James DuCharme
Director of Procurement at Steele Solutions, Inc- Claim this Profile
Click to upgrade to our gold package
for the full feature experience.
Topline Score
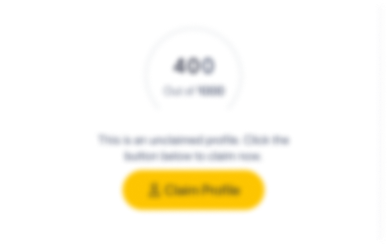
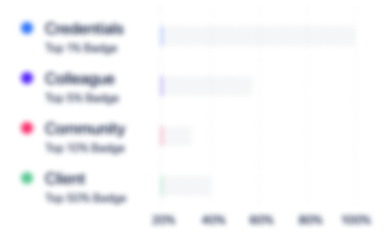
Bio


Experience
-
Steele Solutions, Inc
-
United States
-
Manufacturing
-
100 - 200 Employee
-
Director of Procurement
-
Nov 2022 - Present
Franklin, Wisconsin, United States ● Responsible for on time delivery, inventory turns, inventory accuracy, inventory obsolescence, and day-to-day procurement activities for 4 facilities ● Executed a formal bidding process for a $73M annual steel spend ● Train, supervise, evaluate, and foster personal development for 13 direct reports located in multiple locations. ● Successfully planned and executed a procurement plan for a new product line ● Implemented supply chain best practices for a newly acquired division… Show more ● Responsible for on time delivery, inventory turns, inventory accuracy, inventory obsolescence, and day-to-day procurement activities for 4 facilities ● Executed a formal bidding process for a $73M annual steel spend ● Train, supervise, evaluate, and foster personal development for 13 direct reports located in multiple locations. ● Successfully planned and executed a procurement plan for a new product line ● Implemented supply chain best practices for a newly acquired division which resulted in increased efficiency and department alignment ● Developed and delivered an onboarding plan for new employees and continuing education workshops for current employees focusing on purchasing basics, business specifics, and departmental expectations and goals ● Successfully lead new product sourcing activities focused on pricing, quality, and lead time ● Efficiently manage $20M Inventory to support production and sales targets
-
-
Senior Supply Chain Manager
-
Aug 2021 - Nov 2022
Milwaukee, Wisconsin, United States ● Led a team of 10 buyers in procurement activities for 3 manufacturing facilities and 1 warehouse ● Implemented new reporting and processes to support supply chain day-to-day activities and strategy as business increased 100% year over year ● Drove continuous improvements related to operational efficiencies, inventory best practices, and supplier relationships ● Developed, implemented, and monitored an inventory strategy and parameters for $10M of raw materials and finished goods ●… Show more ● Led a team of 10 buyers in procurement activities for 3 manufacturing facilities and 1 warehouse ● Implemented new reporting and processes to support supply chain day-to-day activities and strategy as business increased 100% year over year ● Drove continuous improvements related to operational efficiencies, inventory best practices, and supplier relationships ● Developed, implemented, and monitored an inventory strategy and parameters for $10M of raw materials and finished goods ● Built and managed new supplier relationships to support the sales growth and production ● Hired, trained, coached 5 new buyers in newly created supply chain roles
-
-
-
CNH Industrial
-
Machinery Manufacturing
-
700 & Above Employee
-
Global Inventory Manager & PMO
-
Jul 2019 - Jul 2021
Racine, Wisconsin ● Led the global implementation of an advanced planning system using agile methodology ● Drove optimization of inventory budgets globally balancing costs and service impacts ● Guided & negotiated with cross-functional and cross-regional teams ensuring governance of processes and method alignment ● Responsible for Global Inventory Management (GIM) process implementation with main target to reduce global spare parts inventory and improve dealer’s availability with continuous… Show more ● Led the global implementation of an advanced planning system using agile methodology ● Drove optimization of inventory budgets globally balancing costs and service impacts ● Guided & negotiated with cross-functional and cross-regional teams ensuring governance of processes and method alignment ● Responsible for Global Inventory Management (GIM) process implementation with main target to reduce global spare parts inventory and improve dealer’s availability with continuous collaboration among regional leaders ● Responsible for change management for the global materials management organization ● Defined global processes from sourcing to final distribution to balance inventory and service with savings of more than $100K a year ● Led monthly reviews with regional leaders to push to meet targets and program milestones
-
-
Global Inventory Analyst
-
