
James Clague
Pilot - Charter at Lyon Aviation- Claim this Profile
Click to upgrade to our gold package
for the full feature experience.
-
German -
Topline Score
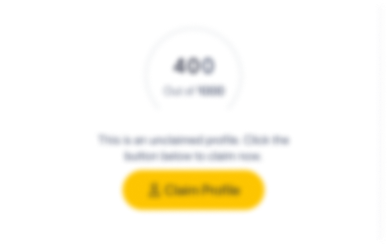
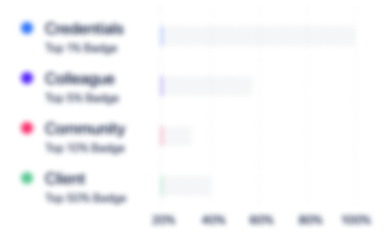
Bio


Experience
-
Lyon Aviation
-
United States
-
Airlines and Aviation
-
1 - 100 Employee
-
Pilot - Charter
-
Jan 2022 - Present
SIC charter pilot PIC type rated in the DA50 SIC charter pilot PIC type rated in the DA50
-
-
-
T&G Flying Club
-
United States
-
Airlines and Aviation
-
1 - 100 Employee
-
Certified Flight Instructor - Instrument
-
Feb 2021 - Present
-
-
-
Aery Aviation, LLC
-
United States
-
Airlines and Aviation
-
1 - 100 Employee
-
Pilot - Medevac & Surgical Transplant
-
Aug 2021 - Jan 2022
SIC medevac pilot PIC type rated in the Premier 1/1A SIC medevac pilot PIC type rated in the Premier 1/1A
-
-
-
Coast Flight Training
-
Airlines and Aviation
-
1 - 100 Employee
-
AAL Cadet
-
Feb 2020 - Jan 2021
FAA Part 141 Flight School (Instrument, Commercial, Multi, and CFI/CFII ratings) FAA Part 141 Flight School (Instrument, Commercial, Multi, and CFI/CFII ratings)
-
-
-
Collins Aerospace
-
United States
-
Aviation and Aerospace Component Manufacturing
-
700 & Above Employee
-
Commodity Manager, Engineered Items
-
May 2017 - Sep 2020
Developed long term sourcing strategies as it related to the engineered items/engine equipment commodity. Responsible for executing commodity strategy through use of internally developed tools in order to meet the business unit goals for cost savings and support of NPI programs. Liaison between engineering and program teams serving as project lead with the supply base to ensure projects met program schedules and performance requirements.. Developed long term sourcing strategies as it related to the engineered items/engine equipment commodity. Responsible for executing commodity strategy through use of internally developed tools in order to meet the business unit goals for cost savings and support of NPI programs. Liaison between engineering and program teams serving as project lead with the supply base to ensure projects met program schedules and performance requirements..
