Jamil Ganondvala
Senior Textile Technologist at Workwear Group- Claim this Profile
Click to upgrade to our gold package
for the full feature experience.
-
English Full professional proficiency
-
Russian Limited working proficiency
Topline Score
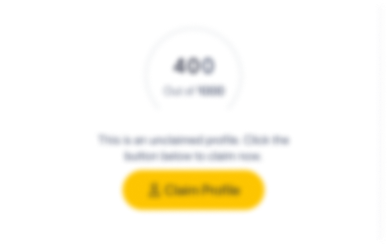
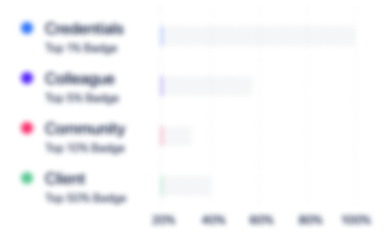
Bio


Experience
-
Workwear Group
-
Australia
-
Retail Apparel and Fashion
-
200 - 300 Employee
-
Senior Textile Technologist
-
May 2018 - Present
-
-
-
Australian Weaving Pty Ltd
-
Textile Manufacturing
-
1 - 100 Employee
-
Account Manager
-
Nov 2016 - May 2018
Key Achievements • Improved import cost by 15% for Esprit Beach Towels by successfully sourcing from alternate Indian jacquard supplier, and negotiating better from existing printed supplier in China. • Increased the Gross Profit Margin of Dri Glo 1000Thread Count Fabric Sheet sets by buying better price i.e US$ 15 for Queen Set from previous import of US$ 18 (approx.). • Reduced import cost (FOB) by 18% for Esprit New Zealand through adding new supplier and re-negotiating with existing supplier base for their 2017 range including printed Quilt Covers, Plain Dyed Sheet sets, & Jacquard towel. • Reviewed & signed-off colour labdips, printed strike-offs, fabric construction and finish, packaging, trims and accessories for Esprit, Dri Glo, Dickies & Freckles. • Managed critical path of bulk orders for David Jones, Myer, Harris Scarfe, TJX, Woolworths, Spotlight, Best & Less • Anticipated and managed delays beforehand due to delay in approvals, raw material delivery to factory, trims and accessories approval and their respective production lead times for both sampling & bulk production.
-
-
-
Afroze Textiles Industries Pvt. Ltd.
-
Pakistan
-
Textile Manufacturing
-
200 - 300 Employee
-
Senior Sales Manager
-
Jul 2007 - Nov 2016
• Developed & converted the yarn dyed hoody jacket into reactive dye over white paste printed plaids. Thus simplified the production process to achieve the required minimum order quantity & cost reduction by 25% of overall garment.• Conceived and developed most economical apron fabric. When normal apron fabric was costing not less than $1.8/pc, by carefully selecting the most economical fabric structure, special material for the binding to give it the weight along with low cost sublimation print on the chest, managed to develop apron with cost of $1.00/pc thus saving cost by 44% of the cost of the garment. The idea was so much appreciated by the buyer and licensor that a bulk order of 100k was placed to be produced in 45 days lead time.• Normal commercial laundry towels and bedlinen are made of durable yarn and construction which can withstand 60-80 high temperature commercial washes. For one the largest Danish laundries, developed a 550gsm 100% Cotton terry towel and T250 PC stripe sateen bedlinen which can withstand 150 high temperature washes. Tested both towels and bedlinen for 150 washes in the laboratory for 45days. And successfully passed all the technical tests in the products.• Developed Cotton & Polyester Cotton blend bottom wears including chino pants, shorts, skirts with Lycra stretch and non-stretch fabrications. This includes Twill, Drill, Satins, Denims• Developed and presented Aprons in various fabrications including Panama, Half Panama, Twills, Drills, Denim fabrics across many styles including long bibs, short waist to customers.• Managed and controlled production and delivery schedule of Hospitality Clothing & Uniforms including Aprons (short, long), Shirts, Pants, Polos & Tote Bags for Moravia Propag in Year 2014-16.• Administered and executed production orders for Best & Less for over 1 year.
-
-
Sales Manager
-
Jun 2004 - Jun 2007
• Developed new innovative fibers fabrics including Bamboo, Lycoell, Tencel, Modal, Recycled PET bottles & cotton-Viscose blend.• Developed Organic cotton fabrics in both wovens and knits.• Developed Polyester Cotton blend knitted terry fabrics for Hoodies & Jackets.• Constructed water repellent rain coat fabrics from 100% polyester and nylon fibers.• Developed round beach towels with fringe lace for Best & Less. As cotton tends to shrink and lint after wash, and creating puckering effect on the round edges. So, to design and develop a flawless product, lace was made from carefully selected and tested pre-shrunk, low lint combed yarns.• Developed promotion table covers and napkins for Czech beer brands in three different constructions including 100% cotton 180gsm and 140gsm fabric for reactive print and polyester cotton blend Jacquard solid dyed fabric• Conceived and developed foil printed towels with coordinated bed linens for Top Shop Stores• Developed baby receiving blankets from special knitted cotton fabrics and cotton flannel fabrics • Conducted Dye identification tests in the laboratory for reactive, VAT, pigments, disperse, direct and indigo.• Reviewed & approved inspection reports from factory & third party inspection based on AQL standards• Conduct wearer tests to ensure that product is suitable for fit purposes.