Jan 2018 - Jul 2019
Racine, WI ● Managed and led continuous improvement projects for the global materials management process which includes 400,000+ aftermarket parts across 8 global regions. ● Optimized $433,000,000 in global inventory through implementing strategic initiatives, analyzing root causes and trends, and deploying countermeasures ● Established and drove positive results in key performance indicators and key activity indicators relating to forecasting, inventory management, and customer… Show more ● Managed and led continuous improvement projects for the global materials management process which includes 400,000+ aftermarket parts across 8 global regions. ● Optimized $433,000,000 in global inventory through implementing strategic initiatives, analyzing root causes and trends, and deploying countermeasures ● Established and drove positive results in key performance indicators and key activity indicators relating to forecasting, inventory management, and customer fill ● Facilitated, drove, and supported collaboration across 8 global material management teams ● Identified and developed solutions for the expansion of the global materials management process ● Partnered with global teams in Material Management, Customer Service, Forecasting, Operations, Purchasing, and New Product Launch ● Developed, facilitated, and evaluated global inventory management training to global colleagues ● Created and delivered monthly status meetings to global leaders
-
-
Project Manager
-
Aug 2016 - Jan 2018
Austin, Texas Area ● Developed and led cutover and conversion project plans for the Materials Requirements Planning (MRP) implementation project ● Led and executed Electronic Data Interchange (EDI) testing with 403 CNH Industrial suppliers ● Developed and performed over 400 end-to-end test cases for the MRP system implementation project ● Identified and fostered the re-development of business processes affected by the new MRP system utilizing lean thinking methodology ● Subject matter expert for the… Show more ● Developed and led cutover and conversion project plans for the Materials Requirements Planning (MRP) implementation project ● Led and executed Electronic Data Interchange (EDI) testing with 403 CNH Industrial suppliers ● Developed and performed over 400 end-to-end test cases for the MRP system implementation project ● Identified and fostered the re-development of business processes affected by the new MRP system utilizing lean thinking methodology ● Subject matter expert for the processes involved in the Global Inventory Management Project ● Led cross-cultural meetings with global partners to promote continuous improvement ● Detected, assessed risk, and resolved data element gaps for future business reporting
-
-
Materials Planning Supervisor
-
Jan 2016 - Aug 2016
Racine, WI ● Supervised, evaluated, and empowered a team of ten Supply Chain Specialists ● Built and maintained positive supplier relationships resulting in improved OTD and service level ● Established and monitored key performance metrics and reporting ● Identified and resolved inefficiencies in the planning, expediting, and forecasting processes ● Optimized team’s portion of a $450,000,000 inventory budget and $2,500,000 airfreight budget by analyzing minimum order quantities, forecasts… Show more ● Supervised, evaluated, and empowered a team of ten Supply Chain Specialists ● Built and maintained positive supplier relationships resulting in improved OTD and service level ● Established and monitored key performance metrics and reporting ● Identified and resolved inefficiencies in the planning, expediting, and forecasting processes ● Optimized team’s portion of a $450,000,000 inventory budget and $2,500,000 airfreight budget by analyzing minimum order quantities, forecasts, demand, and market projections ● Collaborated with Operations, Forecasting, Marketing, Logistics, Quality, global partners, and suppliers ● Led the design and testing meetings for the new MRP system and the new warehouse inventory system ● Initiated and led a global resource initiative to eliminate waste in logistics and handling costs ● Motivated and supported direct reports’ career growth by encouraging trainings and assigning projects to foster career development
-
-
Regional Inventory Specialist
-
Jul 2014 - Jan 2016