-
-
-
UTC Aerospace Systems
-
United States
-
Aviation and Aerospace Component Manufacturing
-
700 & Above Employee
-
New Product Introduction - Supply Chain Specialist / Industrial Engineer
-
Sep 2016 - May 2017
-
-
New Product Introduction - Supply Chain Sr. Analyst / Industrial Engineer
-
Jul 2014 - Sep 2016
-
-
-
Pratt & Whitney
-
United States
-
Aviation and Aerospace Component Manufacturing
-
700 & Above Employee
-
Production Supervisor
-
Nov 2013 - Jun 2014
-Supervising 15 bargaining unit employees in a high volume aerospace manufacturing environment-Assuring of 100% compliance with weekly safety walks, EH&S audits, and quality sweeps-Identifying and incorporating improvements to result in a 25% reduction in scrap, rework, and repair-Implementing a visual management system and supervisor standard work to achieve SWIP throughput, in alignment with customer needs-Supporting ACE Site and Cell Gold reassessments
-
-
Materials Manager
-
Mar 2013 - Oct 2013
-Automated the preparation of inventory, delivery, and planning reports by introducing and coordinating the integration of the Deployment Manager tool to the site, which eliminated 300+ hours per year of manual report preparation, added robustness to the reporting process, and added senior management visibility-Implemented improvements to the Demand Management Process flow and meeting format, based on feedback from its stakeholders and best practices from the UTAS Rockford plant sites which improved 90 day sales order linearity and stability-Developed a metrics reporting package and associated standard work as facilitator and implementation lead for the Master Scheduling team’s monthly ‘Demand Management' meetings-Co-lead a cross functional team to develop a process map, reporting tools, a metrics reporting package, and associated standard work for the newly created monthly Sales, Inventory, and Operations Planning Review Process - which linked together three BU key processes: Demand -Management, Delivery Assurance, and Profit Assurance. -Maintained a capacity planning tool for production planning
-
-
-
Hamilton Sundstrand
-
United States
-
Aviation and Aerospace Component Manufacturing
-
700 & Above Employee
-
Operations Manager
-
Jul 2012 - Feb 2013
-Received UTC Level 1 Award-Coordinated a Low Flow Mixed / Model VSM event with Duggan and Associates and executed the responsibilities of co-lead and implementation lead – with a benefits realization of a significantly reduced cycle time for the site, and a robust expedite process for both OEM and Aftermarket-Developed a metrics reporting package and associated SW for the E&CS ESM Ops team to include monthly results for: Delivery Performance, Delinquency, Kanban Integrity, EH&S, CoPQ, Escapes, -Delivery Performance, and Cycle Time-Maintained site level data integrity report card / associated queries to manage monthly integrity maintenance plan with MRP planners to drive towards 100% Data and SCI Integrity within JDE. ---Reduced data integrity errors by 50% – both for parts setup and SCI (interplant and vendor) and sustained gold level through monthly data integrity maintenance plan-Created, with the input from Supervisors, Operators, Planners, and Management, logic charts for the Plant’s FIFO lanes-Audited the value stream regularly as part of the VSM implementation plan with ‘SWIP to WIP checklist’ to verify and validate FIFO lane compliance within the shop floor-Developed Work Order Stocks / Starts flow sheet to create baseline reporting tool for tracking work order stocks / starts and worked with the newly defined roles to refine this pitch measurement tool as it relates to single point of scheduling future state
-
-
-
EH Orthopaedics
-
United States
-
