Jay Heininger
Quality Manager-Senior Quality Engineer at Johnson Medtech- Claim this Profile
Click to upgrade to our gold package
for the full feature experience.
Topline Score
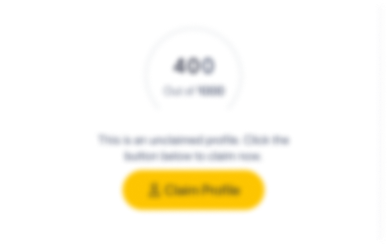
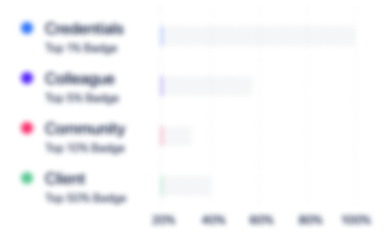
Bio


Experience
-
Johnson Medtech
-
United States
-
Medical Equipment Manufacturing
-
1 - 100 Employee
-
Quality Manager-Senior Quality Engineer
-
Oct 2017 - Present
FDA regulated environment, Class 2 – conductive printed circuits / in-vitro & biosensor monitors Facility transfer and setup in new location. Validation and new product launch. Reduction of Customer Complaints through root cause analysis. Class 7 Clean Room. Scrap cost identification and reduction through training and implementing the Lean Transformation principles of 6S. Integration of visual management and monitoring controls for Poka-yoke inadvertent error prevention. Achieving FDA compliance through principles of cGMP-current Good Manufacturing Practices and cGDP-current Good Documentation Practices. Implemented layered audits and DHR-Device History Record reviews and retention. Documentation of hidden factory knowledge into auditable, repeatable practices. Show less
-
-
-
NuVasive
-
United States
-
Medical Device
-
700 & Above Employee
-
Staff Validation, Engineer
-
Aug 2015 - Sep 2017
FDA regulated environment, Class 3 – spinal implants. Validation design and execution. Historical 483 remediation. Facility system transfer and expansion into a new facility including new design planning, installation, validation and training of High purity compressed air, Ultra High purity water system, Ultrasonic final wash system and Anodize (Type 2 and 3). Created IPM-Integrated Pest Management system. Created Safety (OSHA), Fire (EAP, FPP, Hot work, occupancy), EPA Water and Air discharge documentation and submissions. Contact material identification and tracking through creation of chemical and material specifications. Created and installed PM-Preventative Maintenance tracking system where one was not present before. GAP review of historical changes and risk mitigation. Manufacturing residue and bio-compatibility test validations. Show less
-
-
-
UTC Aerospace Systems
-
United States
-
Aviation and Aerospace Component Manufacturing
-
700 & Above Employee
-
Sr. Supplier Development Engineer – Aircraft Landing Systems
-
Jul 2013 - Aug 2015
Sr. Supplier Development Engineer – Aircraft Wheels and Brakes Sr. Producibility and Technical Support Engineer – Aircraft Landing Systems Supplier Development activities of Company & Supplier initiatives regarding product and key metric improvements systems and supplier trend analysis. Accountable for $95 Million spend. PPAP-Production Part Approval Process and system reviews of the product being outsourced. Sourcing strategy development and potential supplier evaluation. APQP-Advanced Product Quality Planning for producibility and feasibility of NPI-New Product Introduction. REACH-Registration, Evaluation, Authorization and Restriction of Chemicals supplier liaison. Execute Work Transfers, NDA-Non-disclosure Agreements, Export Control, SHA-Supplier Health Assessments and Supplier Cost Recovery. Support the implementation of the ACE-Achieving Competitive Excellence operating system, SIOP (Sales, Inventory, and Operations Planning), Supplier Gold achievement and Lean Transformation including the principles of 5S. Show less
-
-
-
IMDS
-
Vandalia, Ohio
-
Sr. Quality Engineer
-
Apr 2009 - Jul 2013
FDA regulated environment, Class 3 - implants. Validation - Special and standard processes Establish documented evidence and parameters for process and systems to perform effectively and reproducibly for Customer medical product to ISO 13485 and regulatory FDA compliance . IQ,OQ,PQ for Special Processes, contact agents and standard manufacturing equipment and process changes. Define and implement process improvements based on DoE, SPC and Process Limit Challenges for evaluating and monitoring processes. Remove non-value added work and streamline relevant systems into recognized industry standards. Institute Gage R&R and quality evaluation of measurement methods and equipment. ISO13485. Installed, debugged and validated multiple manual and automated ultrasonic wash/passivation systems totaling $700K (largest was 11 station) and including full documentation, mistake proofing, operator training and safety which included OEM review and approval. Problem solved for industry Tier 1 for quality issues of their ultrasonic system through DOE-Design of Experiments and Problem Solving. Show less
