Jack K Moriarty, CQE, CQA
Quality Assurance Manager at Pacific Instruments, Inc.- Claim this Profile
Click to upgrade to our gold package
for the full feature experience.
-
English Native or bilingual proficiency
-
Thai Native or bilingual proficiency
Topline Score
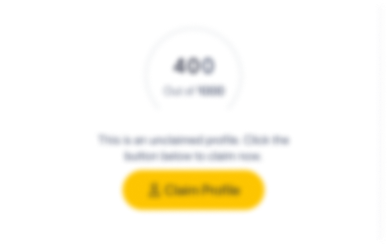
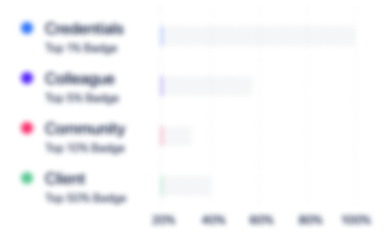
Bio


Credentials
-
Certified Quality Auditor
ASQ - World HeadquartersOct, 2017- Nov, 2024 -
Certified Quality Engineer
ASQ - World HeadquartersJun, 2017- Nov, 2024 -
Heartsaver First Aid CPR AED
American Heart Association | American Stroke AssociationApr, 2016- Nov, 2024
Experience
-
Pacific Instruments, Inc.
-
Medical Equipment Manufacturing
-
1 - 100 Employee
-
Quality Assurance Manager
-
May 2020 - Present
-
-
-
Philips
-
Netherlands
-
Hospitals and Health Care
-
700 & Above Employee
-
Senior Quality Assurance Engineer
-
Mar 2018 - May 2020
• Remediated the Quality Management System of a recent acquired EGI to Philips’ Quality Management System in order to comply with ISO 13485 Standards.• Implemented a process validation program and remediated the manufacturing process validations. Act as reviewer and approver of executed IQ, OQ, and PQ for equipment and process change.• Manage the validation strategy and timeline of manufacturing relocation.• Establish Preventive Maintenance and Calibration program for equipment and tools in the manufacturing area.• Establish the Non-Conformance Procedure and manage the Material Review Boards (MRB).• Support Back Room and act as a Subject Matter Expert during the internal audit or notifying body audit including the MDSAP resulting in only two nonconformance.• Certified as Lead Auditor for Philips Neuro and perform supplier audits.• Investigate, analyze and correct non-conformances (internal, external and systemic issues) and provide corrective actions and ensure their effectiveness.• Act as independent reviewer for the Design Transfer of New Product Introduction/Development.
-
-
-
Thermo Fisher Scientific
-
United States
-
Biotechnology Research
-
700 & Above Employee
-
Quality Engineer
-
Nov 2015 - Feb 2018
• Investigate, analyze and correct non-conformances (internal, external and systemic issues)and provide corrective actions and ensure their effectiveness.• Create, manage and close internal Corrective and Preventative Action (CAPA) plans and Supplier Corrective Action Reports (SCAR).• Create quality documents aligned to regulations and practices, revise quality documentation to better define, improve, or clarify practices, process and/or product quality.• Perform internal audits and participate in external audits.• Facilitate Kaizen events in the finished goods manufacturing as part of continuous improvement process to reduce the number of defects as well as other process related projects.• Perform IQ, OQ, PQ for equipments on site.• Lead quality activities in new product introduction (NPI) processes.• Certified as Process Improvement Facilitator (PPI) through Kaizen training.
-
-
-
Eli Lilly and Company
-
United States
-
Pharmaceutical Manufacturing
-
700 & Above Employee
-
Regulatory Affairs Associate
-
Aug 2014 - Jul 2015
• Create regulatory documents for the TransCIT project, integrating old clinical trail database to the new supply chain system.• Audit manufacturing document for accuracy and quality to ensure completion.• Collaborate with lead scientists on any regulatory opportunities pertaining to clinical trial data.
