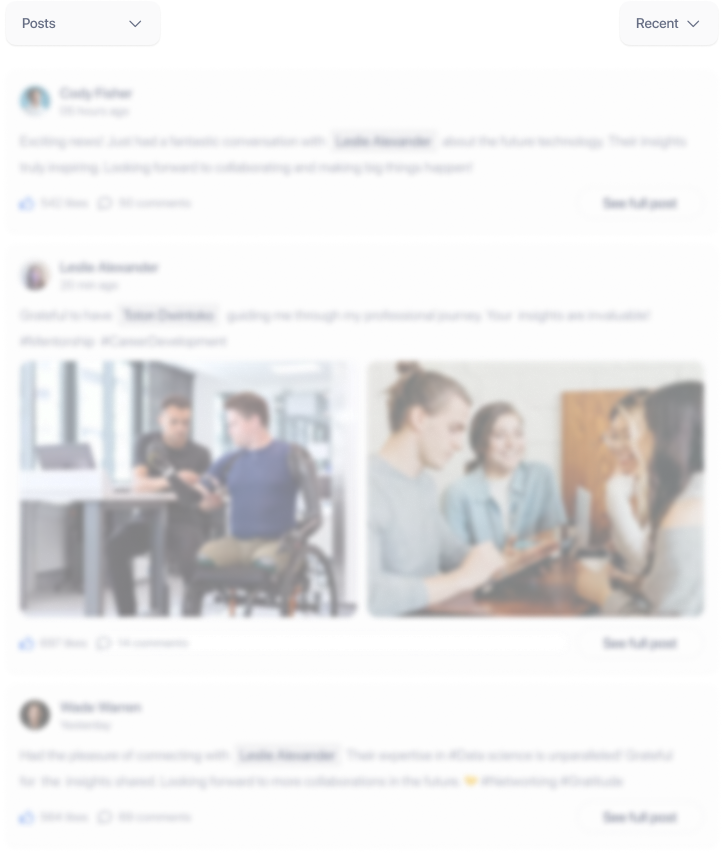