James Lancaster
Design Engineer at BRUKS Siwertell Americas- Claim this Profile
Click to upgrade to our gold package
for the full feature experience.
Topline Score
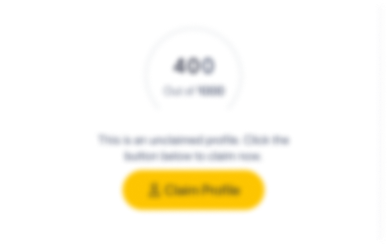
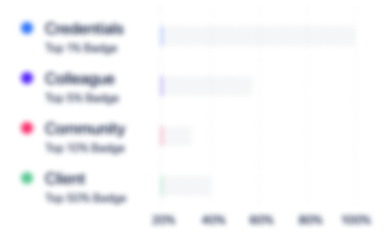
Bio


Experience
-
Bruks Siwertell Americas
-
United States
-
Machinery Manufacturing
-
1 - 100 Employee
-
Design Engineer
-
Jul 2019 - Present
-
-
-
-
Design Engineer and Estimator
-
Apr 2014 - Jul 2019
Created general arrangements and shop fabrication detail drawings for bulk handling equipment. Generated calculations for the required volume, horsepower, shaft size, reducer gear size, and proper material selections per application. Produced material requests for project specific quotes on all major components, such as chain, belt, buckets, bearings, sprockets, pulleys, reducers, and other instrumentation. Developed deeper understanding of CEMA standards and worked with a variety of vendors including Rexnord/Falk, SEW, Dodge, Jeffrey, and Webster. Performed regular fabrication shop visits to inspect progress and traveled with equipment to jobsite for installation. Traveled to Veolia Environmental Service in Port Arthur, TX to provide onsite technical assistance and verify dimensional accuracy of installed components for a 135 foot, 20 degree, 48 inch wide apron pan conveyor. While onsite, inspected various other pieces of equipment and documented conditions and points of improvements. Worked with a 3rd party corrosion specialty company and Veolia plant supervisors to re-design and increase the longevity of a central piece of plant equipment titled the Deslagger. The previous design construction was mild steel with AR400 wear plates and chain which was changed to 2205 duplex stainless steel and 17-4PH chain and sprockets. These changes and many others increased the life of the equipment from 6 months to 2 years. November of 2017, was promoted to a design engineer and estimator. Classified the working loads of each chain and determined chain cross references between manufacturers to lower costs. After learning to design chain drives and shaft mounts, also used similar drive arrangements between manufacturers to lower overall project costs. In 2018, of the 37 projects we quoted, we were able to win 8 of them for a total of $1,276,920 in new contracts.
-
-
-
Blastec Inc.
-
United States
-
Machinery Manufacturing
-
1 - 100 Employee
-
Field Engineer
-
Jun 2012 - Mar 2014
Devised an installation sequence and schedule for a manual air-blast system detailing part locations, orientations, and measurements using 3D modeling pictures and manufacturing drawing callouts. Traveled to Caterpillar Work Tools in Waco, TX and worked directly with local mechanical and electrical contractors to complete the job in six weeks. Supervised the installation of a structural bridge frame de-scaling system for Hirschfield Industries in Colfax, NC. Coordinated the installation of a roller conveyor de-scaling system for The Gateway Company in Joliet, IL. Balanced the schedule to avoid conflicts between union mechanical contractors and non-union electrical contractors. Completed the job in four weeks and saved Blastec $15,000 in labor costs. Traveled to Lucedale, MS to install a plate and structural finishing system (preservation line) for American Tank and Vessel. Working directly with AT&V’s in house mechanics and electricians, the $1.5 million dollar job was completed in nine weeks and show cased to CEO’s and executives of Chevron, BP and Exxon Mobil. Also have done various works for Buckner Barrel in Springville, AL, Lochinvar Corp. in Lebanon, TN, and Trinity Heads in Navasota, TX. Using 3D Inventor models, created manufacturing drawings in AutoCAD with dimensions and welding symbols. Also, using Excel created the corresponding bill of material to order the parts required.
-
-
-
Lehigh Technologies
-
United States
-
Chemical Manufacturing
-
1 - 100 Employee
-
Process Engineer
-
Oct 2011 - Dec 2011
Completed the engineering, procurement and construction of two systems titled Real Time Reclaim (RTR) and Real Time Sampling (RTS). Using venturis, created a low cost solution to a high cost production downtime problem. Realizing another opportunity to utilize the venturi also designed an in-line rubber sampling device that monitored quality control more effectively. Saving the company about $63,000 per year obtained a specific understanding of the rubber grinding process and the equipment used to execute this task: bucket elevators, cryogenic screw conveyors, mills, aero mechanicals, screeners, vacuum sweeps, bag houses, airlocks, dust collectors and silo receivers.
-
-
-
Amec Foster Wheeler
-
United Kingdom
-
Oil and Gas
-
700 & Above Employee
-
Intern
-
May 2007 - Aug 2008
Completed two Mechanical Engineering internships, worked with lead engineers in designing, drawing and purchasing of a boiler in a Waste-to-Energy plant. Worked in AutoCAD examining PID’s directly with senior engineers to size, modify and improve performances within the plant. Installed complete boilers with deaerator, absorber, fabric filters, SCR and also expanded the tipping hall and improved the ash handling conveyor facilities. Obtained a general understanding of the engineering process by learning how the different engineering disciplines interact, working with vendors, following construction codes and use of safety factors in design.
-
-
Education
-
Georgia Institute of Technology
Bachelor of Science (BS), Mechanical Engineering -
Lassiter High School
Mechanical Engineering
Community
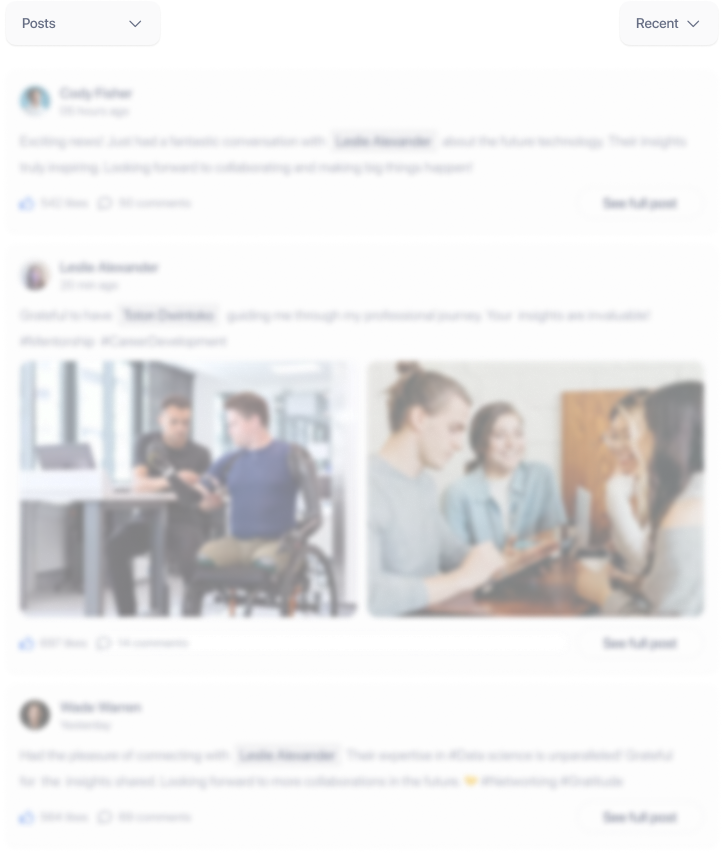