Jake Fearnhead
Stress engineer at Aerotech Design Consultants Ltd- Claim this Profile
Click to upgrade to our gold package
for the full feature experience.
Topline Score
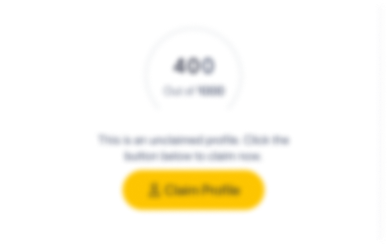
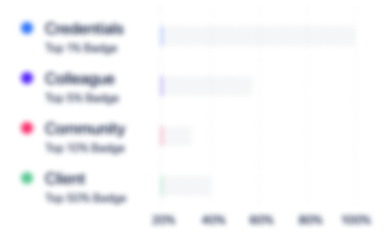
Bio


Experience
-
Aerotech Design Consultants Ltd
-
Aviation & Aerospace
-
1 - 100 Employee
-
Stress engineer
-
Aug 2010 - Present
Experience in static/fatigue stress analysis using hand calculations and FE analysis.Competence using stress analysis software including MathCAD, Patran/Nastran, ESACRACK, CATIA v5 and Microsoft Office suite.Static and fatigue analysis of primary and secondary aircraft structures including:- Check stress task for Honeywell AS907 engine thrust reverser, including FE Analysis using Patran/Nastran. Task involved metallic and composite components.- Updating Structural Repair manual for composite components of the AS907 thrust reverser. This task involved assessing composite components for surface damage, represented by removing the innermost or outermost composite ply, and re-analysing the composite, using "The Laminator" software.- Fatigue analysis of AS907 thrust reverser due to CAA (Chromic Acid Anodising) treatment. Analysis of the structure was required using reduced material allowables due to the CAA treatment. Fatigue failures of the structure were detected, some of which were resolved by improving the analysis methods and certification FEM. Those failures that could not be resolved required crack propagation analysis using ESACRACK software to determine if the crack would propagate sufficiently to exceed the fatigue life requirement of the structure.- Static and acoustic fatigue analysis of a heat shield for the AS907 thrust reverser, including FE analysis using solution type SOL 111. This task involved analysing and developing a heat shield from scratch to be retrofitted to the inner duct of the thrust reverser. As the shield was located in the path of hot exhaust gasses it was essential that acoustic/vibrational fatigue, combined with high temperatures, did not fail the structure.- Static and fatigue analysis of an undercarriage test rig for the Saab Gripen. This task involved static and fatigue analysis of all parts of the test rig from scratch and liaising with design to produce a strong but cost-effective design.
-
-
Education
-
The University of Salford
Bachelor of Engineering (BEng), Aeronautical Engineering -
Wirral Grammar School
Community
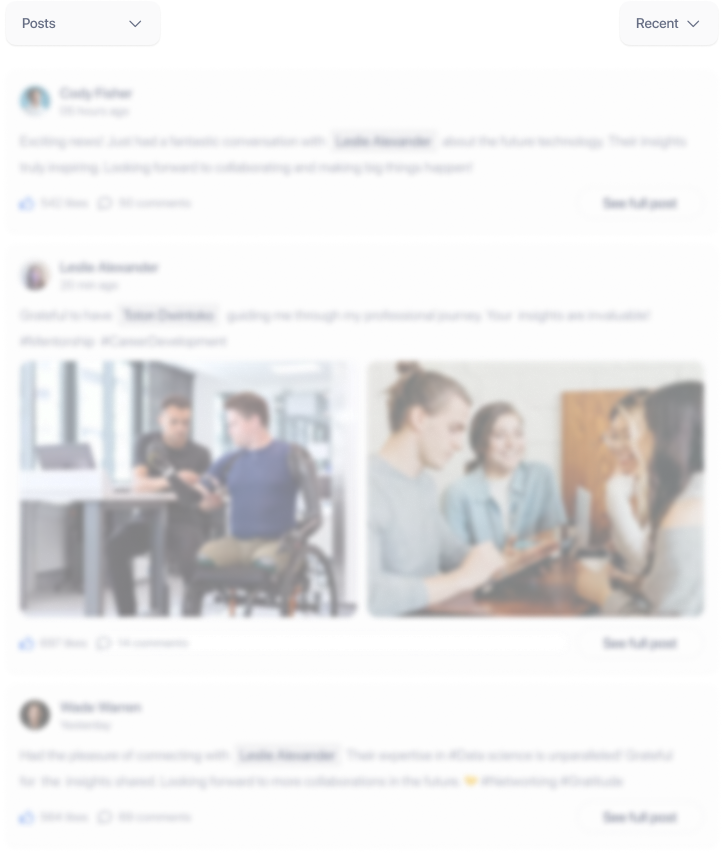