Medical Equipment Manufacturing
-
Project Engineer
-
May 2011 - Aug 2011
-Project Manager for EnHatch’s web-based medical project collaboration tool, CoHatch -Developed a financial model for web-based social product development, consulting, and 510k submission-Coordinated EnHatch’s booth at the ’11 San Diego Shoulder Course, and travelled to assist the CEO for the event -Project Manager for EnHatch’s web-based medical project collaboration tool, CoHatch -Developed a financial model for web-based social product development, consulting, and 510k submission-Coordinated EnHatch’s booth at the ’11 San Diego Shoulder Course, and travelled to assist the CEO for the event
-
-
-
Movado Group, Inc
-
United States
-
Luxury Goods & Jewelry
-
700 & Above Employee
-
GIT Supply Chain Co-op
-
Aug 2010 - Jan 2011
-Provided SAP, SendSuite, and FedEx Ship Manager software, server, and interface support and update testing -Acted as liaison between user, customer, and dev teams to resolve both system and process issues -Created and maintained project documentation, flow charts, and training material-Developed data queries to diagnose discrepancies pertaining to FTZ operations and inventory management-Optimized both FICE and IPD international shipping procedures -Provided SAP, SendSuite, and FedEx Ship Manager software, server, and interface support and update testing -Acted as liaison between user, customer, and dev teams to resolve both system and process issues -Created and maintained project documentation, flow charts, and training material-Developed data queries to diagnose discrepancies pertaining to FTZ operations and inventory management-Optimized both FICE and IPD international shipping procedures
-
-
-
CBRE
-
United States
-
Real Estate
-
700 & Above Employee
-
Facilities Engineering and Management Co-op
-
May 2009 - May 2010
-Coordinated any necessary updates and repairs to the emergency electrical system Validated energy savings and coordinated rebates with NYSERDA and Energy Curtailment Services-Assisted the Project Management team by managing vendor’s project quality / schedule for a number of capital projects, including: ADA compliance retrofit, ADT Access Card System Replacement, Executive A/V installs, and water-proofing-Provided AutoCAD layouts for building events and updated engineering drawings for the various building projects
-
-
-
UPS
-
United States
-
Truck Transportation
-
700 & Above Employee
-
Industrial Engineering Co-Op
-
Aug 2008 - Dec 2008
-Compiled, analyzed, formatted, and sent out Daily and Weekly Engineering Audits to district managers-Updated and assembled weekly vehicle and driver locker reports Assessed NYPD parking ticket database, used Excel to determine high frequency ticket locations and infraction types, conducted on road analysis, and provided quick solutions to reduce month to month parking ticket costs by 30k+ -Audited package scans to analyze and compare district efficiency, analyze workflow, and validate delivery time
-
-
-
-
Co-Founder
-
May 2001 - Aug 2008
-Managed, maintained, and harvested 21 beehives annually -Utilized lean manufacturing principles to reduce waste wax in the processing steps-Marketed and sold products in a cohesive and professional manner to 5 local retailers -Managed, maintained, and harvested 21 beehives annually -Utilized lean manufacturing principles to reduce waste wax in the processing steps-Marketed and sold products in a cohesive and professional manner to 5 local retailers
-
-
Education
-
University of San Diego
Master of Business Administration (M.B.A.), Project Management -
Stevens Institute of Technology
Bachelor's of Engineering, Engineering Management
Community
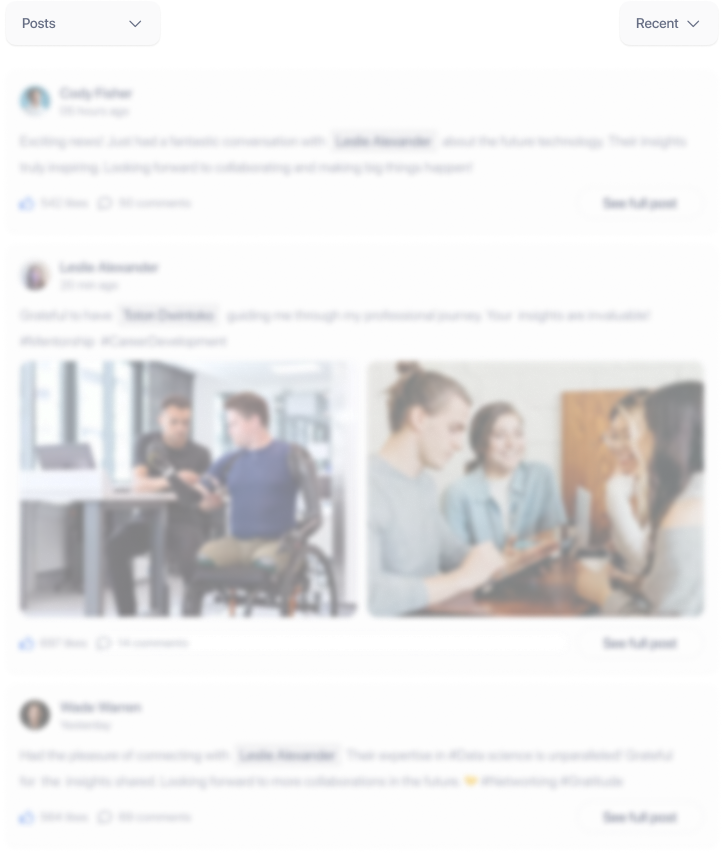