
Jacob Napolitan
Melt Shop Quality Engineer at North American Stainless- Claim this Profile
Click to upgrade to our gold package
for the full feature experience.
-
English Native or bilingual proficiency
Topline Score
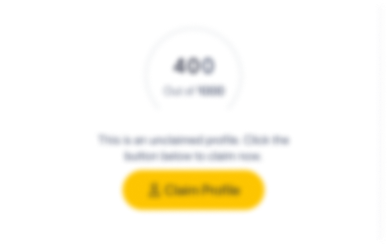
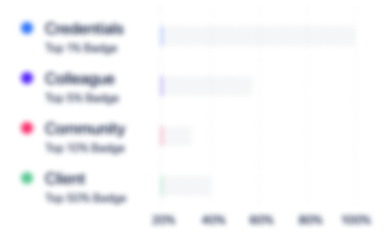
Bio


Credentials
-
Dale Carnegie Course Certification
Dale CarnegieSep, 2018- Nov, 2024 -
Lean Manager Certification
ProductivityMar, 2018- Nov, 2024
Experience
-
North American Stainless
-
Mining
-
400 - 500 Employee
-
Melt Shop Quality Engineer
-
Feb 2019 - Present
-
-
-
ATI - Allegheny Technologies Incorporated
-
United States
-
Mining
-
100 - 200 Employee
-
Continuous Improvement Leader
-
Feb 2018 - Jan 2019
• Position: Continuous Improvement Leader• Led a Lean Transformation Project in billet CNC machining operations in conjunction with the Lean Manager Certification Program at Ohio State University• Decreased CNC cycle time by 4.7% on average and changeover time by 27.1% on average through kaizen events• Developed Value Stream Maps for various processes from melting to fabrication of the completed metal product• Implemented new processes to increase communication between operations and improve flatness of zirconium sheets – resulted in 50% increase in meeting customers’ flatness requirements for on time delivery improvement and cost savings• Led and facilitated task standardization events to eliminate variation within critical operating tasks and improve safety of the operators, quality of the product, and reliability of the equipment
-
-
Process Engineer - Quality Assurance
-
Feb 2017 - Feb 2018
• Position: Process Engineer – Quality Assurance• Investigated root cause of product quality concerns and initiated corrective actions to resolve them• Determined processing steps required to correct and prevent repeated quality issues• Developed standardized rule set to eliminate unfavorable automated line speed transitions within a continuous annealing furnace – implemented into line’s PLC and saved $50,000 in annual Cost of Poor Quality• Performed statistical analysis on historical data for a continuous annealing line’s automated welder and altered critical welding parameters based on results – led to significant decrease in disastrous weld breakage events• Altered quality control procedures to minimize scrap and customer exposure to unsatisfactory quality• Examined annealing cycles and cold rolling practices to ensure consistent mechanical properties and optimize manufacturing efficiency• Presented projects’ impact to company executive leadership including CEO
-
-
-
Parker Hannifin
-
United States
-
Industrial Machinery Manufacturing
-
700 & Above Employee
-
Materials Science Co-op
-
May 2015 - Nov 2016
• Position: Materials Science Co-op• Researched potential plating technologies to enhance corrosion performance of steel products• Conducted ASTM B117 salt spray testing to compare effectiveness of different plating techniques• Built correlation between experimental accelerated corrosion tests and salt spray results to decrease time• Performed failure analysis to determine material fracture mode and improve product quality• Prepared metallographic samples for microstructural analysis and scanning electron microscopy• Conducted material property testing including hardness and chemical composition• Prepared professional reports summarizing results and recommending steps for product improvement• Frequently operated optical emission spectrometer, tensile and fatigue testers, high-performance optical microscope, and scanning electron microscope with energy dispersive spectroscopy capabilities
-
-
-
Triumph Thermal Systems, LLC
-
Aviation and Aerospace Component Manufacturing
-
1 - 100 Employee
-
Engineering Design Co-op
-
May 2014 - Aug 2014
• Position: Engineering Design Co-op• Developed a consistent polishing system for preparing metallographic samples for microscopic analysis• Headed a research and design project – designed a tube-based heat exchanger for performance analysis• Led a portion of a Six Sigma project designed to optimize braze joint quality in aluminum heat exchangers• Utilized CATIA software to measure and calculate braze joint quantities from sample micrographs• Developed MATLAB/Excel programs to calculate weight of specific parts with inputted values• Utilized CATIA software to model parts and solve manufacturing problems• Created braze furnace profiles for aluminum parts to determine optimum brazing parameters
-
-
-
College Works Painting
-
United States
-
Construction
-
300 - 400 Employee
-
Business Manager, Intern
-
Feb 2013 - Aug 2013
• Position: Business Manager, Intern (Lakewood, OH)• Operated exterior house painting business totaling over $150,000 of revenue• Designed and implemented a marketing strategy to discover a potential clientele• Estimated all jobs and booked over 42% upon initial customer contact• Interviewed, hired and personally managed a 14-employee, 5-crew work force• Recognized as top manager nationally out of 1,200+• Broke sales record in state of Ohio by $50,000 in revenue• Worked 28 hours/week during school year with maximum course load
-
-
Education
-
The Ohio State University
Bachelor’s Degree, Materials Science
Community
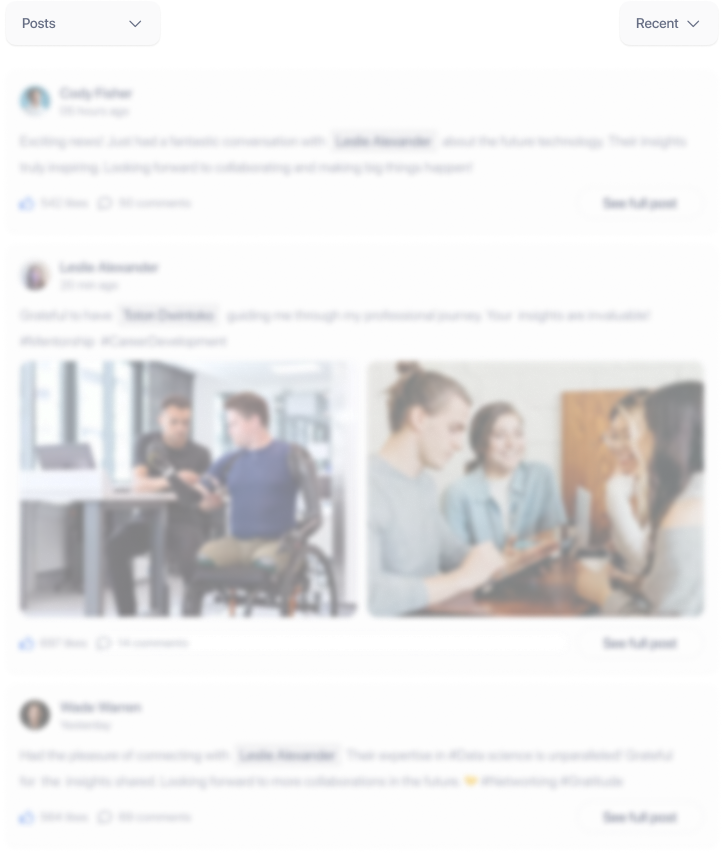