James Manderscheid
Sr. Manager of Co-Manufacturing at Kinder's Premium Quality Seasonings & Sauces- Claim this Profile
Click to upgrade to our gold package
for the full feature experience.
-
Spanish -
Topline Score
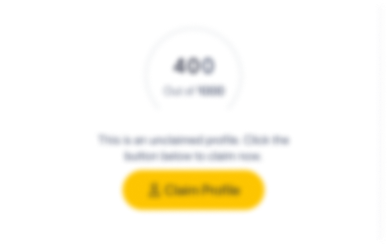
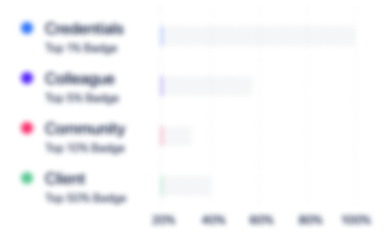
Bio


Credentials
-
BRC Certified (Food Safety, Auditing, & Compliance)
BRCGS
Experience
-
Kinder's Premium Quality Seasonings & Sauces
-
United States
-
Food and Beverage Manufacturing
-
1 - 100 Employee
-
Sr. Manager of Co-Manufacturing
-
Jul 2023 - Present
-
-
-
Primrose Candy Company
-
United States
-
Manufacturing
-
1 - 100 Employee
-
Supply Chain Manager
-
May 2022 - Jul 2023
-
-
-
Hometown Food Company
-
United States
-
Food and Beverage Services
-
1 - 100 Employee
-
Manager of Co-Manufacturing
-
Jan 2020 - May 2022
Recruited to lead relationship management and daily operations for co-manufacturing functions. Collaborate internally and externally to optimize supply chain and logistics for four (4) distribution centers across the U.S. - Facilitate logistics for all finished goods products not manufactured at a company site, coordinating daily shipping for 150+ SKUs with average total volume of 130k cases per week. - Handle partner and supplier relations while ensuring on-time delivery to meet the needs of large grocery store chains operating nationally or regionally. - Manage eight vendors while working to ensure they deliver on all contract commitments. - Lead adoption of strategies to enhance production, transportation, warehousing, and inventory management. - Analyze and utilize data to enhance capabilities, create cost savings, and achieve business objectives. - Enhance supply chain/logistics functions by increasing flexibility to respond to COVID-19 related challenges. - Created a plan for a co-manufacturer in Kansas to ship products directly to the customer, including working with IT teams to set up an EDI interface to automatically generate purchase orders for fulfillment. Turned around relationships with two co-manufacturers to achieve 98%+ fill rate by consistently communicating expectations related to production needs and KPIs. Show less
-
-
-
NEMERA
-
France
-
Medical Equipment Manufacturing
-
700 & Above Employee
-
Production Planner
-
2020 - 2020
Proved instrumental in translating customer orders into “work-in-progress” (WIP) requirements and then final assembly production plans for a medical device manufacturer of plastic injection molding. - Optimized the flow of WIP through the supply chain within the facility by verifying proper SAP transacting. - Identified future capacity constraints for both WIP and final assembly and provided recommendations to ensure the operation could smoothly meet current and future demand. Proved instrumental in translating customer orders into “work-in-progress” (WIP) requirements and then final assembly production plans for a medical device manufacturer of plastic injection molding. - Optimized the flow of WIP through the supply chain within the facility by verifying proper SAP transacting. - Identified future capacity constraints for both WIP and final assembly and provided recommendations to ensure the operation could smoothly meet current and future demand.