-
-
-
Delphi
-
United Kingdom
-
Motor Vehicle Manufacturing
-
700 & Above Employee
-
Quality Supervisor, Sr. Quality Engineer
-
Mar 1999 - Oct 2009
Proven abilities and drive led into Customer interaction on Launch programs and eventually encompassing the position of Quality Supervisor. Train staff, evaluate performance, and disciplinary action. • Reduced Customer Complaints by 85% through root cause analysis and value added auditing. • Cost improvements and mistake proofing through design, process and supplier based work. • Waste reduction through use of Customer and Supplier continuous improvement and metric reviews. • Successfully represent facility for Quality during third part ISO audits. • Instituted and lead upfront program reviews resulting in increased fixture equipment compatibility, part error proofing, and design manufacturability. • Increased manufacturing robustness through trade review and latest technology research. • Responsible for 500K units / month. • Reduced external ppm from 21 and 82 from previous years to under 0.5 ppm. Reduced from 2 spills / year (3 years running) to zero spills (4 years running). • Improved documentation control 98% and maintained for 4,600 documents / 4 product lines. Paperwork reduction projects produced consolidations of 29%, 34%, 47%. • Reduction in gage control discrepancies by 64%. • Improved label verification by 94% through failure analysis. • Eliminated chronic customer issues via SPC quality controls and mistake proofing equipment. • Cost savings of $251K with multifold workload increase through value stream review. • Reduced headcount by 83% ($311K) through upfront, SPC based validation. • Risk reduction and cost improvements by identification & instituting SPC tracking and pro-active reaction to production problem solving areas. • Reduced New Product Launch issues from historical 18 to 3 and then zero on last program resulting from up front design and supplier control work. • Reduced scrap costs through identifying and implemented statistical controls in production. • Reduced Customer complaints by establishing Preventive Maintenance schedule plans. Show less
-
-
-
-
Manufacturing Engineer
-
Dec 1992 - Mar 1999
Industrial & Manufacturing Engineer Administered time studies, coordinated process control, performed cost estimating, conceived & implemented fixture design, evaluated cost reductions and validated product testing. • Industrial Food preparation and Cooking equipment • Designed, installed, documented and trained a multiple model assembly line from (3) month lead to build on-demand. • Designed & re-engineered a multiple area product line into a single on-demand work load balanced, operator run, self sufficient, integrated machining and assembly cell through mentoring and hands on follow through teaching. • Implemented ISO 9000 system for manufacturing facility. • Assisted with machining cell installation and utilization with 97% efficiency including PM and quality checks. • Optimized cycle time and operator ease of use through CNC programming and joint process routing. • Reduced inventory holding through increased quality control and visual Kanban implementation. • Increased throughput from multiple machine, batch runs to one-off cycles through design improvement programs and common process reviews. • Setup scrap reduction programs which achieved good parts first time, every time through total system integration which included programming, documentation, equipment and training. Show less
-
-
Education
-
University of Dayton
BS, Manufacturing Engineering Technology -
University of Dayton
Masters of Business Administration (MBA)
Community
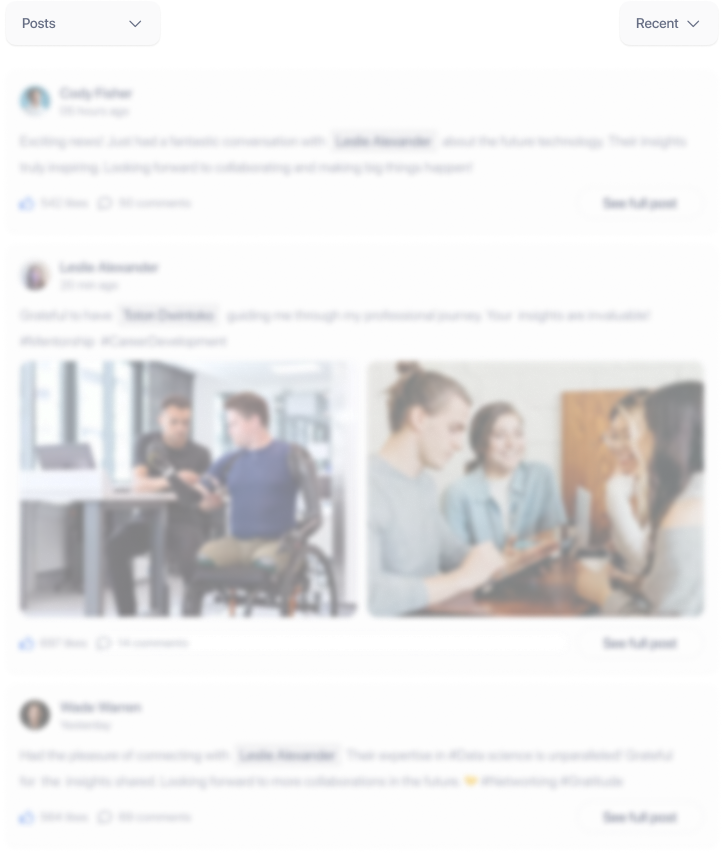