James Drury IEng MSOE MIPlantE
Project Engineer at T&RS Engineering Ltd- Claim this Profile
Click to upgrade to our gold package
for the full feature experience.
Topline Score
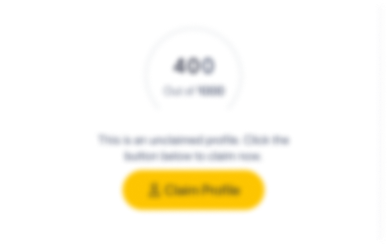
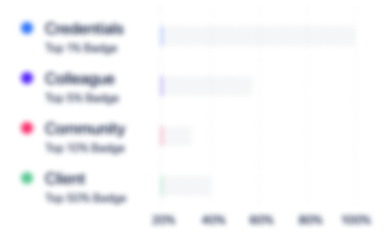
Bio


Experience
-
T&RS Engineering
-
United Kingdom
-
Engineering Services
-
1 - 100 Employee
-
Project Engineer
-
Aug 2017 - Present
-
-
-
Advanex Europe Ltd
-
United Kingdom
-
Industrial Machinery Manufacturing
-
1 - 100 Employee
-
Quality System Engineer
-
Apr 2016 - Aug 2017
-
-
Production Engineer
-
Dec 2013 - Apr 2016
Setup maintenance regime and wrote all the required SOPs (Standard Operating Procedures) for the ISO 14644 class 7 clean room at the Billborough site.Performed a review of SOPs (Standard Operating Procedures) for all production tasks carried out on the Southwell Site, including pharmaceutical and aerospace, updated and wrote new ones to enable more efficient and consistent working by production staff.Implemented and managed a new change control procedure to enable changes to be assessed, managed and implemented in a controlled way ensuring and were appropriate, relevant customers are informed. Show less
-
-
-
Hoval United Kingdom
-
United Kingdom
-
Renewable Energy Semiconductor Manufacturing
-
1 - 100 Employee
-
Technical Support Engineer
-
Jan 2013 - Aug 2013
Supported professional consultants and individual customers in selecting boilers and ancillary components. Assisted boiler engineers, both internal and external to diagnose faults and recommended solutions to rectify the faults. Complied illustrated list of parts for both the TopGas and UltraGas range of boilers to assist part identification for boiler engineers and the internal spare parts department. Compiled and submitted relevant information to successfully get the CompactGas range of boilers approved by the Carbon Trust for inclusion on the Energy Technology List. Show less
-
-
-
James Dawson
-
Lincoln, United Kingdom
-
Production Engineer
-
May 2011 - Nov 2012
Preformed first article inspections of various types rubber hoses to ISO/TS 16949. Assisted various customers with the design and specification of rubber hoses for air oil and coolant transfers. Proven track record of costing both rubber hoses and the mandrels used in their construction for use by the sales team in quoting new orders. Used customers requirement and specifications then turned them into Bills Of Materials and standard work instructions to facilitate production of rubber hoses. Show less
-
-
-
BOMBARDIER
-
Canada
-
Aviation and Aerospace Component Manufacturing
-
700 & Above Employee
-
RAMS LCC Engineer
-
Jun 2001 - Dec 2010
Analysed and reviewed life cycle supplier costs for new trains in order that the cost associated with the multi million pound London Underground contract could be managed effectively. Highlighted cost duplication of £2.7Million in projected life cycle spend between several different suppliers, to enable clarification of cost breakdowns to be reached and reductions entered into project plan. Proven track record of analysing and reviewing, cost/benefit analysis of potential variation to contract requests submitted from London Underground to ensure that any additional costs have been captured and that the customer is satisfied with responses. Worked with London Underground to agree a maintenance schedule that would offer a safe and efficient way to maintain their new trains with their existing depots and limit the amount of new equipment that would have to be purchased. Show less
-
-
-
Ericsson
-
Sweden
-
Telecommunications
-
700 & Above Employee
-
Support technician
-
Jun 2000 - Jun 2001
Contributed to the implementation and commissioning the Scunthorpe sites’ test facility in a timely manner to enable the increase in capacity to be established to the plan. Maintained mobile phone test equipment to ensure maximum production up time. Repair any faults that occurred to test equipment so as to minimise any potential loss of production. Contributed to the implementation and commissioning the Scunthorpe sites’ test facility in a timely manner to enable the increase in capacity to be established to the plan. Maintained mobile phone test equipment to ensure maximum production up time. Repair any faults that occurred to test equipment so as to minimise any potential loss of production.
-
-
Community
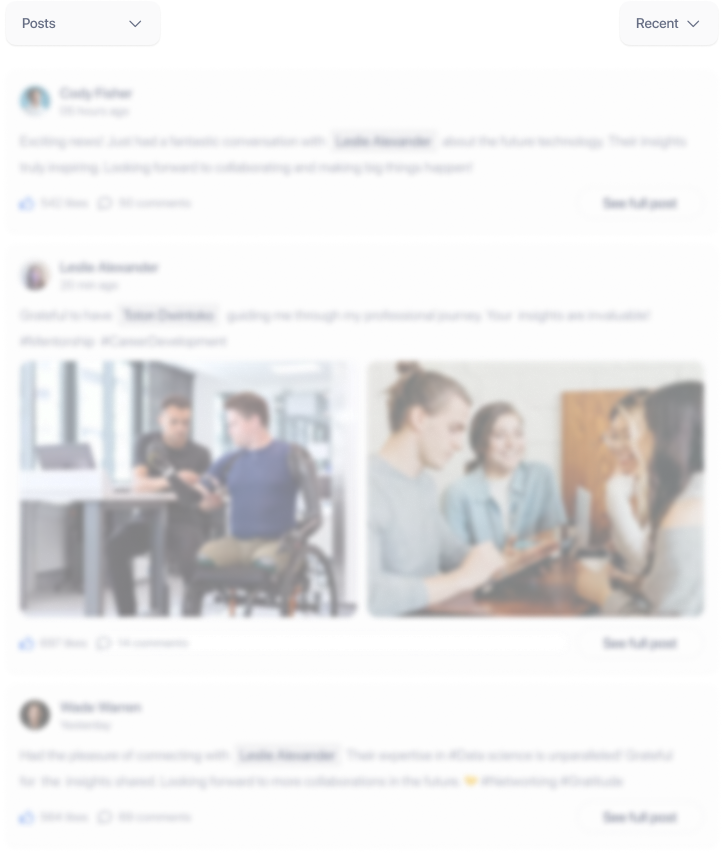