
Jamie Kral
Director, Customer Experience at Norix Furniture- Claim this Profile
Click to upgrade to our gold package
for the full feature experience.
Topline Score
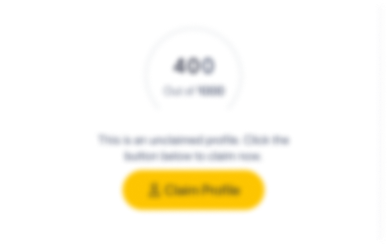
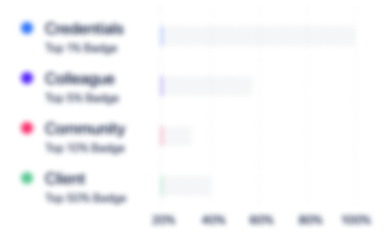
Bio


Experience
-
Norix Furniture
-
United States
-
Furniture and Home Furnishings Manufacturing
-
1 - 100 Employee
-
Director, Customer Experience
-
Jan 2021 - Present
-
-
Customer Experience Manager
-
Jan 2018 - Jan 2021
• Accountable for servicing customers as a top priority by managing the complete order process, from providing quotes to communicating directly with the customers and field representatives on manufacturing, shipping and delivery inquiries.• Training and development of Customer Care Specialists in every facet of the position, particularly in utilizing key software to provide customer support, up-sell customers, and close orders.• Support team in investigation of issues with existing orders and respond to customers in a timely manner, interfacing with manufacturing and shipping on delivery inquiries while reviewing incoming orders for thoroughness and accuracy to ensure orders ship on time and complete.
-
-
Quality Assurance Manager
-
Dec 2016 - Jan 2018
• Develop and maintain guidelines to effectively communicate Company’s requirements and expectations to our present and future supply partnerships.• Develop and maintain a quality production program to ensure conformity of purchased material and final products to quality standards.• Summarize and report defect analyses, corrective actions, implementation status and effectiveness.• Visit supplier facilities on a quarterly, or as needed basis, to review quality specifications and resolve any quality problems as required.• Work directly with Purchasing, Engineering, Manufacturing and supply chain to resolve product and service issues.• Work closely with R&D to develop new product development quality specifications.• Work closely with Engineering and R&D for testing of new products and existing product base as needed.• Develop and maintain testing processes and requirements to gauge acceptance and rejection criteria.• Assist Purchasing and Engineering in new supplier evaluations.
-
-
-
UICO, Maker of duraTOUCH®
-
United States
-
Appliances, Electrical, and Electronics Manufacturing
-
1 - 100 Employee
-
Process Engineering Manager
-
Jan 2014 - Dec 2016
• Managed team designing, testing, documenting effects of critical design specs and tolerances on sensor performance, weighing cost/benefit of each• On Cell Watch Demo: Design, Program Management, Execution, Delivery• Managed team in identifying opportunities to streamline functional test for chip sales model• Transition of programs to Asian Manufacturing Partner, 2016 projected savings $500k• Managed factory move to new facility, projected yearly savings $300k• Solved display bonding hurdles for Key Customers which led to award of business• Manage direct reports in manufacturing and supporting roles• Design influencer for new market product hurdles• Next Gen Chip Test Methodology, Oversaw Design & Implemented at Manufacturing Partner• New Format Technology; Major contributor with CTO through prototype and feasibility stage• Led team of engineers in developing new Sensor Patterns for wearables• Manage factory daily operations• Effective Mentoring, Training and Team buildingSkills• Midlevel Leadership• Manufacturing Operations• Strategic Planning and Execution• New Product Introduction• Design Of Experiment• Design For Manufacturing• Continuous Improvement• Process Development• Value Stream Mapping• Lean Manufacturing• Startup Companies• PQ&A • FMEA Process/Design/Test• ISO 9001• PPAP• Kaizan
