James Simpson
at Promedics Orthopaedic Ltd- Claim this Profile
Click to upgrade to our gold package
for the full feature experience.
Topline Score
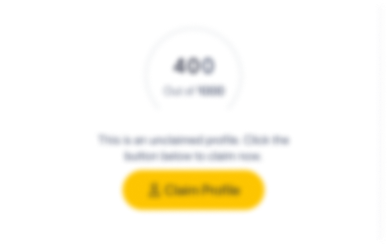
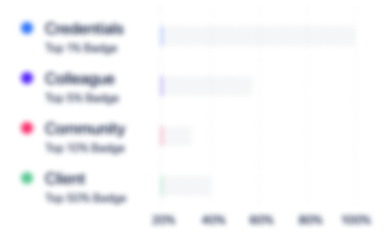
Bio

Aileen Brown
James has worked with the team at John Robertson & Sons Hamcurers Ltd, initially as a management consultant and latterly as Interim Operations Director. He has rolled out performance dashboards and successfully brought in cost savings to the business. He has a highly analytical mind, works in a professional and focused manner at all times, and has been of a great benefit to the company. We would recommend him for all operational projects and wouldn't hesitate to use his services again. On a personal note, I have thoroughly enjoyed working alongside him, and have found him a very good support to me in my position as Finance Director.

Elspeth Talbot
Having worked with James in the past, we were keen to employ his skills once again in his role as management consultant. James has provided a hands-on practical service, tailored to our current requirements. He's highly focused on producing results that are relevant and useful to us. He's good at communicating with all sections of our workforce and encouraging positive relationships within our company. I would highly recommend his services.

Aileen Brown
James has worked with the team at John Robertson & Sons Hamcurers Ltd, initially as a management consultant and latterly as Interim Operations Director. He has rolled out performance dashboards and successfully brought in cost savings to the business. He has a highly analytical mind, works in a professional and focused manner at all times, and has been of a great benefit to the company. We would recommend him for all operational projects and wouldn't hesitate to use his services again. On a personal note, I have thoroughly enjoyed working alongside him, and have found him a very good support to me in my position as Finance Director.

Elspeth Talbot
Having worked with James in the past, we were keen to employ his skills once again in his role as management consultant. James has provided a hands-on practical service, tailored to our current requirements. He's highly focused on producing results that are relevant and useful to us. He's good at communicating with all sections of our workforce and encouraging positive relationships within our company. I would highly recommend his services.

Aileen Brown
James has worked with the team at John Robertson & Sons Hamcurers Ltd, initially as a management consultant and latterly as Interim Operations Director. He has rolled out performance dashboards and successfully brought in cost savings to the business. He has a highly analytical mind, works in a professional and focused manner at all times, and has been of a great benefit to the company. We would recommend him for all operational projects and wouldn't hesitate to use his services again. On a personal note, I have thoroughly enjoyed working alongside him, and have found him a very good support to me in my position as Finance Director.

Elspeth Talbot
Having worked with James in the past, we were keen to employ his skills once again in his role as management consultant. James has provided a hands-on practical service, tailored to our current requirements. He's highly focused on producing results that are relevant and useful to us. He's good at communicating with all sections of our workforce and encouraging positive relationships within our company. I would highly recommend his services.

Aileen Brown
James has worked with the team at John Robertson & Sons Hamcurers Ltd, initially as a management consultant and latterly as Interim Operations Director. He has rolled out performance dashboards and successfully brought in cost savings to the business. He has a highly analytical mind, works in a professional and focused manner at all times, and has been of a great benefit to the company. We would recommend him for all operational projects and wouldn't hesitate to use his services again. On a personal note, I have thoroughly enjoyed working alongside him, and have found him a very good support to me in my position as Finance Director.

