Jan Paul Beeke
QSHE Manager at VDL Weweler bv- Claim this Profile
Click to upgrade to our gold package
for the full feature experience.
-
English -
-
German -
-
French Elementary proficiency
Topline Score
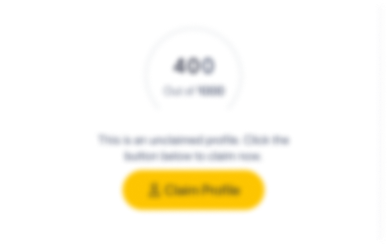
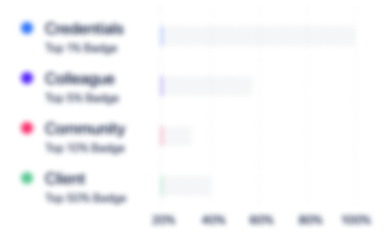
Bio

Frank van Rijnsoever
Jan Paul is an enthusiastic team player has a keen eye on the interests of his clients, is an excellent Field Service Engineer with a strong sense of understanding clients needs and building up relationships. To serve them well Jan Paul will go the extra mile !

Frank van Rijnsoever
Jan Paul is an enthusiastic team player has a keen eye on the interests of his clients, is an excellent Field Service Engineer with a strong sense of understanding clients needs and building up relationships. To serve them well Jan Paul will go the extra mile !

Frank van Rijnsoever
Jan Paul is an enthusiastic team player has a keen eye on the interests of his clients, is an excellent Field Service Engineer with a strong sense of understanding clients needs and building up relationships. To serve them well Jan Paul will go the extra mile !

Frank van Rijnsoever
Jan Paul is an enthusiastic team player has a keen eye on the interests of his clients, is an excellent Field Service Engineer with a strong sense of understanding clients needs and building up relationships. To serve them well Jan Paul will go the extra mile !