-
-
Manufacturing & Process Engineering
-
Dec 2012 - Jan 2014
• Proto/Qual/Pilot Build Management and validation at partner manufacturing facility in Asia• Bridge: Initiate & Implement Engineering Teams initiatives into Operations• Helped engineering solve reliability issues to enable progression to next product launch stage • Redesigned adhesive solving curing issues and improving manufacturing process yield by 10%• Technical Assessment of key alternative suppliers• Created & Implemented Test Plans for Verification and Validation phases of NPI• DFM/Continuous Improvement, driving new concepts & solutions to existing & future designs• Equipment selection, implemented and managed PM of equipment• Onsite problem solving for key customers• Implemented Employee Training Program• Re-designed floor layouts resulting in increased product visibility and efficiency• MFG Metrics; Yield, Scrap, Training, Safety, Committed/Actual Shipments, On time delivery, Quality
-
-
Quality Manager
-
Jul 2009 - Dec 2012
• Oversaw ISO programs, facilitated ISO Certification• Implemented and managed equipment calibration• Continuous Improvement Teams: Production Layout, Continuous Flow Processing, Inventory Management• Supplier Quality: System Audits, Component Verification, Defective Material Reports, Supplier Corrective Action• Customer Quality: FPA, PPAP, Customer Pilot Runs, Line and Field Failure Analysis• Metrics: Weekly Yield, Product Yield, Corrective Actions, On Time Delivery Production & NPI
-
-
-
-
Quality Engineer
-
Mar 2006 - Jul 2009
• Work Instructions, BOM's, Sustaining Engineering, • Control Plans, Process Capability Studies, Pilot Runs, Training, Internal Corrective Action• Process: develop, implement, improve, document, operator train• Program Launch: Design Reviews, Proto and Pilot Builds• Member of ESD Improvement Team, Performed quarterly ESD Audits• Member of Glass Improvement Team, Leader of Targeted Product Improvement Teams• Functional Test: Data Analysis, Test Goals, Test Design & Improvement• Training Experience: Glass Inspection Trainer, Manage Gauge R&R’s
-
-
-
-
Quality Engineer
-
May 2002 - Mar 2006
• Work Instructions, BOM's, Sustaining Engineering, • Control Plans, Process Capability Studies, Pilot Runs, Training, Internal Corrective Action• Process: develop, implement, improve, document, operator train• Program Launch: Design Reviews, Proto and Pilot Builds• Member of ESD Improvement Team, Performed quarterly ESD Audits• Member of Glass Improvement Team, Leader of Targeted Product Improvement Teams• Functional Test: Data Analysis, Test Goals, Test Design & Improvement• Training Experience: Glass Inspection Trainer, Manage Gauge R&R’s
-
-
Intern
-
Oct 1998 - May 2002
• Analyze customer returns• Operate production machinery• Assist engineers
-
-
-
-
Retail Sales Associate
-
May 1996 - Mar 2003
• Assist retail customers• Stock product, food preparation• Operate cash register • Assist retail customers• Stock product, food preparation• Operate cash register
-
-
Education
-
Northern Illinois University
Bachelors, Electrical Engineering Technology -
Waubonsee Community College
Associate of Science (A.S.), Engineering
Community
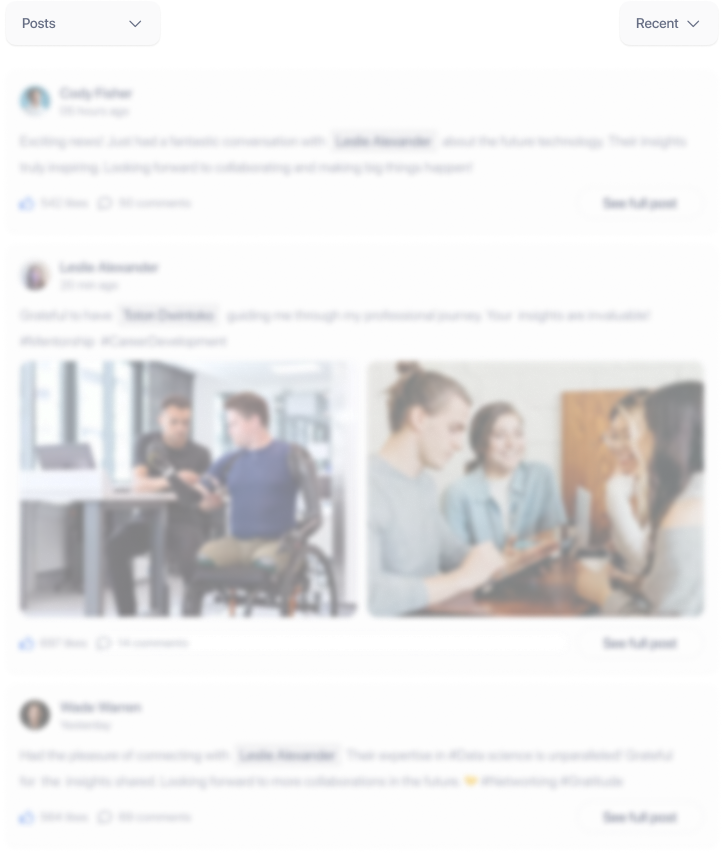