-
-
-
Mondelēz International
-
United States
-
Food and Beverage Manufacturing
-
700 & Above Employee
-
Quality Engineer
-
Feb 2013 - Mar 2014
• Lead a new pilot program for allergen control and tool management to aid operators in their daily tasks and lead the Pest Control Department for the FSSC 22000 and the Corporate International audit• Audited production and quality documentation to ensure completion and accuracy• Performed root cause analysis of nonconformances for in-process goods and provide the corrective and preventative actions and dispositions in the event of quality or safety deviation• Maintained the accuracy and calibration of lab testing equipment in lab and on production floor• Provided training to operators; the use of quality equipment, HACCP, GMP, Kosher, Allergens, and other quality programs• Validated acceptable tolerance from suppliers and out the door products• Worked with a cross-functioning team of operation, production and distribution for any quality opportunities
-
-
-
Stryker
-
United States
-
Medical Equipment Manufacturing
-
700 & Above Employee
-
Quality Engineer / Post Market Surveillance
-
Dec 2010 - Feb 2013
• Responsible for the identification of potential failure modes and risks for medical devices• Performed and exceeded metrics for PER (product experience report) investigations for multiple product lines (Med/Surg and Critical Care beds, Surfaces, Joerns and EMS)• Worked on various projects to aid the Post Market team such as Risk document tracking and updates, corrective action implementation and consistency templates• Determined the root cause of nonconformance with the goal of implementing permanent changes to improve the quality and safety of the products using the NC/CAPA system• Ensured compliance with all US, EU and SO international requirements in conjunction with corporate policies and procedures regarding submissions for market approval of medical devices (over 40 MDR reporting weekly)• Reduced quality reports back-logged and maintains a 90% completion rate over the target of 60%• Maintained a point of contact position for communication to field service technicians
-
-
-
Foxconn
-
Appliances, Electrical, and Electronics Manufacturing
-
700 & Above Employee
-
Supply Chain Process Control
-
Dec 2006 - Jan 2008
-
-
Education
-
Purdue University
Bachelor's Degree
Community
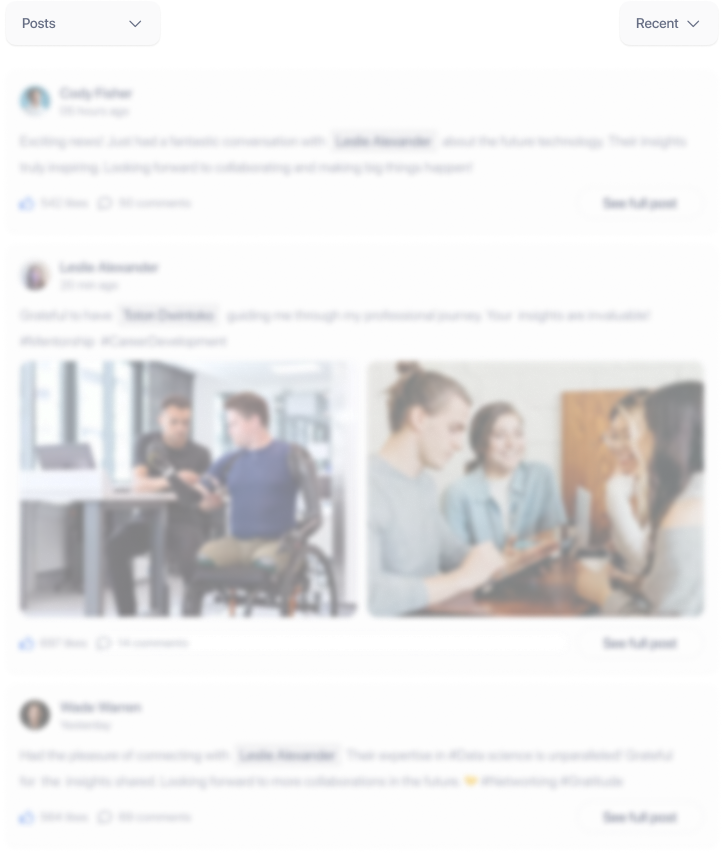