James Millington
Senior Designer at Torton Bodies Limited- Claim this Profile
Click to upgrade to our gold package
for the full feature experience.
Topline Score
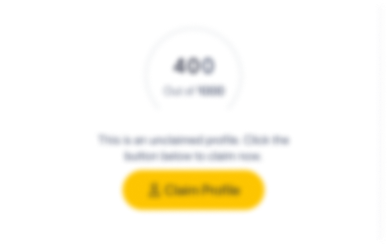
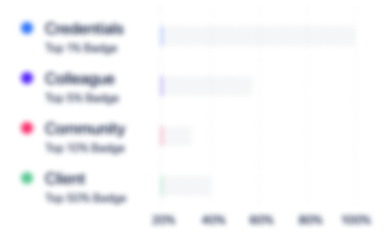
Bio


Credentials
-
APM Project Fundamentals Qualification (PFQ)
Association for Project ManagementAug, 2022- Nov, 2024 -
Project Management Foundations
LinkedInMar, 2022- Nov, 2024 -
Conflict Resolution Foundations
LinkedInFeb, 2022- Nov, 2024 -
Project Leadership
LinkedInFeb, 2022- Nov, 2024 -
Project Management for Designers
LinkedInFeb, 2022- Nov, 2024 -
Stay Lean with Kanban
LinkedInFeb, 2022- Nov, 2024 -
The Top 10 Project Management Mistakes—and How to Avoid Them
LinkedInFeb, 2022- Nov, 2024
Experience
-
Torton Bodies Limited
-
United Kingdom
-
Events Services
-
1 - 100 Employee
-
Senior Designer
-
Apr 2016 - Present
Design Department lead, client facing contact and junior engineer support. Managing the delivery of multiple concurrent new projects from concept to delivery, including design, development, feasibility, and manufacturing.In addition to concept creation, overseeing design projects to ensure they are completed to project scope, with established quality standards and time frames. At design stage - developing budgets, instigating purchasing of specialist materials, and advising on scheduling for the delivery of each phase of the project. Coordination of internal and external manufacturing to complete the project, reporting progress to management and customers. Playing a hands-on role to ensure the project is completed in the established time frame. This includes responsibility for specific design functions through each stage of the project, as well as reviewing the work of construction team and engineers, making changes to ensure the project is completed accurately. Responsible for managing and delivering all printed branding for vehicles and displays to strict timeframes and budgets.Key leader of Individual Vehicle Approval (IVA) implementation to the business, ensuring that vehicles meet all necessary requirements before testing. Conducting inspections on final product and associated documentation.
-
-
Designer
-
2007 - Apr 2016
Creating and developing mobile exhibition trailers and vehicles for a wide range of global clients and agencies, creating successful designs for over 150 bespoke manufactured vehicles. These vehicles transform to become environments and spaces including showrooms, hospitality facilities and exhibition stands. Commonly meeting with marketing departments and end users to help to produce a working solution which represents their brands corporate image. As well as producing visuals and design concept, role expands to directly project managing product from concept to completion, delivering products through manufacture to market. Working with the sales and engineering departments to ensure design intentions are met. Following construction, consulting with manufacturing staff, subcontractors and suppliers. Problem solving helps guide vehicles to being delivered on time and on budget. Working on fast moving projects means constantly reprioritising tasks, managing time between multiple design briefs and builds to ever changing deadlines. - Meeting with and liaising with clients to create design briefs- Create and develop design concepts- Produce 2D and 3D concept visuals- Managing multiple briefs- Delivering new products to market- Produce marketing materials- Design and edit artwork for printed graphics- Research materials, products and processes for production- Progress design concepts through to final manufacture- Produce working engineering drawings.- Problem solving and manufacturing supervision on manufacturing floor- Working with client’s including Jaguar, Ford, Electrolux AEG, TTI, EON, Hyundai, Autoglym, ESPN, NHS, Welsh Blood Service.
-
-
-
Boots Healthcare International
-
Pharmaceutical Manufacturing
-
200 - 300 Employee
-
Packaging Technologist
-
2005 - 2006
Working in Technical Business Improvement department, position centred around continuous improvement of packaging practices within the business, both for own brand products and for licensed multinational brands. Primary role was to support the factory and aid in its capabilities with regards to packaging. Time was split between day to day troubleshooting on the factory floor and with managing multiple long-term quality and cost saving projects. Participation in weekly meetings with different departments and project teams with the objective of improving packing processes. From these meetings projects were formed, creating objectives and subsequent actions which could be investigated and implemented. Medium term projects involved the investigation, testing and trialling either as a new product was introduced or as a result of a problem which had been identified. Upon implementation of new products or packaging processes documentation and guidelines created for manufacturing staff. - Continuous improvement of packaging practises - Managing multiple projects and briefs - Long term quality improvement using Lean processes - Development and implementation of cost saving projects and proposals - Manufacture problem solving directly on manufacturing floor and conducting product trials
-
-
Education
-
Loughborough University
BSc, Industrial Design and Technology -
The Open University
Advanced Level Leadership & Management Course, Project Management
Community
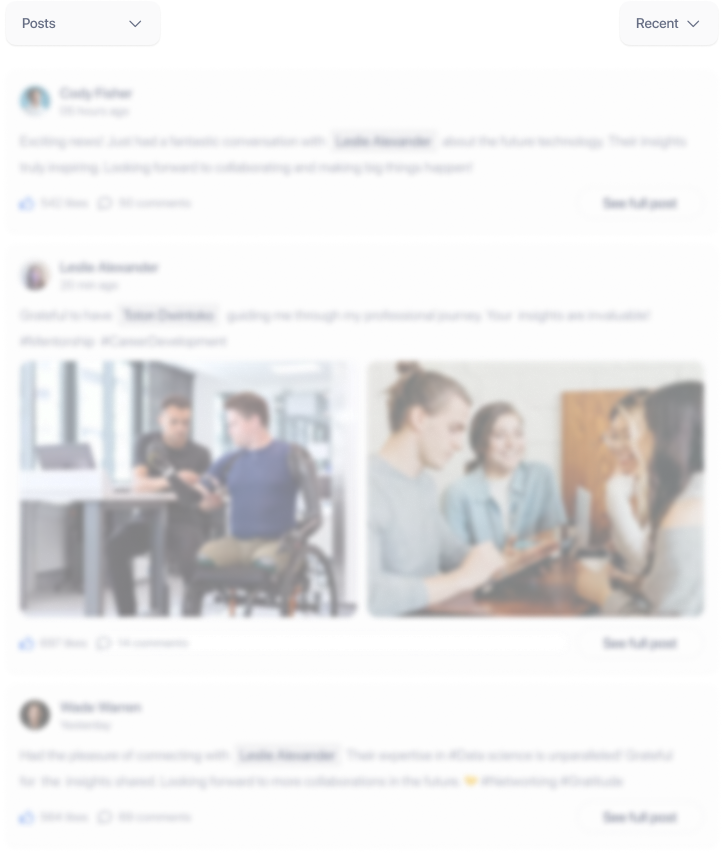