James Hammond III
Project Manager at Global Heat Transfer (GHT)- Claim this Profile
Click to upgrade to our gold package
for the full feature experience.
Topline Score
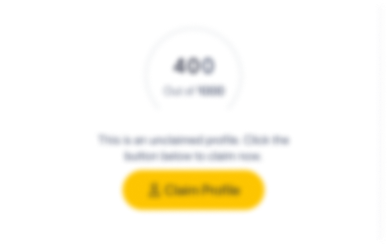
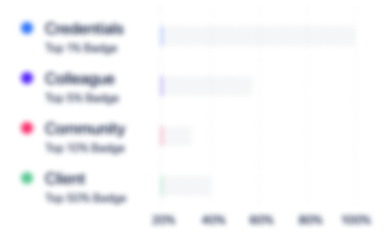
Bio

Robert Dean II
In all the projects I worked with James on he was always very through, consistent and kept the scope on track. James always puts safety and quality as a must in all projects and efficient at reducing waste in projects. James will be a great contributor to his new teams!

Dan Godbout
James is an exceptionally skilled individual with a high degree of experience in drafting, engineering, manufacturing, costing, product management and customer care. Having worked with James, I would recommend him to any employer.

Robert Dean II
In all the projects I worked with James on he was always very through, consistent and kept the scope on track. James always puts safety and quality as a must in all projects and efficient at reducing waste in projects. James will be a great contributor to his new teams!

Dan Godbout
James is an exceptionally skilled individual with a high degree of experience in drafting, engineering, manufacturing, costing, product management and customer care. Having worked with James, I would recommend him to any employer.

Robert Dean II
In all the projects I worked with James on he was always very through, consistent and kept the scope on track. James always puts safety and quality as a must in all projects and efficient at reducing waste in projects. James will be a great contributor to his new teams!

Dan Godbout
James is an exceptionally skilled individual with a high degree of experience in drafting, engineering, manufacturing, costing, product management and customer care. Having worked with James, I would recommend him to any employer.

Robert Dean II
In all the projects I worked with James on he was always very through, consistent and kept the scope on track. James always puts safety and quality as a must in all projects and efficient at reducing waste in projects. James will be a great contributor to his new teams!

Dan Godbout
James is an exceptionally skilled individual with a high degree of experience in drafting, engineering, manufacturing, costing, product management and customer care. Having worked with James, I would recommend him to any employer.