-
-
-
Hostess Brands
-
United States
-
Food and Beverage Services
-
400 - 500 Employee
-
Plant Production Scheduler & Corporate Finished Goods Buyer
-
2018 - 2020
Plant Production Scheduler & Corporate Finished Goods Buyer (2018-2020)Initially promoted from analyst role to serve as a finished goods buyer and then asked to simultaneously handle plant production scheduling for a plant that shipped 50,000 to 75,000 cases per week (across 100+ SKUs).- Expertly planned 50 to 60 semi-truck loads of evolving customer orders on a weekly basis.- Optimized inventory levels and production for 100+ dated SKUs to be shipped to frozen and dry warehouses.- Drove high levels of customer satisfaction by managing incidents related to damaged items during shipping.- Managed customer-specific specific buys that were atypical or required large runs of unique SKUs; partnered with clients to coordinate special purchases for seasonal programs for LTOs.- Created purchase orders ranging from $750K to $1M+ to meet changing customer demand each week.- Handled relationships with 12+ vendors to ensure KPIs were achieved and contract terms were met. Show less
-
-
Supply Chain/Logistics Analyst
-
2014 - 2018
Supply Chain/Logistics Analyst (2014-2018)Astutely leveled logistical and customer data to optimize profit margins and create savings for the client. - Analyzed data to prepare executive reports and recommendations.- Identified costly patterns and worked with customers to improve transportation planning, capturing hundreds of thousands of dollars in annual cost reductions.
-
-
-
Shafer, Kline & Warren
-
United States
-
Construction
-
1 - 100 Employee
-
Land Survey Instrument Operator
-
2013 - 2014
Entry level position as a land surveyor for major surveying organization in the Kansas City area. Provide data relevant to shape, contour, gravitation, location, elevation and dimension of land for engineering purposes. Conduct surveys to determine property boundaries. Entry level position as a land surveyor for major surveying organization in the Kansas City area. Provide data relevant to shape, contour, gravitation, location, elevation and dimension of land for engineering purposes. Conduct surveys to determine property boundaries.
-
-
Education
-
University of Kansas
Bachelor of Science (BS), Business/ Supply Chain Management -
Rockhurst High School
General, General
Community
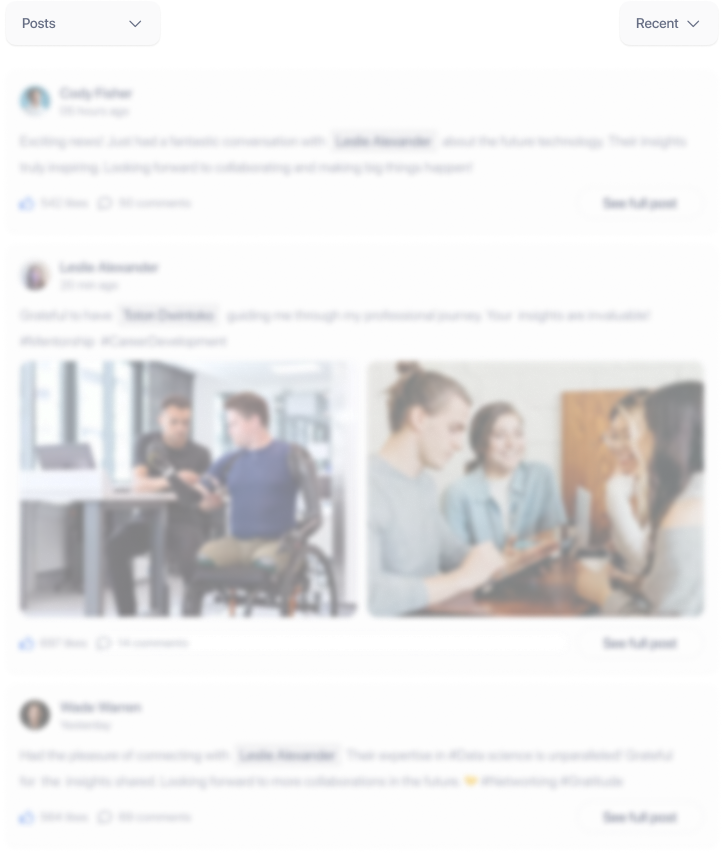