-
-
-
Nina Industries Limited
-
Pakistan
-
Textile Manufacturing
-
1 - 100 Employee
-
Sales Executive
-
Feb 2003 - Jun 2004
Key Achievements • Prepared concept designs for the project “Twister” an adult game, transformed it on the bedlinen products, and successfully managed its production for a licensor in UK called Bed Games • Initiated and managed product development for key retail accounts such as Carrefour in France & Matalan and House of Fraser in UK. Key Achievements • Prepared concept designs for the project “Twister” an adult game, transformed it on the bedlinen products, and successfully managed its production for a licensor in UK called Bed Games • Initiated and managed product development for key retail accounts such as Carrefour in France & Matalan and House of Fraser in UK.
-
-
-
-
Product Development & Quality Assurance Officer (Apparel Technologist)
-
Aug 2001 - Feb 2003
Key Achievements • Developed various fabric constructions from cotton spandex core spun yarn in both warp and weft directions for bottom & top wears. Successfully processed the fabrics from bleaching, dyeing and finishing machines in such a way that fabric didn’t lose its stretch properties during manufacturing processes. Thus awarded the status of first Lycra Fabrics approved vendor from Pakistan. • Developed and tested all the products for the Oeko Tex certifications, which then eventually lead to acquire Oeko Tex certifiation from German authorization body. After which all the apparel/bottom wear products produced in Nakashbani were Oeko Tex certified. • Managed Quality Assurance of Dyed Fabrics over various processing stages including Desizing, Bleaching, Mercerizing, Pad Thermosol Dyeing, Pad Steam Dyeing, Stenter Dyeing, Finishing, Emerizing and Sanforizing. • Developed 100% Cotton & Polyester Cotton blend bottomwears including chino pants, shorts, skirts with Lycra stretch and non-stretch fabrications. This includes Twill, Drill, Satins, Denims. • Developed special functional finished fabrics including Stain Release, Soil Release, Water Repellent, Fire Retardant & Teflon finish for bottom wears. • Controlled and tested production of Peach/Emerized/Raised fabrics for top and bottomwears.
-
-
-
-
Internee
-
Sep 2000 - Sep 2000
Internship in the Textile Applications Laboratory studying and practicing various textile chemical processes and applications on fabrics. Internship in the Textile Applications Laboratory studying and practicing various textile chemical processes and applications on fabrics.
-
-
-
-
Internee
-
Aug 1999 - Aug 1999
Four weeks internship practicing the manufacturing process of Stuffed Toys and Marketing & Promotion of Disney licensed Stuffed Toys to US Markets. Four weeks internship practicing the manufacturing process of Stuffed Toys and Marketing & Promotion of Disney licensed Stuffed Toys to US Markets.
-
-
-
-
Internee
-
Jun 1999 - Jun 1999
Four weeks internship in the weaving section, learning each step of fabrication. Four weeks internship in the weaving section, learning each step of fabrication.
-
-
-
-
Internee
-
Jul 1998 - Jul 1998
Four week internship in Spinning, during which I gained comprehensive understanding of yarn making process. Four week internship in Spinning, during which I gained comprehensive understanding of yarn making process.
-
-
Education
-
Textile Institute of Pakistan
BSc (Hons), Textile Science (Apparel & Textile Manufacturing) -
Aga Khan School Garden, Karachi
Community
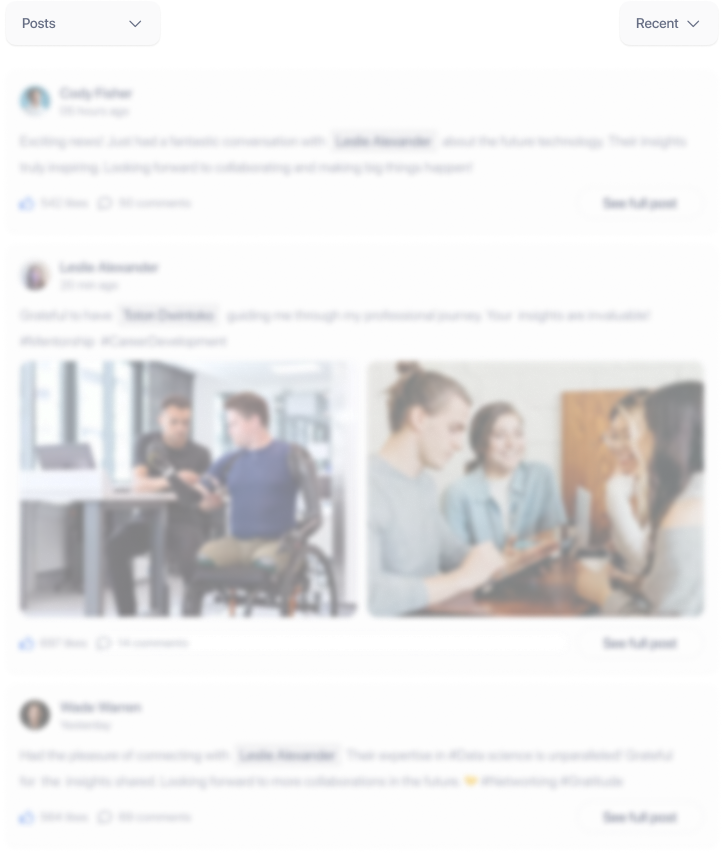