Racine, WI ● Analyzed and optimized $450 million of inventory in 10 distribution centers across North America ● Served as lead analyst on a joint marketing and materials program that increased wholesale sales ● Produced a 2.5% increase in customer fill by developing a database to run the redeployment process ● Developed a Key Performance Indicator (KPI) database to track fill rates, redeployments, and inventory levels for streamline analysis ● Developed a database using Access to maximize… Show more ● Analyzed and optimized $450 million of inventory in 10 distribution centers across North America ● Served as lead analyst on a joint marketing and materials program that increased wholesale sales ● Produced a 2.5% increase in customer fill by developing a database to run the redeployment process ● Developed a Key Performance Indicator (KPI) database to track fill rates, redeployments, and inventory levels for streamline analysis ● Developed a database using Access to maximize efficiency for the joint marketing and materials program ● Analyzed, established, and monitored parameters for fair share and redeployment processes ● Collected and leveraged large amounts of data to drive continuous improvement
-
-
Supply Chain Specialist
-
Mar 2013 - Jul 2014
Racine, WI ● Analyzed and monitored inventory levels of over 9,000 active part numbers to meet the needs of customers ● Ordered and expedited purchase orders based on fluctuations of forecast and demand ● Analyzed data elements which uncovered global inefficiencies and lead the global collaboration to improve the supply chain ● Led the collaboration with global partners that produced a 99.7% reduction in processing time in the purchase order reconciliation process ● Developed a database… Show more ● Analyzed and monitored inventory levels of over 9,000 active part numbers to meet the needs of customers ● Ordered and expedited purchase orders based on fluctuations of forecast and demand ● Analyzed data elements which uncovered global inefficiencies and lead the global collaboration to improve the supply chain ● Led the collaboration with global partners that produced a 99.7% reduction in processing time in the purchase order reconciliation process ● Developed a database using Access to increase the efficiency of ordering mass purchase orders ● Addressed and successfully resolved delivery issues with suppliers on a daily basis
-
-
-
Rockwell Automation
-
United States
-
Automation Machinery Manufacturing
-
700 & Above Employee
-
Manufactured Parts Buyer
-
Nov 2012 - Mar 2013
Milwaukee, WI • Surpassed supplier 97% on-time delivery goal utilizing SAP to evaluate and manage supplier performance • Collaborated with Sourcing, Supplier Development, Product Development, Materials, and Logistics • Developed positive business relationships with suppliers by leading weekly conference meetings • Worked with the Product Development Department to develop the procurement process of new parts • Resolved supplier conflicts to ensure on-time delivery of customer purchase orders
-
-
Production Control Analyst
-
May 2012 - Nov 2012
Richland Center, WI • Led and directed 8 team members in a physical inventory warehouse audit • Analyzed and managed inventory levels for production using SAP • Ordered and expedited purchase orders with suppliers • Collaborated with Suppliers and Quality to disposition and rework defective material • Problem solved inventory surpluses and executed disposition
-
-
-
University of Wisconsin-Platteville
-
United States
-
Higher Education
-
700 & Above Employee
-
Student Manager
-
Mar 2009 - Apr 2012
•Supervised and trained 30 student employees •Communicated effectively with colleagues, supervisees, management, and customers •Problem solved and resolved daily issues regarding scheduling, customer satisfaction, and supervisee errors •Facilitated new regulations and procedures by creating supervisee buy-in •Proposed ideas and lead changes to increase department efficiently
-
-
-
CNH Industrial
-
Machinery Manufacturing
-
700 & Above Employee
-
Parts and Services Supply Chain Intern
-
May 2011 - Sep 2011
•Resolved inventory shortages and surpluses in 10 distribution centers by utilizing redeployments •Analyzed forecast errors and identified improvement opportunities •Managed inventory variances and submitted inventory scrap requests •Developed spreadsheet to track inventory cost, quantity, and forecasts for North America •Evaluated part displacements in the closing of a distribution center •Co-supervised 15 Inbound Material Handlers in daily operations
-
-
Education
-
West Texas A&M University
Master of Business Administration (MBA), General Studies -
University of Wisconsin-Platteville
Bachelor of Science (BS), Business Administration, Supply Chain Management
Community
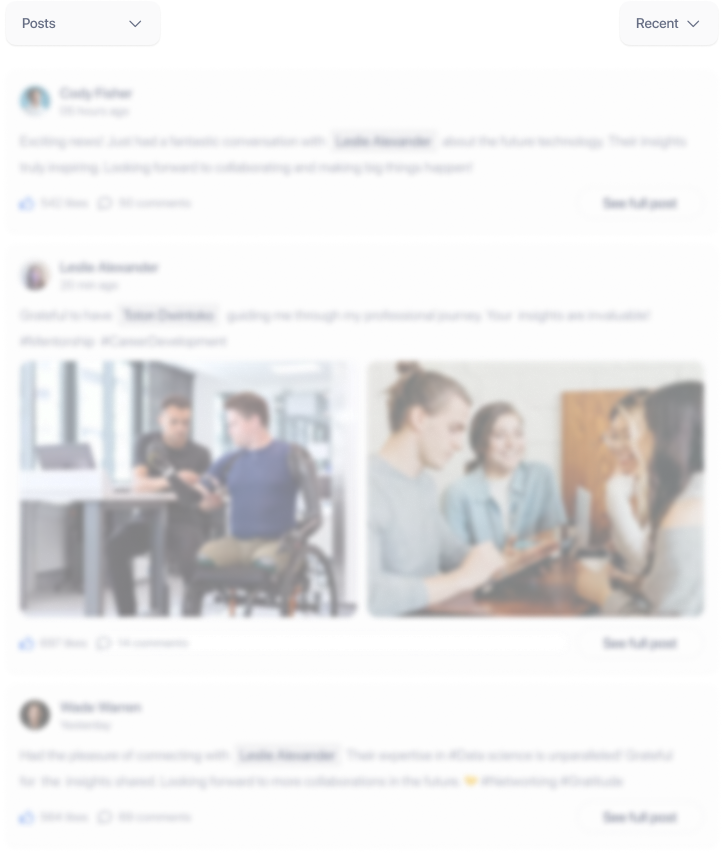