James Mitchum
Sr Cost Accounting Manager at AES Clean Technology- Claim this Profile
Click to upgrade to our gold package
for the full feature experience.
Topline Score
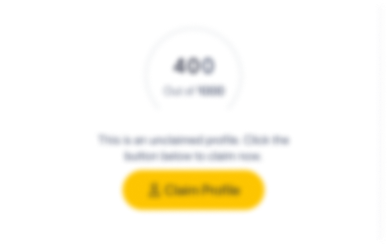
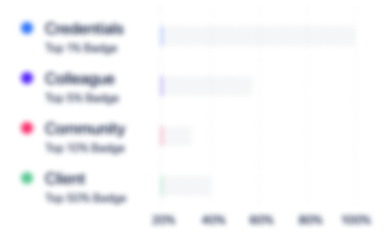
Bio


Experience
-
AES Clean Technology
-
United States
-
Construction
-
100 - 200 Employee
-
Sr Cost Accounting Manager
-
Apr 2019 - Present
• Financial responsibility for all areas of operations financial activities and provided value-added analysis and strategic support to all areas of the company. • Collaborated with management to implement and maintain effective financial and operating metrics, controls, analytics and reports with which to manage the business, drive insight into the key value levers of the business, and enable revenue and profit growth. • Lead the finance team in creating financial analysis to support and test key business decisions; prepare all necessary financial reports (profitability by project, job project budget vs actual performance and estimates used in budget models; presented findings and made recommendations to management and tracked financial results to aid in the decision-making process across the organization. • Identified and validated opportunities to improve operating performance, financial controls, safeguarding assets, attention directing, while understanding the revenue, cost, and profit implications of their decisions. • Developed and maintained a variety of metrics/KPIs and dashboards to ensure the optimal operation of the business. • Identified cost / profitability related issues and opportunities, and the means to leverage or address them. • Supervised the (4) Plant Accountants in all their financial related responsibilities including: the accuracy of the standard costs starting with the bill of materials and item costs, physical inventories, cost / productivity reporting, labor routings, labor rates, labor expense, as well as overhead assignments. • Created manufacturing standards and variances so that Operations Leadership can understand and takes corrective action. • Designed and implemented effective company financial controls, cost measurements / analysis / systems, inventory accuracy, attention directing and accurate business metrics that lead to quality / timely business decisions. Show less
-
-
-
North American Stamping Group
-
United States
-
Motor Vehicle Manufacturing
-
200 - 300 Employee
-
Commercial and Corporate Product Finance Manager
-
Sep 2014 - Apr 2019
• Produced and maintained commercial pricing for periodic updates and engineering changes for current business clients. • Created plans for business growth and developed pricing structures. • Negotiated contracts and claim disputes with clients and suppliers. • Provided corporate level support in capacity planning, budgeting, strategic planning, and cost reduction projects. • Monitored periodic reporting for 7 plants to support accuracy in Financial Reporting and verified changes in price/cost. • Developed and Managed corporate standard cost modeling / quoting standards and pricing models. • Performed variance analysis of labor, yields, usage, and overhead expenses. • Provides direction and support to Plant Cost Accountants for inventory evaluations and cycle counts. • Ensured BOMs/Product routers accurately reflect and measure manufacturing requirements. • Partnered with Sales, Production, Finance, and IT to provide direction and continuous improvement in development and application of quoting rates, product cost methods, and productivity feedback loops. • Lead initiatives for system improvements to streamline process involving product quoting, standards setting, inventory valuations, and management feedback and control systems. • Managed five direct reports Inside Sales Administrators. • Reported to CFO. Show less
-
-
-
Volkswagen of America, Inc
-
United States
-
Motor Vehicle Manufacturing
-
700 & Above Employee
-
Exterior Buying Specialist
-
Jun 2012 - Sep 2014
•Responsible for obtaining & evaluating supplier quotes, preparing sourcing proposals, and making sourcing presentations in sourcing committee.•Negotiates annual price reduction targets set forth by upper management.•Prepares and leads price negotiations for inquiries and quotations while observing timing, quality, and service-related objectives.•Develop and maintain an annual business plan consisting of 4% cost reductions annually. •Interfaces with engineering for development of parts from concept to production. Show less
-
-
Manufacturing Cost Controller
-
May 2010 - Jun 2012
•Analyzed overhead cost, launch cost, salary & benefits cost for Logistics, Quality, Tooling, and Purchasing departments.•Coordinated and prepared budgets for assigned areas as well as developed Bottom up Budgets. •Participated in capital budgeting projects (make-or-buy calculations).•Prepared reports (budgeted vs. actual performance) for management. •Analyzed processes and cost to identify potential for improvements and make recommendations for optimization and savings.