Elspeth Talbot
Having worked with James in the past, we were keen to employ his skills once again in his role as management consultant. James has provided a hands-on practical service, tailored to our current requirements. He's highly focused on producing results that are relevant and useful to us. He's good at communicating with all sections of our workforce and encouraging positive relationships within our company. I would highly recommend his services.
0
/5.0 / Based on 0 ratingsFilter reviews by:
Credentials
-
Institute of Leadership & Management
Level 5 Certificate in Coaching & Mentoring for Managers
Experience
-
Promedics Orthopaedic Ltd
-
United Kingdom
-
Medical Equipment Manufacturing
-
1 - 100 Employee
-
-
Jul 2022 - Present
With over 180 employees in the UK, Promedics are a market leading Orthopaedic manufacturer and supplier into every Hospital in the UK through the NHS, and a key partner to many companies in Europe, USA and other International markets. With one of Europe's largest orthopaedic manufacturing facilities based in the UK, and 40,000 sq foot warehouse. Promedics commitment to European product design and manufacturing is clear, to give unrivalled quality and service levels to our customers in our home market and abroad.As Director of Operations, I oversee all the of operations functions for our customers in both the UK and further afield. Show less
-
-
-
Oct 2021 - Jul 2022
With over 180 employees in the UK, Promedics are a market leading Orthopaedic manufacturer and supplier into every Hospital in the UK through the NHS, and a key partner to many companies in Europe, USA and other International markets. With one of Europe's largest orthopaedic manufacturing facilities based in the UK, and 40,000 sq foot warehouse. Promedics commitment to European product design and manufacturing is clear, to give unrivalled quality and service levels to our customers in our home market and abroad.As Operations Manager, I over the see the supply, manufacture and distribution of our products to all of our customers in both the UK and further afield. Show less
-
-
-
-
Management Consultant
-
Nov 2017 - Present
We are an independent improvement consultancy with a strong focus on LEAN Management, transformational, coaching and cultural change. We are though not restricted to manufacturing companies with experience across a wide range of industries including Food & Drink, FMCG, Electronics & the Service Industry. Each client project is specific to improving and developing their KPI's and overall business improvement.. Our aim is improve business by identifying and then reducing non-value added elements, whist increasing value-added elements, providing a structured improvement plan to do this We can select short term, quick fix projects or full scale transformation programs, as well as providing targeted coaching programs across the workforce. Show less
-
-
-
-
Operations Manager
-
Jul 2019 - Oct 2021
Since 1964, Clarke has provided the largest line of diesel fire pump drivers in the world. We design and assemble all of our engine in accordance to NFPA 20 and list products with Underwriters Limited and Factory Mutual. With expert engineering, 24/7 global customer support, and quality manufacturing partners, we continue our mission of protecting people and property all over the world. Today, Clarke is recognised worldwide as a leading manufacturer of diesel fire pump engines, with manufacturing facilities in Cincinnati, OH USA and Coatbridge, Scotland UK. As Interim Operations Manager, I oversee the Coatbridge production, producing diesel fire pump drivers for the UK, Europe, Africa, Asia and Australasia. Show less
-
-
-
EMS Cognito
-
United Kingdom
-
Business Consulting and Services
-
1 - 100 Employee
-
Associate Process Improvement Consultant
-
May 2018 - Jul 2021
EMS Cognito is an international Operations Consultancy, based in the UK, with a track record of helping leading manufacturers and processors gain competitive advantage in diverse industries. By providing cost-effective consulting, that employs a unique blend of World Class methodologies and an integrated approach to implementation, we help companies make lasting improvements to their operation. EMS Cognito is an international Operations Consultancy, based in the UK, with a track record of helping leading manufacturers and processors gain competitive advantage in diverse industries. By providing cost-effective consulting, that employs a unique blend of World Class methodologies and an integrated approach to implementation, we help companies make lasting improvements to their operation.
-
-
-
-
Interim Operations Director
-
Jan 2018 - May 2019
A multi-site pork abattoir and processor producting a wide range of QMS approved pork and ham products for Food Service, Independent Butchers, and National Retailers. With approximately 100 employees covering the areas of Slaughter, Butchery, Secondary Processing, Warehouse & Logistics key deliverables included: - - Creation of a performing Senior Management Team with the development of a KPI Dashboards - Delivered £200k annual labour saving though cost reduction and Collective Consultation. - Returned business to profit by the end of 2018 - Achieved a BRC “AA” Rating at the Sausage & Cooked Meat Facility covering both High & Low Care environments. Show less
-
-
-
G4S
-
United Kingdom
-
Security and Investigations
-
700 & Above Employee
-
Centre Manager
-
Apr 2016 - Aug 2017
