Jay Cummings
Project Manager at i.M. Branded- Claim this Profile
Click to upgrade to our gold package
for the full feature experience.
Topline Score
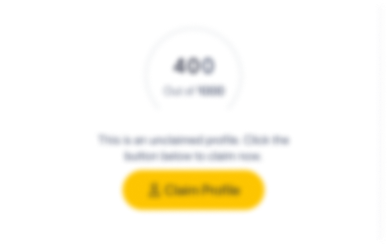
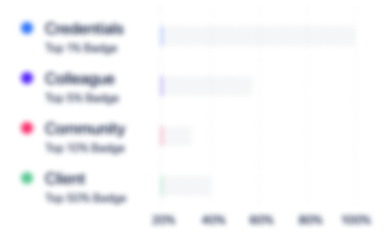
Bio


Experience
-
iMBranded
-
United States
-
Design Services
-
1 - 100 Employee
-
Project Manager
-
Feb 2017 - Present
-
-
-
Great Lakes Woodworking
-
United States
-
Furniture and Home Furnishings Manufacturing
-
1 - 100 Employee
-
Project Manager
-
Mar 2013 - Jan 2017
· Managed all aspects of national store fixture projects, including internal and external communications, scheduling, and implementation · Coordinated internal communications between engineering, purchasing, manufacturing and logistics during all stages of each project · Orchestrated all external communications surrounding projects, including coordination between Store Brand Project Managers, designers, architects and installers · Managed brands nationally, including Everything But Water, Fossil Watch Station, Ivivva, Lululemon, West Elm, Williams Sonoma, Rejuvenation Hardware, Restoration hardware
-
-
-
-
Logistics Manager
-
Oct 2010 - Mar 2013
· Continued all Master scheduling duties and took project management assignments as needed· Cross-trained all junior project managers· Supervised and coordinated activities of workers engaged in verifying outgoing shipments and preparing items for LTL, Full Blanket Wrap Trailer Loads and HLF Local Deliveries· Created shipment scheduling report, bills of lading, orders and other records to determine shipping priorities· Oversaw all outgoing shipping activities to ensure accuracy, completeness and condition of shipments· Analyzed all LTL shipment over a 1 year period to select a new LTL broker to achieve a 20% saving on outbound freight· Maintained vehicle maintenance reports· Excellent track record of on time deliveries & only three freight claims due to damaged freight
-
-
Master Scheduler
-
Aug 2003 - Mar 2013
· Planed and prepared Production Master Schedules for manufacturing of custom millwork and contract office furniture (5.5 M - 6M annual sales)· Maintained, analyzed and monitored compliance with a Ten-Week schedule, published on a weekly basis· Coordinated projected timelines with project managers and dealers· Designed, produced, and implemented an online, real-time Material Requisition and Tracking System to eliminate all paper transactions between planning, purchasing and scheduling · Researched, recommended, and purchased a Manufacturing Resource Planning (MRP) program compatible with current software · Conducted 6 month and annual performance evaluations and professional development goal setting for Planning Department personnel
-
-
Senior Project Manager
-
Aug 2003 - Feb 2006
· Coordinated efforts between architects, dealers, end users, engineering and manufacturing during all stages of each project· Reviewed project design for compliance with engineering manufacturing capabilities and company standards to meet architect and customer requirements and related specifications· Instructed and trained project/assistant Auto CAD draftsman to create shop drawings or client · · approvals and manufacturing· Instrumental in the transformation of the HLF’s change in direction from 85% flat panel manufacturing process/15% custom product, to a shift of 60% custom millwork and the adaptation from plastic laminate to hardwood and veneer as primary product components· Resumed master scheduling duties and responsibilities during sales slowdown and change in target markets
-
-
Material Manager: Manufacturing
-
Feb 1998 - Aug 2003
· Managed Project Department, Material Planning, Purchasing and Inventory for custom and contract office furniture manufacturing (6.2M annual sales)· Restructured and improved communications and procedures within and between material planning and production departments· Coordinated activities involved in procuring raw materials, equipment, tools, parts, and shop supplies · Managed vendor all aspects of external vendor relationships including obtaining product information, lead-time, delivery schedule, and managing all price negotiations. Contiguously worked to improve defective and unacceptable goods and services· Forecasted basic raw material (board, hardware, PVC, metal outsource components, custom stamping) with successful analysis of historical data and sales forecasts · Developed new and improved product lines in collaboration with the sales and marketing department by re-engineering product concepts, outsourcing, costing material and estimating and adjusting manufacturing costs· Implemented new procedures and create hardware pick lists for five different product lines · Assisted subordinates and supervisors throughout company in evaluating systems and processes to identify and eliminate waste to improve efficiency and cost-effectiveness· Conducted six month reviews for Purchasing Manager, Project Assistant, and Planners
-
-
Community
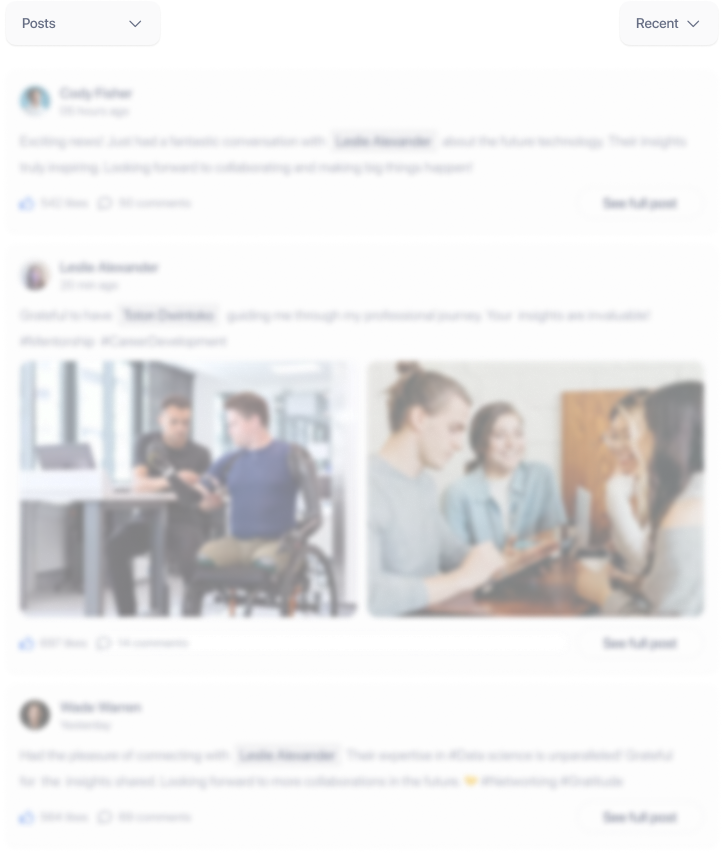