Experience
-
VDL Weweler bv
-
Netherlands
-
Manufacturing
-
100 - 200 Employee
-
QSHE Manager
-
Mar 2022 - Present
-
-
Senior Quality Engineer
-
May 2014 - Mar 2022
The Senior Quality Engineer ensures that internal and external quality requirements are adequately addressed in the project organization. The quality status of project results and project specific processes is checked and recorded by performing suitable verification procedures (e.g. participation in review meetings, development process checks). Deviations of defined standards are recognized in time and reported to management, corrective actions are initiated and tracked. Core Responsibilities: ¬ Planning and tracking of quality goals and quality assurance tasks (e.g. reviews, qualifications) ¬ Check for process compliancy within the project ¬ Agreement to process tailoring ¬ Independent reporting on quality assurance issues ¬ Initiation of corrective actions in case of process deviations ¬ Support and coaching of the project team regarding all quality issues and processes ¬ Coordinate with Engineering department. ¬ Support and coaching of the launch team regarding all production quality issues and processes ¬ Support of customer quality functions per customer assignment ¬ Access to all project documents including change requests and development results ¬ Independent reporting (esp. from the reporting of the Project Manager)¬ ¬ Escalation of process deviations and problems to Head of quality in case of red project status.¬ SQA - Supplier Development, executing process audits (VDA 6.3) at casting foundries and Forging companies in Europe, India and China. Show less
-
-
-
Human Empowerment
-
Netherlands
-
Human Resources
-
1 - 100 Employee
-
Interim Quality Engineer
-
Jan 2014 - May 2014
The Senior Quality Engineer ensures that internal and external quality requirements are adequately addressed in the project organization. The quality status of project results and project specific processes is checked and recorded by performing suitable verification procedures (e.g. participation in review meetings, development process checks). Deviations of defined standards are recognized in time and reported to management, corrective actions are initiated and tracked. Core Responsibilities: ¬ Planning and tracking of quality goals and quality assurance tasks (e.g. reviews, qualifications) ¬ Check for process compliancy within the project ¬ Agreement to process tailoring ¬ Independent reporting on quality assurance issues ¬ Initiation of corrective actions in case of process deviations ¬ Support and coaching of the project team regarding all quality issues and processes ¬ Coordinate with Engineering department. ¬ Support and coaching of the launch team regarding all production quality issues and processes ¬ Support of customer quality functions per customer assignment ¬ Access to all project documents including change requests and development results ¬ Independent reporting (esp. from the reporting of the Project Manager) ¬ Escalation of process deviations and problems to Head of quality in case of red project status. Show less
-
-
-
Quality Tracking B.V.
-
Almere
-
Business Developer
-
Mar 2013 - Dec 2013
Executing customer specific projects according to planning Develop and ensure business continuation of Quality Tracking B.V. Executing customer specific projects according to planning Develop and ensure business continuation of Quality Tracking B.V.
-
-
-
JP Beeke BV
-
Baarn
-
DGA (shareholder)
-
Mar 2012 - Feb 2013
Taking time off to be with my wife and youngest daughter and having a fresh start. (Inter-)national job inquiries are preciated and welcome. Taking time off to be with my wife and youngest daughter and having a fresh start. (Inter-)national job inquiries are preciated and welcome.
-
-
-
voestalpine
-
Austria
-
Mining
-
700 & Above Employee
-
Project Engineer
-
Mar 2011 - Mar 2012
Project Leader for new business, resource planning to reach PPAP status.Coordinator Project team.Informs and communicate progress with customer.
-
-
Customer Services - Field Service Engineer
-
May 2004 - Feb 2011
Worked with all personnel and outside contacts to satisfy clients and achieve company goalsIdentify areas of improvement in the company and assist in creating and implementing solutionsIdentify wasteful or inefficient practices and other unnecessary expenses to maintain a strong “Index of 1”Have a thorough working knowledge customer specific quality demands.Has a thorough understanding of and practices techniques to identify and analyse quality defects in steel automotive press parts.Perform remedial repair, sort out or replace activities on customer site in case of severe quality defects.Require infrequent backline support while performing remedial activities on-site.Recognize situations requiring a service call Escalation and follows proper Escalation Procedures.Provide the support required to close service events promptly, within the SLA and to the satisfaction of the customer (“fix the customer”)As needed, communicates frequently with customers and back office Quality departmentValidating actual problem and validating correct parts to be used for serviceEffective 'debrief' and reporting of service call for future enhancementsTravel to and from customer locations (usually by car), documenting work activity and maintainingadministrative paperwork. Show less
-
-
Material Planner
-
Mar 1995 - May 2004
Responsable for ordering raw materials for automotive pressing parts.Keep up economical and physical stock control.Member of purchasing team for ordering process.Participate in improvement processes.
-
-
Teamleader production
-
Nov 1991 - Mar 1995
Build up new equipment for blanking coils to sheets for pressing steel automotive press parts for various OEMs
-
-
-
Vogels Engineering
-
Bussum
-
Junior designer
-
Jun 1991 - Sep 1991
Company went bankrupt. Not my fault, :-) Company went bankrupt. Not my fault, :-)
-
-
Education
-
Symbol
Black & Green belt, Lean Six Sigma -
Kenteq
CREBO 94422, Commercial Engineer -
Regina Coeli
A2, French Studies -
MBO
uni, mechanical engineering
Community
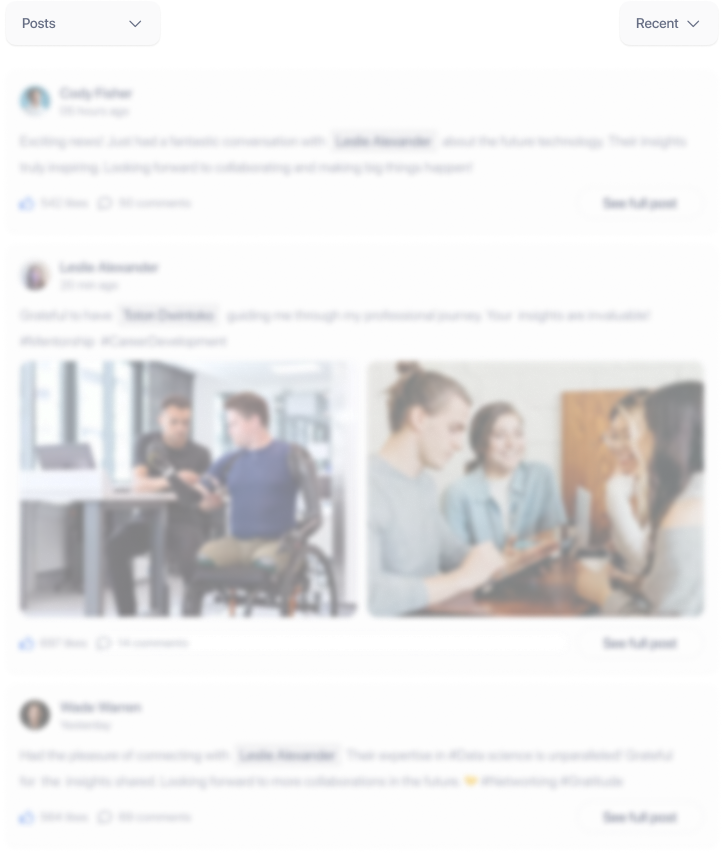