Jason Glocka
Sr. Supplier Quality Engineer - Standex ETG at Standex Engineering Technologies Group- Claim this Profile
Click to upgrade to our gold package
for the full feature experience.
Topline Score
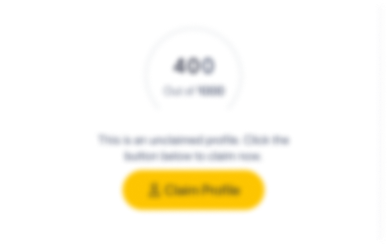
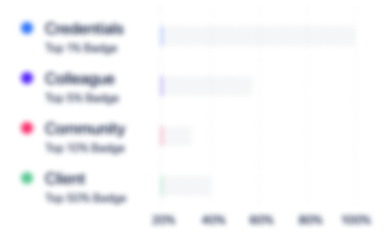
Bio


Experience
-
Standex Engineering Technologies Group (ETG)
-
United States
-
Aviation and Aerospace Component Manufacturing
-
1 - 100 Employee
-
Sr. Supplier Quality Engineer - Standex ETG
-
May 2022 - Present
-
-
-
Spincraft
-
United States
-
Aviation and Aerospace Component Manufacturing
-
1 - 100 Employee
-
Quality Manager
-
May 2015 - May 2022
-Maintain the QMS in compliance with AS9100C:ISO9001 standards; write, revise, and audit procedures as required-Management representative and champion of Management Review-Organize, schedule and facilitate all 3rd party and external audits-Maintain internal audit schedule designed with strategic layering for maximum effectiveness-Process all RMA's and warranty claims; interact with customers as required -Manage the RCCA process internally and externally; initiate, provide support or respond as appropriate utilizing the 5 why and 8D methodologies-Process owner for controlling nonconforming material, including identification, storage, disposition, and corrective action where necessary-Support role for Engineering with development activities including control plans, FMEAs, measurement methods and gage/fixture design-Provide support to specification review and flow down, change and configuration management, and transfer of work Show less
-
-
Quality Supervisor
-
Sep 2014 - May 2015
-Oversee inspection department and coordinate daily work load-QMS support role for NCR processing and calibration system
-
-
-
Ace Precision Machining
-
United States
-
Aviation & Aerospace
-
1 - 100 Employee
-
Quality Manager - Repair & Overhaul
-
Jun 2007 - Sep 2014
-Responsible for maintaining FAA FAR 145 regulations through quality systems management -Direct liaison for FAA, Air Agency, internal/external customer or supplier audits -Maintain PPM rating for global lead customer below 500 for 2 consecutive years -Ensure compliance to Company, Customer, and Federal Aviation Requirements by maintaining internal auditing systems -Facilitate corrective actions associated with internal/external rejections designed to eliminate reoccurrence and costs associated with poor quality -Utilize data collection to provide metrics that identify inadequate practices and processes; implement quality standards to improve processes and increase efficiencies -Support project management by assisting engineering with development, launch, and configuration management; submit FAIRs -Demonstrate leadership skills to develop motivational ethics within a team environment; capable of developing cross-functional teams -Oversee inspection department, provide appropriate coaching to motivate staff, discipline and reward employees, and resolve problems -Incorporate measurement methods and techniques to ensure the highest level of quality is maintained; manage calibration system including care, proper use, and storage of instruments -Designed a Quality database that incorporates verification of data entry to host program to eliminate human errors associated with legibility and paperwork Show less
-
-
-
Power-Packer
-
Netherlands
-
Motor Vehicle Manufacturing
-
100 - 200 Employee
-
Quality Engineering Technician
-
Jun 2005 - Jun 2007
-Responsible for receiving product evaluations and support of project development for hydraulic actuator systems for automotive companies such as GM, Pontiac, and Volkswagen -Documented accurate cost recovery for Supplier based nonconformance's -Certificate of Excellence Award for tracking supplier poor quality costs totaling 200k -Assisted with PPAP submittals by ballooning drawings, dimensional layouts, and compiling documentation, Capability studies, FMEA’s, and gage R&R -Provided assistance with local Supplier Quality development with onsite evaluations and process control Show less
-
-
-
Ace Precision Machining
-
United States
-
Aviation & Aerospace
-
1 - 100 Employee
-
Repair Analyst/Inspector
-
Nov 2001 - Jun 2005
-Perform receiving evaluation of APU components and determine appropriate repair level to bring units back into airworthy conditions -Provide manufacturing support by performing in-process and final inspection acceptance of repaired components; certified end units with air-worthy compliance to FAA and customer regulations -Investigated customer warranty claims; reviewed internal nonconformances for root cause/contributing cause to assist in preventive measures -Oversee final inspection plans for proper gage/method assignment and provide training to new inspectors Show less
-
-
Education
-
United States Army
Combat Engineer, Freedom
Community
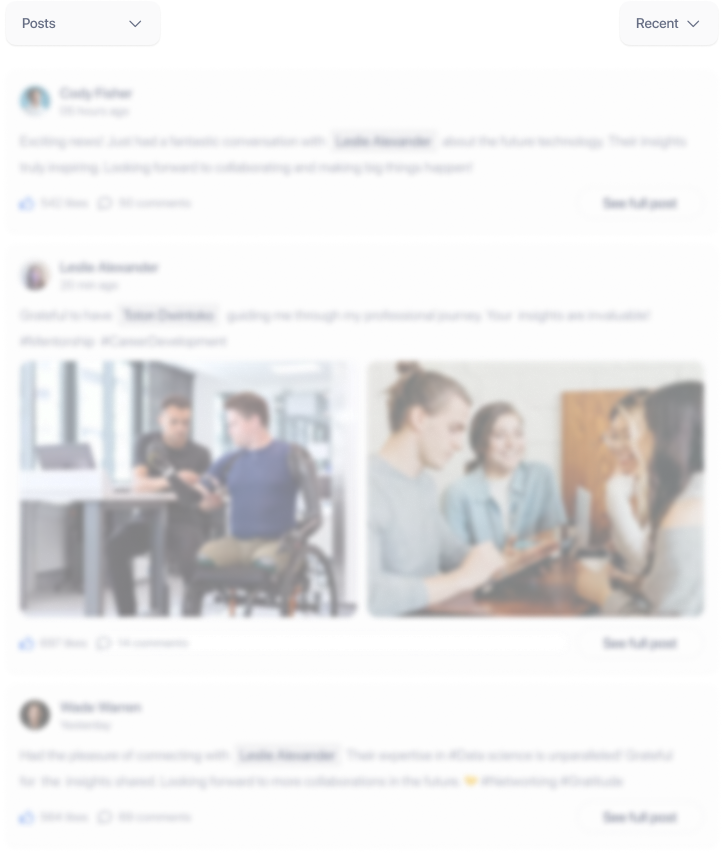