G4S Cash Solutions is the UK's leading provider of integrated cash management solutions. In addition to the provision of secure transportation and storage of cash and valuables across the country, the business also acts as the outsource partner for a number of major banks including Lloyds, Santander and the Clydesdale Bank. As Centre Manager, I was responsible for the successful delivery of all contractual SLA’s and the annual budget across the Glasgow operation. Key accountabilities included: • Full Cost Centre Management in the setting, maintaining and monitoring of the cash centre budget. • Ensure full compliance of all security & Health & Safety procedures within the centre. • To manage and forecast the processing operations of the cash centre for current and future demands. • Meet and exceed customer’s contractual Service Level Agreements. • Account management and key point of contact for the Clydesdale outsource contract. • Maximising business performance through the staff engagement, operational efficiencies and CapEx delivery. • Ensuring zero waste and losses throughout the operation for both customers and the G4S business. Show less
-
-
-
Scottish Enterprise
-
United Kingdom
-
Government Relations Services
-
700 & Above Employee
-
Manufacturing Practitioner
-
Jun 2012 - Apr 2016
Working within the Scottish Manufacturing Advisory Service (SMAS), I specialise in providing manufacturing firms of all sizes across the West of Scotland with expert advice, one-to-one support, training and project management on their continuous improvement journey to delivery increased efficiencies and company growth Working within the Scottish Manufacturing Advisory Service (SMAS), I specialise in providing manufacturing firms of all sizes across the West of Scotland with expert advice, one-to-one support, training and project management on their continuous improvement journey to delivery increased efficiencies and company growth
-
-
-
-
Performance Delivery Manager
-
Jun 2007 - Jun 2012
Responsible for the complete management of a £20 million business account. Key accountabilities include: - • Operational Management across the business unit of 150 Repair Technicians, 5 Contact Centre Advisors and an associated management team across operational sites in the UK. • Account Management for the business unit, providing the key interface between the various clients and Regenersis across a variety of management levels. • Maximising business efficiencies through the application of Kaizen Continuous Improvement techniques. • Ensuring that the business provides the best possible Customer Experience to both the client and the end user predominantly through the philosophy of Right First Time. Show less
-
-
-
Premier Foods
-
France
-
Food and Beverage Manufacturing
-
Manufacturing Manager
-
Oct 2005 - May 2007
Manufacturing Manager Responsible for the effective management of the production function across the site. Key accountabilities include: • Budgetary control, through the effective management of labour, raw materials and performance. • The Utilisation of ‘Lean Manufacturing’ techniques to ensure the effective Supply Chain Management of the site, delivering fresh bread across the country within a 12 hour timescale from customer order to delivery. • Delivery of the site Key Performance Indicators including Accident Rate, Customer Complaints, Conformance to Plan. • Implementation of OEE task teams, to drive process and throughput improvements on each of the plants. Show less
-
-
-
United Biscuits
-
United Kingdom
-
Food Production
-
700 & Above Employee
-
-
Aug 2003 - Oct 2005
Responsible for the receipt and supply of £22 million of ingredients across the factory. Managing a total of 25 operators and supervisors across all 3 shifts. Key accountabilities included:• Full responsibility and management of a £750,000 Cost-Centre.• Effective Management of all Ingredient Control Systems across the site utilising SAP and other MRP tools to ensure the effective supply of ingredients to the production lines.• Full adherence to all legislative requirements in accordance to BRC and FSC standards for ingredient control. Show less
-
-
-
Jan 2002 - Jul 2003
During my time in this role, I managed 2 separate production lines producing cake bars, flapjacks and muffins. Working on a rotational shift basis and managing a team of up to 40 employees key accountabilities included:• Day to day management of a production line ensuring the plant was scheduled effectively and delivered agreed quality standards.• The management of various employee relation issues including health & safety, absence reviews, disciplinary meetings, payroll issues, recruitment and both team and individual development. Show less
-
-
-
Sep 2000 - Dec 2001
Joining United Biscuits through the Operations Graduate Scheme, I spent the first 2 years working at both the Glasgow Bakery and the company's Head Office at Hayes Park, London.During this time I completed 3 key projects.Cost Based Release Project - Working within the Flexible Packaging department of the Procurement Team, I was challenged with delivering £15 million of savings across the businessWaste Management Review - Working with SugaRich, a waste processing company supporting the site. I designed and installed an automated waste management system. This provided the site with accurate real time information on the waste produced on each line.SAP Site Installation - Working in part of a company-wide project, installing SAP across the business I was a key member of the Tollcross installation team. I designed and implemented the site controls, which would deliver the data required for SAP production recording on a daily basis. Show less
-
-
Education
-
Strathclyde University
MEng DiplMan, Manufacturing Sciences and Engineering with a Diploma in Management for Engineers -
Gryffe High School
Community
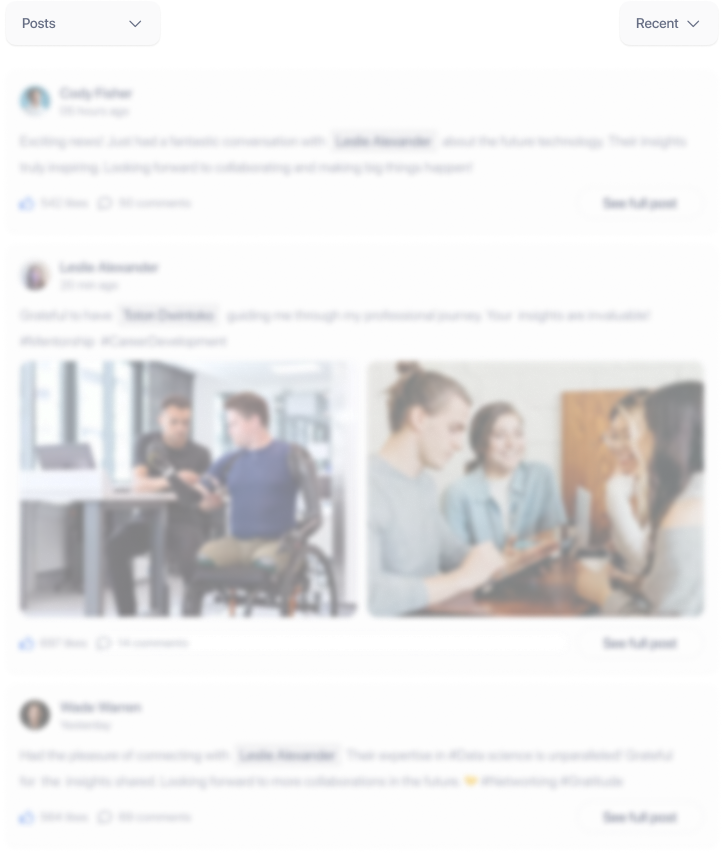