-
-
-
Bosch USA
-
United States
-
Software Development
-
700 & Above Employee
-
Sr Cost Analyst
-
Nov 2002 - May 2010
•Produced product costs for Corner Modules Assemblies, Hub Rotor Bearing Assemblies, Rotors, Calipers, and Drums for a Tier 1 Automotive Parts Manufacturer. •Supported the new product development teams by evaluating financial feasibility of new products and capital expenditures related to new product launch and production. •Maintained and enhanced financial decision making models used to evaluate investment opportunities, pricing exceptions, and product financial performance from concept to production. •Performed process analysis/audit to compare quoted to actual cost. •Active Participant on cost reductions teams. Evaluated VA/VE. •Provided NPV, IRR, and PBP for Project/Capital Expenditure Approvals. •Presented Monthly Report Outs on production cost variances (budgeted vs. actual performance) to Plant Leadership Show less
-
-
-
AEMP/ALCOA/ALUMAX Corporation
-
Jackson, Tennessee Area
-
Group Leader Cost Engineering
-
Mar 1998 - Nov 2002
•Responsible for time studies, developing standard and target throughput rates, feasibility studies, and cost related to product. •Also developed quotations for aluminum injection molded semi-solid forging parts for the tier 2 automotive industry. •Developed piece price by analyzing raw materials and costing out process cost per unit, identifying and developing total labor cost (variable and fixed overhead). •Used Net Prophet II activity based model program, Excel, and Access Data Base. Show less
-
-
-
Dana Incorporated
-
United States
-
Motor Vehicle Manufacturing
-
700 & Above Employee
-
Senior Cost Engineer
-
Mar 1996 - Mar 1998
•Responsible for all cost estimating activities for the manufacture of automotive and small engine extruded rubber products and assemblies for the Tier One, Two and OEM markets. •Performed time studies, product routing, and maintained bills of material. •Worked regularly with Kaizen teams as well as performing Kaizen audits and VA/VE studies. •Coordinated new product review meetings with cross-functional teams. •Worked with three manufacturing plants. •Used IBM AS/400 system and Excel, Word, Access. •Provided senior leadership to three cost clerks. Show less
-
-
Education
-
Murray State University
Master's degree, Business Administration and Management, General -
Tennessee State University
Bachelor's degree, Industrial Technology/Technician
Community
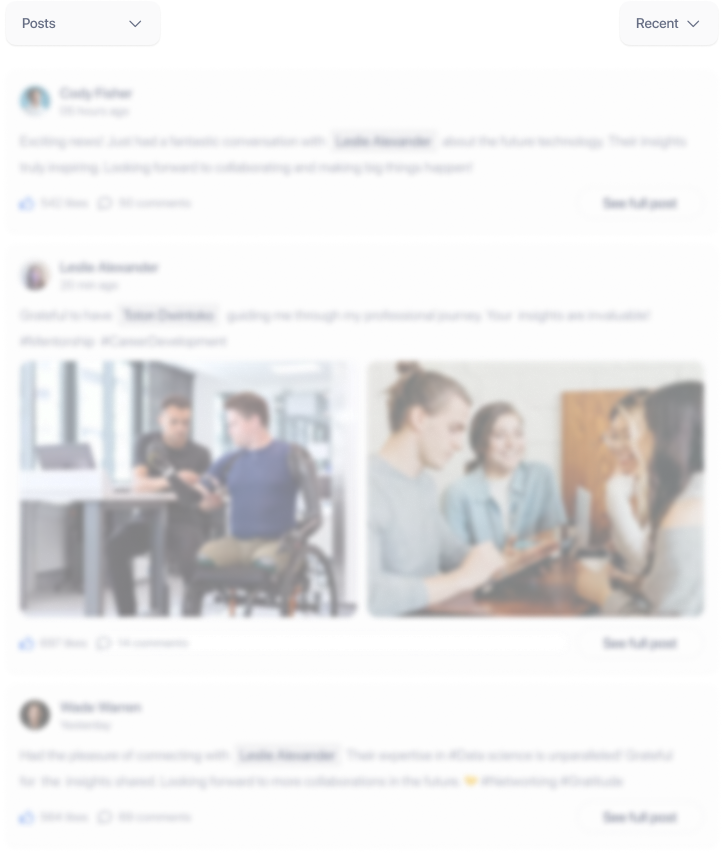