Credentials
-
Project Management Practices and Methodologies
Capella UniversityJan, 2021- Nov, 2024 -
Lean Foundations
Acuity InstituteSep, 2018- Nov, 2024
Experience
-
Global Heat Transfer (GHT)
-
United States
-
Oil and Gas
-
1 - 100 Employee
-
Project Manager
-
Jan 2022 - Present
Interfaced with customers to determine project scope: equipment, environment, thermal, and deadlines. • Managed power generation and gas/oil/water cooler projects from beginning to completion. • Compiled technical quotes, verified inventory, and managed purchase orders. • Conducted thermal analysis for all new cooler and radiator requests. • Performed airflow/static pressure simulations for fans and motors on all cooler/radiator units. • Coordinated with customers, engineering, procurement, manufacturing, and shipping to ensure all customer orders are on time, correct, and complete.
-
-
Project Manager
-
May 2021 - Jan 2022
-
-
-
Lone Star College
-
United States
-
Higher Education
-
700 & Above Employee
-
Adjunct DFTG Cypress
-
Aug 2015 - Present
• Teaches Computer-Aided Design Technologies such as AutoCAD, Inventor, and Technical Drafting at all three levels Beginner, Intermediate, and Advance • Creates engaging lessons that promote student involvement and application of the material. • Utilizes a course syllabus for each course following established institutional guidelines. • Meets with and advises students either before or after class, or electronic communication. • Evaluates students to measure their progress in achieving course objectives and informs students promptly of their progress.
-
-
-
Global Heat Transfer (GHT)
-
United States
-
Oil and Gas
-
1 - 100 Employee
-
Product Manager (Sales III)
-
Dec 2019 - Apr 2020
• Interfaced with customers to determine project scope: equipment, environment, thermal, and deadlines. • Managed power generation and gas/oil/water cooler projects from beginning to completion. • Compiled technical quotes, verified inventory, and managed purchase orders. • Conducted thermal analysis for all new cooler and radiator requests. • Performed airflow/static pressure simulations for fans and motors on all cooler/radiator units. • Executed field tests on new products; provided field service support on new equipment. • Coordinated with customers, engineering, procurement, manufacturing, and shipping to ensure all customer orders are on time, correct, and complete.
-
-
Manufacturing Engineer III / Safety Champion
-
Feb 2018 - Dec 2019
• Decreased safety incidents by 40% • Conducted incident investigations • Trained employees on numerous safety aspects. • Develop and implement a new safety procedure for new processes and equipment. • Red Line drawings for improved manufacturing drawings. • Resolve problems that arise during development. • Set up and Utilized a testing area for Hydrostatic testing of coolers according to ASME. • Quality Control of new production and service equipment down to 1% of products. • Writes Standards, Work Instructions, and Operating Procedures. • Implementation of Lean Manufacturing. • Engineering Liaison with the main Engineering Department in Canada.• Pressure Washer and Truck Wash Engineer dealing with wastewater. • Implemented the Safety Observation Card to create an environment where team members feel free to speak and know that their concerns will be addressed. • Provide training and support to manufacturing personnel. • Create and maintain production routes for material moving through the factory. • Utilized Root Cause and Corrective Action activities.
-
-
-
Baker Hughes
-
United States
-
Oil and Gas
-
700 & Above Employee
-
Eng Technologist II
-
Oct 2013 - Sep 2017
• Subject Matter Expert for Hydraulics, Chassis, and Powertrain for oil and gas equipment. • Managed the Technical Support Portal (TPS) to improve worldwide communications. • Managed the Quality Notifications system for Engineering Pressure Pumping from the supply chain, warehouse, and outside companies. • Rolled out the Technical Support Portal to Baker Hughes Pressure Pumping in the United States and Internationally. • Created Engineering bulletins addressing performance and safety concerns on Pressure Pumping Equipment. • Created 2D assembly and detail drawings • Created 3D modeling of parts and assembly, ultimately remedying safety issues and giving clarity to manufacturers regarding production. • Trained the Engineering department on how to respond to the Technical Support Portal requests, ensuring the successful execution of all responses and improved communication between engineers and those working in the field. • Lead in the data collection and documented results from districts on numerous improvement testing. • Redesigned the tools used for maintenance of the Pacemaker pump to make them safer to use. • Utilize 3D printing to create prototypes. • Trained Quality Assurance personnel in the understanding and execution of inspecting company drawings.
-
-
RDD Design Drafter
-
Sep 2010 - Oct 2013
• Assisted with powertrain components, chassis specifications, and hydraulic schematics & designs. • Created 2D assembly and detail drawings (AutoCAD and NX) • Created 3D models (Inventor and NX). • Provided technical support for manufacturing and worldwide districts. • Created drawings and 3D models to resolve the issue of water getting into the hydraulic system on pressure pumping equipment. • Assisted with the investigation into the stimulation equipment’s transmissions to prematurely fail, resulting in less downtime on the job and increased life of the transmission. • Streamed line hydraulics hoses and all filters to one manufacture, resulting in better pricing and lower inventory counts.
-
-
Production Control Coordinator - Manufacturing
-
Feb 2006 - Sep 2010
• Communicated with the Engineering department. • Trained new employees to the Production Control Department. • Created manufacturing Bills of Material (BOM) • Researched weekly shortage/staff-hour reports.• Implemented Material Requirements Planning (MRP) into manufacturing, resulting in better inventory control and just in time parts. • Coordinated with external vendors and purchasing department for delivery of parts and equipment, ensuring equipment got built promptly and within budget. • Inspected outside equipment for Quality Assurance. • Created the drawings and bill of materials for capillary skids, helping to bring new equipment line to the company. • Created a manufacturing routing system to better track hours.
-
-
-
US Army
-
United States
-
Armed Forces
-
700 & Above Employee
-
25U - Signal Support Systems Specialist
-
Jan 2004 - Nov 2005
• Responsible for the set-up, operation, and maintenance of communication equipment for the S3 shop at headquarters. • Responsible for the set-up, operation, and maintenance of communication equipment for the S3 shop at headquarters.
-
-
-
Baker Hughes
-
United States
-
Oil and Gas
-
700 & Above Employee
-
Parts Clerk
-
Mar 2001 - Sep 2003
• Responsible for inventory control for all inventory at the district level. • Created work orders based on truck reports. • Issued parts to mechanics and logged the part in the JD Edwards database system. • Worked directly with outside vendors to procure stock items and to increase inventory levels. • Processed accounts receivable by coding invoices for payment. • Responsible for inventory control for all inventory at the district level. • Created work orders based on truck reports. • Issued parts to mechanics and logged the part in the JD Edwards database system. • Worked directly with outside vendors to procure stock items and to increase inventory levels. • Processed accounts receivable by coding invoices for payment.
-
-
Education
-
Capella University
Bachelor of Science - BS, Business Administration -
Lone Star College
Associate of Applied Science, Mechanical Engineering Technology -
University of Houston
Bachelor of Science - BS, Mechancal Engineering Technology -
Baker Hughes
Lean Six Sigma - Yellow Belt
Community
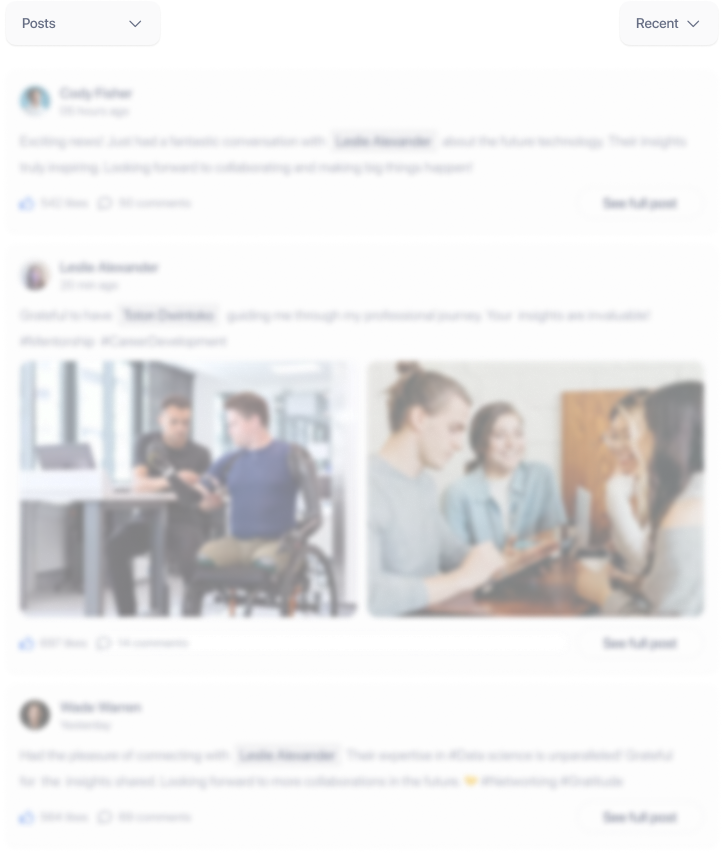