Jackie Griffiths (nee Bull)
Manufacturing Engineer at Rolls-Royce SMR- Claim this Profile
Click to upgrade to our gold package
for the full feature experience.
Topline Score
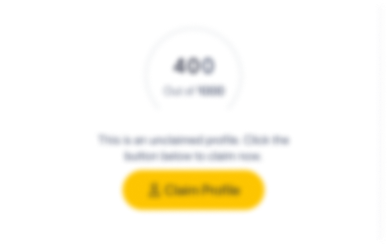
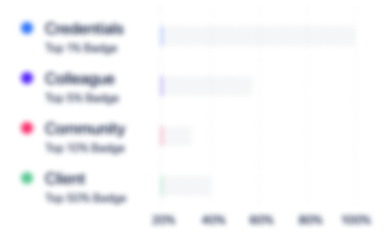
Bio


Experience
-
Rolls-Royce SMR
-
United Kingdom
-
Nuclear Electric Power Generation
-
300 - 400 Employee
-
Manufacturing Engineer
-
Jun 2022 - Present
-
-
-
UK Atomic Energy Authority
-
United Kingdom
-
Research Services
-
700 & Above Employee
-
Project Manager
-
Nov 2021 - May 2022
Management and development of key supplier relationships to support delivery of large test rig components. Management and development of key supplier relationships to support delivery of large test rig components.
-
-
-
AMRC
-
United Kingdom
-
Research Services
-
300 - 400 Employee
-
Project Manager
-
Mar 2021 - Nov 2021
Responsible for delivery of transformational research activities across a wide range of subject areas. I worked to successfully delivery projects through effective management of project finances, resource, risk and reporting. Responsible for delivery of transformational research activities across a wide range of subject areas. I worked to successfully delivery projects through effective management of project finances, resource, risk and reporting.
-
-
-
Rolls-Royce
-
Industrial Machinery Manufacturing
-
700 & Above Employee
-
Capability Acquisition Lead (Inspection)
-
Jul 2017 - Dec 2020
Working to develop and deliver inspection capability to meet the future needs of the turbines business. I worked collaboratively with company specialists, external research establishments and equipment suppliers to deliver next generation inspection capability.
-
-
ABCF Equipment and Installation Lead
-
Feb 2011 - Jul 2017
Responsible for delivery of circa £40m of equipment into the new Rolls-Royce Advanced Blade Casting Facility. I took an active role in securing funding for equipment and acted as a point of contact for the ABCF project team to enable problem resolution and progression to plan supporting equipment procurement, manufacture, installation and testing.
-
-
IPT Lead - High Performance Disk Manufacture
-
Jul 2009 - Feb 2011
Working within the Rotatives business I led the initial phase of activity to transform the complete manufacturing method for five critical component types (26 part numbers) with the intent of delivering significant cycle time and productivity improvements. I secured circa £800k of funding for 2009 and supported funding applications for 2010; I established a cross functional team incorporating external research partners and key suppliers. Cycle time reductions of 50% and the potential to double productivity were demonstrated on two representative components.
-
-
Near Net and Fusion Welding - Team Leader
-
Jan 2005 - Jul 2009
Leading a team of ten, including several noted company experts, I was responsible for development and implementation of novel forming, joining and additive manufacturing techniques. I worked with the team to define strategy, secure funding and deliver programs in support of both original component manufacture and subsequent repair
-
-
Manufacturing Engineer - Manufacturing Technology
-
Jan 2002 - Dec 2004
Working on a number of advanced joining techniques. I delivered Linear Friction Welding capability for manufacture of two Blisk (bladed disk) components, advanced development of laser welding capability for application to large casting structures and lead a project to demonstrate application of Shaped Metal Deposition (TIG based ALM) to large aero engine components.
-
-
Graduate Trainee
-
Sep 2000 - Dec 2001
Completed an 18 month engineering training scheme including multiple work placements and a structured training program.
-
-
Education
-
Cranfield University
Master of Science (MSc), Operations Excellence -
The University of Birmingham
Master in Science (MSci Hons), Physics
Community
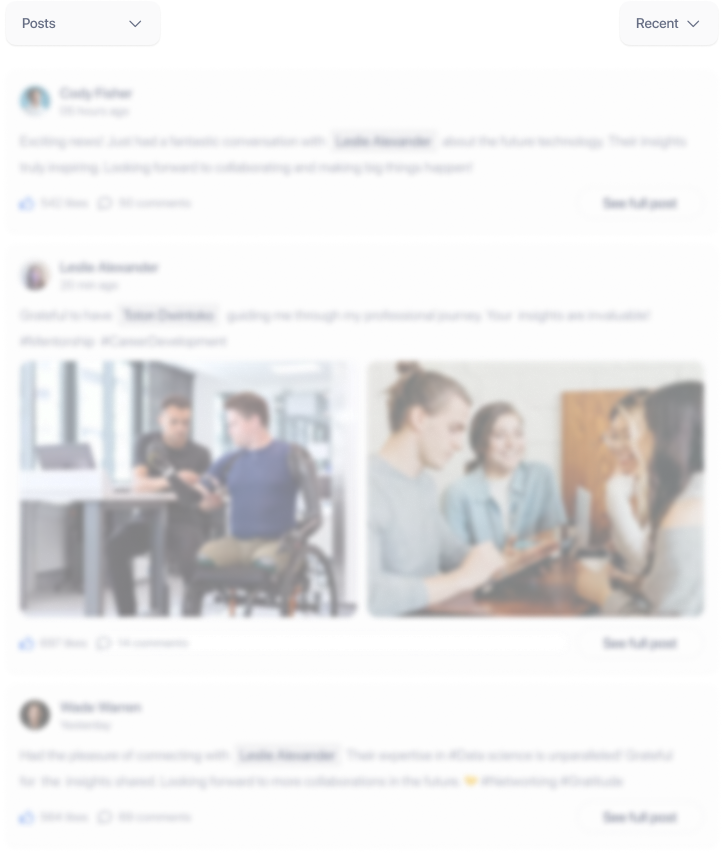